Los reactores discontinuos, aunque versátiles y muy utilizados en laboratorios y en la producción a pequeña escala, presentan varios inconvenientes importantes.Entre ellas, los elevados costes de mano de obra, las dificultades para aumentar la producción, los largos tiempos de inactividad durante las operaciones, la limitada instrumentación, la calidad irregular del producto y los riesgos de seguridad, como las explosiones.Además, los reactores discontinuos suelen ser más adecuados para reacciones homogéneas, lo que limita su aplicabilidad en procesos industriales más complejos.Estos inconvenientes los hacen menos eficaces y rentables que los reactores de flujo continuo, que ofrecen mayores rendimientos, mejor control y menores costes de fabricación.
Explicación de los puntos clave:
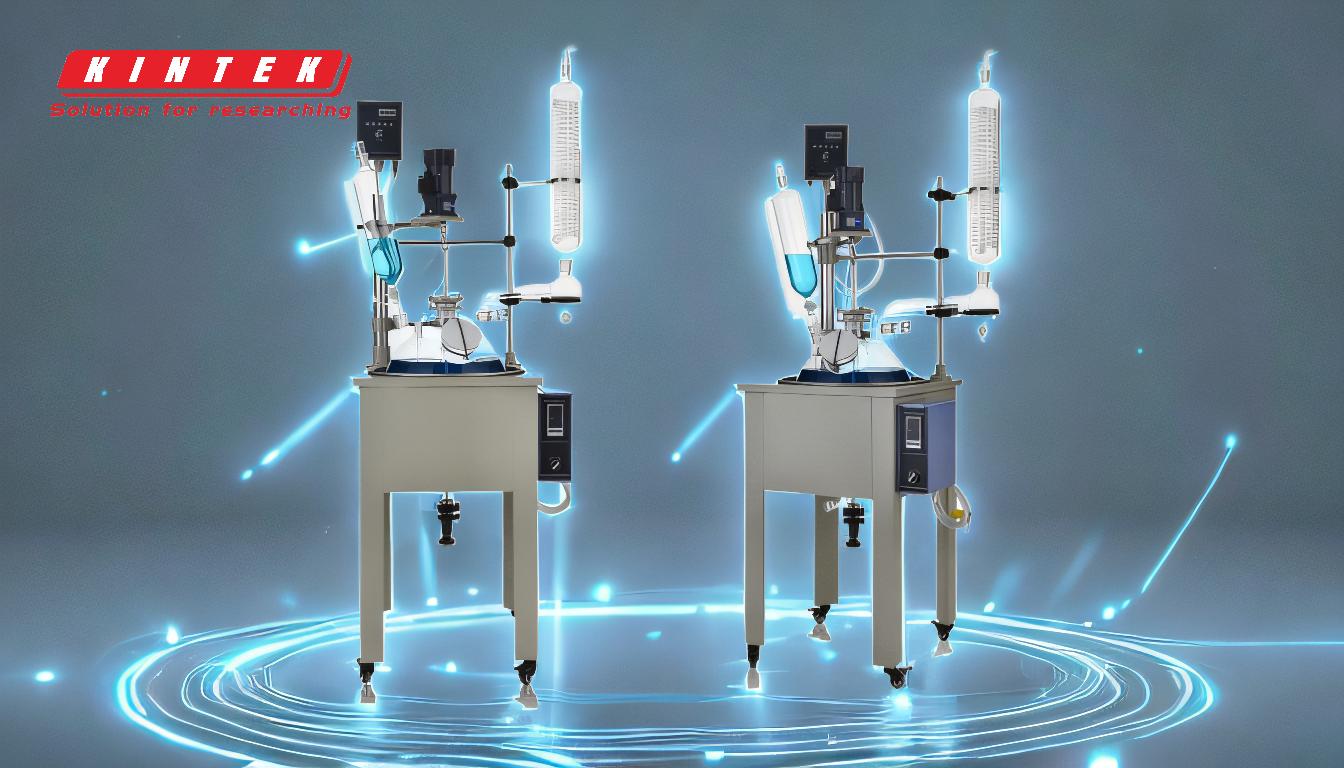
-
Elevados costes de mano de obra por unidad de producción
- Los reactores discontinuos requieren una intervención manual significativa para tareas como la carga, la descarga y la limpieza.Esto aumenta los costes de mano de obra, especialmente si se comparan con los reactores de flujo continuo, que están más automatizados y requieren menos supervisión humana.
- La naturaleza repetitiva de los procesos por lotes también genera ineficiencias, ya que los trabajadores deben realizar las mismas tareas varias veces para cada lote.
-
Dificultad para mantener la producción a gran escala
- Los reactores discontinuos no son adecuados para la producción industrial a gran escala debido a su capacidad limitada y a la necesidad de frecuentes ciclos de arranque y parada.
- Aumentar la producción con reactores discontinuos suele implicar el uso de varios reactores, lo que aumenta los costes y la complejidad.Los reactores de flujo continuo, por el contrario, están diseñados para la producción de grandes volúmenes y pueden funcionar continuamente sin interrupciones.
-
Largos tiempos muertos durante la carga y descarga
- Una parte significativa del ciclo de producción de los reactores discontinuos se dedica a tareas no productivas, como la carga de reactivos, el calentamiento o enfriamiento del sistema y la descarga de productos.
- Estos tiempos de inactividad reducen la eficiencia y el rendimiento globales, lo que hace que los reactores discontinuos sean menos adecuados para procesos de producción sensibles al tiempo o de alta demanda.
-
Falta de instrumentación y control
- Los reactores discontinuos suelen carecer de sistemas avanzados de instrumentación y control, lo que dificulta la supervisión y optimización de las condiciones de reacción en tiempo real.
- Esto puede provocar incoherencias en la calidad del producto y reducir la fiabilidad del proceso, ya que los operarios tienen menos control sobre variables como la temperatura, la presión y la mezcla.
-
Calidad y consistencia deficientes del producto
- Debido a la falta de un control preciso y a la variabilidad inherente entre lotes, los reactores discontinuos suelen producir productos de calidad irregular.
- Esto es especialmente problemático en industrias en las que la uniformidad del producto es crítica, como la farmacéutica o las especialidades químicas.
-
Riesgos de explosión durante el vaciado
- Los reactores discontinuos pueden plantear riesgos de seguridad, especialmente durante la fase de vaciado, cuando los reactantes residuales o los subproductos pueden reaccionar de forma impredecible.
- El diseño de los reactores discontinuos no está optimizado para manejar explosiones potentes, lo que los hace menos seguros que los reactores de flujo continuo, que están diseñados para gestionar condiciones de alta presión y alta temperatura de forma más eficaz.
-
Aplicabilidad limitada a reacciones homogéneas
- Los reactores discontinuos son adecuados principalmente para reacciones homogéneas, en las que los reactivos y los productos se encuentran en una sola fase (por ejemplo, líquida o gaseosa).
- Son menos eficaces para las reacciones heterogéneas, en las que intervienen varias fases (por ejemplo, sólido-líquido o gas-líquido), lo que limita aún más su versatilidad en las aplicaciones industriales.
-
Mayores costes de fabricación y funcionamiento
- Aunque los reactores discontinuos pueden ahorrar costes de fabricación iniciales debido a su diseño más sencillo, sus ineficiencias operativas y sus mayores requisitos de mano de obra suelen traducirse en mayores costes a largo plazo.
- Los reactores de flujo continuo, a pesar de su mayor inversión inicial, ofrecen menores costes de fabricación y mayores relaciones valor-producto (VTO) a lo largo del tiempo.
-
Incapacidad para alcanzar condiciones de estado estacionario
- Los reactores discontinuos no alcanzan un estado estacionario, lo que significa que las condiciones de reacción (por ejemplo, temperatura, presión y concentración) cambian con el tiempo.
- Esto dificulta el control y la optimización de la reacción, lo que puede dar lugar a ineficiencias y rendimientos de producto inferiores a los óptimos.
-
Diseño y tecnología obsoletos
- Los reactores discontinuos han experimentado mínimos cambios de diseño a lo largo del tiempo, basándose en métodos tradicionales que carecen de los avances observados en los reactores de flujo continuo.
- Esto limita su capacidad para competir con las modernas tecnologías de reactores, que ofrecen mejores prestaciones, mayores rendimientos y características de seguridad mejoradas.
En resumen, aunque los reactores discontinuos son sencillos y versátiles, sus desventajas -que van desde los elevados costes de mano de obra y la escasa escalabilidad hasta los riesgos de seguridad y la inconsistencia de la calidad del producto- los hacen menos adecuados para las aplicaciones industriales modernas.Los reactores de flujo continuo, con su tecnología avanzada y su eficiencia superior, son cada vez más preferidos para los procesos de producción a gran escala y de alta demanda.
Cuadro sinóptico:
Desventaja | Descripción |
---|---|
Costes laborales elevados | Requiere una importante intervención manual, lo que incrementa los costes operativos. |
Escalabilidad deficiente | No es ideal para la producción a gran escala debido a los frecuentes ciclos de arranque y parada. |
Largos tiempos de inactividad | Las tareas no productivas, como la carga y descarga, reducen la eficiencia. |
Instrumentación limitada | La falta de supervisión y control en tiempo real da lugar a resultados incoherentes. |
Calidad incoherente del producto | La variabilidad entre lotes afecta a la uniformidad del producto. |
Riesgos de seguridad | Riesgos de explosión durante el vaciado debido a reacciones imprevisibles. |
Limitado a reacciones homogéneas | Menos eficaz para reacciones complejas y multifásicas. |
Mayores costes operativos | Las ineficiencias a largo plazo compensan el ahorro inicial. |
Sin condiciones estables | Las condiciones de reacción cambian con el tiempo, lo que dificulta la optimización. |
Tecnología obsoleta | Carece de los avances que se observan en los reactores de flujo continuo modernos. |
Descubra cómo los reactores de flujo continuo pueden resolver sus retos de producción. póngase en contacto con nosotros ¡!