Los reactores discontinuos se utilizan mucho en industrias como la alimentaria, la farmacéutica y la química por su versatilidad, facilidad de manejo y adecuación a la producción a pequeña escala.Ofrecen altos índices de conversión por unidad de volumen, flexibilidad en las condiciones de funcionamiento y bajos costes iniciales.Sin embargo, también presentan notables inconvenientes, como los elevados costes de mano de obra, la ineficacia en la producción a gran escala, los largos tiempos de inactividad y los posibles riesgos para la seguridad.Comprender los pros y los contras de los reactores discontinuos es crucial para seleccionar el equipo adecuado para aplicaciones específicas.
Puntos clave explicados:
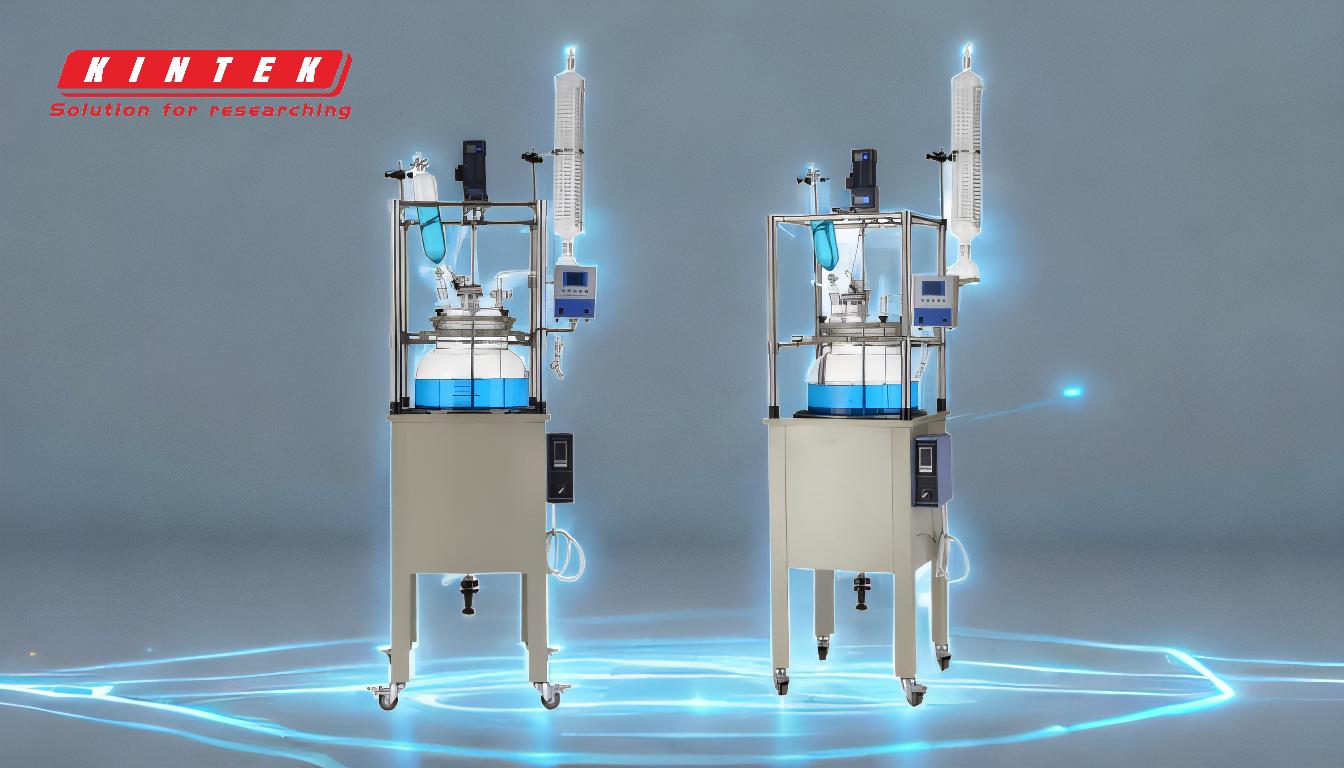
1. Ventajas de los reactores discontinuos
- Alta conversión por unidad de volumen:Los reactores discontinuos son eficientes a la hora de conseguir altas tasas de conversión, lo que los hace ideales para reacciones en las que maximizar el rendimiento es fundamental.
- Facilidad de limpieza:Su diseño permite una limpieza sencilla entre lotes, lo que resulta esencial en industrias como la farmacéutica y la alimentaria para evitar la contaminación cruzada.
- Bajo coste:Los reactores discontinuos suelen tener unos costes de capital iniciales inferiores a los de los reactores continuos, lo que los hace accesibles para la producción a pequeña escala e intermedia.
- Versatilidad:Un único reactor discontinuo puede gestionar múltiples operaciones sin romper la contención, lo que resulta especialmente beneficioso para procesar compuestos tóxicos o muy potentes.
- Flexibilidad en las condiciones de funcionamiento:Pueden adaptarse a una amplia gama de temperaturas, presiones y tiempos de reacción, lo que las hace adecuadas para diversas aplicaciones.
- Idoneidad para la producción a pequeña escala:Los reactores discontinuos son ideales para la producción a pequeña escala e intermedia, así como para su uso en países en desarrollo donde la infraestructura puede ser limitada.
- No es necesario rediseñar durante la optimización:Permiten optimizar el proceso sin necesidad de rediseñar el reactor, ahorrando tiempo y recursos.
2. Desventajas de los reactores discontinuos
- Elevados costes de mano de obra:Los reactores discontinuos requieren una importante intervención manual para la carga, descarga y limpieza, lo que conlleva mayores costes de mano de obra por unidad de producción.
- Dificultad en la producción a gran escala:Son menos eficientes para la producción a gran escala debido a la necesidad de ciclos de lotes repetidos, que pueden consumir mucho tiempo y recursos.
- Largos tiempos de inactividad:El proceso de carga y descarga de materiales da lugar a largos tiempos de inactividad, lo que reduce la productividad global.
- Falta de instrumentación:Los reactores discontinuos suelen tener una instrumentación limitada, lo que dificulta la supervisión y el control precisos del proceso de reacción.
- Mala calidad del producto:Las condiciones de reacción incoherentes entre lotes pueden provocar variaciones en la calidad del producto.
- Riesgos para la seguridad:El proceso de vaciado de los reactores discontinuos, especialmente en el caso de materiales volátiles o explosivos, puede plantear importantes riesgos de seguridad.
- Limitado a reacciones homogéneas:Los reactores discontinuos suelen preferirse para reacciones homogéneas, lo que limita su aplicabilidad en procesos más complejos.
3. Aplicaciones de los reactores discontinuos
- Industrias alimentaria y farmacéutica:Los reactores discontinuos se utilizan ampliamente en estas industrias debido a su capacidad para manipular materiales sensibles y mantener estrictas normas de higiene.
- Compuestos tóxicos o potentes:Su capacidad de contención las hace adecuadas para procesar compuestos tóxicos o muy potentes sin riesgo de contaminación.
- Producción intermedia y a pequeña escala:Son ideales para producir pequeñas cantidades de productos especializados, como productos químicos o farmacéuticos a medida.
4. Consideraciones para los compradores de equipos
- Escala de producción:Los reactores discontinuos son los más adecuados para la producción a pequeña escala o intermedia.Para operaciones a gran escala, los reactores continuos pueden ser más eficientes.
- Disponibilidad de mano de obra:Los elevados costes de mano de obra asociados a los reactores discontinuos deben sopesarse con la disponibilidad y el coste de la mano de obra cualificada.
- Requisitos de seguridad:Los compradores deben tener en cuenta los riesgos para la seguridad, especialmente cuando se trate de materiales volátiles o explosivos, y asegurarse de que se aplican las medidas de seguridad adecuadas.
- Flexibilidad del proceso:Si el proceso de producción requiere cambios frecuentes u optimización, los reactores discontinuos ofrecen la flexibilidad necesaria sin necesidad de un rediseño significativo.
- Consistencia de la calidad del producto:Para las industrias en las que la consistencia de la calidad del producto es crítica, deben evaluarse cuidadosamente las limitaciones de los reactores discontinuos a la hora de mantener condiciones uniformes.
En conclusión, los reactores discontinuos ofrecen ventajas significativas en términos de versatilidad, flexibilidad y rentabilidad para la producción a pequeña escala e intermedia.Sin embargo, hay que tener muy en cuenta sus limitaciones en la producción a gran escala, la intensidad de mano de obra y los posibles riesgos para la seguridad.Los compradores de equipos deben evaluar sus necesidades específicas de producción, la disponibilidad de mano de obra y los requisitos de seguridad para determinar si los reactores discontinuos son la opción adecuada para sus operaciones.
Tabla resumen:
Aspecto | Ventajas | Desventajas |
---|---|---|
Eficiencia de conversión | Alta conversión por unidad de volumen | Limitado a reacciones homogéneas |
Coste | Bajos costes de capital inicial | Costes de mano de obra elevados |
Versatilidad | Maneja múltiples operaciones sin romper la contención | Ineficiente para la producción a gran escala |
Flexibilidad | Se adapta a amplios rangos de temperatura, presión y tiempo de reacción | Largos tiempos de inactividad entre lotes |
Limpieza | Fácil de limpiar, ideal para industrias sensibles | Mala calidad del producto debido a condiciones inconsistentes |
Seguridad | Adecuado para compuestos tóxicos o potentes | Riesgos de seguridad durante el vaciado, especialmente con materiales volátiles |
Aplicaciones | Ideal para alimentos, productos farmacéuticos y producción a pequeña escala | Instrumentación limitada para un control preciso |
¿Necesita ayuda para seleccionar el reactor adecuado a sus necesidades? Póngase en contacto hoy mismo con nuestros expertos para un asesoramiento personalizado.