En la industria farmacéutica, los reactores son equipos esenciales para las reacciones químicas, la síntesis de fármacos y la producción biofarmacéutica.Proporcionan entornos controlados para optimizar las condiciones de reacción, mejorar el rendimiento y garantizar la pureza del producto.Los reactores son de varios tipos: reactores de alta presión para acelerar la producción de moléculas complejas, reactores de vidrio para productos biofarmacéuticos como anticuerpos monoclonales y enzimas, y reactores especializados para API.Estos reactores permiten un control cinético preciso, reducen el tiempo de desarrollo y apoyan procesos como el cultivo celular, la fermentación y el procesamiento posterior.Su versatilidad y adaptabilidad los hacen indispensables en el desarrollo y la fabricación de fármacos.
Explicación de los puntos clave:
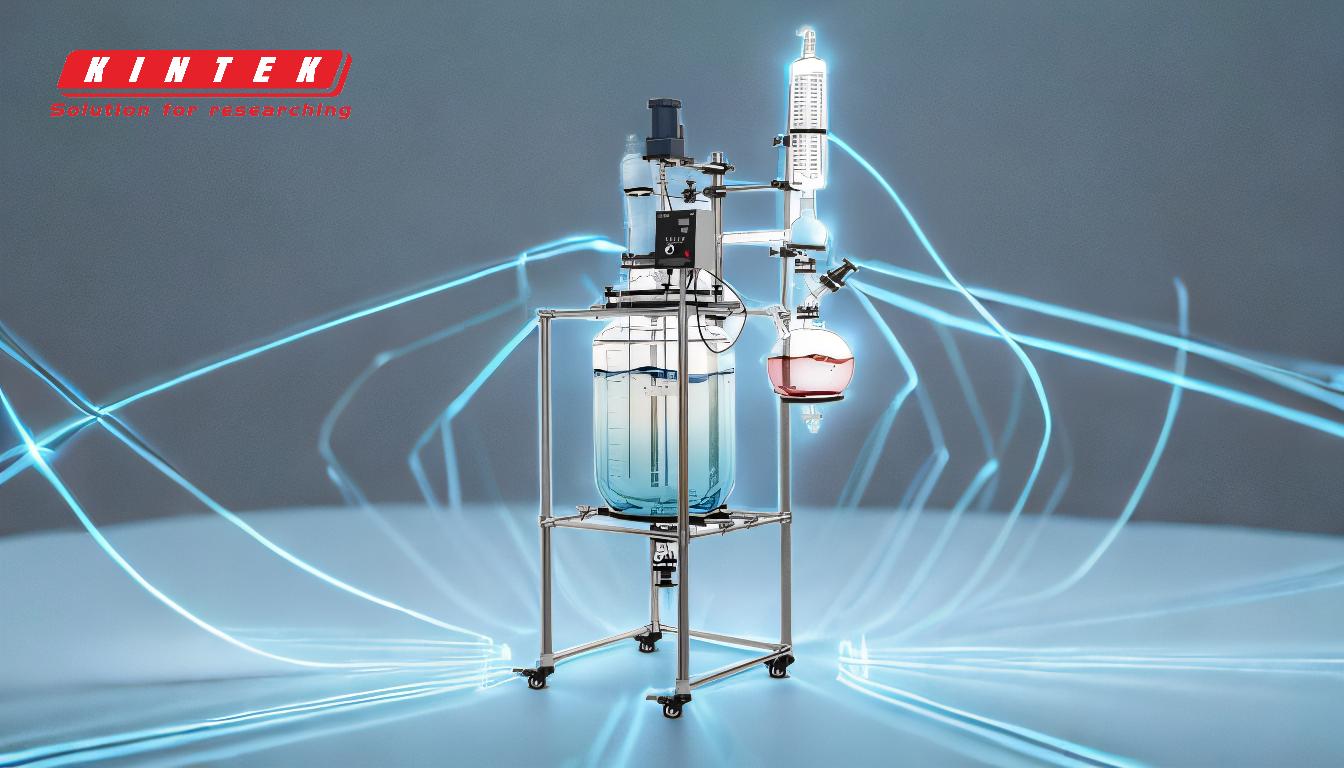
-
Definición y finalidad de los reactores en la industria farmacéutica
- Los reactores son recipientes especializados diseñados para facilitar las reacciones químicas en condiciones controladas.
- Son fundamentales para la síntesis de fármacos, la producción biofarmacéutica y la optimización de parámetros de reacción como la temperatura, la presión y la mezcla.
- Los reactores garantizan altos rendimientos, pureza del producto y consistencia, que son vitales para la fabricación farmacéutica.
-
Tipos de reactores utilizados en la industria farmacéutica
-
Reactores de alta presión:
- Se utilizan para acelerar la producción de moléculas complejas.
- Permiten un control cinético preciso, reduciendo el tiempo necesario para el desarrollo de fármacos.
- Ideales para reacciones de varios pasos y síntesis a alta presión.
-
Reactores de vidrio:
- De uso común para la producción biofarmacéutica, incluidos los anticuerpos monoclonales, las proteínas recombinantes y las enzimas terapéuticas.
- Proporcionan un entorno claro y controlado para el cultivo celular, la fermentación y el procesamiento posterior.
- Adecuados para la síntesis de fármacos, especialmente en la producción de ingredientes farmacéuticos activos (API).
-
Otros tipos de reactores:
- Reactor de flujo tapón, reactor continuo de tanque agitado, reactor de bucle, reactor discontinuo, reactor catalítico y reactor discontinuo.
- Cada tipo se adapta a aplicaciones específicas, como el procesamiento continuo o la producción por lotes.
-
Reactores de alta presión:
-
Aplicaciones de los reactores en la industria farmacéutica
-
Síntesis de fármacos:
- Los reactores se utilizan para producir API y otros compuestos farmacéuticos.
- Optimizan las condiciones de reacción para lograr altos rendimientos y pureza.
-
Producción biofarmacéutica:
- Los reactores de vidrio son esenciales para producir productos biofarmacéuticos como proteínas, enzimas y vacunas.
- Sirven de apoyo a los procesos de cultivo celular y fermentación, garantizando un entorno controlado para el crecimiento y la producción.
-
Desarrollo de procesos:
- Los reactores permiten a los investigadores estudiar y ampliar las reacciones desde el laboratorio hasta la escala industrial.
- Reducen el tiempo de desarrollo al acelerar las reacciones de varios pasos y proporcionar un control preciso de los parámetros de reacción.
-
Síntesis de fármacos:
-
Ventajas del uso de reactores en la industria farmacéutica
-
Precisión y control:
- Los reactores permiten un control preciso de la temperatura, la presión y la mezcla, garantizando unas condiciones de reacción óptimas.
-
Eficacia:
- Los reactores de alta presión y los reactores de flujo continuo reducen el tiempo de producción y mejoran la eficacia.
-
Escalabilidad:
- Los reactores facilitan la transición de los experimentos a escala de laboratorio a la fabricación a gran escala.
-
Versatilidad:
- Existen configuraciones personalizadas y reactores especializados para aplicaciones específicas, como la investigación de biocombustibles o la producción biofarmacéutica.
-
Precisión y control:
-
Consideraciones para la selección de reactores
-
Compatibilidad de materiales:
- Los reactores de vidrio son los preferidos para los productos biofarmacéuticos por su naturaleza inerte y su transparencia.
- Los reactores de alta presión suelen fabricarse con materiales duraderos como el acero inoxidable.
-
Requisitos del proceso:
- La elección del reactor depende del proceso específico, como la producción por lotes o continua.
-
Escalabilidad:
- Los reactores deben ser escalables para adaptarse a las necesidades de producción desde el laboratorio hasta la escala industrial.
-
Personalización:
- Pueden ser necesarias configuraciones personalizadas para aplicaciones especializadas, como los biocombustibles o procesos únicos de síntesis de fármacos.
-
Compatibilidad de materiales:
-
Tendencias futuras en reactores farmacéuticos
-
Automatización y digitalización:
- Uso creciente de sistemas automatizados y controles digitales para mejorar la precisión y la eficiencia.
-
Sostenibilidad:
- Desarrollo de reactores que minimicen los residuos y el consumo de energía.
-
Materiales avanzados:
- Uso de materiales avanzados para mejorar la durabilidad, la compatibilidad y el rendimiento.
-
Integración con la IA y el aprendizaje automático:
- Aprovechar la IA para optimizar las condiciones de reacción y predecir los resultados, reduciendo aún más el tiempo de desarrollo.
-
Automatización y digitalización:
Al comprender el papel, los tipos y las aplicaciones de los reactores en la industria farmacéutica, las partes interesadas pueden tomar decisiones informadas para mejorar el desarrollo de fármacos y los procesos de fabricación.
Cuadro sinóptico:
Aspecto | Detalles |
---|---|
Tipos de reactores | Alta presión, Vidrio, Plug Flow, Tanque agitado continuo, Loop, Batch, Catalítico, Semi-batch |
Aplicaciones clave | Síntesis de fármacos, producción biofarmacéutica, desarrollo de procesos |
Ventajas | Control de precisión, eficiencia, escalabilidad, versatilidad |
Factores de selección | Compatibilidad de materiales, requisitos del proceso, escalabilidad, personalización |
Tendencias futuras | Automatización, sostenibilidad, materiales avanzados, integración de IA |
¿Está listo para mejorar sus procesos farmacéuticos? Póngase en contacto hoy mismo con nuestros expertos para encontrar el reactor perfecto para sus necesidades.