Los moldes de compresión son herramientas esenciales en los procesos de fabricación, especialmente para dar forma a materiales como plásticos, caucho y materiales compuestos.Los cuatro tipos principales de moldes de compresión son los moldes flash, positivos, positivos aterrizados y semipositivos, siendo los moldes flash los más utilizados.Estos moldes difieren en su diseño, funcionalidad e idoneidad para la aplicación.Además, las técnicas de moldeo por compresión se clasifican en moldeo a granel y moldeo en láminas, y el moldeo a granel implica una mezcla de rellenos, catalizadores, estabilizadores, pigmentos y refuerzos de fibra.Comprender estos tipos y sus aplicaciones es crucial para seleccionar el molde adecuado para las necesidades específicas de fabricación.
Explicación de los puntos clave:
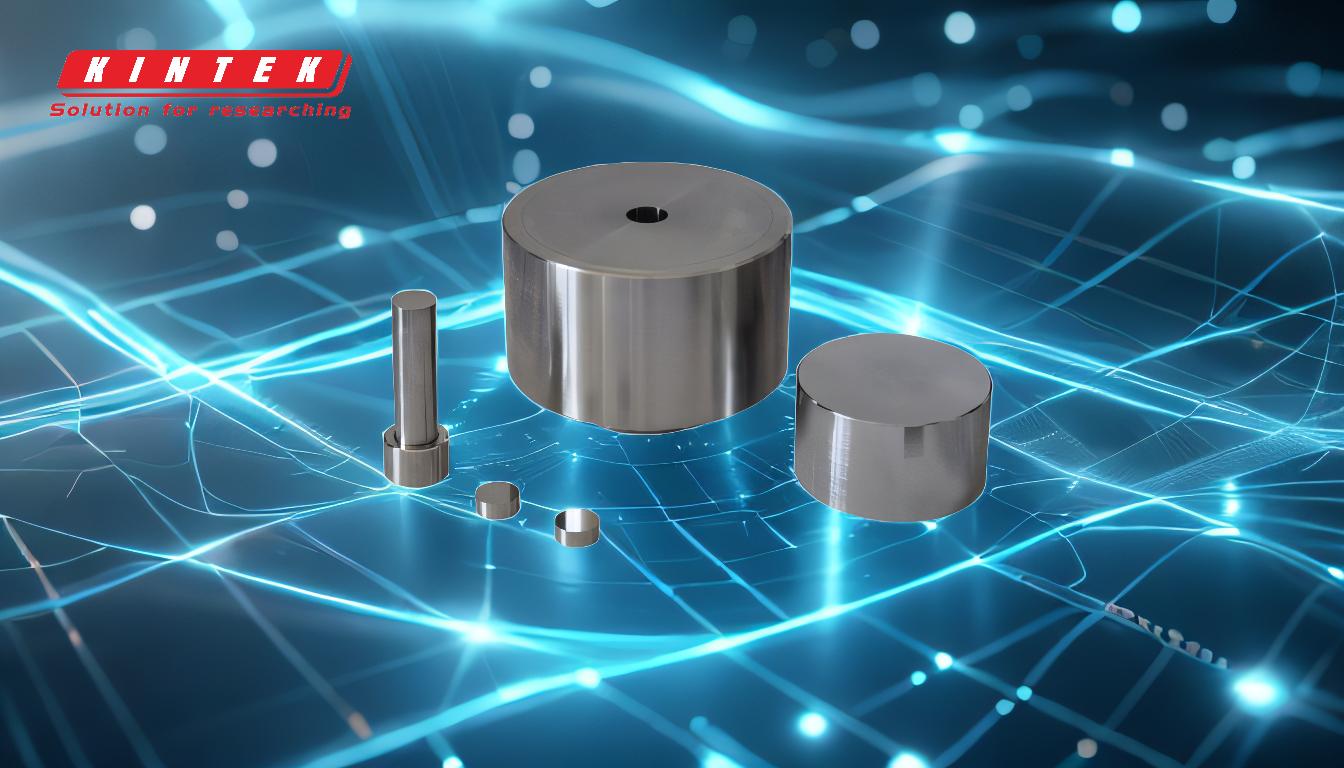
-
Moldes Flash:
- Diseño:Los moldes flash están diseñados para que el material sobrante fluya fuera de la cavidad del molde durante la compresión.
- Funcionalidad:El material sobrante, o flash, se recorta tras el proceso de moldeo.
- Aplicaciones:Comúnmente utilizadas para la producción de grandes volúmenes debido a su simplicidad y rentabilidad.
- Ventajas:Fácil de fabricar y mantener, adecuado para piezas con geometrías sencillas.
- Desventajas:Desperdicio de material debido al destello, puede requerir un tratamiento posterior adicional.
-
Moldes positivos:
- Diseño:Los moldes positivos tienen una cavidad que se cierra completamente durante el proceso de moldeo.
- Funcionalidad:No hay escapes de material sobrante, lo que garantiza un control preciso de las dimensiones finales del producto.
- Aplicaciones:Ideal para producir piezas con tolerancias estrechas y formas complejas.
- Ventajas:Alta precisión, mínimo desperdicio de material.
- Desventajas:Más complejos y caros de fabricar, requieren una alineación precisa.
-
Moldes positivos aterrizados:
- Diseño:Una variación de los moldes positivos con una zona de aterrizaje que detiene el molde en un punto específico.
- Funcionalidad:Garantiza un espesor constante de la pieza y evita la sobrecompresión.
- Aplicaciones:Adecuado para piezas que requieren un espesor uniforme y una gran precisión dimensional.
- Ventajas:Mejor control de las dimensiones de la pieza, menor riesgo de sobrecompresión.
- Desventajas:Mayor coste y complejidad en comparación con los moldes flash.
-
Moldes semipositivos:
- Diseño:Combina las características de los moldes flash y positivos, con una cantidad controlada de material que se escapa.
- Funcionalidad:Permite cierto flujo de material manteniendo un control preciso sobre las dimensiones de la pieza.
- Aplicaciones:Se utiliza para piezas que requieren a la vez precisión y cierta flexibilidad en el flujo de material.
- Ventajas:Equilibra la precisión y la eficiencia del material, adecuado para una amplia gama de aplicaciones.
- Desventajas:Más complejos que los moldes flash, pueden requerir un ajuste fino para un rendimiento óptimo.
-
Moldeo a granel:
- Proceso:Consiste en utilizar una mezcla de cargas, catalizadores, estabilizadores, pigmentos y fibras de refuerzo.
- Aplicaciones:Se utiliza habitualmente para fabricar piezas grandes y complejas de gran resistencia y durabilidad.
- Ventajas:Versátil, puede producir piezas con propiedades mecánicas mejoradas.
- Desventajas:Requiere un control preciso de la composición del material y de las condiciones de moldeo.
-
Moldeo de láminas:
- Proceso:Se trata de láminas de material preformadas que se comprimen para darles la forma deseada.
- Aplicaciones:Adecuado para la producción de piezas planas o ligeramente curvadas con un espesor constante.
- Ventajas:Eficaz para la producción de grandes volúmenes, distribución uniforme del material.
- Desventajas:Limitado a geometrías más simples, puede requerir un procesamiento adicional para formas complejas.
Comprender los diferentes tipos de moldes de compresión y sus respectivas técnicas de moldeo es crucial para seleccionar el método adecuado para las necesidades específicas de fabricación.Cada tipo ofrece ventajas y retos únicos, por lo que es esencial tener en cuenta factores como la complejidad de la pieza, las propiedades del material y el volumen de producción a la hora de elegir el molde adecuado.
Tabla resumen:
Tipo | Diseño | Aplicaciones | Ventajas | Desventajas |
---|---|---|---|---|
Moldes flash | El material sobrante fluye fuera de la cavidad del molde durante la compresión. | Producción de gran volumen, geometrías sencillas. | Fácil de fabricar, rentable. | Desperdicio de material, postprocesado adicional. |
Moldes positivos | Cavidad completamente cerrada, sin escapes de material sobrante. | Piezas con tolerancias estrechas y formas complejas. | Alta precisión, mínimo desperdicio de material. | Fabricación compleja y costosa, requiere una alineación precisa. |
Positivo aterrizado | Variación de moldes positivos con una zona de aterrizaje para un espesor uniforme. | Piezas que requieren un espesor uniforme y una gran precisión dimensional. | Mayor control de las dimensiones, menor riesgo de sobrecompresión. | Mayor coste y complejidad en comparación con los moldes flash. |
Semi-Positivo | Combina las características de los moldes flash y positivos, flujo de material controlado. | Piezas que requieren precisión y flexibilidad en el flujo de material. | Equilibra la precisión y la eficiencia del material. | Más complejo que los moldes flash, puede requerir un ajuste fino. |
Moldeo a granel | Utiliza una mezcla de cargas, catalizadores, estabilizadores, pigmentos y fibras. | Piezas grandes y complejas de gran resistencia y durabilidad. | Propiedades mecánicas versátiles y mejoradas. | Requiere un control preciso de la composición del material y de las condiciones de moldeo. |
Moldeo de láminas | Chapas preformadas comprimidas en las formas deseadas. | Piezas planas o ligeramente curvadas con un grosor uniforme. | Eficaz para la producción de grandes volúmenes, distribución uniforme del material. | Limitado a geometrías más sencillas, puede requerir procesamiento adicional para formas complejas. |
¿Necesita ayuda para elegir el molde de compresión adecuado para su proyecto? Póngase en contacto con nuestros expertos para recibir asesoramiento personalizado.