Los reactores de lecho fluidizado (FBR) se utilizan ampliamente en la industria por sus ventajas, como la mezcla uniforme de partículas, los gradientes de temperatura y el funcionamiento continuo. Sin embargo, también presentan varias desventajas que pueden afectar su eficiencia, costo y escalabilidad. Estos incluyen un mayor tamaño de la vasija del reactor, mayores requisitos de bombeo, arrastre de partículas, erosión de componentes internos y desafíos relacionados con la comprensión del comportamiento de los materiales y los escenarios de pérdida de presión. Comprender estos inconvenientes es crucial para que las industrias tomen decisiones informadas sobre su aplicación y desarrollen estrategias para mitigar estos problemas.
Puntos clave explicados:
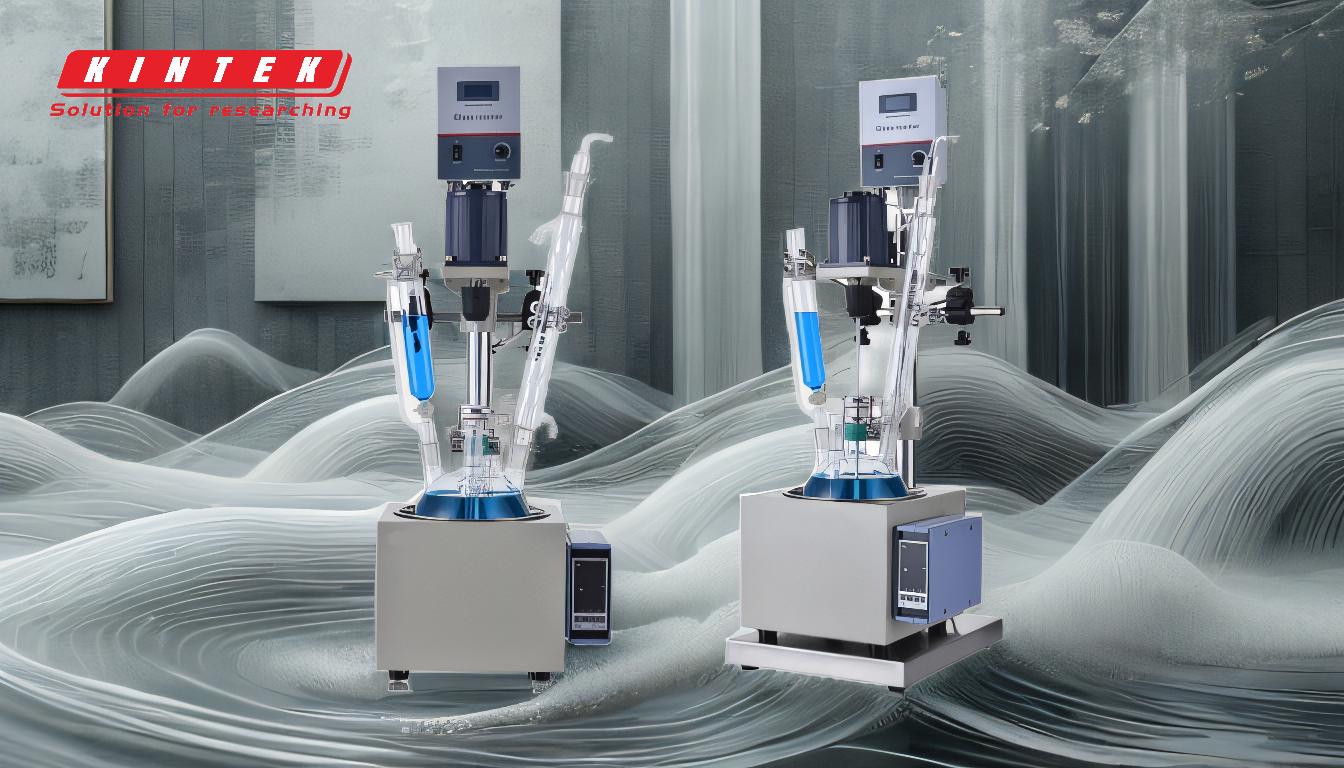
-
Aumento del tamaño de la vasija del reactor:
- Los reactores de lecho fluidizado requieren recipientes de mayor tamaño en comparación con otros tipos de reactores. Esto se debe a la necesidad de adaptarse al proceso de fluidización, que implica suspender partículas sólidas en un gas o líquido para crear un estado similar a un fluido. El mayor tamaño aumenta los costos de capital y los requisitos de espacio, lo que hace que los FBR sean menos adecuados para aplicaciones donde el espacio es limitado.
-
Mayores requisitos de bombeo y caída de presión:
- Mantener el estado de fluidización requiere un aporte de energía significativo, lo que genera mayores requisitos de bombeo. Esto resulta en mayores costos operativos. Además, la caída de presión en el reactor es mayor debido a la resistencia que ofrecen las partículas fluidizadas, lo que puede forzar aún más el sistema de bombeo y reducir la eficiencia general.
-
Arrastre de partículas:
- Uno de los desafíos importantes en los FBR es el arrastre de partículas, donde el gas fluidizante saca las partículas finas del reactor. Esto puede provocar pérdida de producto, contaminación de equipos posteriores y la necesidad de procesos de separación adicionales, como ciclones o filtros, para capturar y reciclar las partículas arrastradas.
-
Falta de comprensión actual del comportamiento material:
- El comportamiento de los materiales en un lecho fluidizado es complejo y aún no se comprende completamente. Esto incluye la dinámica del movimiento de partículas, la transferencia de calor y las reacciones químicas. La falta de modelos integrales y herramientas predictivas puede dificultar la optimización del diseño y la operación del reactor, lo que genera un rendimiento subóptimo y posibles riesgos para la seguridad.
-
Erosión de componentes internos:
- El movimiento continuo de partículas en un lecho fluidizado puede provocar la erosión de los componentes internos, como las paredes del reactor, las placas distribuidoras y los intercambiadores de calor. Esta erosión puede generar requisitos de mantenimiento frecuentes, mayor tiempo de inactividad y mayores costos operativos. En casos severos, puede comprometer la integridad estructural del reactor.
-
Escenarios de pérdida de presión:
- Los FBR son susceptibles a escenarios de pérdida de presión, donde el proceso de fluidización se interrumpe, lo que provoca una distribución desigual de las partículas y un rendimiento deficiente del reactor. Esto puede ocurrir debido a cambios en las condiciones operativas, como variaciones en el caudal de gas o la distribución del tamaño de las partículas. Los escenarios de pérdida de presión pueden dar lugar a una reducción de la calidad del producto, un mayor consumo de energía y posibles riesgos de seguridad.
En resumen, si bien los reactores de lecho fluidizado ofrecen varias ventajas, como una mezcla uniforme y control de temperatura, también presentan desafíos importantes que deben gestionarse con cuidado. Estos incluyen un mayor tamaño del reactor, mayores requisitos de energía, arrastre de partículas, incertidumbres sobre el comportamiento de los materiales, erosión de los componentes y problemas de pérdida de presión. Abordar estas desventajas mediante un diseño mejorado, materiales avanzados y un mejor control de procesos puede ayudar a maximizar los beneficios de las RBA en aplicaciones industriales.
Tabla resumen:
Desventaja | Descripción |
---|---|
Aumento del tamaño de la vasija del reactor | Los buques más grandes aumentan los costos de capital y los requisitos de espacio. |
Mayores requisitos de bombeo | Se necesita un importante aporte de energía, lo que genera mayores costes operativos. |
Arrastre de partículas | Se desprenden partículas finas, provocando pérdidas de producto y riesgos de contaminación. |
Erosión de componentes internos | El movimiento continuo de partículas erosiona las piezas del reactor, aumentando los costos de mantenimiento. |
Escenarios de pérdida de presión | Las interrupciones en la fluidización reducen la eficiencia y plantean riesgos para la seguridad. |
¿Necesita ayuda para abordar los desafíos de los reactores de lecho fluidizado? Póngase en contacto con nuestros expertos hoy ¡Para soluciones personalizadas!