Los imanes se colocan detrás del blanco en el sputtering para aumentar la eficiencia y eficacia del proceso de deposición.Al crear un campo magnético, los electrones quedan atrapados cerca de la superficie del blanco, lo que aumenta la longitud de su trayectoria y la probabilidad de colisiones ionizantes con el gas argón.El resultado es una mayor densidad del plasma y una mayor velocidad de sputtering, lo que permite una deposición más rápida y uniforme de la capa fina a presiones más bajas.El campo magnético también ayuda a contener el plasma cerca del objetivo, reduciendo el bombardeo de electrones sobre el sustrato y evitando daños térmicos.En general, los imanes mejoran la eficacia del sputtering, la velocidad de deposición y la calidad de la película.
Explicación de los puntos clave:
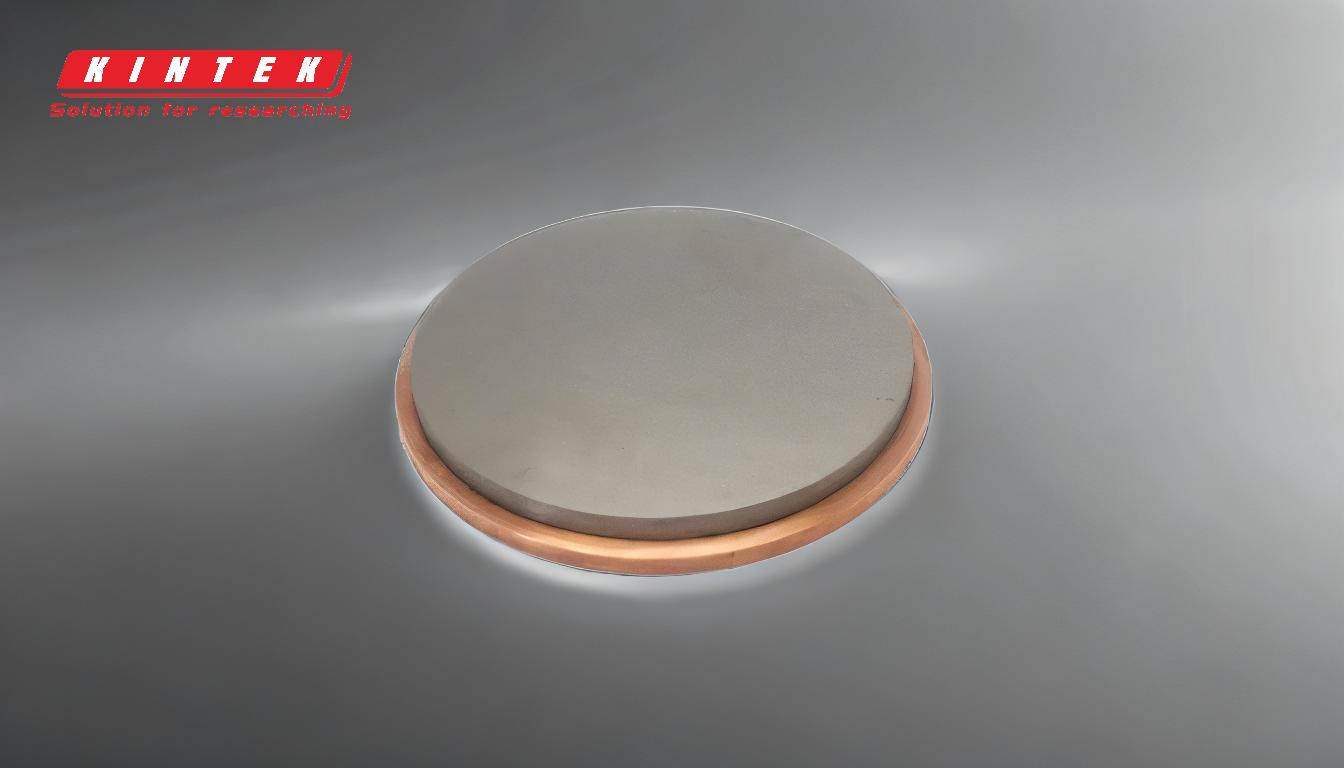
-
Contención del plasma y mejora de la ionización:
- Los imanes crean un campo magnético que atrapa electrones secundarios cerca de la superficie del blanco.
- Los electrones giran en espiral alrededor de las líneas del campo magnético, aumentando la longitud de su trayectoria y el número de colisiones ionizantes con el gas argón.
- Esto aumenta la ionización del plasma cerca del blanco, lo que conduce a una mayor densidad de iones de argón.
- Una mayor densidad de iones aumenta la probabilidad de colisiones entre los iones de argón y el material objetivo, aumentando la velocidad de sputtering.
-
Aumento de la tasa de sputtering:
- El campo magnético acelera la ionización del gas argón, aumentando el número de iones de argón disponibles para bombardear el blanco.
- Un mayor número de iones de argón que golpean el blanco provoca una mayor tasa de expulsión de material de la superficie del blanco.
- Esto conduce a una deposición más rápida de la película fina sobre el sustrato.
-
Menor presión de funcionamiento:
- La mayor ionización cerca del objetivo permite mantener el plasma a presiones más bajas.
- Una menor presión reduce el número de colisiones en fase gaseosa, lo que permite que los átomos pulverizados se desplacen más directamente al sustrato.
- El resultado es un proceso de deposición más eficaz con menos defectos en la película fina.
-
Reducción del bombardeo de electrones sobre el sustrato:
- El campo magnético confina el plasma cerca del objetivo, reduciendo el número de electrones que llegan al sustrato.
- Esto minimiza el daño térmico al sustrato y mejora la calidad de la película depositada.
-
Erosión uniforme del blanco:
- Los imanes ayudan a crear un patrón de erosión estable y uniforme en la superficie objetivo.
- La erosión uniforme garantiza velocidades de deposición y espesores de película uniformes en todo el sustrato.
- Esto es crucial para conseguir películas finas de alta calidad y reproducibles.
-
Crecimiento mejorado de películas finas:
- El campo magnético aumenta el porcentaje de material objetivo que se ioniza.
- Es más probable que los átomos ionizados interactúen con otras partículas y se depositen en el sustrato.
- Esto mejora la eficiencia del proceso de deposición, permitiendo que las películas finas crezcan más rápida y uniformemente.
-
Eficiencia energética:
- Al atrapar electrones y potenciar la ionización, los imanes reducen la energía necesaria para mantener el plasma.
- Esto hace que el proceso de sputtering sea más eficiente energéticamente, reduciendo los costes operativos.
-
Versatilidad en las aplicaciones:
- El uso de imanes en el sputtering permite la deposición de una amplia gama de materiales, incluidos metales, semiconductores y aislantes.
- Esta versatilidad hace del sputtering por magnetrón una técnica preferida en diversas industrias, como la electrónica, la óptica y los recubrimientos.
En resumen, los imanes colocados detrás del blanco en el sputtering desempeñan un papel crucial en la mejora de la eficacia, uniformidad y calidad del proceso de deposición de películas finas.Lo consiguen atrapando electrones, aumentando la densidad del plasma y mejorando la ionización, todo lo cual contribuye a una deposición más rápida y controlada de los materiales sobre el sustrato.
Cuadro resumen:
Beneficio clave | Explicación |
---|---|
Contención del plasma | Los imanes atrapan electrones, aumentando la ionización y la densidad del plasma cerca del objetivo. |
Mayor velocidad de sputtering | La mayor densidad de iones de argón acelera la expulsión de material para una deposición más rápida. |
Menor presión de funcionamiento | La ionización mejorada permite una deposición eficaz a presiones reducidas. |
Reducción del daño al sustrato | El confinamiento del plasma minimiza el bombardeo de electrones, evitando daños térmicos. |
Erosión uniforme del blanco | Garantiza velocidades de deposición y espesores de película uniformes. |
Crecimiento mejorado de la película fina | Los átomos ionizados se asientan de forma más eficiente, mejorando la calidad de la película. |
Eficiencia energética | Reduce la energía necesaria para mantener el plasma, disminuyendo los costes operativos. |
Aplicaciones versátiles | Adecuado para depositar metales, semiconductores y aislantes. |
¿Desea optimizar su proceso de sputtering? Póngase en contacto con nuestros expertos para obtener más información.