La pulverización catódica es una técnica muy utilizada en la deposición de películas finas y, de hecho, es posible pulverizar silicio.Este proceso consiste en utilizar un blanco de silicio y seguir los pasos estándar del sputtering para depositar una fina capa de silicio sobre un sustrato.El proceso aprovecha los principios del bombardeo iónico y la transferencia de energía para expulsar átomos de silicio del blanco, que luego se depositan sobre el sustrato para formar una fina película.A continuación, desglosaremos los aspectos clave del sputtering de silicio, incluidos los pasos del proceso, las consideraciones y las aplicaciones.
Explicación de los puntos clave:
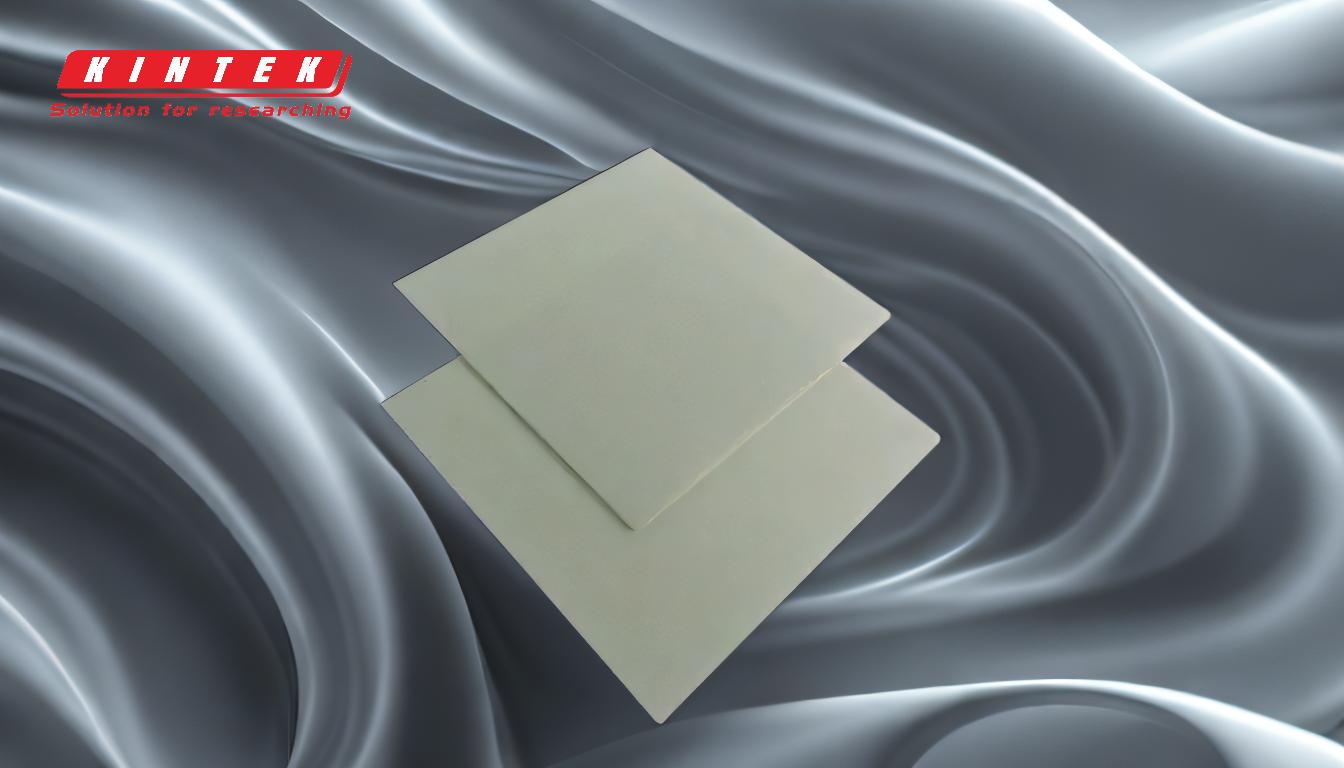
-
Visión general del proceso de sputtering:
- El sputtering es una técnica de deposición física de vapor (PVD) en la que un material objetivo (en este caso, silicio) es bombardeado con iones de alta energía de un gas inerte, normalmente argón.
- La colisión entre los iones de argón y el objetivo de silicio expulsa átomos neutros de silicio, que viajan a través del vacío y se depositan sobre un sustrato para formar una fina película.
-
Pasos para la pulverización catódica de silicio:
- Creación de vacío:La cámara de reacción se evacua a una presión de aproximadamente 1 Pa para eliminar la humedad y las impurezas, garantizando un entorno limpio para la deposición.
- Introducción del gas inerte:Se introduce gas argón en la cámara para crear una atmósfera de baja presión, esencial para ionizar el gas.
- Calentamiento:La cámara se calienta a temperaturas comprendidas entre 150°C y 750°C, en función de las propiedades deseadas de la película de silicio.
- Creación del campo magnético:Se colocan herramientas entre el blanco de silicio y un electroimán para generar un campo magnético, que potencia la ionización del gas argón.
- Ionización y bombardeo:Se aplica un alto voltaje para ionizar los átomos de argón, creando iones de argón cargados positivamente.El blanco de silicio está cargado negativamente y atrae los iones de argón.Estos iones colisionan con el blanco de silicio, expulsando átomos de silicio.
- Deposición de la película:Los átomos de silicio expulsados viajan a través del vacío y se depositan sobre el sustrato, formando una fina película de silicio.
-
Consideraciones para la pulverización catódica de silicio:
- Pureza objetivo:La calidad del blanco de silicio es fundamental.Se necesitan blancos de silicio de alta pureza para garantizar que la película depositada tenga las propiedades eléctricas y estructurales deseadas.
- Preparación del sustrato:El sustrato debe estar limpio y debidamente preparado para garantizar una buena adherencia y uniformidad de la película de silicio.
- Parámetros del proceso:Parámetros como la presión del gas, la temperatura y el voltaje deben controlarse cuidadosamente para conseguir las propiedades deseadas de la película.
-
Aplicaciones del silicio pulverizado:
- Fabricación de semiconductores:Las películas de silicio pulverizado se utilizan en la producción de circuitos integrados y otros dispositivos semiconductores.
- Recubrimientos ópticos:Las películas de silicio se utilizan en aplicaciones ópticas, como revestimientos antirreflectantes y espejos.
- Células solares:El silicio pulverizado se utiliza en la fabricación de células solares de película fina.
En resumen, el pulverizado de silicio es un proceso bien establecido que implica varios pasos cuidadosamente controlados para depositar una fina película de silicio sobre un sustrato.Esta técnica se utiliza ampliamente en industrias como la fabricación de semiconductores, la óptica y la energía solar.Si se conocen los pasos y consideraciones clave, se puede utilizar eficazmente el sputtering para producir películas de silicio de alta calidad para diversas aplicaciones.
Tabla resumen:
Aspecto | Detalles |
---|---|
Resumen del proceso | Deposición física en fase vapor (PVD) que utiliza iones de argón para expulsar átomos de silicio. |
Pasos | Creación de vacío, introducción de gas inerte, calentamiento, creación de campo magnético. |
Consideraciones clave | Pureza del blanco, preparación del sustrato, parámetros de proceso controlados. |
Aplicaciones | Fabricación de semiconductores, revestimientos ópticos, células solares de película fina. |
Descubra cómo el sputtering de silicio puede mejorar sus proyectos. contacte hoy mismo con nuestros expertos ¡!