Los elementos calefactores pueden dejar de funcionar por diversas razones, que van desde la degradación física hasta problemas de funcionamiento.Las causas principales son la formación de puntos calientes, la oxidación debida al funcionamiento intermitente, la fragilización por crecimiento del grano y la contaminación o corrosión.Además, los problemas eléctricos, como disyuntores activados, fusibles fundidos o interruptores defectuosos, pueden impedir que la energía llegue al elemento calefactor, dejándolo inoperativo.Comprender estos mecanismos de fallo es crucial para mantener la longevidad y eficacia de los elementos calefactores en diversas aplicaciones.
Explicación de los puntos clave:
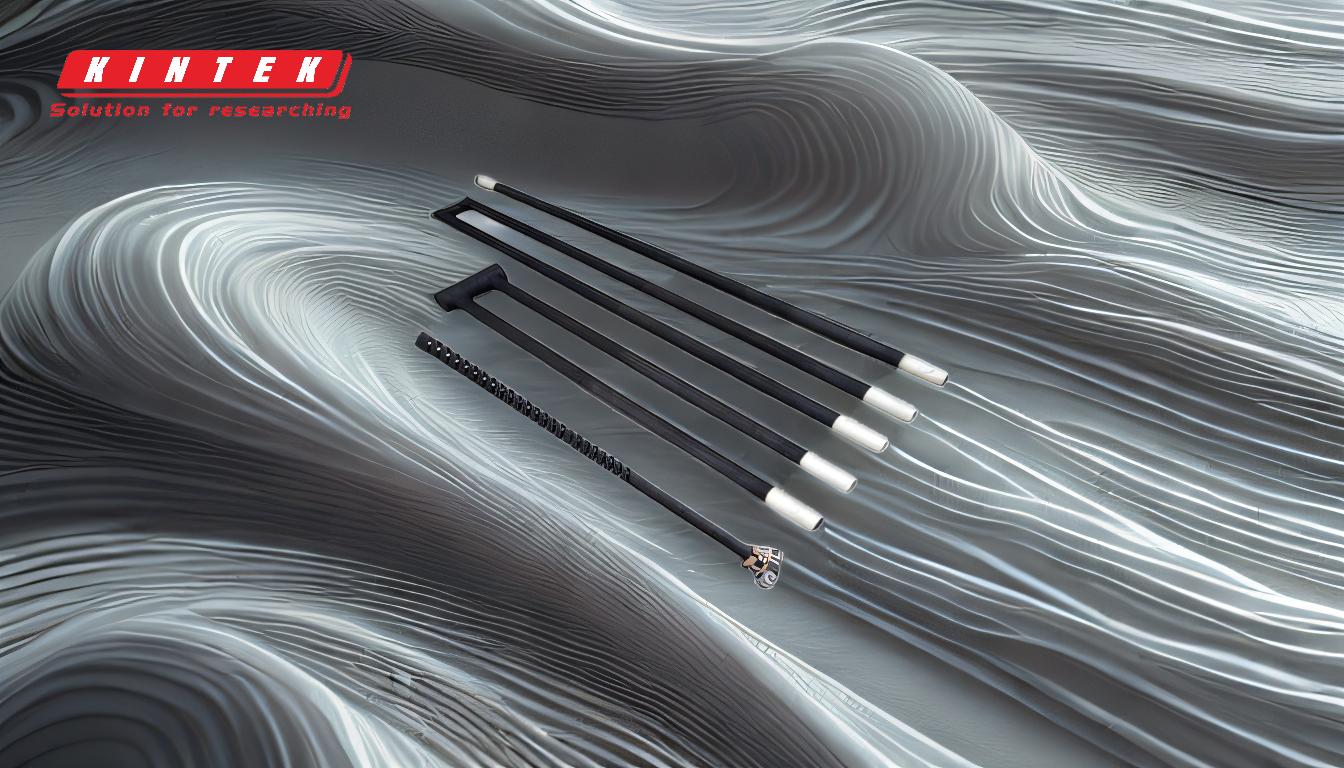
-
Formación de puntos calientes
- Descripción:Los puntos calientes se producen cuando determinadas zonas del elemento calefactor se calientan mucho más que el resto.Esto puede deberse a una elevada oxidación local o al apantallamiento por los soportes.
- Impacto:Estas altas temperaturas localizadas pueden provocar una degradación acelerada y, finalmente, el fallo del elemento calefactor.
- Prevención:Garantizar un calentamiento uniforme y una colocación adecuada de los soportes puede ayudar a mitigar la formación de puntos calientes.
-
Oxidación e intermitencia de funcionamiento
- Descripción:Los frecuentes ciclos de calentamiento y enfriamiento hacen que la capa de óxido del elemento calefactor se agriete y se desprenda, exponiendo el metal fresco a una mayor oxidación.
- Impacto:Este proceso debilita el elemento con el paso del tiempo, provocando su rotura.
- Prevención:Minimizar los cambios rápidos de temperatura y utilizar materiales con mayor resistencia a la oxidación puede prolongar la vida útil del elemento.
-
Fragilización debida al crecimiento del grano
- Descripción:Las aleaciones que se calientan, especialmente las que contienen hierro, pueden formar granos grandes y quebradizos a altas temperaturas.
- Impacto:Esta fragilización hace que el elemento sea más susceptible de agrietarse y romperse bajo tensión.
- Prevención:El uso de aleaciones diseñadas para resistir el crecimiento del grano y el mantenimiento de temperaturas de funcionamiento óptimas pueden ayudar a prevenir la fragilización.
-
Contaminación y corrosión
- Descripción:La exposición a gases o humos corrosivos en el entorno del horno puede contaminar los elementos calefactores, provocando corrosión seca.
- Impacto:La contaminación y la corrosión degradan el material, reduciendo su eficacia y provocando fallos.
- Prevención:Una ventilación adecuada y el uso de materiales resistentes a la corrosión pueden proteger los elementos de la contaminación.
-
Problemas eléctricos
- Descripción:Los problemas de alimentación eléctrica, como disyuntores disparados, fusibles fundidos o interruptores defectuosos, pueden impedir que el elemento calefactor reciba alimentación.
- Impacto:Sin alimentación, el elemento calefactor no puede funcionar, independientemente de su estado físico.
- Prevención:Las comprobaciones periódicas de mantenimiento del sistema eléctrico y la sustitución inmediata de los componentes defectuosos pueden garantizar un suministro eléctrico constante.
Al abordar estos puntos clave, los usuarios pueden comprender mejor los posibles modos de fallo de los elementos calefactores y tomar medidas proactivas para prevenirlos, garantizando un funcionamiento fiable y eficiente a largo plazo.
Tabla resumen:
Causa del fallo | Descripción | Impacto | Prevención |
---|---|---|---|
Formación de puntos calientes | Altas temperaturas localizadas debidas a la oxidación o al apantallamiento por los soportes. | Degradación acelerada y fallo. | Asegurar un calentamiento uniforme y una colocación adecuada del soporte. |
Oxidación | Los frecuentes ciclos de calentamiento/enfriamiento agrietan la capa de óxido, dejando al descubierto metal fresco. | Debilita el elemento con el tiempo. | Minimizar los cambios bruscos de temperatura; utilizar materiales resistentes a la oxidación. |
Fragilización | Formación de granos grandes y quebradizos al calentar las aleaciones a altas temperaturas. | Aumento de la susceptibilidad al agrietamiento y la rotura. | Utilizar aleaciones resistentes al crecimiento del grano; mantener temperaturas de funcionamiento óptimas. |
Contaminación/Corrosión | La exposición a gases o humos corrosivos contamina el elemento. | Degradación y fallo del material. | Implemente una ventilación adecuada; utilice materiales resistentes a la corrosión. |
Problemas eléctricos | Los disyuntores disparados, los fusibles fundidos o los interruptores defectuosos impiden el suministro eléctrico. | El elemento calefactor no puede funcionar sin corriente. | Realice comprobaciones periódicas del sistema eléctrico; sustituya rápidamente los componentes defectuosos. |
¿Necesita ayuda para mantener o sustituir sus elementos calefactores? Póngase en contacto con nuestros expertos para obtener soluciones a medida.