El sputtering y el metalizado son técnicas utilizadas para depositar películas finas sobre sustratos, pero difieren significativamente en sus mecanismos, procesos y aplicaciones.El sputtering es un tipo de deposición física en fase vapor (PVD) que consiste en bombardear un material con iones energéticos para expulsar átomos que se depositan sobre un sustrato.En cambio, el metalizado suele implicar procesos electroquímicos en los que los iones metálicos de una solución se reducen y depositan sobre un sustrato.El sputtering no requiere fundir el material de partida y funciona a presiones de gas más altas, mientras que el metalizado se basa en reacciones químicas y suele requerir un medio líquido.Ambos métodos se utilizan en sectores como la electrónica, la óptica y los revestimientos, pero su elección depende de los requisitos específicos de la aplicación.
Explicación de los puntos clave:
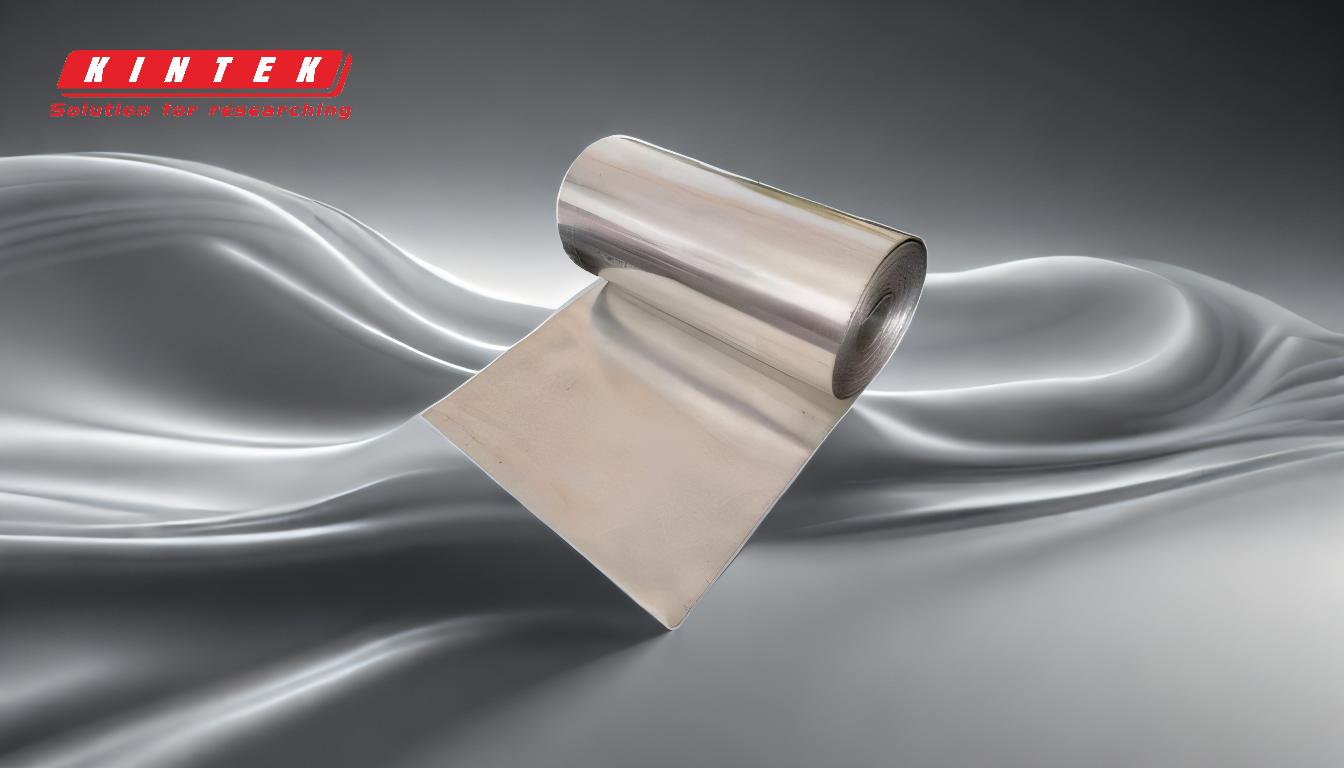
-
Mecanismo de deposición:
- Pulverización catódica:Consiste en el uso de iones energéticos (normalmente de un plasma) para bombardear un material objetivo, provocando la expulsión de átomos del objetivo debido a la transferencia de momento.Estos átomos expulsados se desplazan y depositan sobre un sustrato para formar una fina película.El proceso no requiere que el material objetivo se funda.
- Revestimiento:Normalmente se basa en procesos electroquímicos.Los iones metálicos de una solución se reducen en la superficie del sustrato, formando un revestimiento metálico.Este proceso suele implicar una corriente eléctrica para impulsar la reacción de reducción.
-
Entorno del proceso:
- Pulverización catódica:Funciona en un entorno de vacío o de baja presión con gases inertes (por ejemplo, argón).El proceso puede producirse a presiones de gas más elevadas (5-15 mTorr), en las que las partículas pulverizadas pueden sufrir colisiones en fase gaseosa antes de alcanzar el sustrato.
- Revestimiento:Suele tener lugar en un medio líquido (solución electrolítica).El sustrato se sumerge en la solución y los iones metálicos se depositan en su superficie mediante reacciones electroquímicas.
-
Fuente de energía:
- Pulverización catódica:Utiliza energía eléctrica para generar un plasma, que produce los iones energéticos necesarios para bombardear el material objetivo.El proceso se basa en el bombardeo físico y no en la energía térmica.
- Revestimiento:Se basa en la energía eléctrica para impulsar la reducción de los iones metálicos en la solución.La energía se utiliza para facilitar las reacciones químicas que depositan el metal sobre el sustrato.
-
Velocidad y control de la deposición:
- Pulverización catódica:Generalmente tiene una tasa de deposición inferior en comparación con otros métodos de PVD como la evaporación térmica.Sin embargo, ofrece un excelente control sobre la composición y uniformidad de la película, lo que lo hace adecuado para aplicaciones precisas.
- Revestimiento:Puede alcanzar altos índices de deposición, especialmente en procesos de galvanoplastia.El espesor y la uniformidad del revestimiento pueden controlarse ajustando parámetros como la densidad de corriente y el tiempo de revestimiento.
-
Compatibilidad de materiales:
- Pulverización catódica:Puede depositar una amplia gama de materiales, incluidos metales, aleaciones y cerámicas.Es especialmente útil para materiales con altos puntos de fusión que son difíciles de evaporar.
- Revestimiento:Se utiliza principalmente para depositar metales y aleaciones.El proceso se limita a materiales que pueden disolverse en una solución electrolítica y reducirse sobre el sustrato.
-
Aplicaciones:
- Pulverización catódica:Se utiliza habitualmente en la industria de semiconductores, revestimientos ópticos y células solares de película fina.También se emplea en la creación de revestimientos duros para herramientas y revestimientos decorativos.
- Revestimiento:Muy utilizado en industrias como la automoción (para la resistencia a la corrosión), la electrónica (para capas conductoras) y la joyería (para acabados decorativos).
-
Ventajas y limitaciones:
-
Pulverización catódica:
- Ventajas:Alta precisión, capacidad para depositar materiales complejos, buena adherencia y uniformidad.
- Limitaciones:Menor velocidad de deposición, mayor coste de los equipos y necesidad de un entorno de vacío.
-
Revestimiento:
- Ventajas:Altos índices de deposición, rentabilidad para la producción a gran escala y capacidad para revestir geometrías complejas.
- Limitaciones:Limitado a sustratos conductores, posibilidad de problemas medioambientales debido a los residuos químicos y menor control sobre la composición de la película en comparación con el sputtering.
-
Pulverización catódica:
En resumen, el sputtering y el metalizado son técnicas de deposición distintas con mecanismos, entornos y aplicaciones únicos.El sputtering destaca por su precisión y versatilidad de materiales, mientras que el metalizado es preferible por su rapidez y rentabilidad en la deposición de metales a gran escala.La elección entre uno y otro depende de los requisitos específicos de la aplicación, como las propiedades deseadas del material, la velocidad de deposición y las características del sustrato.
Cuadro sinóptico:
Aspecto | Pulverización catódica | Metalizado |
---|---|---|
Mecanismo | Deposición física en fase vapor (PVD) que utiliza iones energéticos para expulsar los átomos objetivo. | Reducción electroquímica de iones metálicos en una solución. |
Entorno | Vacío o baja presión con gases inertes. | Medio líquido (solución electrolítica). |
Fuente de energía | Energía eléctrica para generar plasma. | Energía eléctrica para impulsar las reacciones de reducción. |
Velocidad de deposición | Menor velocidad, mayor precisión. | Velocidad más alta, adecuada para la producción a gran escala. |
Compatibilidad de materiales | Metales, aleaciones, cerámica. | Principalmente metales y aleaciones. |
Aplicaciones | Semiconductores, revestimientos ópticos, células solares. | Automoción, electrónica, joyería. |
Ventajas | Alta precisión, versatilidad de materiales, buena adherencia. | Alta velocidad de deposición, rentable para la producción a gran escala. |
Limitaciones | Menor velocidad de deposición, mayor coste de los equipos, necesidad de vacío. | Limitada a sustratos conductores, problemas medioambientales por los residuos químicos. |
¿Necesita ayuda para elegir la técnica de deposición adecuada? Póngase en contacto con nuestros expertos para recibir asesoramiento personalizado.