La pirólisis de plásticos es un proceso que convierte los residuos plásticos en productos valiosos como aceite de pirólisis, gas y carbón.El tipo de reactor utilizado en este proceso desempeña un papel fundamental a la hora de determinar la eficiencia, la escalabilidad y la idoneidad para tipos específicos de plásticos.Entre los reactores más comunes se encuentran los de lecho fluidizado, los de lecho fijo y los de ciclón, cada uno de ellos diseñado para diferentes procesos de pirólisis, como la pirólisis rápida o la lenta.Estos reactores están construidos con materiales resistentes a altas temperaturas, como el acero Q245R y Q345R, que garantizan la durabilidad y la eficacia de la transferencia de calor.La elección del reactor depende de factores como el tipo de materia prima, los productos deseados y los requisitos del proceso.
Explicación de los puntos clave:
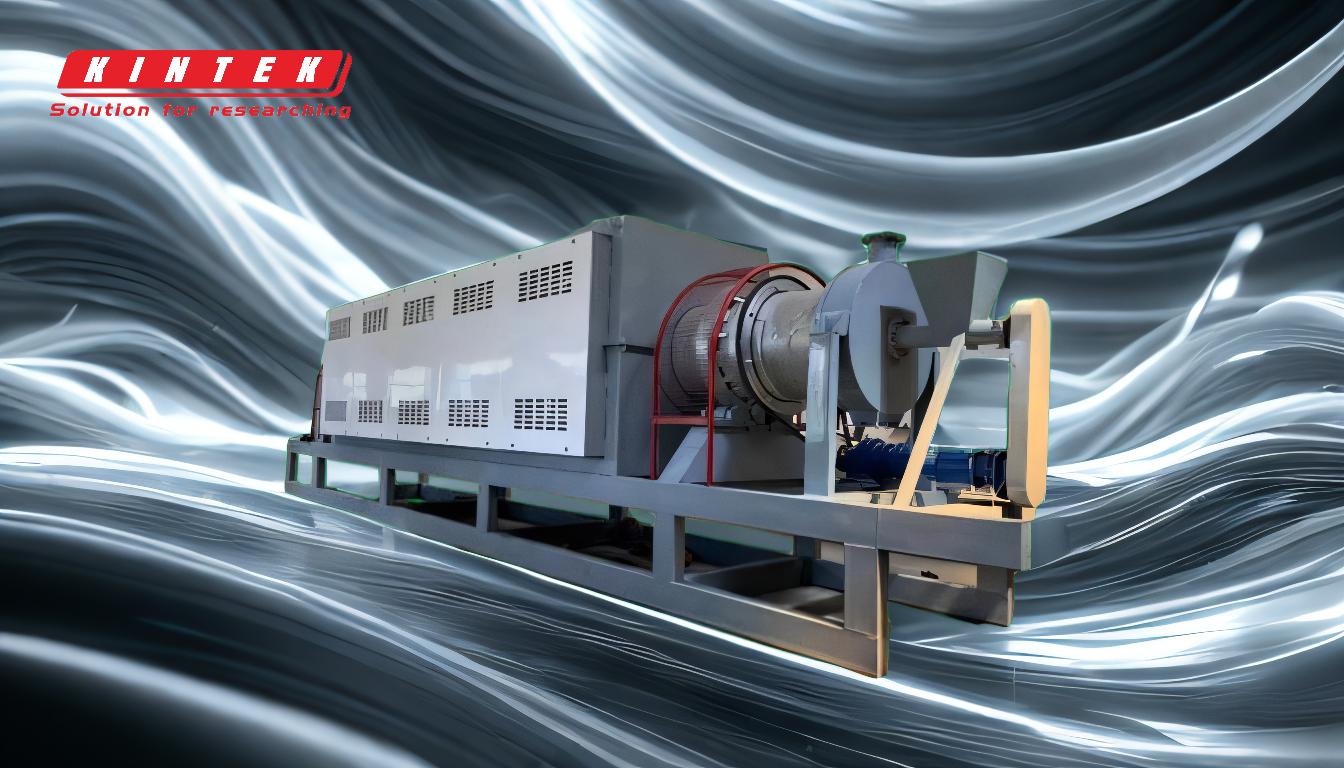
-
Tipos de reactores en la pirólisis de plásticos:
-
Reactores de lecho fluidizado:
- Estos reactores suspenden partículas de plástico en un gas o líquido, garantizando un calentamiento uniforme y una transferencia de calor eficaz.
- Son ideales para la pirólisis rápida debido a su capacidad para manejar altas velocidades de calentamiento y tiempos de residencia cortos.
- Entre los subtipos se incluyen los pirolizadores de lecho fluidizado burbujeante y los lechos fluidizados circulantes, que ofrecen un mayor control sobre la transferencia de calor y la manipulación de la materia prima.
-
Reactores de lecho fijo:
- Estos reactores utilizan un lecho estacionario de material, lo que los hace adecuados para procesos de pirólisis lentos.
- Su diseño y funcionamiento son más sencillos, pero pueden presentar limitaciones en cuanto a la eficacia de la transferencia de calor y la escalabilidad.
-
Reactores de ciclón:
- Estos reactores utilizan fuerzas centrífugas para separar y procesar materiales, lo que los hace eficaces para manipular partículas finas y garantizar un alto rendimiento.
- A menudo se utilizan junto con otros tipos de reactores para mejorar la eficacia global del sistema.
-
Reactores de lecho fluidizado:
-
Idoneidad de los materiales:
- Los reactores de pirólisis pueden procesar una amplia gama de plásticos, como HDPE, LDPE, PP, PS y PC.
- Sin embargo, plásticos como el PVC y el PET no son adecuados debido a su composición química, que puede liberar gases nocivos como el cloro durante la pirólisis.
-
Construcción y durabilidad:
- Los reactores suelen fabricarse con materiales resistentes a altas temperaturas, como el acero Q245R y Q345R.
- Estos materiales garantizan una vida útil de entre 5 y 8 años y mantienen la eficacia de la transferencia de calor, incluso en condiciones extremas.
-
Etapas del proceso de pirólisis de plásticos:
- El proceso comienza con la trituración y el secado de los residuos plásticos, seguido de un tratamiento previo para eliminar los contaminantes no plásticos.
- La fase de pirólisis consiste en calentar el plástico en el reactor para descomponerlo en aceite, gas y carbón.
- Los pasos posteriores a la pirólisis incluyen la destilación y purificación del aceite de pirólisis, seguido de su almacenamiento y envío.
-
Ventajas de los distintos tipos de reactores:
- Reactores de lecho fluidizado:Alta eficiencia de transferencia de calor, corto tiempo de residencia e idoneidad para pirólisis rápida.
- Reactores de lecho fijo:Simplicidad de diseño y funcionamiento, ideal para pirólisis lenta.
- Reactores de ciclón:Eficaz para manipular partículas finas y mejorar el rendimiento del sistema.
Al conocer los distintos tipos de reactores y sus aplicaciones específicas, los compradores de equipos pueden tomar decisiones informadas para optimizar sus procesos de pirólisis de plásticos.
Tabla resumen:
Tipo de reactor | Características principales | Lo mejor para |
---|---|---|
Lecho fluidizado | Alta transferencia de calor, corto tiempo de residencia, soporta altas velocidades de calentamiento | Pirólisis rápida |
Lecho fijo | Diseño sencillo, lecho fijo, fácil manejo | Pirólisis lenta |
Ciclón | Fuerza centrífuga, tratamiento de partículas finas, alto rendimiento | Procesamiento de partículas finas |
¿Está listo para optimizar su proceso de pirólisis de plásticos? Póngase en contacto con nuestros expertos para obtener soluciones a medida.