El moldeo por inyección es un proceso de fabricación utilizado para producir piezas inyectando material fundido en un molde.El proceso es muy eficaz y puede dividirse en cuatro etapas principales: sujeción, inyección, enfriamiento y expulsión.Cada etapa desempeña un papel fundamental para garantizar que el producto final cumpla las especificaciones deseadas.El ciclo completo suele durar entre 2 segundos y 2 minutos, dependiendo de la complejidad de la pieza y del material utilizado.A continuación, exploraremos cada etapa en detalle para proporcionar una comprensión global del proceso de moldeo por inyección.
Explicación de los puntos clave:
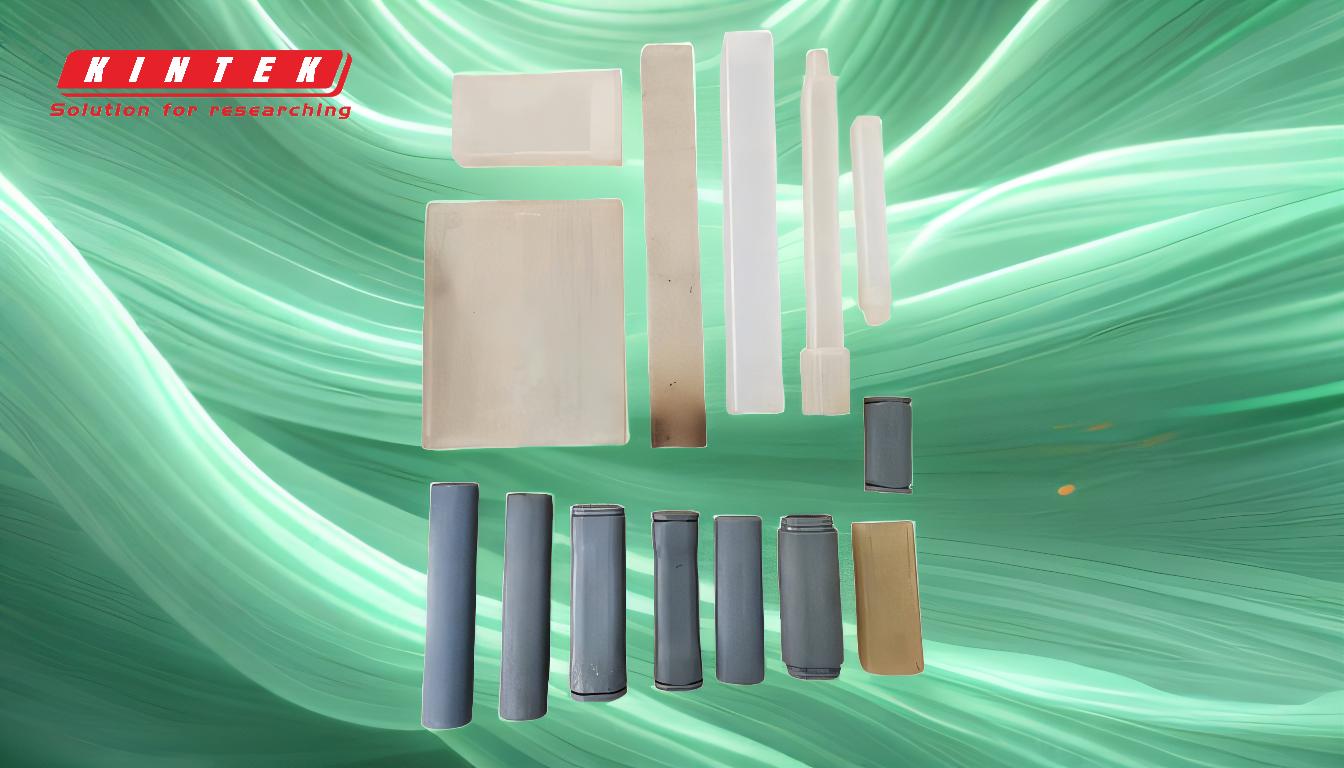
-
Etapa de sujeción
- Finalidad:La etapa de sujeción consiste en asegurar las dos mitades del molde para preparar la inyección del material fundido.
-
Proceso:
- El molde consta de dos mitades: la mitad fija (sujeta a la máquina de moldeo por inyección) y la mitad móvil (que se abre y se cierra).
- Una unidad de sujeción aplica presión para mantener las mitades del molde firmemente unidas durante el proceso de inyección.
- La fuerza de sujeción debe ser suficiente para soportar la presión del material inyectado, evitando cualquier fuga o deformación del molde.
- Importancia:Una sujeción adecuada garantiza que el molde permanezca cerrado y estable, lo que es fundamental para producir piezas de alta calidad con dimensiones precisas.
-
Etapa de inyección
- Propósito:En esta etapa, se inyecta material fundido en la cavidad del molde para formar la pieza deseada.
-
Proceso:
- El material (normalmente granulado de plástico) se introduce en un barril caliente, donde se funde y homogeneiza.
- Un tornillo o émbolo alternativo empuja el material fundido en la cavidad del molde a alta presión.
- El material llena la cavidad y adopta la forma del molde.
-
Factores a tener en cuenta:
- La presión de inyección, la velocidad y la temperatura deben controlarse cuidadosamente para garantizar que el material llene el molde por completo y de manera uniforme.
- El llenado excesivo o insuficiente del molde puede provocar defectos como alabeos, marcas de hundimiento o piezas incompletas.
- Importancia:La etapa de inyección determina la forma inicial y la integridad de la pieza, por lo que es un paso crítico en el proceso.
-
Etapa de enfriamiento
- Propósito:Después de llenar el molde, el material debe enfriarse y solidificarse para mantener su forma.
-
Proceso:
- El enfriamiento comienza en cuanto se inyecta el material en el molde.
- El molde está diseñado con canales de refrigeración por los que circula un refrigerante (normalmente agua) para disipar el calor.
- El tiempo de enfriamiento depende de las propiedades del material, el grosor de la pieza y el diseño del molde.
-
Factores a tener en cuenta:
- Un enfriamiento insuficiente puede provocar deformaciones o tensiones internas en la pieza.
- Un enfriamiento excesivo puede aumentar la duración del ciclo, reduciendo la eficacia de la producción.
- Importancia:Una refrigeración adecuada garantiza que la pieza se solidifique correctamente, manteniendo la precisión dimensional y la integridad estructural.
-
Etapa de expulsión
- Propósito:Una vez que la pieza se ha enfriado y solidificado, se expulsa del molde.
-
Proceso:
- El molde se abre y los pasadores o placas eyectoras empujan la pieza fuera de la cavidad del molde.
- A continuación, la pieza se retira de la máquina, manual o automáticamente.
-
Factores a tener en cuenta:
- La expulsión debe realizarse con cuidado para evitar dañar la pieza o el molde.
- El diseño adecuado del molde, incluida la colocación de los pasadores eyectores, es crucial para garantizar una expulsión sin problemas.
- Importancia:La etapa de expulsión completa el ciclo, lo que permite preparar el molde para la siguiente inyección.
Consideraciones adicionales para los compradores de equipos y consumibles:
- Selección de materiales:El tipo de material utilizado (por ejemplo, termoplásticos, polímeros termoestables) afecta al proceso de moldeo y a las propiedades del producto final.
- Diseño del molde:Un molde bien diseñado con canales de refrigeración y mecanismos de expulsión adecuados es esencial para una producción eficiente.
- Especificaciones de la máquina:La máquina de moldeo por inyección debe tener la fuerza de cierre, la presión de inyección y la capacidad de refrigeración adecuadas para satisfacer los requisitos específicos de la pieza.
- Optimización del tiempo de ciclo:Reducir la duración de los ciclos manteniendo la calidad es clave para mejorar la eficacia de la producción y reducir los costes.
Al comprender estas etapas y su importancia, los compradores de equipos y consumibles pueden tomar decisiones informadas para optimizar el proceso de moldeo por inyección para sus necesidades específicas.
Tabla resumen:
Etapa | Objetivo | Proceso clave | Importancia |
---|---|---|---|
Sujeción | Asegurar las mitades del molde para la inyección | Aplica fuerza de sujeción para mantener el molde firmemente; evita fugas o deformaciones | Garantiza la estabilidad del molde y unas dimensiones precisas de la pieza |
Inyección | Inyectar material fundido en la cavidad del molde | Fundir el material, introducirlo en el molde a alta presión; controlar la presión, la velocidad y la temperatura | Determina la forma y la integridad de la pieza; fundamental para obtener resultados sin defectos |
Enfriamiento | Solidificar el material para mantener la forma | Hacer circular el refrigerante por los canales del molde; controlar el tiempo de enfriamiento en función del material y el grosor de la pieza | Garantiza la precisión dimensional y la integridad estructural; evita la deformación |
Expulsión | Retirar la pieza solidificada del molde | Abre el molde y utiliza clavijas/placas eyectoras para empujar la pieza hacia fuera; garantiza una expulsión suave | Completa el ciclo; prepara el molde para la siguiente inyección |
¿Está preparado para optimizar su proceso de moldeo por inyección? Póngase en contacto con nuestros expertos para obtener soluciones a medida.