El moldeo por inyección es un proceso de fabricación muy utilizado para producir piezas de plástico, y la elección entre un diseño de molde de 2 placas o de 3 placas influye significativamente en el proceso de producción, la calidad de la pieza y el coste.La principal diferencia radica en la estructura del molde, el sistema de inyección y el mecanismo de expulsión.Un molde de 2 placas es más sencillo y rentable, y suele utilizar compuertas laterales para introducir el material en la cavidad.Por el contrario, un molde de 3 placas es más complejo, ya que permite la introducción de material en cualquier punto de la cavidad, lo que resulta especialmente útil para diseños complejos o piezas grandes con orificios centrales.Esta flexibilidad hace que los moldes de 3 placas sean ideales para aplicaciones de alta precisión, pero tiene un coste y una complejidad mayores.
Explicación de los puntos clave:
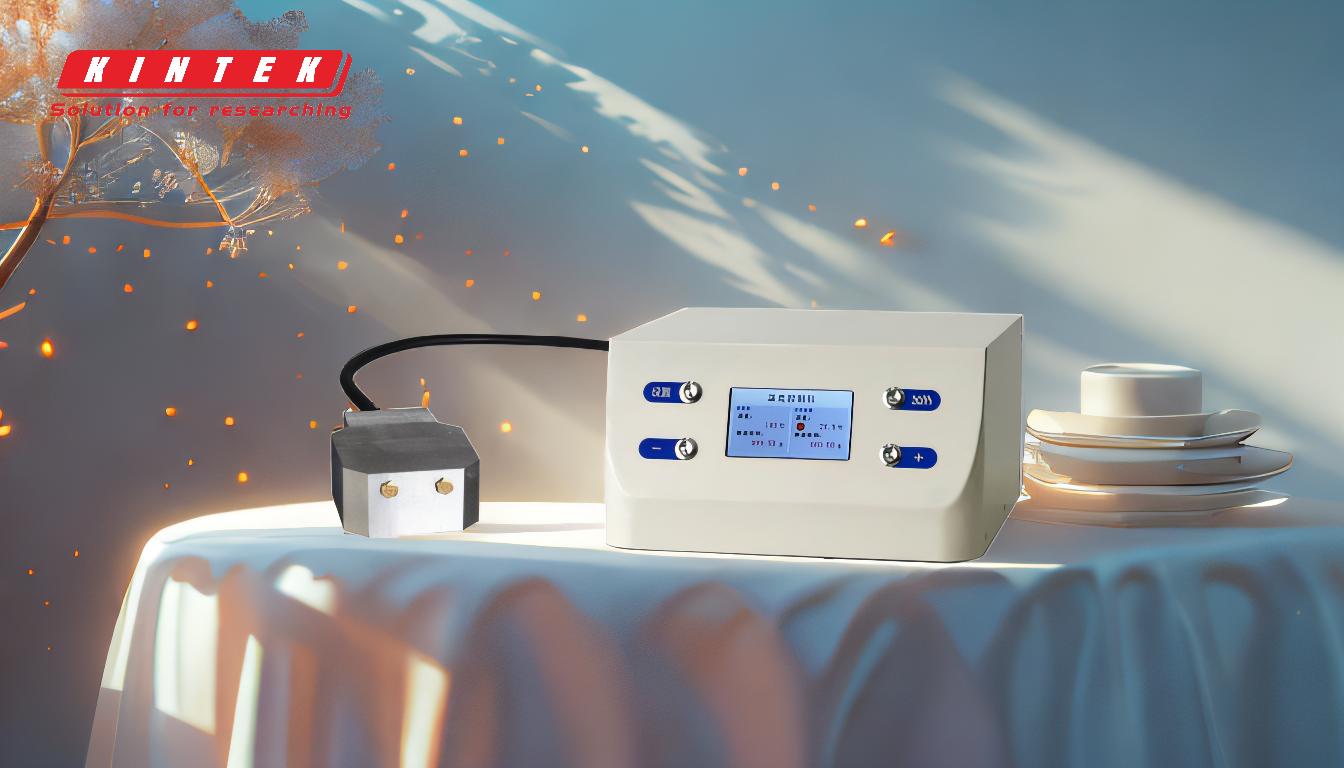
-
Estructura del molde:
- Molde de 2 placas:Consta de dos placas principales: la placa de cavidad y la placa de núcleo.Este diseño es más simple y sencillo, lo que facilita su fabricación y mantenimiento.
- Molde de 3 placas:Incluye una placa adicional (la placa de rodadura) entre las placas de cavidad y de núcleo.Esta placa adicional permite sistemas de compuerta más complejos y un mejor control del flujo de material.
-
Sistema de compuertas:
- Molde de 2 placas:Normalmente utiliza compuertas laterales, que introducen material en la cavidad desde el borde exterior.Es adecuado para piezas más sencillas, pero puede dejar marcas visibles.
- Molde de 3 placas:Permite inyectar material en cualquier punto de la cavidad.Es ideal para piezas complejas o que requieran gran precisión, ya que minimiza las marcas de la compuerta y permite una mejor distribución del material.
-
Mecanismo de expulsión:
- Molde de 2 placas:El mecanismo de expulsión es más sencillo, normalmente con pasadores eyectores que empujan la pieza fuera del molde después de enfriarse.
- Molde de 3 placas:La placa de canal adicional complica el proceso de expulsión, por lo que a menudo se requiere un sistema más sofisticado para separar la pieza del canal y la compuerta.
-
Aplicaciones:
- Molde de 2 placas:El más adecuado para piezas más sencillas en las que el coste y la facilidad de fabricación son las principales preocupaciones.Se utiliza habitualmente en la producción de grandes volúmenes de piezas menos complejas.
- Molde de 3 placas:Ideal para piezas complejas, de gran tamaño o que requieren una colocación precisa del material.Suelen utilizarse en aplicaciones en las que la calidad y la precisión de la pieza son críticas, como en dispositivos médicos o componentes de automoción.
-
Coste y complejidad:
- Molde de 2 placas:Generalmente menos costoso y más fácil de diseñar y fabricar.Los menores costes de mantenimiento y un funcionamiento más sencillo lo convierten en una opción rentable para muchas aplicaciones.
- Molde de 3 placas:Más caro debido a la placa adicional y a los sistemas de inyección y expulsión más complejos.Costes de mantenimiento y funcionamiento más elevados, pero justificados para piezas de alta precisión o complejas.
-
Eficacia del material:
- Molde de 2 placas:Puede resultar en más desperdicio de material debido al sistema de compuerta lateral, que puede dejar marcas de compuerta más grandes y requerir más recorte.
- Molde de 3 placas:Más eficiente en cuanto al material, ya que la inyección milimétrica minimiza el desperdicio y permite un mejor control de la distribución del material, reduciendo la necesidad de postprocesado.
En resumen, la elección entre un molde de inyección de 2 o 3 placas depende de la complejidad de la pieza, la precisión requerida y las limitaciones presupuestarias.Mientras que los moldes de 2 placas son más sencillos y rentables, los moldes de 3 placas ofrecen mayor flexibilidad y precisión, por lo que son adecuados para aplicaciones más exigentes.
Tabla resumen:
Característica | Molde de 2 placas | Molde de 3 placas |
---|---|---|
Estructura del molde | 2 placas (cavidad y núcleo) | 3 placas (cavidad, canal y núcleo) |
Sistema de compuertas | Puertas laterales | Compuertas puntuales |
Mecanismo de expulsión | Más sencillo, pasadores eyectores | Sistemas más complejos y avanzados |
Aplicaciones | Piezas más sencillas, producción de gran volumen | Piezas complejas, necesidades de alta precisión |
Coste y complejidad | Menor coste, diseño más sencillo | Mayor coste, diseño más complejo |
Eficiencia del material | Más residuos, marcas más grandes | Menos residuos, marcas mínimas |
¿Necesita ayuda para elegir el molde de inyección adecuado para su proyecto? Póngase en contacto hoy mismo con nuestros expertos para un asesoramiento personalizado.