La principal diferencia entre un molde de 2 placas y uno de 3 placas radica en su diseño, sistemas de inyección y aplicaciones.Un molde de 2 placas es más sencillo y suele utilizar compuertas laterales para introducir material en la cavidad desde el exterior, por lo que es adecuado para piezas sencillas.Por el contrario, un molde de 3 placas es más complejo, ya que permite la inyección puntual en cualquier punto de la cavidad, lo que resulta ideal para diseños complejos o piezas que requieran varias entradas.El molde de 3 placas también separa el sistema de canales de la pieza, lo que permite una mayor flexibilidad en la ubicación de las compuertas y un mejor control del flujo de material.Ambos moldes presentan distintas ventajas en función de los requisitos del producto.
Explicación de los puntos clave:
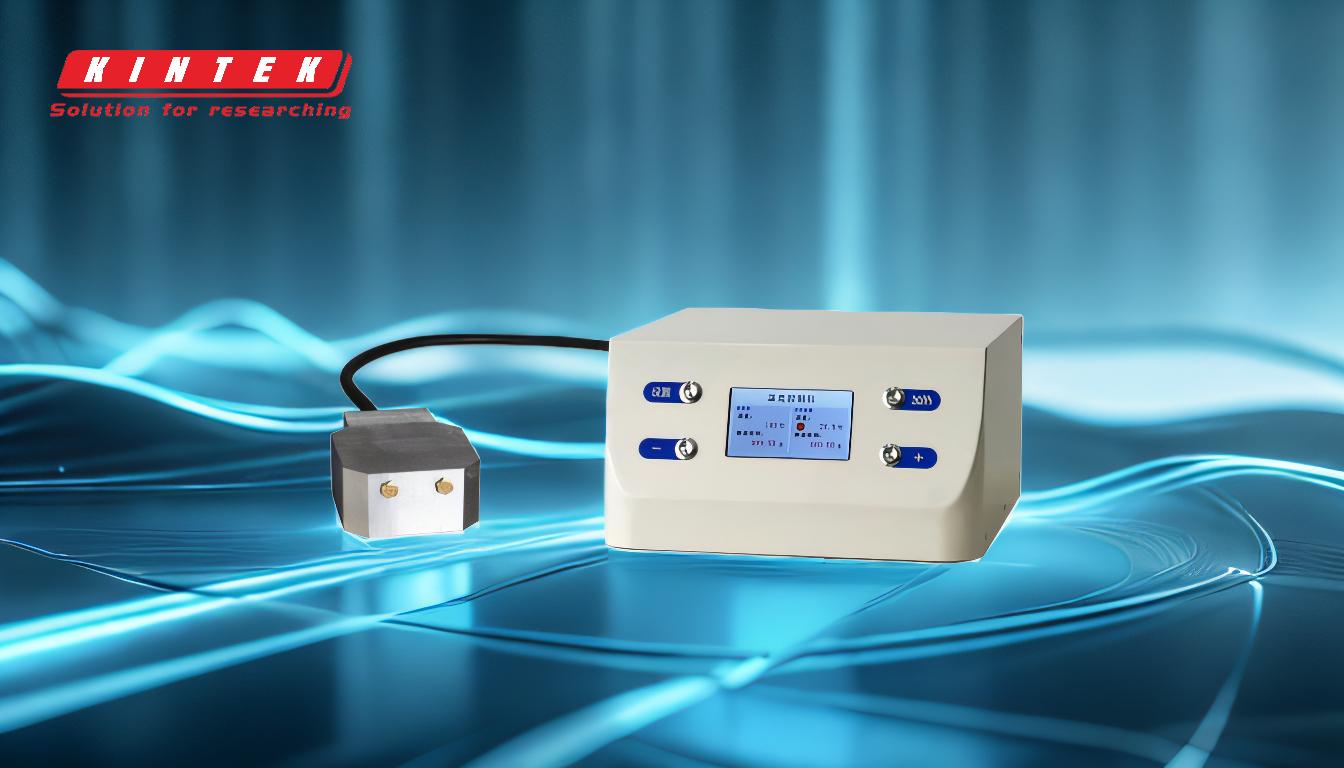
-
Complejidad del diseño:
- Molde de 2 placas:Este diseño consta de dos placas principales: la placa de cavidad y la placa de núcleo.Es más sencillo y fácil de fabricar, por lo que resulta rentable para piezas sencillas.
- Molde de 3 placas:Este diseño incluye una placa adicional entre las placas de cavidad y de núcleo, que separa el sistema de canal de la pieza.La complejidad añadida permite mecanismos de inyección y expulsión más precisos.
-
Sistemas de compuerta:
- Molde de 2 placas:Normalmente utiliza compuertas laterales, que introducen material en la cavidad desde el lado exterior.Es adecuado para piezas que no requieren una inyección compleja o múltiples puntos de inyección.
- Molde de 3 placas:Permite la colocación de compuertas puntuales en cualquier punto de la cavidad.Esta flexibilidad es beneficiosa para piezas complejas que requieren varias compuertas o un control preciso del flujo de material.
-
Aplicaciones:
- Molde de 2 placas:El más adecuado para piezas sencillas con requisitos mínimos de inyección.Se suele utilizar para productos que no tienen grandes orificios ni diseños intrincados en el centro.
- Molde de 3 placas:Ideal para piezas complejas con grandes orificios o diseños intrincados en el centro.La posibilidad de abrir desde cualquier punto de la cavidad lo hace versátil para una amplia gama de aplicaciones.
-
Flujo y control de materiales:
- Molde de 2 placas:El flujo de material suele ser directo, con menos control sobre los puntos de inyección.Esto puede dar lugar a problemas como líneas de soldadura o distribución desigual del material en piezas complejas.
- Molde de 3 placas:Ofrece un mejor control del flujo de material, reduciendo el riesgo de defectos.La separación del sistema de canales de la pieza permite una inyección y expulsión más precisas.
-
Coste y mantenimiento:
- Molde de 2 placas:Generalmente menos costosa de fabricar y mantener debido a su diseño más sencillo.Es una solución rentable para la producción de grandes volúmenes de piezas sencillas.
- Molde de 3 placas:Más caro de producir y mantener debido a su complejidad.Sin embargo, el coste añadido puede justificarse en el caso de piezas que requieran un control preciso del material.
-
Mecanismo de expulsión:
- Molde de 2 placas:El mecanismo de expulsión es sencillo y suele utilizar pasadores eyectores para empujar la pieza fuera del molde.
- Molde de 3 placas:La placa adicional permite mecanismos de expulsión más complejos, lo que puede ser beneficioso para piezas con diseños intrincados o múltiples socavados.
En resumen, la elección entre un molde de 2 o 3 placas depende de la complejidad de la pieza, del sistema de inyección necesario y del nivel de control que se necesite sobre el flujo de material.Mientras que los moldes de 2 placas son más sencillos y rentables para piezas sencillas, los moldes de 3 placas ofrecen mayor flexibilidad y precisión para diseños complejos.
Tabla resumen:
Característica | Molde de 2 placas | Molde de 3 placas |
---|---|---|
Complejidad del diseño | Diseño más sencillo, 2 placas principales | Más complejo, 3 placas con separación del canal |
Sistema de compuertas | Compuertas laterales para la alimentación de la cavidad exterior | Compuertas puntuales para un flujo preciso del material |
Aplicaciones | Ideal para piezas sencillas | Ideal para diseños complejos e intrincados |
Control del material | Menos control, posibilidad de defectos | Mejor control, menor riesgo de defectos |
Coste y mantenimiento | Menor coste, mantenimiento más sencillo | Mayor coste, mantenimiento más complejo |
Mecanismo de expulsión | Pasadores de expulsión sencillos | Mecanismos complejos para piezas complejas |
¿Necesita ayuda para elegir el molde adecuado para su proyecto? Póngase en contacto con nuestros expertos para un asesoramiento personalizado.