Los recubrimientos CVD (deposición química de vapor) y PVD (deposición física de vapor) se utilizan ampliamente en diversas industrias para mejorar las propiedades superficiales de los materiales. El espesor de estos recubrimientos es un factor crítico que influye en su rendimiento y aplicación. Los recubrimientos CVD generalmente varían desde nanómetros hasta menos de 20 micrones, mientras que los recubrimientos PVD suelen ser más delgados, desde 0,25 micrones hasta 5 micrones. Ambos métodos ofrecen ventajas únicas según las propiedades deseadas, como dureza, suavidad y resistencia a la corrosión. La elección entre CVD y PVD a menudo depende de los requisitos específicos de la aplicación, incluido el material del sustrato, las propiedades de recubrimiento deseadas y las condiciones operativas.
Puntos clave explicados:
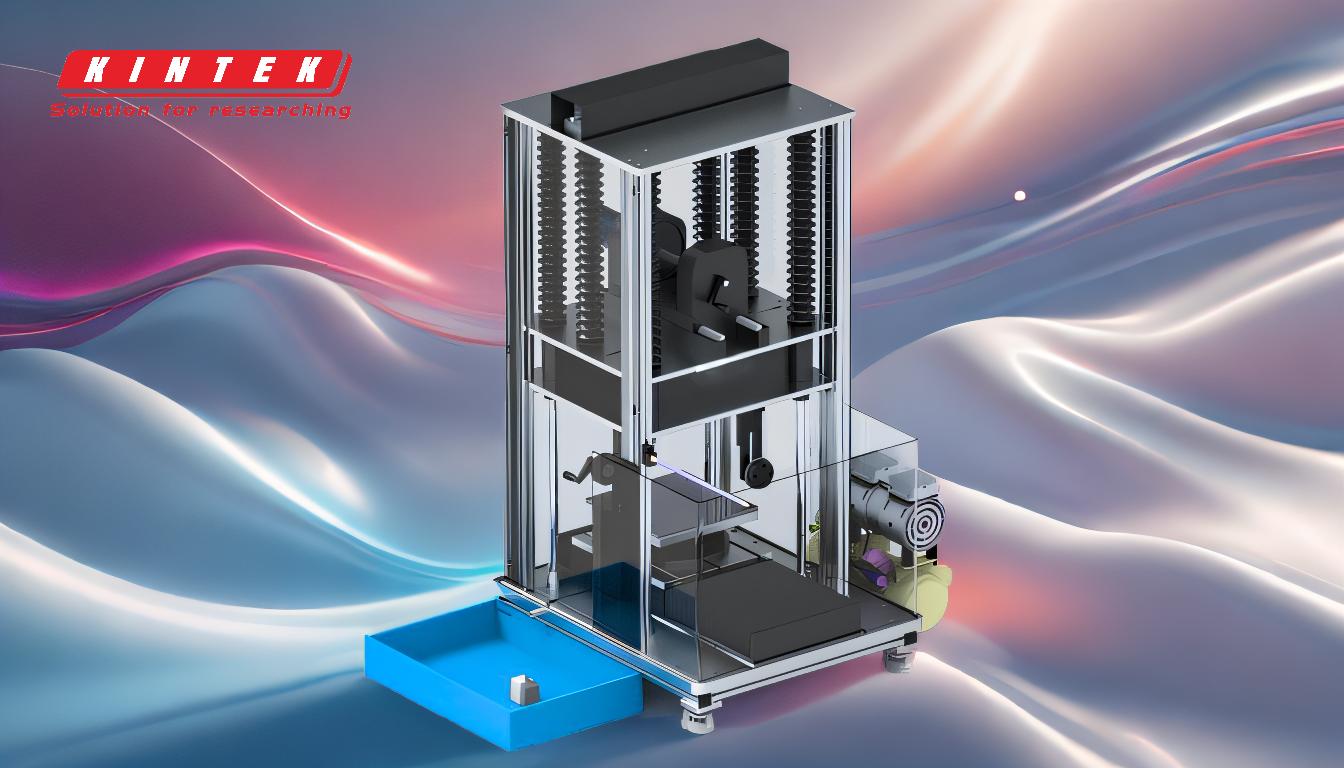
-
Rangos de espesor típicos:
- Recubrimientos CVD: Los métodos CVD pueden depositar capas de películas delgadas que van desde nanómetros hasta menos de 20 micrones. Esta amplia gama permite flexibilidad en aplicaciones que requieren recubrimientos más gruesos.
- Recubrimientos PVD: Los recubrimientos PVD son generalmente más delgados y suelen oscilar entre 0,25 micrones y 5 micrones. Esta delgadez garantiza que los recubrimientos no alteren significativamente las dimensiones o especificaciones de las piezas diseñadas.
-
Factores que influyen en el espesor del recubrimiento:
- ECV: El espesor de los recubrimientos CVD puede verse influenciado por varios parámetros, incluido el tipo de sustrato, la temperatura del sustrato, la composición química de los gases reactivos y la presión total del flujo de gas. Estos factores se pueden ajustar para lograr el espesor y las propiedades del recubrimiento deseados.
- PVD: El espesor de los recubrimientos PVD depende del tipo de material de recubrimiento y del proceso PVD específico utilizado. Incluso si los recubrimientos están hechos del mismo material, el método de aplicación puede afectar significativamente su rendimiento y propiedades.
-
Aplicaciones y beneficios:
- ECV: Debido a su capacidad para depositar recubrimientos más gruesos, el CVD se utiliza a menudo en aplicaciones que requieren mayor durabilidad y resistencia al desgaste y la corrosión. Los revestimientos más gruesos pueden proporcionar una mejor protección en entornos hostiles.
- PVD: La naturaleza delgada de los recubrimientos PVD los hace ideales para aplicaciones donde es crucial mantener las dimensiones y apariencia originales de la pieza. Los recubrimientos PVD se utilizan comúnmente para mejorar propiedades como suavidad, dureza y resistencia a la corrosión sin alterar la apariencia de la pieza.
-
Comparación de espesor:
- CVD frente a PVD: Mientras que los recubrimientos CVD pueden ser significativamente más gruesos (hasta 20 micrones), los recubrimientos PVD son generalmente mucho más delgados (de 0,25 a 5 micrones). Esta diferencia de espesor es una consideración clave a la hora de elegir entre los dos métodos para una aplicación específica.
-
Rendimiento y Propiedades:
- ECV: Los recubrimientos más gruesos proporcionados por CVD pueden ofrecer un rendimiento superior en términos de resistencia al desgaste y durabilidad. Sin embargo, el proceso puede requerir temperaturas más altas y equipos más complejos.
- PVD: Los recubrimientos PVD, al ser más delgados, son excelentes para aplicaciones que requieren un control preciso sobre el espesor del recubrimiento y un impacto mínimo en las dimensiones de la pieza. También son conocidos por su excelente adherencia y uniformidad.
En resumen, el espesor de los recubrimientos CVD y PVD varía significativamente: el CVD ofrece recubrimientos más gruesos adecuados para aplicaciones más exigentes, mientras que el PVD proporciona recubrimientos más delgados ideales para aplicaciones estéticas y de precisión. La elección entre los dos métodos depende de los requisitos específicos de la aplicación, incluidas las propiedades deseadas y las condiciones operativas.
Tabla resumen:
Aspecto | Recubrimientos CVD | Recubrimientos PVD |
---|---|---|
Rango de espesor | Nanómetros a < 20 micras | 0,25 a 5 micras |
Factores clave que influyen | Tipo de sustrato, temperatura, composición del gas, presión. | Material de revestimiento, tipo de proceso PVD |
Aplicaciones | Durabilidad, resistencia al desgaste, protección contra la corrosión. | Precisión, suavidad, mínimo cambio dimensional. |
Actuación | Resistencia al desgaste superior, durabilidad | Excelente adherencia, uniformidad y delgadez. |
¿Necesita ayuda para elegir el método de recubrimiento adecuado para su aplicación? ¡Póngase en contacto con nuestros expertos hoy!