La fundición de moldes cerámicos es un proceso de fundición de precisión utilizado para crear piezas metálicas complejas y detalladas. Consiste en crear un molde cerámico aplicando una lechada cerámica a un patrón de molde, dejándola secar y retirando después la lechada seca para formar el molde. A continuación, el molde se cura eliminando los volátiles mediante calentamiento a baja temperatura y se endurece en un horno a alta temperatura. Este proceso es ideal para producir piezas con detalles finos, superficies lisas y gran precisión dimensional. A continuación encontrará un desglose detallado de los pasos clave de la fundición de moldes cerámicos.
Explicación de los puntos clave:
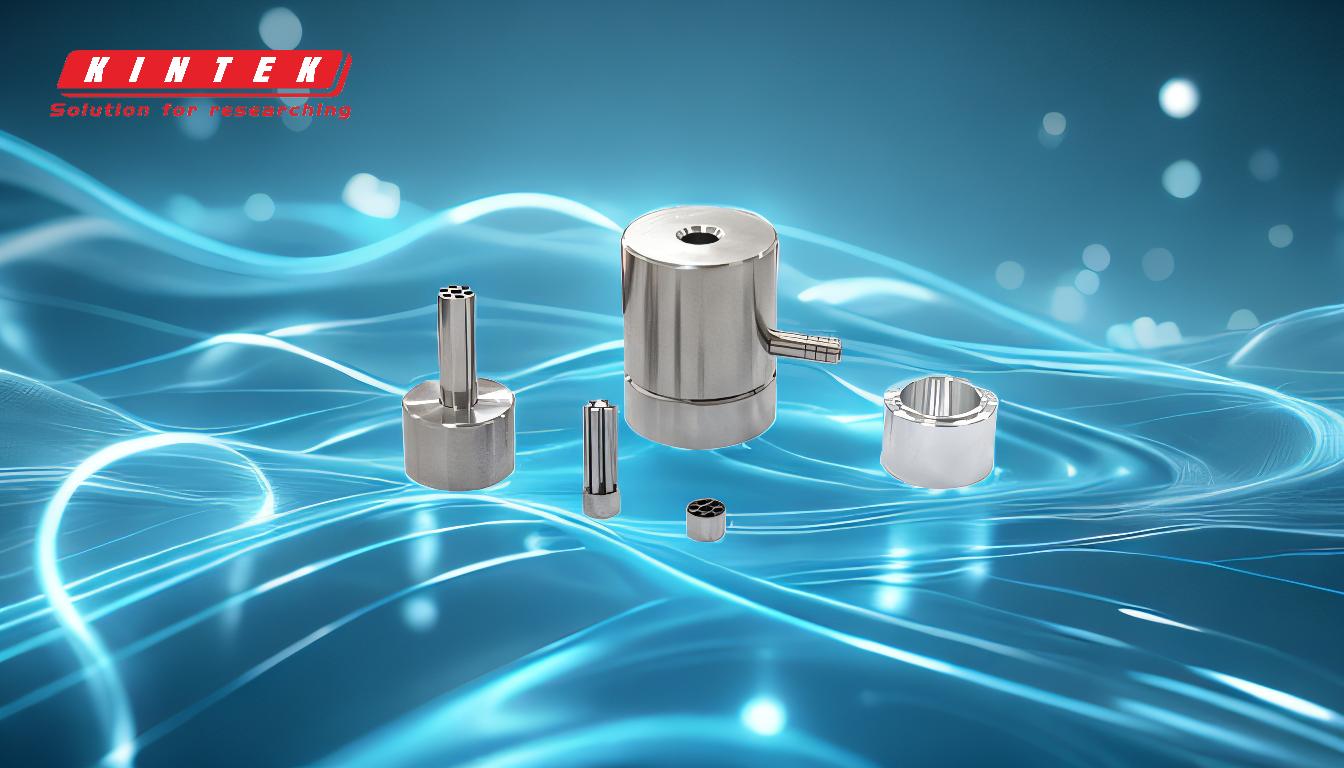
-
Aplicar y solidificar la lechada cerámica sobre el patrón del molde:
- El proceso comienza con la preparación de una lechada cerámica, que es una mezcla de partículas cerámicas finas y un aglutinante líquido. Esta pasta se aplica a un molde, normalmente de cera, plástico o metal, que tiene la forma del producto final.
- La pasta se aplica cuidadosamente sobre el molde para garantizar una cobertura uniforme y captar todos los detalles del molde. Una vez aplicada, la pasta se deja secar y solidificar, formando una capa de cerámica alrededor del modelo.
-
Retire la pasta seca para crear un molde para el objeto deseado:
- Una vez que la pasta cerámica se ha secado y solidificado, el siguiente paso es retirar el molde. Esto se hace normalmente fundiendo, quemando o disolviendo el material del patrón, dejando tras de sí un molde hueco de cerámica que replica la forma del patrón original.
- Este paso es crucial, ya que garantiza que el molde represente con exactitud la forma y los detalles del producto final. El proceso de extracción debe realizarse con cuidado para evitar dañar el delicado molde de cerámica.
-
Elimine los volátiles colocando el molde en un horno a baja temperatura o utilizando un soplete de llama:
- Una vez retirado el patrón del molde, es posible que el molde cerámico aún contenga sustancias volátiles, como humedad residual o aglutinantes orgánicos, que deben eliminarse antes de que el molde pueda utilizarse para la fundición.
- El molde se coloca en un horno a baja temperatura o se expone a un soplete de llama para expulsar lentamente estos volátiles. Este paso, conocido como desparafinado o quemado, garantiza que el molde esté libre de cualquier sustancia que pueda causar defectos en la pieza de fundición final.
-
Endurecimiento del molde en un horno de alta temperatura:
- Una vez eliminados los volátiles, el molde cerámico se endurece aún más calentándolo en un horno de alta temperatura. Este paso, conocido como sinterización, refuerza el material cerámico y lo prepara para soportar las altas temperaturas del metal fundido durante la fundición.
- El proceso de sinterización también ayuda a eliminar cualquier porosidad restante en el molde cerámico, garantizando una superficie lisa y sin defectos en la pieza de fundición final.
-
Vertido del metal fundido en el molde cerámico:
- Una vez que el molde cerámico está totalmente preparado, está listo para el proceso de fundición. El metal fundido se vierte en el molde, llenando la cavidad y adoptando la forma del patrón original.
- El molde está diseñado para soportar las altas temperaturas del metal fundido, garantizando que la pieza final conserve todos los intrincados detalles y dimensiones del patrón original.
-
Enfriamiento y extracción de la pieza fundida:
- Después de verter el metal fundido en el molde, se deja enfriar y solidificar. Una vez que el metal se ha enfriado, el molde cerámico se desmolda con cuidado para mostrar la pieza fundida final.
- El molde cerámico suele destruirse durante este proceso, ya que está diseñado para ser un molde de un solo uso. Sin embargo, el alto nivel de detalle y precisión que se consigue con la fundición de moldes cerámicos lo convierte en un proceso valioso para producir piezas metálicas complejas y de alta calidad.
-
Acabado posterior a la fundición:
- Tras extraer la pieza del molde, puede someterse a procesos de acabado adicionales, como esmerilado, pulido o tratamiento térmico, para conseguir el acabado superficial y las propiedades mecánicas deseados.
- Estos pasos de acabado garantizan que la pieza final cumpla las especificaciones requeridas y esté lista para su uso en la aplicación prevista.
En resumen, la fundición de moldes cerámicos es un proceso de fundición muy preciso y detallado que implica la creación de un molde cerámico a partir de un patrón, el curado y endurecimiento del molde y, a continuación, el colado de metal fundido en el molde para producir una pieza final. El proceso es ideal para crear piezas complejas e intrincadas con gran precisión dimensional y superficies lisas.
Tabla resumen:
Paso | Descripción |
---|---|
1. Aplicar lechada cerámica | Recubra un patrón de molde con lechada cerámica para capturar detalles finos. |
2. 2. Retirar el molde | Derrita o disuelva el patrón para dejar un molde hueco de cerámica. |
3. Eliminar volátiles | Utilice un calentamiento a baja temperatura o un soplete de llama para eliminar las sustancias residuales. |
4. Endurecer el molde | Sinterice el molde en un horno de alta temperatura para obtener resistencia y suavidad. |
5. Verter el metal fundido | Llene el molde cerámico con metal fundido para formar la pieza final. |
6. Enfriar y retirar la pieza | Rompa el molde cerámico para descubrir la pieza fundida acabada. |
7. Acabado posterior a la fundición | Desbaste, pulido o tratamiento térmico de la pieza para obtener las propiedades deseadas. |
Descubra cómo la fundición de moldes cerámicos puede mejorar su producción. póngase en contacto con nuestros expertos hoy mismo ¡!