Un calcinador es un equipo especializado de procesamiento térmico utilizado principalmente en aplicaciones industriales y metalúrgicas para calentar materiales a altas temperaturas por debajo de sus puntos de fusión.Su objetivo principal es eliminar impurezas volátiles, como agua, dióxido de carbono o dióxido de azufre, de minerales metálicos u otras sustancias.Este proceso, conocido como calcinación, es fundamental en industrias como la de producción de cemento, donde la piedra caliza se calcina para producir clínker, un ingrediente clave del hormigón.Además, los calcinadores se utilizan para el secado, la oxidación y las transformaciones químicas, lo que los convierte en herramientas versátiles en el procesamiento de materiales.Funcionan en entornos de alta temperatura, a menudo en hornos rotatorios, y son esenciales para conseguir las propiedades y la pureza deseadas de los materiales.
Explicación de los puntos clave:
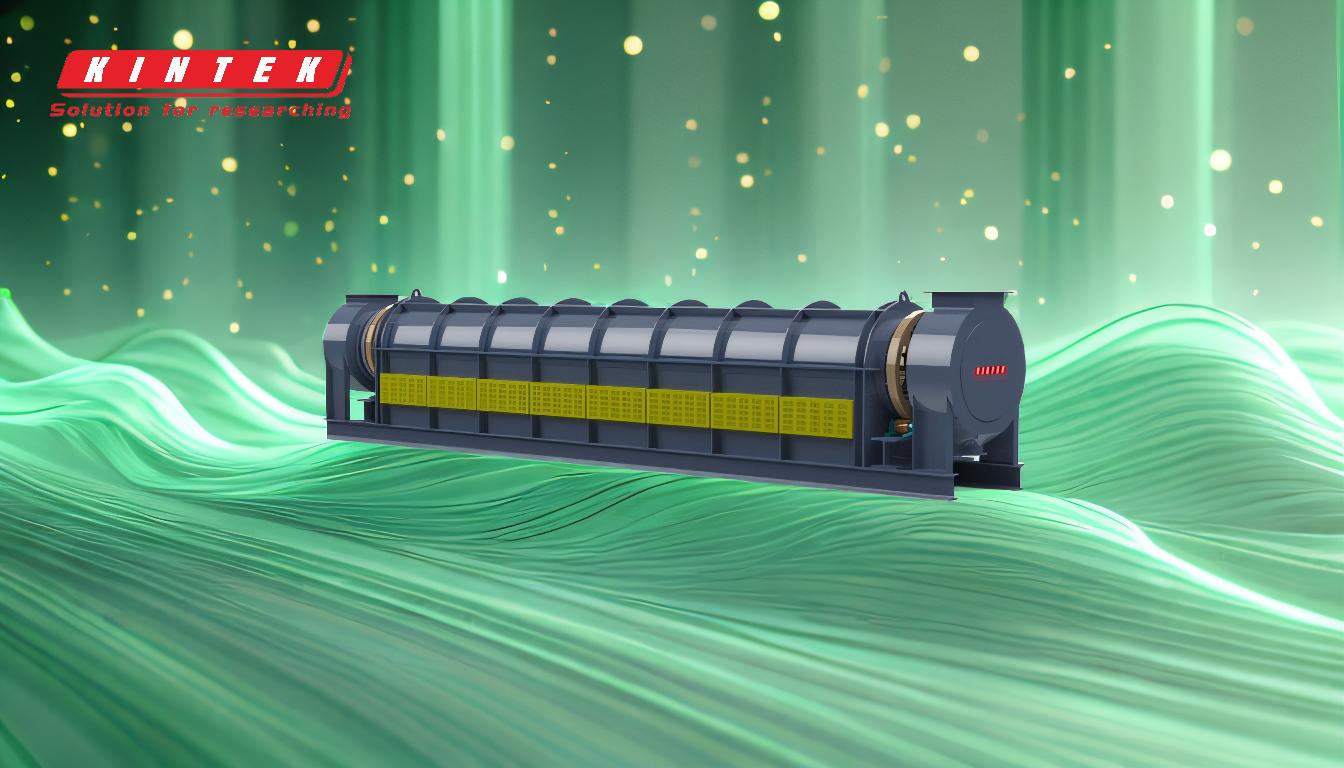
-
Definición y finalidad de la calcinación:
- La calcinación es un proceso térmico en el que los materiales se calientan a altas temperaturas (por debajo de sus puntos de fusión) en presencia limitada de aire u oxígeno.
- El objetivo principal es eliminar las impurezas volátiles, como la humedad, el dióxido de carbono o el dióxido de azufre, de los minerales metálicos u otras sustancias.
- Este proceso es crucial para purificar materiales y prepararlos para su posterior uso industrial.
-
Aplicaciones de los calcinadores:
- Eliminar el agua:Los calcinadores se utilizan para eliminar la humedad absorbida por los materiales, garantizando su sequedad y estabilidad.
- Eliminación de componentes volátiles:Eliminan compuestos volátiles como el dióxido de carbono o el dióxido de azufre, que pueden interferir en las propiedades del material.
- Oxidación:Los calcinadores pueden oxidar una parte o la totalidad de una sustancia, alterando su composición química para aplicaciones específicas.
- Producción de cemento:Uno de los usos más comunes es la calcinación de piedra caliza para producir clínker, un componente clave en la fabricación de cemento.
-
Papel en los procesos industriales:
- Los calcinadores forman parte integrante de los procesos pirometalúrgicos, en los que se utilizan altas temperaturas para extraer y purificar los metales de los minerales.
- También se utilizan en transformaciones químicas, combustión orgánica y desorción térmica, lo que los hace versátiles en diversas industrias.
-
Funcionalidad de los hornos rotatorios:
- Los hornos rotatorios, a menudo utilizados como calcinadores, están diseñados para proporcionar entornos de temperatura ultraelevada para procesos continuos o discontinuos.
- Funcionan como intercambiadores de calor, secadores, calcinadores e incineradores, lo que los hace adecuados para una amplia gama de tareas de procesamiento térmico.
- En la producción de cemento, los hornos rotatorios facilitan la calcinación de la piedra caliza, iniciando las reacciones químicas necesarias para formar el clínker.
-
Importancia en la producción de clínker:
- En la fabricación de cemento, el calcinador es el lugar donde se mezclan el crudo precalentado y el combustible dentro de una corriente de aire caliente para iniciar la reacción de calcinación.
- Esta reacción es el primer paso en la producción de clínker, que luego se muele para fabricar cemento.
-
Versatilidad y adaptabilidad:
- Las calcinadoras se adaptan a diversos materiales y procesos, como el secado, la sinterización, el tostado por reducción y la incineración.
- Su capacidad para funcionar a altas temperaturas y manipular distintos materiales las hace indispensables en sectores como la metalurgia, el procesamiento químico y la construcción.
Al comprender estos puntos clave, los compradores de equipos y consumibles pueden evaluar mejor el papel de las calcinadoras en sus aplicaciones industriales específicas y tomar decisiones informadas sobre su uso y mantenimiento.
Tabla resumen:
Aspecto clave | Descripción |
---|---|
Definición | Proceso térmico para eliminar impurezas volátiles a altas temperaturas. |
Objetivo principal | Purificar materiales eliminando agua, CO₂ o SO₂. |
Aplicaciones | Secado, oxidación, transformaciones químicas y producción de cemento. |
Papel en la industria | Esencial en la pirometalurgia, la fabricación de cemento y el procesamiento químico. |
Funcionalidad en hornos rotatorios | Entornos de alta temperatura para procesos continuos o discontinuos. |
Versatilidad | Adaptable para secado, sinterización, calcinación por reducción e incineración. |
¿Está listo para optimizar el procesamiento de materiales con un calcinador? Póngase en contacto con nuestros expertos para obtener más información.