El acabado PVD (deposición física de vapor) utiliza una amplia gama de materiales, tanto inorgánicos como orgánicos, para crear revestimientos con propiedades funcionales y estéticas específicas.Los materiales utilizados en los revestimientos PVD incluyen metales, aleaciones, cerámicas y compuestos especializados como carburos, nitruros, siliciuros y boruros.Algunos ejemplos comunes son el titanio, el circonio, el aluminio, el oro y el carbono tipo diamante (DLC).Estos revestimientos se aplican a sustratos como acero inoxidable, titanio, vidrio, plásticos y cerámica, a menudo tras procesos de pretratamiento como la galvanoplastia.La elección de los materiales depende de las propiedades deseadas, como la dureza, la conductividad o la resistencia a la corrosión, y de la aplicación específica, ya sea en la industria aeroespacial, automovilística, de dispositivos médicos o decorativa.
Explicación de los puntos clave:
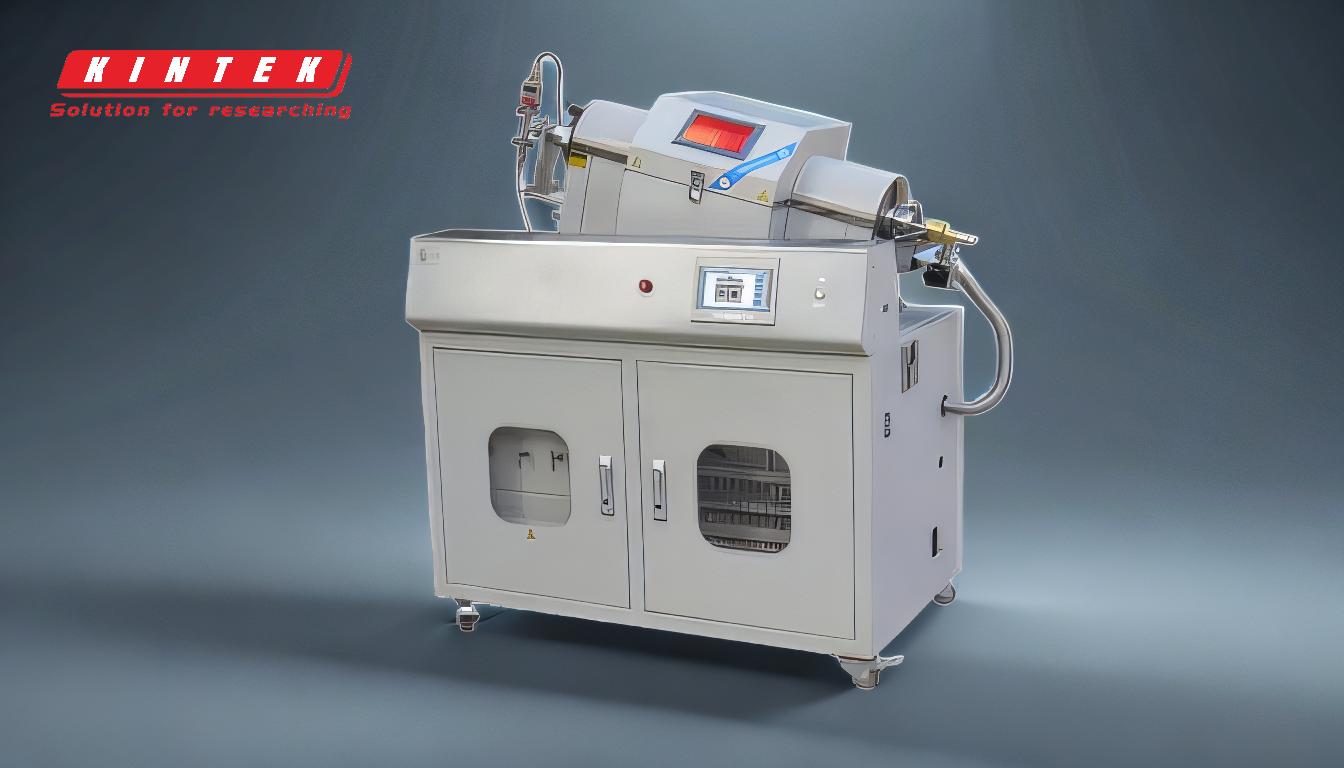
-
Tipos de materiales utilizados en los recubrimientos PVD:
- Metales y aleaciones:Se suelen utilizar titanio, circonio, aluminio, acero inoxidable, cobre y oro.Estos materiales ofrecen propiedades como durabilidad, conductividad y estética.
- Cerámica:Materiales como el óxido de silicio y el aluminio-cromo (AlCr) se utilizan por su dureza y resistencia al desgaste.
- Compuestos especializados:Los carburos (p. ej., TiC), nitruros (p. ej., TiN, Cr2N), siliciuros y boruros se emplean para requisitos de rendimiento específicos, como la resistencia a altas temperaturas o la mejora de la vida útil de la herramienta.
- Materiales orgánicos:También se puede utilizar una gama limitada de materiales orgánicos en revestimientos PVD, aunque son menos comunes en comparación con los materiales inorgánicos.
-
Materiales de revestimiento PVD comunes y sus aplicaciones:
- Oro:Se utiliza en la electrónica aeroespacial y en aplicaciones decorativas como relojes y joyas.
- Nitruro de titanio (TiN):Muy utilizado con fines decorativos (por ejemplo, teléfonos, gafas) y para aumentar la durabilidad de herramientas y herrajes.
- Zinc Estaño (ZnSn):Se aplica como revestimiento óptico en ventanas y cristales de baja emisividad (low-e).
- Carbono tipo diamante (DLC):Proporciona una dureza excepcional y baja fricción, por lo que es adecuado para componentes de automoción e industriales.
- Óxido de indio y estaño (ITO):Se utiliza en LCD, pantallas de plasma y paneles táctiles debido a su alta conductividad y transparencia.
-
Sustratos adecuados para revestimientos PVD:
- Metales:Los aceros inoxidables (p. ej., 303, 440C, 17-4), las aleaciones de titanio y los aceros para herramientas suelen recubrirse.El aluminio se utiliza raramente debido a su bajo punto de fusión.
- No metales:El vidrio, la cerámica, los plásticos (por ejemplo, ABS) y el nailon también pueden recubrirse, siempre que sean compatibles con el vacío.
- Tratamiento previo:Los sustratos suelen pretratarse con revestimientos orgánicos o electrodepositarse con níquel y cromo para mejorar la adherencia y la durabilidad.
-
Aplicaciones específicas de la industria:
- Aeroespacial:Recubrimientos de oro para electrónica y compuestos especializados para la resistencia a altas temperaturas.
- Automoción:Recubrimientos DLC y TiN para la resistencia al desgaste y la mejora del rendimiento de los componentes del motor.
- Dispositivos médicos:El acero inoxidable y las aleaciones de titanio están recubiertos para ofrecer biocompatibilidad y resistencia a la corrosión.
- Decorativo:Los revestimientos de TiN y oro se utilizan en joyería, relojería y electrónica de consumo por su atractivo estético.
-
Factores que influyen en la selección de materiales:
- Requisitos de rendimiento:La dureza, la resistencia al desgaste, la conductividad y la resistencia a la corrosión determinan la elección de los materiales.
- Compatibilidad del sustrato:El material debe resistir el proceso de PVD, que implica el calentamiento a altas temperaturas (hasta 800 °F).
- Entorno de aplicación:Las condiciones de funcionamiento (por ejemplo, alta temperatura, exposición a productos químicos) influyen en la selección de los materiales de revestimiento.
-
Ventajas de los revestimientos PVD:
- Versatilidad:El PVD puede depositar una amplia gama de materiales sobre diversos sustratos.
- Durabilidad:Los revestimientos son muy resistentes al desgaste, la corrosión y las altas temperaturas.
- Atractivo estético:Materiales como el oro y el TiN proporcionan acabados decorativos.
- Respeto del medio ambiente:El PVD es un proceso más limpio que los métodos tradicionales de revestimiento, con un mínimo de residuos y emisiones.
En resumen, el acabado PVD emplea una amplia gama de materiales, cada uno seleccionado por sus propiedades únicas y su idoneidad para aplicaciones específicas.El proceso es muy versátil y permite crear revestimientos duraderos, funcionales y estéticamente agradables en numerosos sectores.
Tabla resumen:
Categoría | Materiales | Aplicaciones |
---|---|---|
Metales y aleaciones | Titanio, circonio, aluminio, acero inoxidable, cobre, oro | Durabilidad, conductividad, estética |
Cerámica | Óxido de silicio, aluminio-cromo (AlCr) | Dureza, resistencia al desgaste |
Compuestos especializados | Carburos (TiC), nitruros (TiN, Cr2N), siliciuros, boruros | Resistencia a altas temperaturas, mayor vida útil de la herramienta |
Materiales orgánicos | Gama limitada de materiales orgánicos | Aplicaciones menos comunes y especializadas |
Aplicaciones comunes | Oro (aeroespacial, decorativo), TiN (herramientas, hardware), DLC (automoción) | Industrias aeroespacial, de automoción, de dispositivos médicos y decorativa |
Descubra cómo los revestimientos PVD pueden mejorar sus productos. póngase en contacto para recibir asesoramiento experto.