Los revestimientos PVD (deposición física de vapor) son famosos por su excepcional durabilidad y resistencia al desgaste, la corrosión y el desconchado.Estos revestimientos se unen a nivel molecular con el sustrato, creando una capa fuerte y fina que es muy resistente a las fuerzas externas.Gracias a sus propiedades de dureza, resistencia al desgaste y baja fricción, los revestimientos PVD son menos propensos a astillarse que los revestimientos tradicionales.Su capacidad para soportar entornos difíciles, como altas temperaturas y condiciones corrosivas, aumenta aún más su durabilidad.Aunque ningún revestimiento es totalmente inmune a los daños, los revestimientos PVD se encuentran entre las opciones más duraderas disponibles, por lo que son ideales para aplicaciones exigentes en sectores como el de la automoción, el aeroespacial y el médico.
Explicación de los puntos clave:
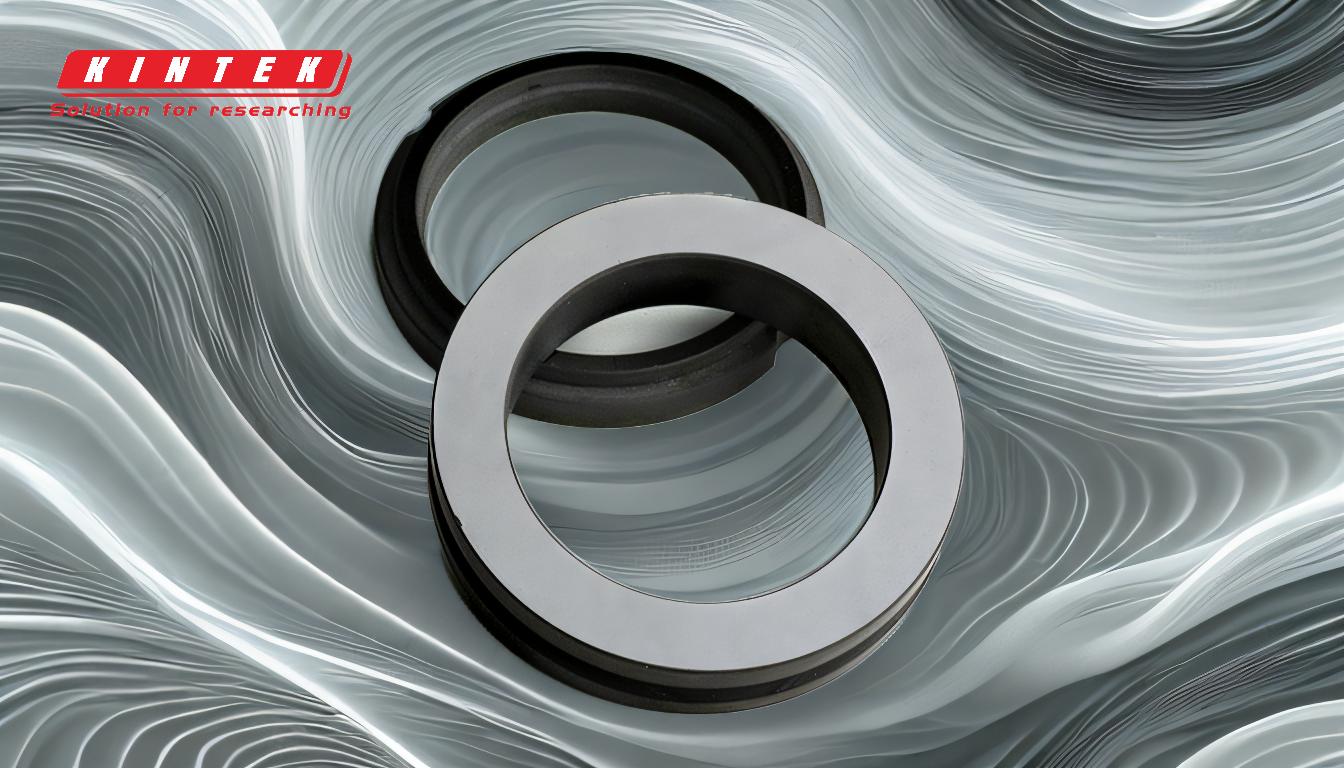
-
Enlace molecular y adhesión
- Los revestimientos PVD forman una unión a nivel molecular con el sustrato, creando una conexión fuerte y duradera.
- Este mecanismo de unión garantiza que el revestimiento se adhiera firmemente a la superficie, haciéndola resistente al desconchado incluso bajo tensión mecánica o impacto.
-
Dureza y resistencia al desgaste
- Los revestimientos PVD son conocidos por su gran dureza, que a menudo supera la de los revestimientos tradicionales.
- La dureza del revestimiento contribuye a su capacidad para resistir el desgaste, la abrasión y el desconchado, incluso en entornos de gran tensión.
-
Capa fina y duradera
- Los revestimientos PVD son extremadamente finos, normalmente de 0,5 a 5 micras.
- A pesar de su delgadez, estos revestimientos son muy duraderos y difíciles de eliminar, lo que reduce aún más la probabilidad de que se astillen.
-
Resistencia a la corrosión y la oxidación
- El entorno de vacío durante el proceso de PVD elimina la contaminación y evita la oxidación, lo que da como resultado un revestimiento muy resistente a la corrosión y a la degradación ambiental.
- Esta resistencia aumenta la durabilidad y longevidad general del revestimiento, reduciendo el riesgo de que se astille con el tiempo.
-
Aplicaciones en industrias exigentes
- Los revestimientos PVD se utilizan ampliamente en industrias como la automovilística, la aeroespacial y la médica, donde la durabilidad y la resistencia al desgaste son fundamentales.
- Su capacidad para soportar condiciones duras y tensiones mecánicas hace que sean menos propensos al desconchado en comparación con otros revestimientos.
-
Comparación con los revestimientos tradicionales
- A diferencia de los acabados tradicionales, los revestimientos PVD son mucho más duros y resistentes al desgaste y la corrosión.
- Esta durabilidad superior hace que sea menos probable que se astillen, incluso cuando se someten a una manipulación brusca o a condiciones extremas.
-
Rendimiento en el mundo real
- Se ha demostrado que los revestimientos PVD mejoran el límite de fatiga y la resistencia de los materiales, como la aleación Ti-6Al-4V, en porcentajes significativos.
- Estas mejoras de rendimiento demuestran además la capacidad del revestimiento para resistir los daños, incluido el desconchado, en condiciones reales.
En resumen, aunque ningún revestimiento es totalmente inmune a los daños, los revestimientos PVD se encuentran entre las opciones más duraderas y resistentes al desconchado disponibles.Su unión molecular, dureza, delgadez y resistencia a la corrosión y al desgaste los convierten en una opción excelente para aplicaciones en las que la durabilidad y la longevidad son primordiales.
Tabla resumen:
Característica clave | Descripción |
---|---|
Adhesión molecular | Forma una fuerte unión a nivel molecular con el sustrato, reduciendo los riesgos de astillado. |
Dureza y resistencia al desgaste | Supera a los revestimientos tradicionales, ofreciendo una resistencia superior al desgaste y la abrasión. |
Capa fina y duradera | Extremadamente fina (0,5-5 micras) pero muy duradera, minimizando el desconchado. |
Resistencia a la corrosión | Resiste la corrosión y la oxidación, mejorando la longevidad en entornos difíciles. |
Aplicaciones industriales | Ampliamente utilizado en automoción, aeroespacial y medicina por su durabilidad y rendimiento. |
Rendimiento en el mundo real | Mejora los límites de fatiga y la resistencia, reduciendo los daños en condiciones extremas. |
¿Desea mejorar la durabilidad de sus materiales con revestimientos de PVD? Póngase en contacto con nosotros para obtener más información.