El revestimiento PVD (deposición física de vapor) es una técnica de acabado de superficies muy avanzada y duradera que mejora significativamente la dureza, la resistencia al desgaste y la vida útil de los materiales.Es especialmente conocido por su capacidad para crear revestimientos finos y duros de entre 0,5 y 5 micras de grosor, que se aplican a metales como el acero inoxidable.Los revestimientos PVD son cuatro veces más duros que el cromo, lo que los hace excepcionalmente resistentes a los arañazos, la corrosión y la oxidación.Esto los hace ideales para aplicaciones en entornos difíciles, como piezas de automoción, herramientas industriales y proyectos costeros.Además, los revestimientos PVD son respetuosos con el medio ambiente, funcionan a temperaturas más bajas y son adecuados para herramientas de precisión y componentes complejos, por lo que ofrecen ventajas prácticas y éticas frente a métodos de revestimiento tradicionales como el cromado.
Explicación de los puntos clave:
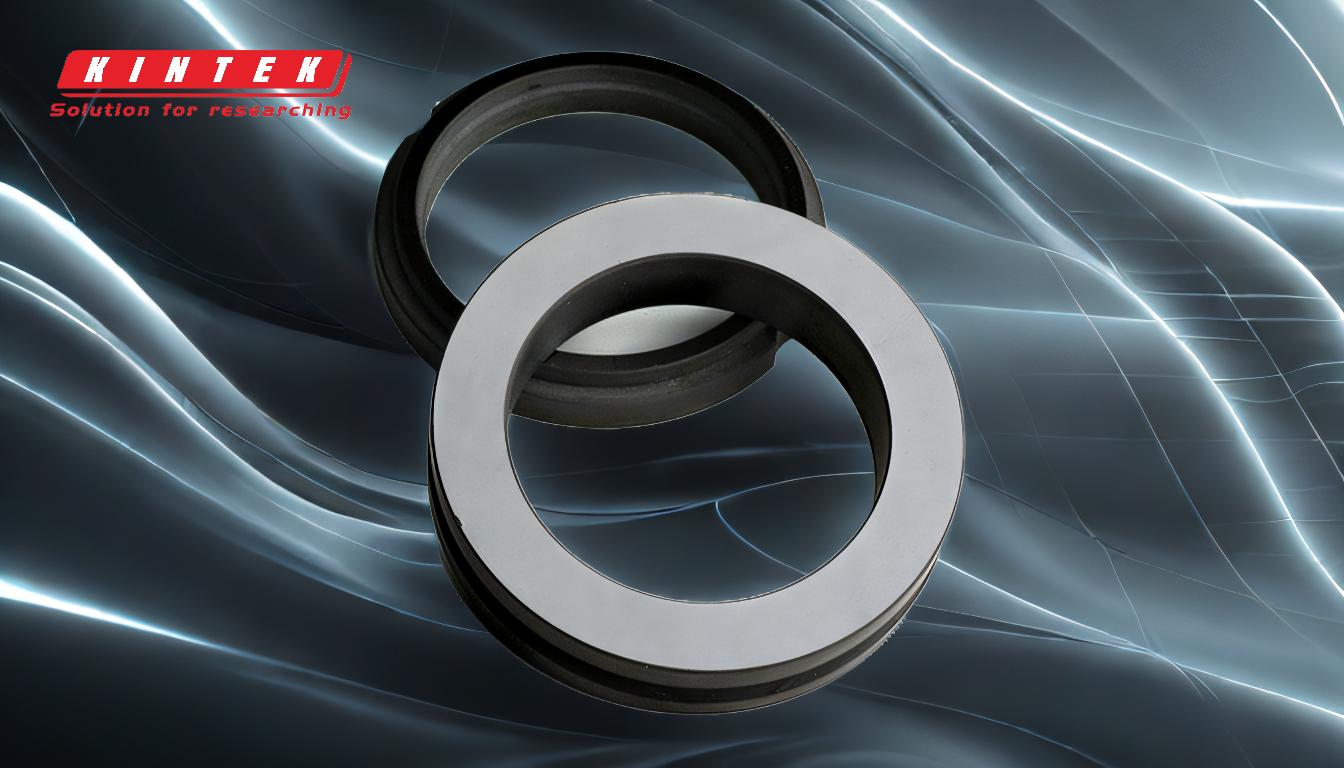
-
Dureza de los revestimientos PVD:
- Los revestimientos PVD son cuatro veces más duros que el cromo, lo que los hace muy resistentes a los arañazos y el desgaste.Esta dureza se consigue mediante la alteración a nivel molecular de la superficie metálica durante el proceso de recubrimiento.
- La dureza de los revestimientos PVD los hace ideales para aplicaciones que requieren durabilidad, como herramientas de corte, componentes de automoción y maquinaria industrial.
-
Espesor y durabilidad:
- Los revestimientos PVD son extremadamente finos, normalmente de 0,5 a 5 micras.A pesar de su delgadez, proporcionan una durabilidad y longevidad excepcionales.
- La delgadez del revestimiento preserva el filo de las herramientas, como las cuchillas, y reduce la fuerza de corte y el calor durante el uso.
-
Resistencia a la corrosión y la oxidación:
- Los revestimientos de PVD son muy resistentes a la corrosión y la oxidación, lo que los hace adecuados para su uso en entornos difíciles, como zonas costeras o entornos industriales.
- Esta resistencia prolonga la vida útil de los productos revestidos, reduciendo la necesidad de sustituciones o mantenimiento frecuentes.
-
Ventajas medioambientales y prácticas:
- El revestimiento PVD es una alternativa ecológica a procesos tradicionales como el cromado, que genera subproductos tóxicos.
- El proceso funciona a temperaturas más bajas (alrededor de 500 °C), lo que reduce el riesgo de daños térmicos al sustrato y minimiza la distorsión del material.
-
Versatilidad en las aplicaciones:
- Los revestimientos PVD son adecuados para una amplia gama de aplicaciones, como herramientas de corte de acero rápido (HSS) y carburo, componentes de moldeo por inyección de plástico, herramientas de corte fino y revestimientos ópticos.
- El proceso es compatible tanto con la fabricación de grandes volúmenes como con la producción de pequeños lotes, lo que lo hace versátil para diversas industrias.
-
Ventajas sobre los revestimientos tradicionales:
- Los revestimientos de PVD ofrecen una dureza, resistencia al desgaste y durabilidad superiores a las de los revestimientos tradicionales, como el cromado.
- La tensión de compresión que se forma durante el enfriamiento evita la formación y expansión de grietas, lo que hace que los recubrimientos PVD sean ideales para procesos de corte interrumpido como el fresado.
-
Eficacia operativa:
- Las máquinas de revestimiento PVD están controladas por ordenador, lo que permite una aplicación precisa y uniforme de los revestimientos.Esto reduce los costes de producción y los plazos de entrega.
- La rápida velocidad de deposición y la baja temperatura de deposición de las máquinas PVD las hacen eficaces y adecuadas para el recubrimiento de herramientas complejas y de precisión.
En resumen, el recubrimiento PVD es una técnica de acabado de superficies muy eficaz y versátil que ofrece una dureza, durabilidad y resistencia a la corrosión y la oxidación superiores.Sus beneficios medioambientales, combinados con su capacidad para mejorar la vida útil y el rendimiento de los productos, la convierten en la opción preferida para una amplia gama de aplicaciones industriales y comerciales.
Cuadro sinóptico:
Aspecto | Detalles |
---|---|
Dureza | 4 veces más duro que el cromo, ideal para aplicaciones duraderas. |
Espesor | De 0,5 a 5 micras, fino pero muy duradero. |
Resistencia a la corrosión | Excelente resistencia a la corrosión y la oxidación, adecuada para entornos difíciles. |
Impacto medioambiental | Respetuoso con el medio ambiente, funciona a temperaturas más bajas (≈500 °C). |
Aplicaciones | Herramientas de corte, piezas de automoción, maquinaria industrial y mucho más. |
Mejore sus productos con la durabilidad superior del revestimiento PVD. póngase en contacto con nosotros para obtener más información.