La distribución del tamaño de las partículas en la molienda depende de varios factores, como el tamaño y la densidad de las bolas de molienda, el tiempo de molienda, el número de ciclos de molienda, el tiempo de residencia, la velocidad de alimentación, la velocidad de rotación y la temperatura.Las bolas de molienda más pequeñas y los tiempos de molienda más largos suelen producir partículas más pequeñas, ya que aumentan la frecuencia de las colisiones y la energía transferida al material.El número de ciclos de molienda y el tiempo de permanencia afectan directamente al grado de reducción de tamaño, ya que un mayor número de ciclos produce partículas más finas.Además, la naturaleza del material que se muele, la velocidad de alimentación y la velocidad de rotación del molino también desempeñan un papel importante.La temperatura puede influir en el equilibrio entre la generación de defectos y la recombinación, afectando al tamaño final del grano.
Explicación de los puntos clave:
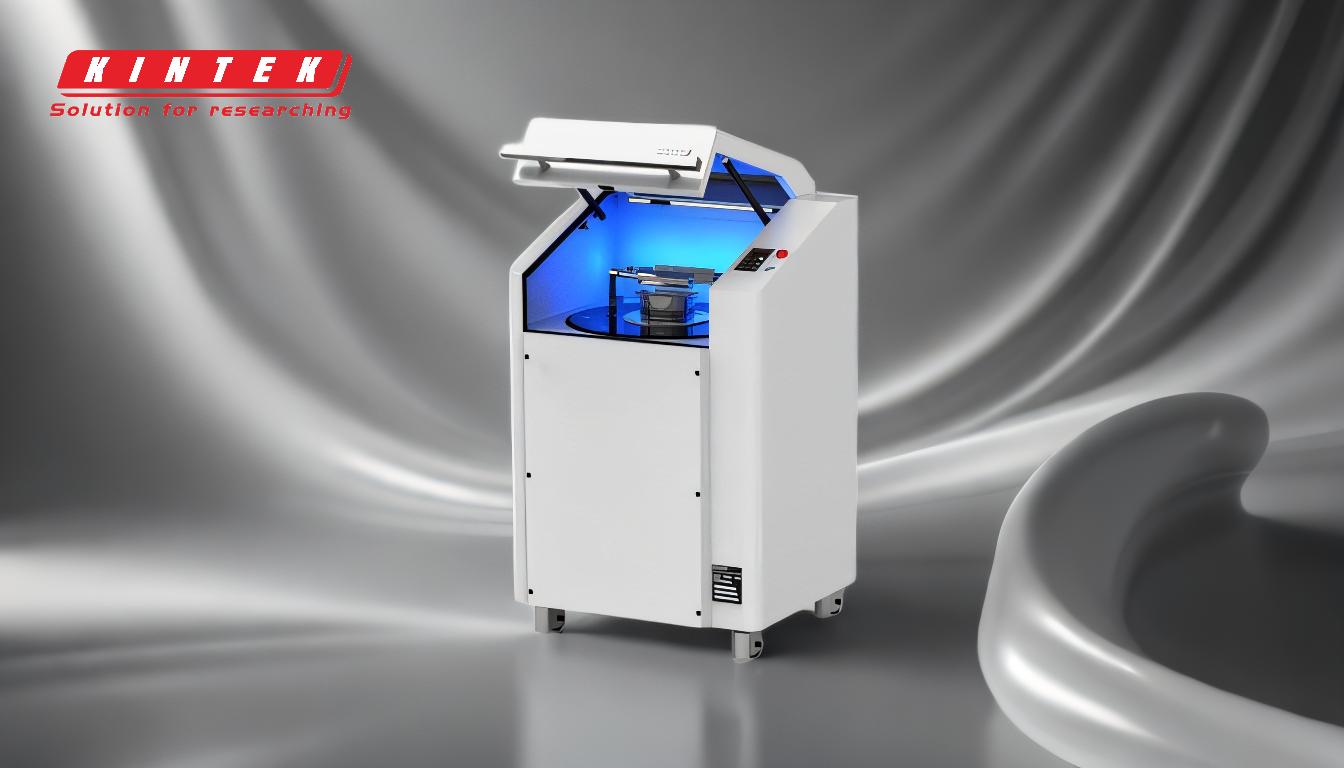
-
Tamaño y densidad de las bolas de molienda:
- Explicación:Las bolas de molienda más pequeñas son más eficaces para producir partículas más pequeñas porque aumentan la frecuencia de las colisiones y la energía transferida al material.La densidad de las bolas también afecta a la fuerza de impacto, ya que los materiales más densos proporcionan una molienda más eficaz.
- Impacto en el tamaño de las partículas:Las bolas más pequeñas y densas dan lugar a partículas más finas debido al aumento de la frecuencia de colisión y de la transferencia de energía.
-
Tiempo de molienda y número de ciclos de molienda:
- Explicación:Tiempos de molienda más largos y más ciclos de molienda permiten más colisiones y transferencia de energía, lo que conduce a una mayor reducción de tamaño.Cada ciclo contribuye a la erosión de las partículas más grandes en fragmentos más pequeños.
- Impacto en el tamaño de las partículas:El aumento del tiempo y de los ciclos de molienda da lugar a un mayor número de partículas más pequeñas, ya que las partículas más grandes se descomponen progresivamente.
-
Tiempo de residencia:
- Explicación:El tiempo que el material pasa dentro de la cámara del molino afecta al grado de reducción de tamaño.Los tiempos de permanencia más largos permiten más interacciones entre las bolas de molienda y el material.
- Impacto en el tamaño de las partículas:Los tiempos de residencia más largos generalmente conducen a partículas más finas debido a la mayor exposición a las fuerzas de molienda.
-
Velocidad de alimentación y nivel en el recipiente:
- Explicación:La velocidad a la que se introduce el material en el molino y el nivel de material en el recipiente pueden influir en la eficacia del proceso de molienda.Unas tasas de alimentación óptimas garantizan una molienda uniforme, mientras que el nivel afecta a la interacción entre el material y los medios de molienda.
- Impacto en el tamaño de las partículas:Unas velocidades de alimentación y unos niveles de recipiente adecuados garantizan una molienda eficaz, lo que se traduce en una distribución más uniforme del tamaño de las partículas.
-
Velocidad de rotación del cilindro:
- Explicación:La velocidad a la que gira el cilindro del molino afecta a la energía cinética de las bolas de molienda y a la frecuencia de las colisiones.Las velocidades más altas pueden aumentar la energía transferida al material.
- Impacto en el tamaño de las partículas:Las velocidades de rotación más elevadas pueden dar lugar a partículas más finas debido al aumento de la frecuencia de colisión y de la transferencia de energía.
-
Naturaleza del material de molienda:
- Explicación:Las propiedades físicas y químicas del material a moler, como su dureza y fragilidad, influyen en su respuesta al molido.Los materiales más duros pueden requerir más energía para conseguir la reducción de tamaño.
- Impacto en el tamaño de las partículas:La naturaleza del material determina la facilidad con que puede molerse, lo que afecta a la distribución granulométrica final.
-
Temperatura:
- Explicación:La temperatura puede influir en el equilibrio entre la generación de defectos y la recombinación durante la molienda.Las temperaturas más altas pueden facilitar la recuperación de defectos, afectando al tamaño final del grano.
- Impacto en el tamaño de las partículas:El control de la temperatura es crucial para conseguir el tamaño de partícula deseado, ya que afecta a la respuesta del material a las fuerzas de molienda.
Comprendiendo y optimizando estos factores, se puede conseguir la distribución de tamaño de partícula deseada en los procesos de molienda.Cada factor desempeña un papel fundamental en la eficiencia y eficacia del proceso de molienda, y su interacción determina el resultado final.
Cuadro sinóptico:
Factor | Impacto en el tamaño de las partículas |
---|---|
Tamaño y densidad de las bolas de molienda | Las bolas más pequeñas y densas producen partículas más finas debido al aumento de la frecuencia de colisión y la transferencia de energía. |
Tiempo y ciclos de molienda | Los tiempos de molienda más largos y el mayor número de ciclos dan como resultado partículas más finas al descomponer los fragmentos más grandes. |
Tiempo de residencia | Tiempos de residencia más largos conducen a partículas más finas debido a una mayor exposición a las fuerzas de molienda. |
Velocidad de alimentación y nivel del recipiente | Las velocidades de alimentación y los niveles de recipiente óptimos garantizan una molienda eficaz y un tamaño de partícula uniforme. |
Velocidad de rotación | Las velocidades más altas aumentan la frecuencia de colisión y la transferencia de energía, produciendo partículas más finas. |
Naturaleza del material de molienda | La dureza y fragilidad del material determinan la facilidad de molienda y el tamaño final de las partículas. |
Temperatura | La temperatura afecta a la generación y recombinación de defectos, influyendo en el tamaño final del grano. |
¿Necesita ayuda para optimizar su proceso de fresado? Póngase en contacto con nuestros expertos para obtener soluciones a medida.