Los trenes de laminación son equipos esenciales en la metalurgia, utilizados para moldear y procesar metales en diversas formas como barras, varillas, chapas y más.La principal diferencia entre los trenes de laminación de dos y tres cilindros radica en su diseño, eficacia operativa y funcionalidad.Un laminador de dos niveles consta de dos rodillos que giran en direcciones opuestas, mientras que un laminador de tres niveles añade un rodillo intermedio que gira en dirección opuesta a los rodillos superior e inferior.Este diseño permite la laminación continua sin invertir el sentido de la marcha, lo que hace que los laminadores de tres alturas sean más eficaces y fáciles de usar que los de dos alturas.A continuación, analizamos en detalle las principales diferencias y ventajas de cada tipo.
Explicación de los puntos clave:
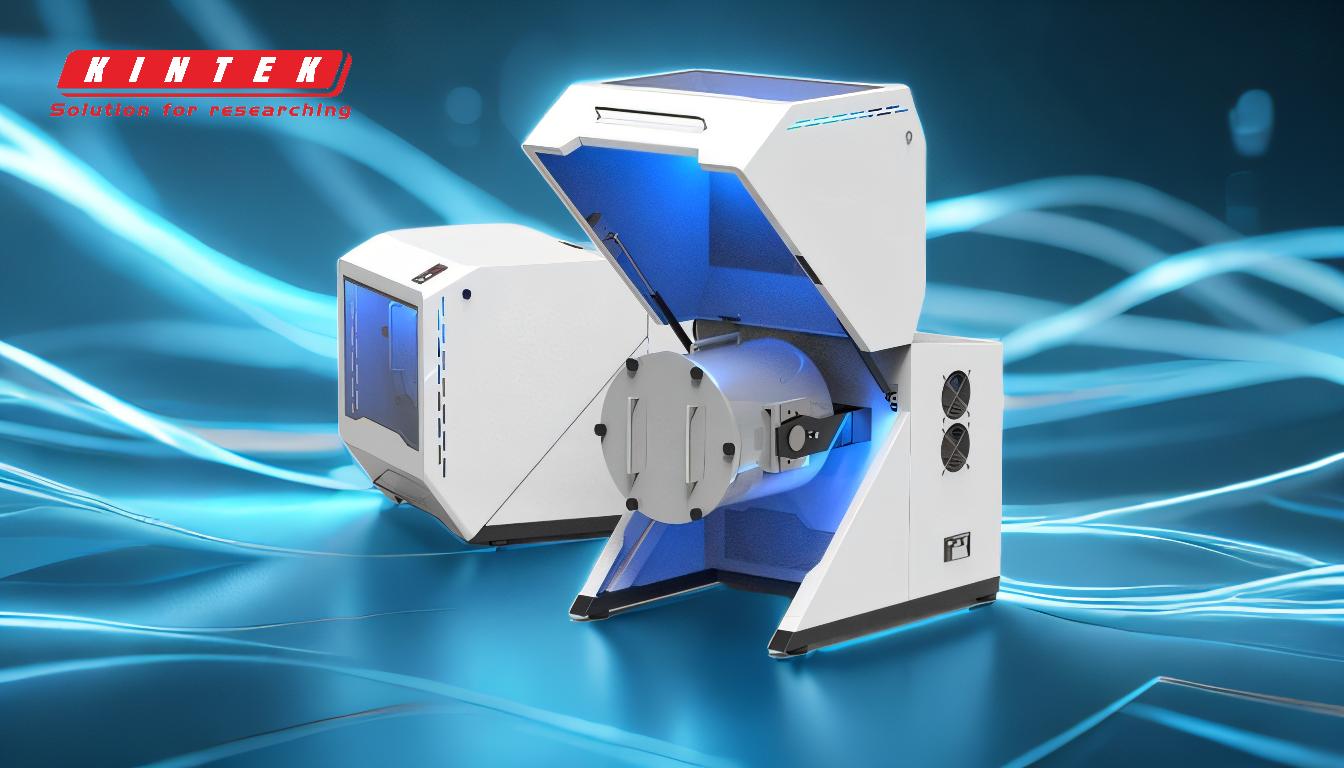
-
Diseño y configuración:
- Trenes de laminación a dos alturas:Estos molinos constan de dos rodillos horizontales apilados verticalmente.Los rodillos giran en direcciones opuestas, permitiendo que el metal pase a través de ellos y se le dé forma.Después de cada pasada, puede ser necesario invertir la dirección de los rodillos para que el metal vuelva a ser procesado.
- Trenes de laminación a tres alturas:Estos laminadores añaden un tercer rodillo intermedio que gira en sentido contrario a los rodillos superior e inferior.Esta configuración elimina la necesidad de invertir la dirección del accionamiento entre pasadas, lo que permite una laminación continua.
-
Eficiencia operativa:
- Trenes de laminación a dos alturas:Aunque son eficaces, estos laminadores requieren invertir la dirección del rodillo después de cada pasada, lo que puede ralentizar el proceso de laminado y reducir la eficacia global.
- Trenes de laminación de tres pisos:La incorporación del rodillo intermedio permite laminar de forma continua sin invertir el sentido de marcha, lo que mejora significativamente la eficacia y reduce los tiempos de inactividad.
-
Facilidad de uso:
- Trenes de laminación a dos alturas:Estos laminadores tienen un diseño más sencillo, pero pueden requerir una mayor intervención manual, como la inversión de la dirección de los rodillos, lo que puede complicar las operaciones.
- Trenes de laminación de tres alturas:El proceso de laminado continuo hace que estos laminadores sean más fáciles de manejar, ya que no es necesario parar e invertir los rodillos entre pasadas.
-
Aplicaciones:
- Ambos tipos de laminadores se utilizan en la producción de barras, varillas, alambrón, flejes, aros, formas metálicas, chapas e incluso joyas.Sin embargo, la elección entre ambos depende de los requisitos específicos del proceso de producción, como la necesidad de laminación continua o el tipo de metal que se procesa.
-
Especificaciones y consideraciones:
- A la hora de elegir un tren de laminación, hay que tener en cuenta especificaciones importantes como el diámetro de los rodillos, el tipo de metal que se va a laminar, los rodillos de trabajo, los rodillos de apoyo, el gorrón de los rodillos, la fuerza máxima de separación a 1000 pies por minuto (fpm), el área total de la columna y el espacio estimado en planta.Estos factores influirán en la elección entre un tren de laminación de dos o tres alturas en función de las necesidades específicas de la operación.
En resumen, aunque tanto los laminadores de dos alturas como los de tres alturas tienen el mismo propósito fundamental de dar forma y procesar metales, el laminador de tres alturas ofrece una mayor eficiencia y facilidad de uso debido a su capacidad de laminación continua.La elección entre ambos dependerá de los requisitos específicos del proceso de producción, incluida la necesidad de un funcionamiento continuo y el tipo de metal que se procese.
Cuadro sinóptico:
Característica | Tren de laminación de dos pisos | Tren de laminación a tres alturas |
---|---|---|
Diseño | Dos rodillos horizontales apilados verticalmente | Tres rodillos: superior, central e inferior, con el rodillo central girando en sentido opuesto |
Eficiencia operativa | Requiere invertir la dirección del rodillo después de cada pasada, lo que reduce la eficiencia | Permite el laminado continuo sin inversión, lo que mejora la eficiencia |
Facilidad de uso | Diseño más sencillo, pero puede requerir intervención manual para invertir la marcha | Más fácil de manejar sin necesidad de parar e invertir los rodillos |
Aplicaciones | Se utiliza para barras, varillas, chapas y más; depende de las necesidades de producción | Preferida para procesos de laminación continua y operaciones de alta eficiencia |
Especificaciones | Diámetro del rodillo, tipo de metal, rodillos de trabajo, rodillos de apoyo, diario del rodillo, fuerza de separación, etc. | Consideraciones similares pero optimizado para laminación continua y mayor productividad |
¿Necesita ayuda para elegir el laminador adecuado para sus necesidades metalúrgicas? Póngase en contacto con nuestros expertos hoy mismo ¡!