Los revestimientos PVD (deposición física de vapor) son conocidos por su elevada dureza, que suele oscilar entre 1500 HV (dureza Vickers) y 4500 HV, dependiendo del tipo de revestimiento, el material del sustrato y el método PVD utilizado. A título comparativo, los aceros al carbono tienen una dureza de unos 250 HV, mientras que los aceros nitrurados o niquelados/cromados oscilan entre 600 HV y 1000 HV. Los revestimientos PVD, como el TiN (nitruro de titanio), son especialmente apreciados por su capacidad para mejorar la resistencia al desgaste, la resistencia a la corrosión y la durabilidad. En algunos casos, los recubrimientos especializados como el DLC (Carbono similar al diamante) pueden alcanzar valores de dureza de hasta 9000 HV. La dureza de los revestimientos PVD es un factor crítico en su rendimiento, lo que los hace adecuados para aplicaciones exigentes en industrias como la automovilística, la aeroespacial y la médica.
Puntos clave explicados:
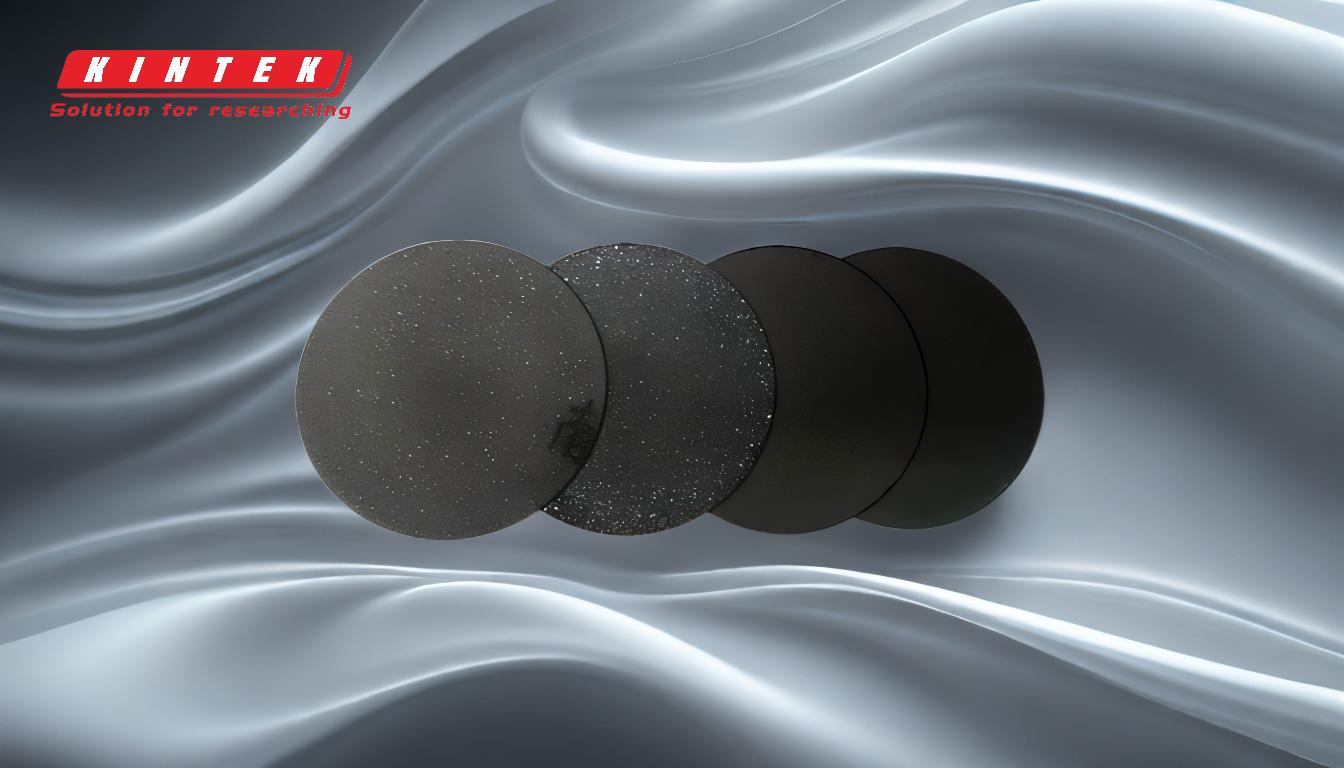
-
Rango de dureza de los recubrimientos PVD:
- Los revestimientos PVD suelen tener un rango de dureza de 1500 HV a 4500 HV dependiendo del material y del proceso de revestimiento.
- Como referencia 900 HV corresponde a 67 HRC (Rockwell C) que es significativamente más duro que muchos materiales comunes como el acero al carbono (250 HV) o los aceros nitrurados (600-1000 HV).
- Revestimientos especializados, como DLC (carbono similar al diamante) pueden alcanzar valores de dureza aún mayores, de hasta 9000 HV .
-
Factores que influyen en la dureza:
-
La dureza de los recubrimientos PVD depende de varios factores:
- Material de revestimiento: Los distintos materiales (por ejemplo, TiN, TiCN, CrN, DLC) tienen distintos niveles de dureza.
- Material del sustrato: El material subyacente puede influir en las propiedades del revestimiento. Por ejemplo, los revestimientos de TiN sobre aleación Ti-6Al-4V mejoran los límites de fatiga y la resistencia.
- Método PVD: El proceso de PVD específico (por ejemplo, pulverización catódica, evaporación por arco) y las habilidades del operario pueden afectar a la dureza del revestimiento.
- Espesor: Los revestimientos PVD son muy finos (0,5-5 micras), pero su dureza está optimizada para el rendimiento.
-
La dureza de los recubrimientos PVD depende de varios factores:
-
Comparación con otros materiales:
- Aceros al carbono: Típicamente tienen una dureza de alrededor de 250 HV (25 HRC) .
- Aceros Nitrurados o Niquelados/Cromados: Oscilan entre 600 HV y 1000 HV .
- Recubrimientos PVD: En 1500-4500 HV los revestimientos de PVD son significativamente más duros, lo que los hace ideales para aplicaciones que requieren una gran resistencia al desgaste y durabilidad.
-
Aplicaciones y ventajas:
- Los revestimientos PVD se utilizan ampliamente en industrias como automoción, aeroespacial y médica debido a su gran dureza, resistencia al desgaste y resistencia a la corrosión.
- También proporcionan baja fricción y apariencia estética por lo que son adecuados tanto para fines funcionales como decorativos.
-
Dureza y resistencia al desgaste:
- Mientras que una dureza elevada generalmente se correlaciona con una mayor resistencia al desgaste no existe una relación directa entre ambas. Los valores de dureza por encima del umbral óptimo pueden indicar descarburación que puede reducir el rendimiento.
- Los revestimientos de PVD logran un equilibrio entre la dureza y otras propiedades como tenacidad y adherencia para garantizar la durabilidad a largo plazo.
-
Recubrimientos especializados:
- Recubrimientos DLC: Se encuentran entre los revestimientos de PVD más duros, con valores de dureza que alcanzan los 9000 HV . Son especialmente apreciados por su baja fricción y excelente resistencia al desgaste .
- Recubrimientos TiN: Comúnmente utilizados por su aspecto dorado y alta dureza, son ideales para herramientas de corte, moldes y aplicaciones decorativas.
-
Medición de la dureza:
- La dureza se mide normalmente utilizando el método dureza Vickers (HV) que es adecuada para revestimientos finos. A modo de comparación, Rockwell C (HRC) en la que 900 HV equivalen a 67 HRC.
-
Dureza y resistencia a la corrosión óptimas:
- Los revestimientos PVD alcanzan un nivel óptimo de dureza que mejora su resistencia a la corrosión . Una dureza excesiva puede dar lugar a la formación de fases duras, que pueden comprometer el rendimiento.
En resumen, la dureza de los revestimientos PVD es una propiedad clave que los hace muy duraderos y adecuados para aplicaciones exigentes. Su dureza oscila entre 1500 HV y 4500 HV, con revestimientos especializados como el DLC que alcanzan hasta 9000 HV. Esta excepcional dureza, combinada con la resistencia al desgaste, a la corrosión y a la fricción, hace que los revestimientos PVD sean muy valiosos en diversos sectores.
Tabla resumen:
Aspecto | Detalles |
---|---|
Rango de dureza | 1500-4500 HV (hasta 9000 HV para recubrimientos DLC) |
Materiales de comparación | Acero al carbono: 250 HV; Aceros nitrurados: 600-1000 HV |
Principales ventajas | Alta resistencia al desgaste, resistencia a la corrosión, baja fricción y durabilidad |
Aplicaciones | Automoción, aeroespacial, médica y decorativa |
Recubrimientos especializados | TiN (nitruro de titanio), DLC (carbono similar al diamante) |
Medición | Dureza Vickers (HV); 900 HV = 67 HRC |
Descubra cómo los recubrimientos PVD pueden mejorar el rendimiento de sus materiales. póngase en contacto con nuestros expertos hoy mismo ¡!