Los revestimientos PVD (deposición física de vapor) son revestimientos avanzados de película fina conocidos por su excepcional dureza, resistencia al desgaste, resistencia a la corrosión y propiedades de baja fricción.Su uso está muy extendido en sectores como la automoción, el aeroespacial, el médico y la fabricación de semiconductores, debido a su durabilidad y a sus ventajas medioambientales en comparación con los métodos de revestimiento tradicionales, como el cromado.Los revestimientos PVD se aplican a temperaturas relativamente bajas, son muy uniformes y se adhieren bien a los sustratos, por lo que son adecuados para diversas aplicaciones, como la prolongación de la vida útil de herramientas, piezas de automóviles y dispositivos médicos.Los revestimientos PVD más comunes incluyen materiales como el nitruro de titanio (TiN), el nitruro de cromo (CrN) y el carbono tipo diamante (DLC), cada uno de los cuales ofrece propiedades únicas adaptadas a casos de uso específicos.
Explicación de los puntos clave:
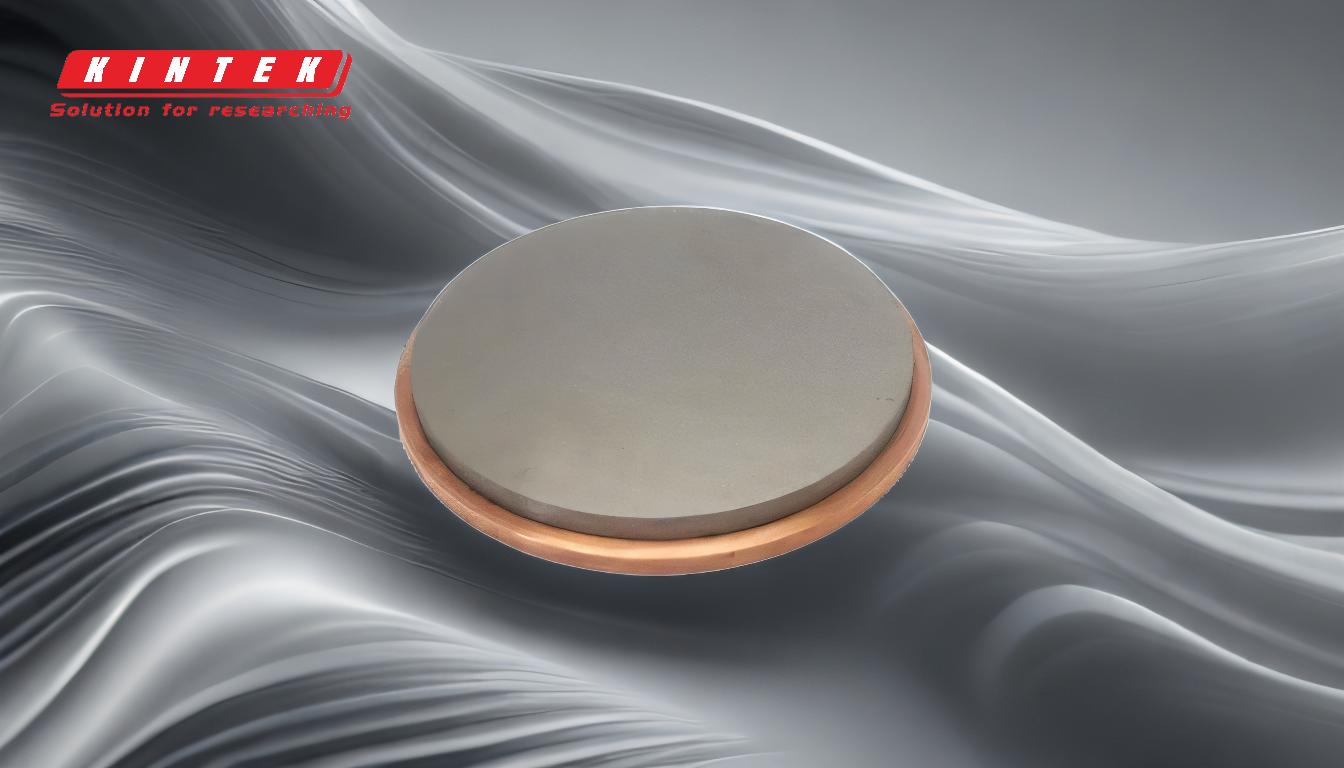
-
¿Qué es el recubrimiento PVD?
- El revestimiento PVD es un proceso de deposición de película fina en el que un material sólido se vaporiza en el vacío y luego se deposita sobre un sustrato.Este proceso crea un revestimiento muy duradero, uniforme y adherente.
- Los revestimientos suelen ser muy finos, de 0,5 a 5 micras, pero proporcionan mejoras significativas en dureza, resistencia al desgaste y resistencia a la corrosión.
-
Propiedades clave de los revestimientos PVD
- Alta dureza: Los recubrimientos PVD son significativamente más duros que los recubrimientos galvánicos tradicionales, lo que los hace ideales para aplicaciones que requieren resistencia al desgaste.
- Resistencia a la corrosión y la oxidación: Estos revestimientos son muy resistentes a la degradación ambiental, por lo que son adecuados para condiciones duras.
- Baja fricción: Los revestimientos de PVD reducen la fricción, lo que es beneficioso para las piezas móviles en aplicaciones de automoción y aeroespaciales.
- Uniformidad y adherencia: Los revestimientos son muy uniformes y se adhieren bien al sustrato, lo que garantiza un rendimiento constante.
- Respetuoso con el medio ambiente: A diferencia del cromado, los revestimientos PVD no producen sustancias tóxicas, lo que los convierte en una opción más sostenible.
-
Tipos comunes de revestimientos PVD
- Nitruro de titanio (TiN): Conocido por su aspecto similar al oro, el TiN se utiliza ampliamente por su gran dureza, resistencia al desgaste y capacidad para aumentar el límite de fatiga de los sustratos.
- Nitruro de cromo (CrN): Ofrece una excelente resistencia a la corrosión y suele utilizarse en aplicaciones que requieren estabilidad a altas temperaturas.
- Carbono tipo diamante (DLC): Proporciona una fricción extremadamente baja y una alta resistencia al desgaste, por lo que es ideal para aplicaciones médicas y de automoción.
- Nitruro de aluminio y titanio (AlTiN): Conocido por su rendimiento a altas temperaturas y se utiliza habitualmente en herramientas de corte.
-
Aplicaciones de los recubrimientos PVD
- Industria del automóvil: Se utiliza para recubrir piezas de automóviles como pistones, ruedas y componentes del motor para mejorar la durabilidad y reducir la fricción.
- Industria aeroespacial: Aplicado a álabes de turbinas y otros componentes críticos para mejorar la resistencia al desgaste y la corrosión.
- Dispositivos médicos: Utilizados para herramientas quirúrgicas e implantes para garantizar la biocompatibilidad y la longevidad.
- Semiconductores y electrónica: Empleado en revestimientos de película fina para fotovoltaica, dispositivos semiconductores y revestimientos antirreflectantes.
- Herramientas y maquinaria: Prolonga la vida útil de brocas, herramientas de corte y moldes al proporcionar una superficie dura y resistente al desgaste.
-
Ventajas sobre los métodos de recubrimiento tradicionales
- Durabilidad: Los revestimientos PVD pueden prolongar la vida útil de los productos hasta diez veces, con algunos revestimientos que duran más de 25 años.
- Ventajas medioambientales: El proceso no implica productos químicos tóxicos, por lo que es una alternativa más ecológica al cromado.
- Versatilidad: Los revestimientos PVD pueden aplicarse a una amplia gama de materiales, incluidos metales, polímeros y cerámicas.
-
Retos y limitaciones
- Uniformidad del revestimiento: Aunque los revestimientos de PVD suelen ser uniformes, lograr un espesor uniforme en geometrías complejas (por ejemplo, la parte posterior y los laterales de las herramientas) puede ser un reto debido a la baja presión del aire durante la deposición.
- Coste: Los requisitos de equipamiento y proceso para el revestimiento PVD pueden ser más caros que los métodos tradicionales, aunque los beneficios a largo plazo suelen justificar la inversión.
-
Tendencias futuras en recubrimientos PVD
- Materiales avanzados: Se está investigando el desarrollo de nuevos revestimientos PVD con características de rendimiento aún mayores, como una mayor estabilidad térmica y una biocompatibilidad mejorada.
- Sostenibilidad: A medida que las industrias den prioridad a procesos de fabricación más ecológicos, se espera que crezca la demanda de revestimientos PVD debido a sus ventajas medioambientales.
En resumen, los revestimientos PVD son una opción superior para aplicaciones que requieren gran durabilidad, resistencia al desgaste y sostenibilidad medioambiental.Su versatilidad y rendimiento los hacen indispensables en sectores que van desde la automoción hasta los dispositivos médicos, y los avances en curso siguen ampliando sus aplicaciones potenciales.
Cuadro sinóptico:
Aspecto clave | Detalles |
---|---|
¿Qué es el revestimiento PVD? | Proceso de deposición de película fina que crea revestimientos duraderos, uniformes y adherentes. |
Propiedades clave | Alta dureza, resistencia a la corrosión, baja fricción, uniformidad, respetuoso con el medio ambiente. |
Tipos comunes | TiN (nitruro de titanio), CrN (nitruro de cromo), DLC (carbono tipo diamante). |
Aplicaciones | Industria automovilística, aeroespacial, dispositivos médicos, herramientas y semiconductores. |
Ventajas | Durabilidad, ventajas medioambientales, versatilidad. |
Desafíos | Uniformidad en geometrías complejas, mayor coste inicial. |
Tendencias futuras | Materiales avanzados, innovaciones centradas en la sostenibilidad. |
¿Está listo para mejorar sus productos con revestimientos PVD? Póngase en contacto con nosotros para obtener más información.