Los recubrimientos de carbono tipo diamante (DLC) son ampliamente conocidos por sus excelentes propiedades, como su alta dureza, baja fricción y resistencia al desgaste.Sin embargo, también presentan varios inconvenientes que pueden limitar su aplicabilidad en determinados escenarios.Entre ellos se encuentran los problemas relacionados con los procesos de deposición, la compatibilidad de los materiales y el rendimiento en condiciones específicas.Comprender estas limitaciones es crucial para tomar decisiones informadas a la hora de considerar los recubrimientos de DLC para diversas aplicaciones.
Explicación de los puntos clave:
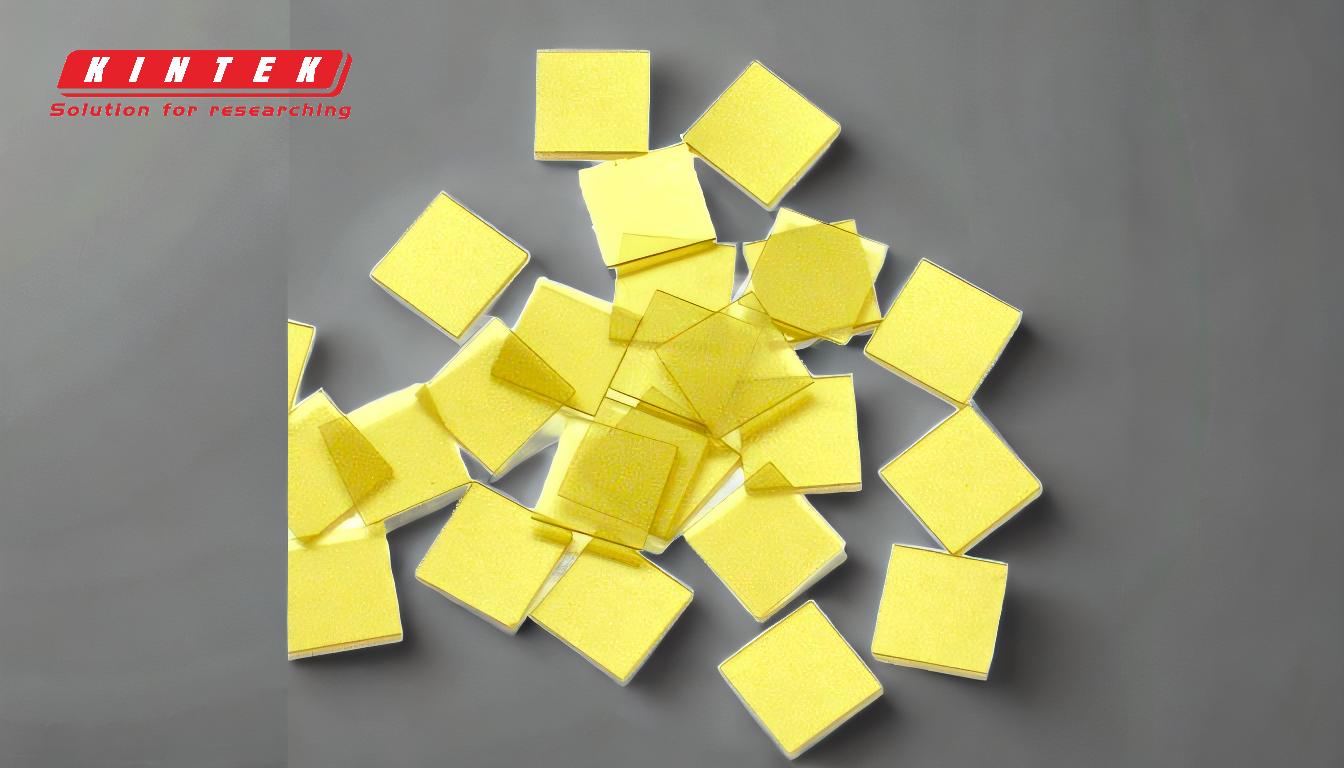
-
Limitaciones del proceso de deposición:
- Altas temperaturas de procesamiento:Los recubrimientos de DLC, especialmente los aplicados mediante deposición química de vapor (CVD), suelen requerir altas temperaturas de procesamiento (800-1000 °C).Esto limita su uso a materiales que puedan soportar tal calor, como el carburo cementado.Muchos materiales, especialmente los polímeros y algunos metales, no pueden soportar estas temperaturas, lo que restringe la gama de aplicaciones.
- Dificultades de enmascaramiento:Los revestimientos CVD son difíciles de enmascarar, lo que a menudo da lugar a un revestimiento de todo o nada.Esto significa que el recubrimiento selectivo de áreas específicas es un reto, lo que puede ser un inconveniente importante cuando sólo algunas partes de un componente requieren recubrimiento.
- Limitaciones de tamaño:El tamaño de las piezas que pueden recubrirse está limitado por la capacidad de la cámara de reacción.Los componentes grandes o complejos pueden tener que dividirse en piezas más pequeñas, lo que complica el proceso y aumenta los costes.
-
Espesor del revestimiento y problemas de tensión:
- Revestimientos gruesos y tensión de tracción:Los revestimientos de DLC, especialmente los aplicados mediante CVD, pueden ser relativamente gruesos (10-20 μm).Durante el enfriamiento, estos recubrimientos gruesos pueden generar tensiones de tracción, dando lugar a finas grietas.Estas grietas pueden propagarse bajo un impacto externo, provocando el desprendimiento del recubrimiento.Esto hace que los revestimientos de DLC sean menos adecuados para aplicaciones que implican procesos de corte interrumpido, como el fresado, donde el revestimiento es más propenso a fallar.
- Desafíos de adherencia:La adhesión de los revestimientos de DLC a determinados sustratos puede ser problemática, sobre todo si el material del sustrato no es compatible con las altas temperaturas o si la preparación de la superficie es inadecuada.Una adhesión deficiente puede provocar delaminación y reducir el rendimiento del recubrimiento.
-
Limitaciones de rendimiento en condiciones específicas:
- Procesos de corte interrumpidos:Los revestimientos de DLC no son ideales para procesos de corte interrumpido como el fresado.Los repetidos impactos y ciclos térmicos de estos procesos pueden agravar la formación de grietas y provocar el fallo del revestimiento.Esto limita su uso en determinadas aplicaciones de mecanizado en las que otros revestimientos podrían dar mejores resultados.
- Contenido de hidrógeno y estabilidad:Algunos revestimientos de DLC contienen hidrógeno, lo que puede afectar a su estabilidad y rendimiento, especialmente a temperaturas elevadas.Los recubrimientos de DLC hidrogenados pueden degradarse o perder sus propiedades cuando se exponen a altas temperaturas, lo que limita su uso en aplicaciones de alta temperatura.
-
Coste y complejidad:
- Alto coste de deposición:Los equipos y procesos necesarios para depositar recubrimientos DLC, especialmente mediante CVD, son complejos y caros.Esto puede hacer que los recubrimientos DLC resulten prohibitivos para algunas aplicaciones, especialmente si se comparan con otros recubrimientos alternativos.
- Complejidad del proceso:La necesidad de altas temperaturas, equipos especializados y un control preciso de los parámetros de deposición aumenta la complejidad del proceso.Esto puede aumentar el tiempo y los costes de producción, lo que hace que los recubrimientos de DLC sean menos atractivos para aplicaciones de gran volumen o bajo coste.
-
Compatibilidad de materiales y gama de aplicaciones:
- Compatibilidad limitada con sustratos:Los revestimientos de DLC no son universalmente compatibles con todos los materiales.Por ejemplo, es posible que no se adhieran bien a determinados metales o polímeros, lo que limita su uso en aplicaciones en las que predominan estos materiales.
- Campo de aplicación restringido:Debido a las limitaciones mencionadas anteriormente, los recubrimientos de DLC suelen restringirse a aplicaciones específicas en las que sus propiedades únicas, como la baja fricción y la alta resistencia al desgaste, son esenciales.En otros casos, pueden resultar más adecuados otros revestimientos.
En resumen, aunque los recubrimientos de DLC ofrecen importantes ventajas en cuanto a dureza, reducción de la fricción y resistencia al desgaste, también presentan notables desventajas.Entre ellas se encuentran los problemas relacionados con el proceso de deposición, el grosor y la tensión del revestimiento, el rendimiento en condiciones específicas, el coste y la compatibilidad de los materiales.Comprender estas limitaciones es crucial para seleccionar el revestimiento adecuado para una aplicación determinada y garantizar un rendimiento y una durabilidad óptimos.
Cuadro sinóptico:
Desventaja | Descripción |
---|---|
Altas temperaturas de procesado | Requiere 800-1000 °C, lo que limita su uso a materiales resistentes al calor. |
Dificultades de enmascarado | El revestimiento selectivo es un reto; a menudo resulta en una aplicación de todo o nada. |
Limitaciones de tamaño | Limitado por el tamaño de la cámara de reacción, lo que complica los componentes grandes o complejos. |
Recubrimientos gruesos y tensión de tracción | Los revestimientos gruesos (10-20 μm) pueden agrietarse bajo tensión, lo que conduce al pelado. |
Problemas de adherencia | Una mala adherencia a determinados sustratos puede provocar delaminación. |
Procesos de corte interrumpidos | No es ideal para el fresado debido a la formación de grietas bajo impactos repetidos. |
Contenido en hidrógeno y estabilidad | Los revestimientos hidrogenados pueden degradarse a altas temperaturas. |
Alto coste de deposición | Los equipos complejos y caros aumentan los costes totales. |
Compatibilidad limitada con los sustratos | No es universalmente compatible con todos los materiales, lo que restringe la gama de aplicaciones. |
¿Necesita ayuda para elegir el revestimiento adecuado para su aplicación? Póngase en contacto con nuestros expertos hoy mismo ¡!