Los moldes de dos placas se utilizan mucho en el moldeo por inyección por su sencillez y rentabilidad.Sin embargo, presentan ciertas desventajas, sobre todo en los diseños con varias cavidades.Uno de los principales retos es equilibrar el flujo de plástico fundido a través de múltiples cavidades, lo que puede provocar un llenado desigual y defectos en el producto final.Además, la alineación de la línea de apertura con la compuerta en un molde de dos placas puede complicar el proceso de diseño y fabricación.Estas limitaciones pueden repercutir en la eficacia, la calidad y el coste de producción, por lo que es esencial evaluar cuidadosamente su idoneidad para aplicaciones específicas.
Explicación de los puntos clave:
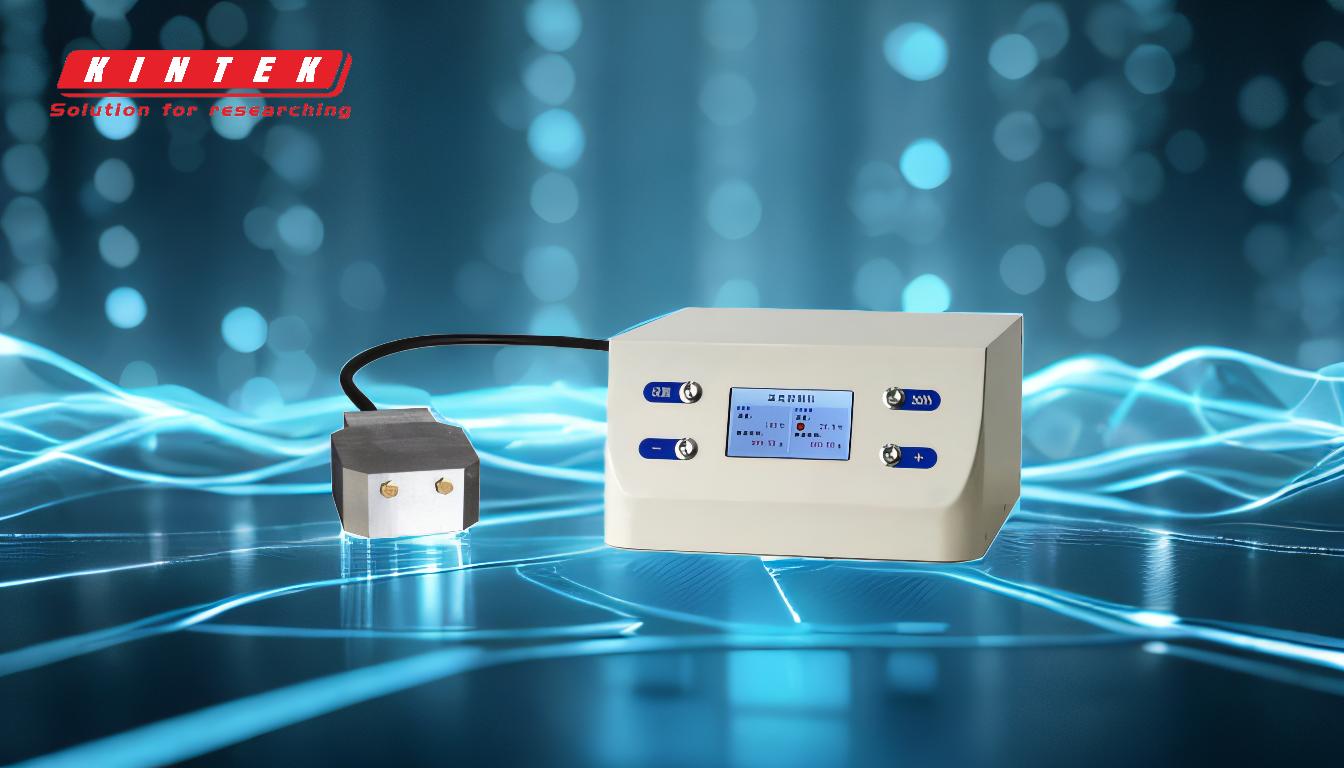
-
Desafíos en el equilibrado del flujo de plástico fundido:
- En los moldes de dos placas con múltiples cavidades, es difícil garantizar una distribución uniforme del plástico fundido en cada cavidad.
- Un flujo irregular puede provocar defectos como disparos cortos, alabeos o dimensiones irregulares de las piezas.
- Este problema se agrava en diseños complejos en los que las cavidades están situadas a distintas distancias de la compuerta.
-
Alineación de la línea de separación con la compuerta:
- La línea de apertura en un molde de dos placas debe alinearse con la compuerta, lo que restringe la flexibilidad del diseño.
- Esta alineación puede complicar el diseño del molde, especialmente en el caso de piezas complejas o configuraciones con varias cavidades.
- También puede aumentar el riesgo de formación de rebabas u otros defectos en la línea de apertura.
-
Flexibilidad de diseño limitada:
- Los moldes de dos placas son menos versátiles que los moldes de tres placas o los sistemas de canal caliente.
- No son ideales para piezas que requieran un encapsulado complejo o con requisitos estéticos específicos.
- La simplicidad de los moldes de dos placas suele tener como contrapartida una reducción de las opciones de personalización.
-
Mayor riesgo de defectos:
- Debido a las dificultades de equilibrado del flujo y alineación de las compuertas, los moldes de dos placas son más propensos a los defectos.
- Entre los problemas más comunes se encuentran las líneas de soldadura, las trampas de aire y la calidad irregular de las piezas.
- Estos defectos pueden aumentar las tasas de rechazo y los costes de producción.
-
Tiempos de ciclo más largos:
- Las limitaciones de los moldes de dos placas pueden provocar tiempos de enfriamiento y de ciclo más largos.
- Esto es especialmente cierto en el caso de los moldes de varias cavidades, en los que puede producirse un enfriamiento desigual.
- Los tiempos de ciclo más largos reducen la eficiencia global de la producción y aumentan los costes operativos.
-
Mayores requisitos de mantenimiento:
- La complejidad de equilibrar el flujo y alinear las compuertas puede provocar un mayor desgaste del molde.
- Se requiere un mantenimiento regular para garantizar un rendimiento constante, lo que aumenta el coste total de propiedad.
-
No apto para todas las aplicaciones:
- Los moldes de dos placas son los más adecuados para piezas sencillas con requisitos de inyección simples.
- Para piezas complejas o aplicaciones de alta precisión, pueden ser más apropiados otros diseños de molde (por ejemplo, moldes de tres placas o sistemas de canal caliente).
Al comprender estas desventajas, los fabricantes pueden tomar decisiones informadas sobre si un molde de dos placas es la opción adecuada para sus necesidades de producción específicas.Aunque ofrecen simplicidad y ahorro de costes, sus limitaciones deben sopesarse cuidadosamente frente a los requisitos del proyecto.
Cuadro sinóptico:
Desventaja | Impacto |
---|---|
Retos del equilibrado de flujos | Llenado desigual, defectos como disparos cortos, alabeos o dimensiones incoherentes. |
Alineación de la línea de partición | Flexibilidad de diseño limitada, mayor riesgo de formación de rebabas. |
Flexibilidad de diseño limitada | Menos versátil para piezas complejas o requisitos estéticos específicos. |
Mayor riesgo de defectos | Las líneas de soldadura, las trampas de aire y la calidad irregular de las piezas aumentan las tasas de desechos. |
Tiempos de ciclo más largos | Una refrigeración desigual reduce la eficiencia de la producción. |
Mayores necesidades de mantenimiento | Mayor desgaste que requiere un mantenimiento regular. |
No apto para todas las aplicaciones | El mejor para piezas sencillas; los diseños complejos pueden necesitar moldes alternativos. |
¿Necesita ayuda para elegir el molde adecuado para su proyecto? Póngase en contacto con nuestros expertos para obtener soluciones a medida.