CVD (deposición química de vapor) y PVD (deposición física de vapor) son dos técnicas de recubrimiento ampliamente utilizadas para insertos, cada una con distintos procesos, propiedades y aplicaciones. La CVD implica reacciones químicas a altas temperaturas, que producen recubrimientos densos y uniformes adecuados para aplicaciones de alta temperatura y resistentes al desgaste. PVD, por otro lado, utiliza procesos físicos en vacío a temperaturas más bajas, lo que da como resultado recubrimientos más delgados y menos densos con excelente adhesión y acabado superficial. La elección entre CVD y PVD depende de factores como la compatibilidad del material, los requisitos de la aplicación y las condiciones de funcionamiento.
Puntos clave explicados:
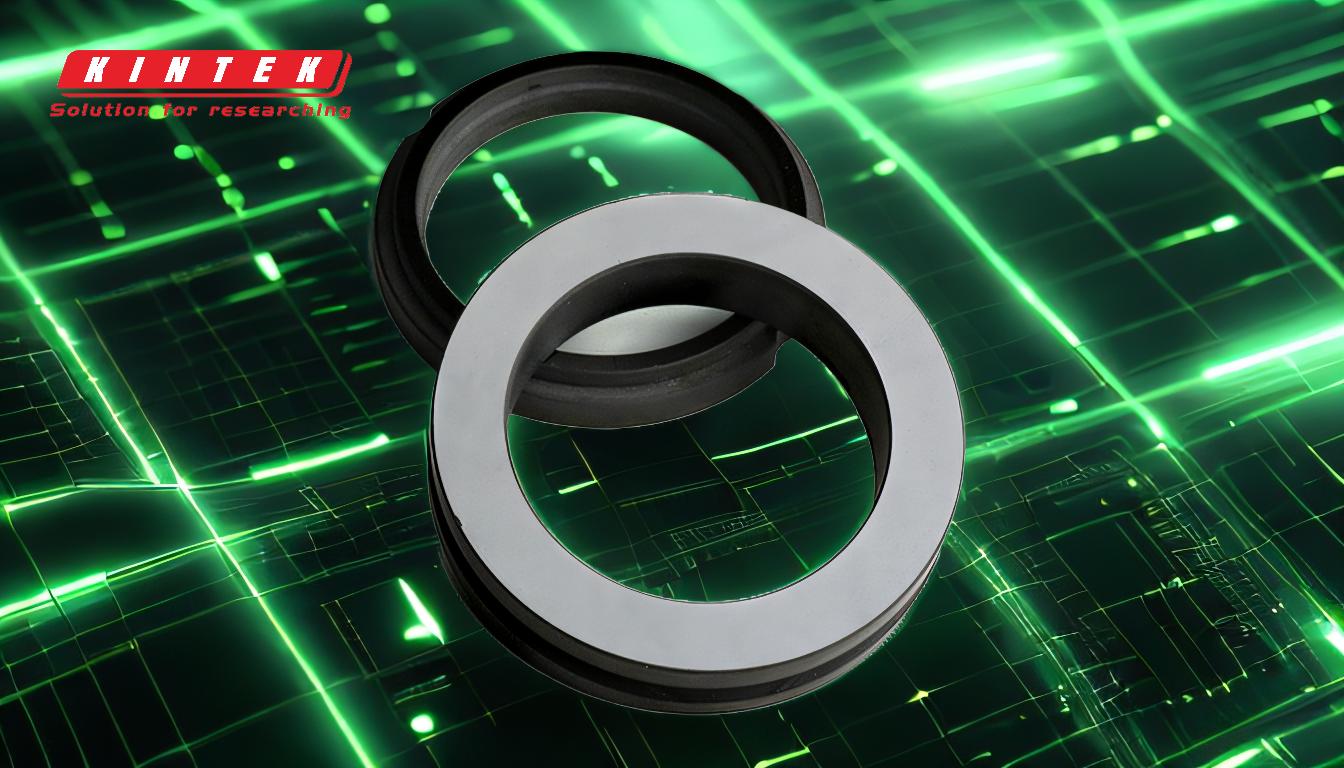
-
Mecanismo de deposición:
- ECV: Utiliza reacciones químicas entre precursores gaseosos y el sustrato para formar un recubrimiento sólido. El proceso es multidireccional, lo que permite una cobertura uniforme incluso en geometrías complejas.
- PVD: Depende de procesos físicos, como la pulverización catódica o la evaporación, para depositar material sobre el sustrato. Es un proceso de línea de visión, lo que significa que solo se recubren las superficies directamente expuestas a la fuente.
-
Temperaturas de funcionamiento:
- ECV: Funciona a altas temperaturas (450°C a 1050°C), lo que puede provocar tensiones de tracción y grietas finas en el revestimiento. Esto lo hace adecuado para aplicaciones de alta temperatura.
- PVD: Funciona a temperaturas más bajas (de 250 °C a 450 °C), lo que reduce el estrés térmico y lo hace adecuado para sustratos sensibles a la temperatura.
-
Materiales de revestimiento:
- ECV: Normalmente limitado a cerámicas y polímeros debido a la naturaleza química del proceso.
- PVD: Puede depositar una gama más amplia de materiales, incluidos metales, aleaciones y cerámicas, lo que ofrece una mayor versatilidad.
-
Propiedades del recubrimiento:
- ECV: Produce recubrimientos más densos y uniformes, ideal para aplicaciones que requieren alta resistencia al desgaste y estabilidad térmica.
- PVD: Da como resultado recubrimientos menos densos y menos uniformes, pero ofrece una adhesión y un acabado superficial superiores, lo que lo hace adecuado para aplicaciones de precisión.
-
Velocidad y espesor de aplicación:
- ECV: Lleva más tiempo aplicarlo debido al proceso de reacción química, pero puede producir recubrimientos más gruesos (10~20μm).
- PVD: Es más rápido de aplicar, pero generalmente produce recubrimientos más delgados (3~5 μm), que son suficientes para muchas aplicaciones de precisión.
-
Estrés y grietas:
- ECV: Las altas temperaturas de procesamiento pueden provocar tensiones de tracción y grietas finas, que pueden afectar la durabilidad del recubrimiento.
- PVD: Forma tensión de compresión durante el enfriamiento, lo que reduce la probabilidad de agrietamiento y mejora la durabilidad del recubrimiento.
-
Aplicaciones:
- ECV: Se utiliza comúnmente en aplicaciones resistentes al desgaste y a altas temperaturas, como herramientas de corte y componentes aeroespaciales.
- PVD: Preferido para aplicaciones que requieren excelente acabado superficial y adhesión, como dispositivos médicos y herramientas de mecanizado de precisión.
Comprender estas diferencias ayuda a seleccionar el método de recubrimiento adecuado según los requisitos específicos de la aplicación.
Tabla resumen:
Aspecto | ECV | PVD |
---|---|---|
Mecanismo de deposición | Reacciones químicas, cobertura multidireccional. | Procesos físicos, cobertura de línea de visión. |
Temperatura de funcionamiento | Alto (450°C a 1050°C), adecuado para aplicaciones de alta temperatura | Inferior (de 250 °C a 450 °C), ideal para sustratos sensibles a la temperatura |
Materiales de revestimiento | Limitado a cerámicas y polímeros. | Amplia gama, incluidos metales, aleaciones y cerámicas. |
Propiedades del recubrimiento | Denso, uniforme, alta resistencia al desgaste, estabilidad térmica. | Más delgado, menos denso, adhesión superior, excelente acabado superficial |
Velocidad de aplicación | Recubrimientos más lentos y gruesos (10~20μm) | Recubrimientos más rápidos y delgados (3~5μm) |
Estrés y grietas | Tensión de tracción, posibles grietas finas | Tensión de compresión, agrietamiento reducido |
Aplicaciones | Alta temperatura, resistente al desgaste (por ejemplo, herramientas de corte, aeroespacial) | Aplicaciones de precisión (por ejemplo, dispositivos médicos, herramientas de mecanizado) |
¿Aún no estás seguro de qué revestimiento es el adecuado para tus inserciones? Póngase en contacto con nuestros expertos hoy para asesoramiento personalizado!