Los revestimientos PVD (deposición física de vapor) son conocidos por sus propiedades finas, duraderas y de alto rendimiento.El tamaño o grosor de los revestimientos PVD suele oscilar entre 0,25 micras y 5 micras, en función de la aplicación y el material.Esta delgadez garantiza que los revestimientos no alteren las especificaciones de las piezas de ingeniería, al tiempo que proporcionan una excelente dureza, resistencia a la corrosión y durabilidad.Los revestimientos PVD se utilizan ampliamente en sectores como la joyería, la electrónica y la fabricación debido a su rendimiento superior en comparación con los métodos de revestimiento tradicionales, como la galvanoplastia.Factores como el material del sustrato, el grosor del revestimiento y las condiciones de aplicación influyen en la longevidad y eficacia de los revestimientos PVD.
Explicación de los puntos clave:
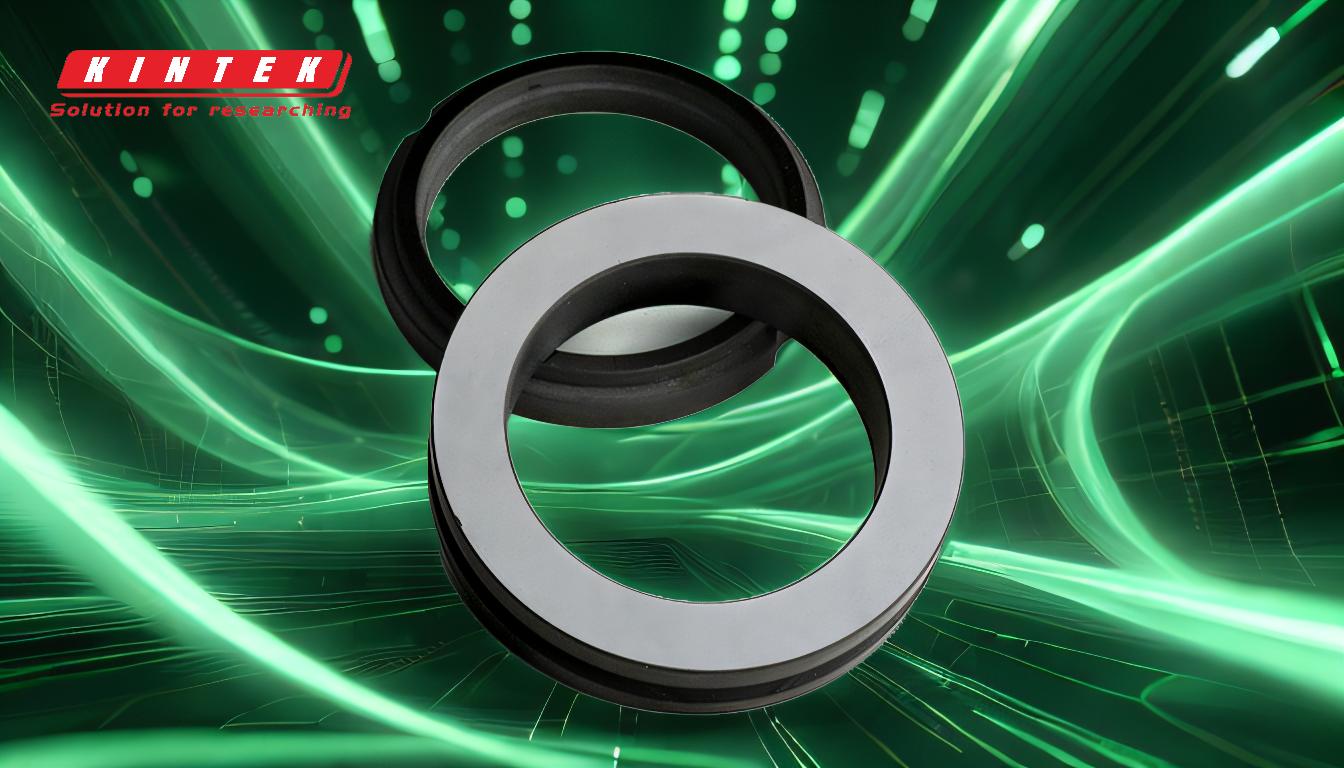
-
Gama de espesores típicos de los recubrimientos PVD:
- Los revestimientos de PVD suelen ser muy finos, desde 0,25 micras a 5 micras .Esta gama es significativamente más fina que el diámetro de un cabello humano, que es de unas 70 micras.La delgadez garantiza que el revestimiento no altere las dimensiones o especificaciones del material subyacente, lo que lo hace ideal para aplicaciones de precisión.
-
Aplicaciones y variaciones de espesor:
-
El grosor de los revestimientos PVD puede variar en función de la aplicación.Por ejemplo:
- En joyería el grosor del revestimiento suele oscilar entre 0,25 micras y 5 micras, lo que proporciona un acabado duradero y estéticamente agradable.
- En aplicaciones industriales como el recubrimiento de obleas, los espesores pueden ser tan bajos como 3 nanómetros como se ve en el ejemplo de un recubrimiento de Oro/Paladio aplicado a una oblea de 6 pulgadas utilizando un recubridor por pulverización catódica.
-
El grosor de los revestimientos PVD puede variar en función de la aplicación.Por ejemplo:
-
Comparación con otros métodos de recubrimiento:
- Los revestimientos PVD son más finos que los producidos por deposición química de vapor (CVD) que suelen oscilar entre 5 y 10 micras.A pesar de su delgadez, los revestimientos PVD son más duros, más resistentes a la corrosión y más respetuosos con el medio ambiente que los métodos tradicionales, como la galvanoplastia y la pintura.
-
Durabilidad y longevidad:
-
Los revestimientos de PVD son conocidos por su durabilidad.
10 años a cientos de años
dependiendo de factores como
- El material del sustrato que se recubre.
- El espesor del revestimiento .
- Las condiciones de aplicación como la exposición a altas temperaturas o entornos corrosivos.
-
Los revestimientos de PVD son conocidos por su durabilidad.
10 años a cientos de años
dependiendo de factores como
-
Ventajas de los recubrimientos PVD:
- Dureza y resistencia a la corrosión:Los revestimientos de PVD son más duros y resistentes a la corrosión que los revestimientos galvánicos.
- Rendimiento a altas temperaturas:Pueden soportar altas temperaturas y tienen buena resistencia al impacto.
- Resistencia a la abrasión:Con una capa superior transparente adicional resistente a la abrasión, los revestimientos PVD consiguen una excelente resistencia al desgaste.
- Respetuoso con el medio ambiente:El PVD es un proceso más sostenible y ecológico que los métodos de recubrimiento tradicionales.
-
Proceso de producción:
-
Los revestimientos PVD se producen por
condensación de vapores
de materiales como metales, carbono, cerámica, vidrio o polímeros sobre una superficie adecuada.Las dos tecnologías de recubrimiento PVD más utilizadas son:
- Evaporación:Consiste en calentar el material de revestimiento hasta que se vaporiza y depositarlo sobre el sustrato.
- Pulverización catódica:Utiliza un plasma para expulsar átomos de un material objetivo, que luego se depositan sobre el sustrato.
-
Los revestimientos PVD se producen por
condensación de vapores
de materiales como metales, carbono, cerámica, vidrio o polímeros sobre una superficie adecuada.Las dos tecnologías de recubrimiento PVD más utilizadas son:
-
Importancia de la delgadez:
- La delgadez de los revestimientos de PVD (de 0,5 micras a 5 micras) garantiza que no alteren las las especificaciones de las piezas .Esto es especialmente importante en sectores en los que la precisión y la exactitud dimensional son fundamentales, como el electrónico y el aeroespacial.
Al conocer el tamaño y las propiedades de los revestimientos PVD, los compradores pueden tomar decisiones informadas sobre su idoneidad para aplicaciones específicas, garantizando un rendimiento y una longevidad óptimos.
Tabla resumen:
Aspecto clave | Detalles |
---|---|
Grosor típico | 0,25 micras a 5 micras |
Aplicaciones | Joyería (0,25-5 micras), Industrial (tan bajo como 3 nanómetros) |
Comparación con CVD | Más fino (5-10 micras para CVD), más duro y más resistente a la corrosión |
Durabilidad | De 10 a cientos de años, según el sustrato y las condiciones |
Ventajas | Alta dureza, resistencia a la corrosión, rendimiento a altas temperaturas |
Proceso de producción | Evaporación y sputtering |
Importancia de la finura | Mantiene las especificaciones de la pieza, ideal para aplicaciones de precisión |
¿Está preparado para mejorar sus aplicaciones con recubrimientos PVD? Póngase en contacto con nosotros para obtener más información.