El revestimiento de carbono tipo diamante (DLC) se aplica mediante técnicas de deposición avanzadas que garantizan un revestimiento resistente, duradero y de alto rendimiento.Los métodos más comunes son el depósito físico en fase vapor (PVD) y el depósito químico en fase vapor (CVD), con variaciones como el CVD asistido por plasma de radiofrecuencia (RF PECVD) y el CVD de filamento caliente.Estos métodos implican la creación de un entorno controlado en una cámara de vacío, donde los átomos de carbono se activan y depositan sobre el sustrato.La elección del método depende del material del sustrato, las propiedades deseadas del revestimiento y los requisitos de la aplicación.Los revestimientos de DLC suelen ser finos (de 0,5 a 2,5 micras) y ofrecen una excelente resistencia al desgaste, baja fricción y mayor durabilidad.
Explicación de los puntos clave:
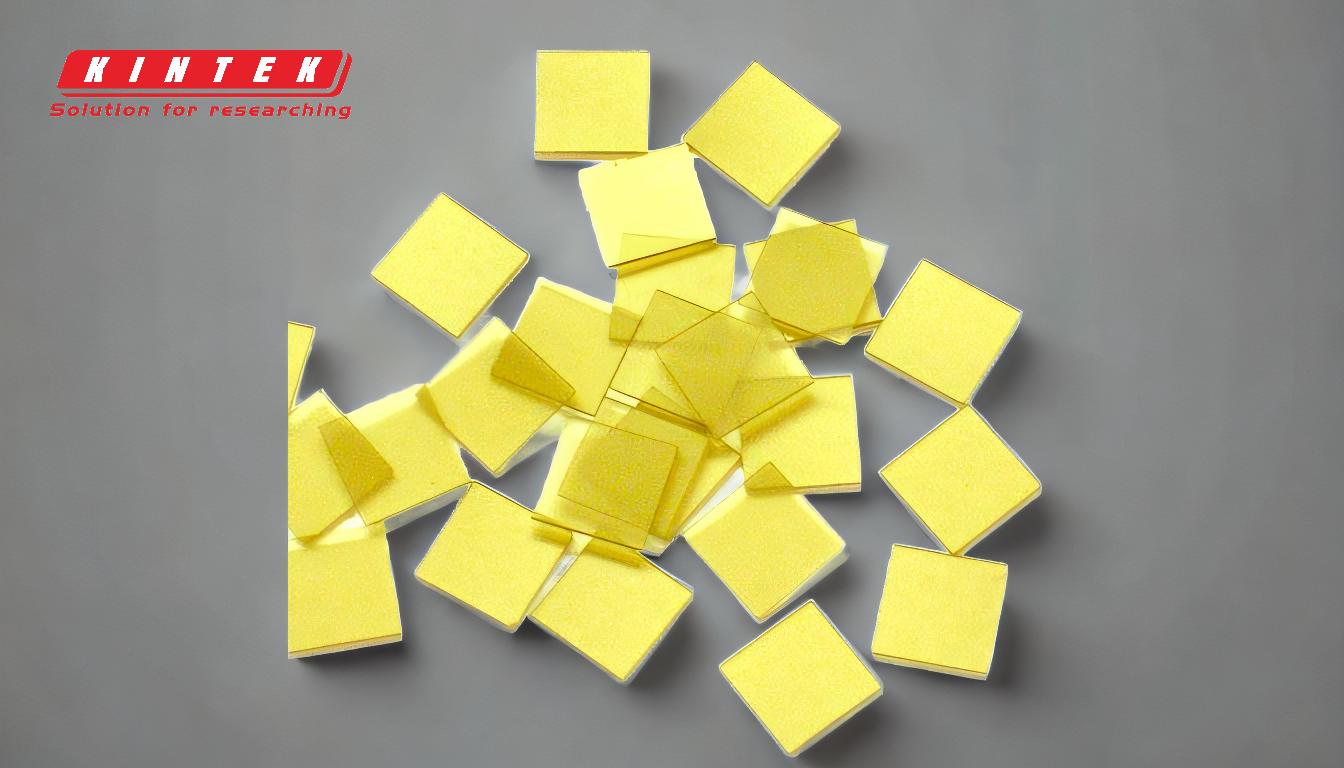
-
Descripción general de la aplicación de recubrimientos DLC
- Los recubrimientos DLC se aplican mediante técnicas de deposición avanzadas para crear una capa fina y duradera de carbono con una proporción significativa de enlaces sp3.
- El proceso de recubrimiento se adapta al material del sustrato y a la aplicación prevista, garantizando un rendimiento óptimo.
-
Métodos de deposición habituales
-
Deposición física en fase vapor (PVD):
- Consiste en evaporar un material fuente y dejar que se condense sobre el sustrato.
- Adecuado para aplicar revestimientos de DLC en herramientas de carburo, con un grosor típico de 0,5 a 2,5 micras.
- Las ventajas incluyen un control preciso del grosor y la uniformidad del revestimiento.
-
Deposición química en fase vapor (CVD):
- Consiste en depositar átomos de carbono a partir de una fase gaseosa (por ejemplo, hidrógeno y metano) sobre el sustrato.
- Entre las técnicas más comunes se encuentran la CVD por filamento caliente, la CVD asistida por plasma de radiofrecuencia (RF PECVD) y la CVD por plasma de microondas (MPCVD).
- Requiere altas temperaturas (más de 750°C) para activar las moléculas de gas y formar una película de diamante.
-
Deposición física en fase vapor (PVD):
-
Proceso paso a paso del recubrimiento CVD
-
Preparación:
- El sustrato (por ejemplo, herramientas de carburo de tungsteno) se limpia y se prepara para garantizar una adhesión adecuada del revestimiento.
-
Carga en la cámara:
- Las herramientas preparadas se colocan en una cámara de vacío que contiene gases de hidrógeno y metano.
-
Activación de las moléculas de gas:
- Los hilos de tungsteno calentados a más de 2.300°C proporcionan la energía necesaria para romper las moléculas de gas y calentar las herramientas a más de 750°C.
-
Deposición de átomos de carbono:
- Los átomos de carbono activados se recombinan en la superficie de la herramienta para formar una película de diamante puro.
-
Enfriamiento y retirada:
- Tras la deposición, las herramientas se enfrían y se retiran de la cámara, listas para su uso.
-
Preparación:
-
Ventajas de los distintos métodos
-
PVD:
- Temperaturas de procesamiento más bajas, lo que lo hace adecuado para sustratos sensibles a la temperatura.
- Alta precisión y uniformidad en el espesor del revestimiento.
-
CVD:
- Produce películas de diamante puro de alta calidad con excelente adherencia.
- Ideal para aplicaciones de alta temperatura y sustratos que puedan soportar condiciones extremas.
-
PVD:
-
Aplicaciones de los recubrimientos DLC
-
Herramientas de corte:
- Mejora la resistencia al desgaste y prolonga la vida útil de las herramientas.
-
Componentes de automoción:
- Reduce la fricción y mejora la eficiencia del combustible en las piezas del motor.
-
Dispositivos médicos:
- Proporciona biocompatibilidad y resistencia al desgaste para instrumentos quirúrgicos.
-
Electrónica:
- Mejora la durabilidad y el rendimiento de componentes como discos duros y sensores.
-
Herramientas de corte:
-
Consideraciones para los compradores de equipos y consumibles
-
Compatibilidad del sustrato:
- Asegúrese de que el método elegido es compatible con el material del sustrato (por ejemplo, carburo, acero o cerámica).
-
Espesor y uniformidad del revestimiento:
- Evalúe el grosor y la uniformidad necesarios para la aplicación específica.
-
Coste y escalabilidad:
- Considere la rentabilidad y escalabilidad del método elegido para la producción a gran escala.
-
Factores medioambientales y de seguridad:
- Evalúe el impacto medioambiental y los requisitos de seguridad del proceso de deposición.
-
Compatibilidad del sustrato:
Al comprender estos puntos clave, los compradores de equipos y consumibles pueden tomar decisiones informadas sobre el mejor método de recubrimiento de DLC para sus necesidades específicas, garantizando un rendimiento y una rentabilidad óptimos.
Tabla resumen:
Aspecto | Detalles |
---|---|
Métodos comunes | PVD, CVD (RF PECVD, CVD de filamento caliente) |
Espesor del revestimiento | 0,5 a 2,5 micras |
Principales ventajas | Resistencia al desgaste, baja fricción, durabilidad |
Aplicaciones | Herramientas de corte, piezas de automoción, dispositivos médicos, electrónica |
Compatibilidad de sustratos | Carburo, acero, cerámica |
Rango de temperatura | PVD:Temperaturas más bajas; CVD:Más de 750°C |
Factores ambientales | Cámara de vacío, entorno de gas controlado |
Descubra la solución de revestimiento de DLC ideal para sus necesidades. contacte hoy mismo con nuestros expertos ¡!