El número de placas utilizadas en un molde de inyección depende del diseño y la complejidad del molde.Normalmente, los moldes se diseñan como moldes de dos o tres placas.Los moldes de dos placas son más sencillos y constan de dos placas principales: una para el núcleo y otra para la cavidad.Estos moldes suelen utilizarse para piezas sencillas y requieren menos tiempo de preparación.Por otro lado, los moldes de tres placas incluyen una placa adicional, lo que permite diseños de piezas más complejos y la expulsión automática de piezas.La elección entre moldes de dos o tres placas depende de la geometría de la pieza, los requisitos de producción y los costes.
Explicación de los puntos clave:
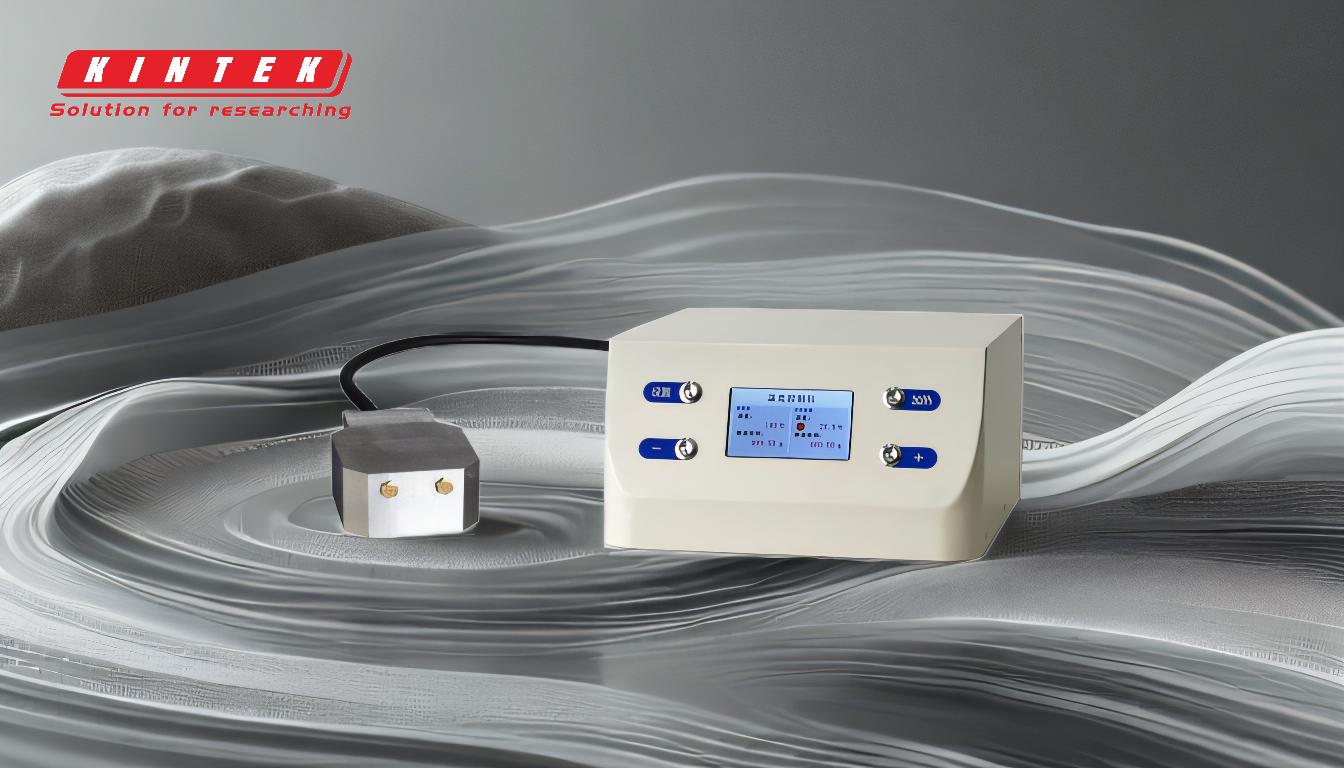
-
Moldes de dos placas:
- Estructura:Consta de dos placas principales: una para el núcleo y otra para la cavidad.
- Uso:Ideal para piezas más simples con geometrías sencillas.
-
Ventajas:
- Más fácil de diseñar y fabricar.
- Menor coste gracias al menor número de componentes.
- Puesta a punto más rápida y ciclos de producción más cortos.
- Desventajas:Flexibilidad limitada para diseños de piezas complejos o sistemas de expulsión automatizados.
-
Moldes de tres placas:
- Estructura:Incluye una placa adicional, lo que lo convierte en un sistema de tres placas.
- Uso:Adecuado para piezas más complejas que requieren múltiples puertas o expulsión automática.
-
Ventajas:
- Mayor flexibilidad en el diseño de piezas.
- Permite múltiples puntos de inyección, mejorando la calidad de la pieza.
- Admite la expulsión automática de piezas, lo que reduce el trabajo manual.
-
Desventajas:
- Diseño y proceso de fabricación más complejos.
- Mayor coste debido a los componentes adicionales.
- Mayor tiempo de preparación y ciclos de producción.
-
Factores que influyen en la elección:
- Parte Complejidad:Las piezas complejas con geometrías intrincadas o múltiples características pueden requerir un molde de tres placas.
- Volumen de producción:La producción de gran volumen puede beneficiarse de la eficacia de los moldes de dos placas, mientras que las piezas de bajo volumen o personalizadas pueden requerir la flexibilidad de los moldes de tres placas.
- Consideraciones sobre costes:Los moldes de dos placas suelen ser más rentables, pero la funcionalidad añadida de los moldes de tres placas puede justificar el mayor coste para determinadas aplicaciones.
- Duración del ciclo:Los moldes de dos placas suelen tener tiempos de ciclo más cortos, lo que los hace más adecuados para la producción a alta velocidad.
-
Consideraciones prácticas:
- Utillaje y mantenimiento:Los moldes de tres placas requieren un utillaje y un mantenimiento más sofisticados, lo que puede repercutir en los costes operativos a largo plazo.
- Flujo de materiales:El diseño de las placas del molde afecta al flujo del plástico fundido, influyendo en la calidad y consistencia de la pieza.
- Mecanismo de expulsión:Los moldes de tres placas suelen incluir sistemas de expulsión automatizados, que pueden mejorar la eficacia de la producción pero aumentan la complejidad del molde.
Al comprender estos puntos clave, un comprador puede tomar una decisión informada sobre si optar por un molde de dos o tres placas en función de los requisitos específicos de su proyecto.
Tabla resumen:
Característica | Moldes de dos placas | Moldes de tres placas |
---|---|---|
Estructura | Dos placas principales (núcleo y cavidad) | Tres placas (placa adicional incluida) |
Utilización | Piezas simples con diseños sencillos | Piezas complejas con múltiples compuertas |
Ventajas | Diseño más sencillo, menor coste, configuración más rápida | Mayor flexibilidad, expulsión automática |
Desventajas | Flexibilidad limitada para diseños complejos | Coste más elevado, mayor tiempo de preparación |
Ideal para | Grandes volúmenes, geometrías sencillas | Bajo volumen, geometrías complejas |
¿Aún no sabe qué molde es el adecuado para su proyecto? Póngase en contacto con nuestros expertos para un asesoramiento personalizado.