Los reactores de lecho fluidizado (FBR) se utilizan ampliamente en diversas industrias debido a sus ventajas, como la mezcla uniforme de partículas, los gradientes de temperatura y el funcionamiento continuo.Sin embargo, también presentan varios inconvenientes notables.Entre ellas se encuentran el aumento del tamaño del recipiente del reactor, mayores requisitos de bombeo y caída de presión, arrastre de partículas, erosión de los componentes internos y escenarios de pérdida de presión.Además, los pirolizadores de lecho fluidizado, un tipo específico de FBR, se enfrentan a retos como la necesidad de partículas de pequeño tamaño, grandes cantidades de gases inertes y elevados costes de funcionamiento.Comprender estos inconvenientes es crucial para tomar decisiones informadas a la hora de considerar los FBR para aplicaciones específicas.
Explicación de los puntos clave:
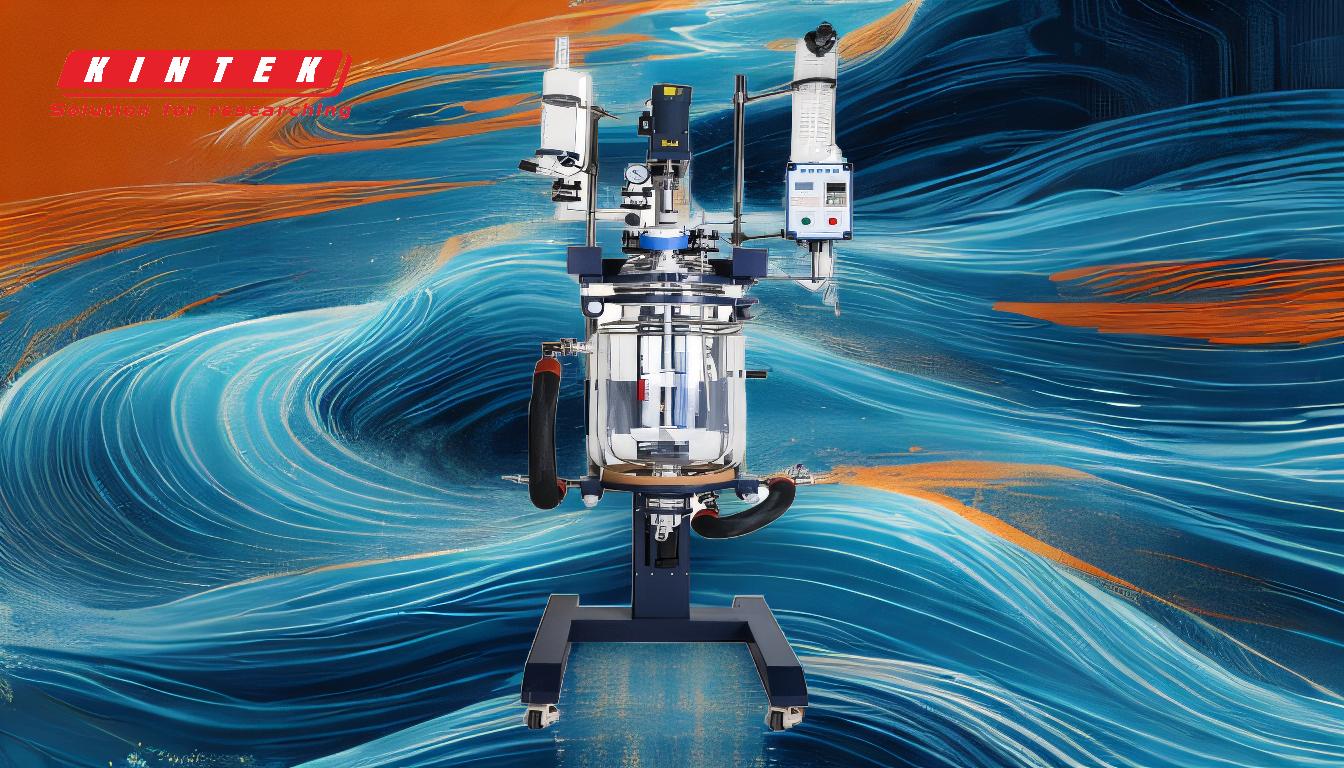
-
Aumento del tamaño de la vasija del reactor:
- Los reactores de lecho fluidizado suelen requerir recipientes de mayor tamaño que otros tipos de reactores.Esto se debe a la necesidad de acomodar las partículas fluidizadas y garantizar unas condiciones de mezcla y reacción adecuadas.El mayor tamaño puede conllevar mayores costes de capital y más requisitos de espacio, lo que puede no ser factible para todas las aplicaciones.
-
Mayores requisitos de bombeo y caída de presión:
- Los FBR suelen requerir una mayor potencia de bombeo para mantener el estado fluidizado de las partículas.Esto se traduce en un aumento del consumo de energía y de los costes operativos.Además, la caída de presión a través del lecho puede ser significativa, lo que requiere sistemas de bombeo robustos y costosos para mantener los caudales deseados.
-
Arrastre de partículas:
- Uno de los retos de los FBR es el arrastre de partículas finas en la corriente de gas.Esto puede provocar la pérdida de reactivos o productos valiosos y puede requerir equipos adicionales, como ciclones o filtros, para capturar y reciclar las partículas arrastradas.Esto añade complejidad y coste al sistema.
-
Erosión de los componentes internos:
- El movimiento continuo de partículas en un lecho fluidizado puede provocar la erosión de los componentes internos, como las paredes del reactor, las placas distribuidoras y los intercambiadores de calor.Esta erosión puede llevar a un mantenimiento frecuente y a la sustitución de piezas, aumentando los costes operativos generales y el tiempo de inactividad.
-
Escenarios de pérdida de presión:
- Los FBR son susceptibles de sufrir pérdidas de presión, que pueden interrumpir el proceso de fluidización y afectar al rendimiento global del reactor.Gestionar y mitigar estas pérdidas de presión requiere un diseño y una supervisión cuidadosos, lo que aumenta la complejidad y el coste del sistema.
-
Necesidad de partículas de pequeño tamaño:
- Los pirolizadores de lecho fluidizado, un tipo específico de FBR, requieren partículas de pequeño tamaño para lograr un rendimiento óptimo.Esto requiere pasos de procesamiento adicionales para reducir el tamaño de las partículas, lo que puede aumentar el coste global y la complejidad del sistema.
-
Gran cantidad de gases inertes:
- El funcionamiento de los pirólizadores de lecho fluidizado suele requerir una gran cantidad de gases inertes para mantener las condiciones de reacción deseadas.Esto puede suponer mayores costes operativos y la necesidad de infraestructuras adicionales de manipulación y almacenamiento de gases.
-
Costes de explotación elevados:
- La combinación de unos mayores requisitos de bombeo, el arrastre de partículas, la erosión de los componentes internos y la necesidad de partículas de pequeño tamaño y gases inertes contribuye a los elevados costes de funcionamiento asociados a los FBR.Estos costes pueden ser un inconveniente importante, especialmente para aplicaciones en las que la rentabilidad es un factor crítico.
En resumen, aunque los reactores de lecho fluidizado ofrecen varias ventajas, como la mezcla uniforme y los gradientes de temperatura, también presentan desventajas notables que deben considerarse cuidadosamente.Entre ellas se encuentran el aumento del tamaño del reactor, los mayores requisitos de bombeo, el arrastre de partículas, la erosión de los componentes internos, los escenarios de pérdida de presión y los elevados costes de funcionamiento.Comprender estos inconvenientes es esencial para tomar decisiones informadas a la hora de seleccionar y diseñar los FBR para aplicaciones específicas.
Cuadro sinóptico:
Desventaja | Descripción |
---|---|
Mayor tamaño de la vasija del reactor | Los recipientes más grandes aumentan los costes de capital y las necesidades de espacio. |
Mayores necesidades de bombeo | Requiere más energía y sistemas robustos para mantener la fluidización. |
Arrastre de partículas | Las partículas finas pueden escapar, requiriendo equipo adicional para su recuperación. |
Erosión de los componentes internos | El movimiento continuo de partículas provoca desgaste, lo que obliga a un mantenimiento frecuente. |
Escenarios de pérdida de presión | Las caídas de presión pueden interrumpir la fluidización, lo que requiere un diseño y una supervisión cuidadosos. |
Necesidad de partículas de pequeño tamaño | Procesamiento adicional necesario para reducir el tamaño de las partículas, lo que aumenta los costes. |
Gran cantidad de gases inertes | Elevados costes operativos debido a la necesidad de gases inertes. |
Elevados costes operativos | La combinación de estos factores da lugar a importantes gastos de explotación. |
¿Necesita ayuda para decidir si los reactores de lecho fluidizado son adecuados para su aplicación? Póngase en contacto con nuestros expertos hoy mismo.