El prensado isostático en caliente (HIP) es un proceso de fabricación que combina altas temperaturas y presión isostática para densificar materiales, eliminar defectos y mejorar las propiedades mecánicas.Se utiliza mucho en sectores como el aeroespacial, la automoción y los dispositivos médicos para fabricar componentes de alto rendimiento con una integridad estructural superior.El proceso consiste en colocar los materiales en un recipiente de alta presión lleno de un gas inerte, normalmente argón, y someterlos a una presión uniforme desde todas las direcciones mientras se calientan.Así se obtienen productos densos y sin huecos con propiedades mejoradas como dureza, resistencia al desgaste y resistencia a la fatiga.El HIP es especialmente eficaz para consolidar polvos, unir materiales distintos y resolver problemas en piezas fundidas e impresas en 3D.
Explicación de los puntos clave:
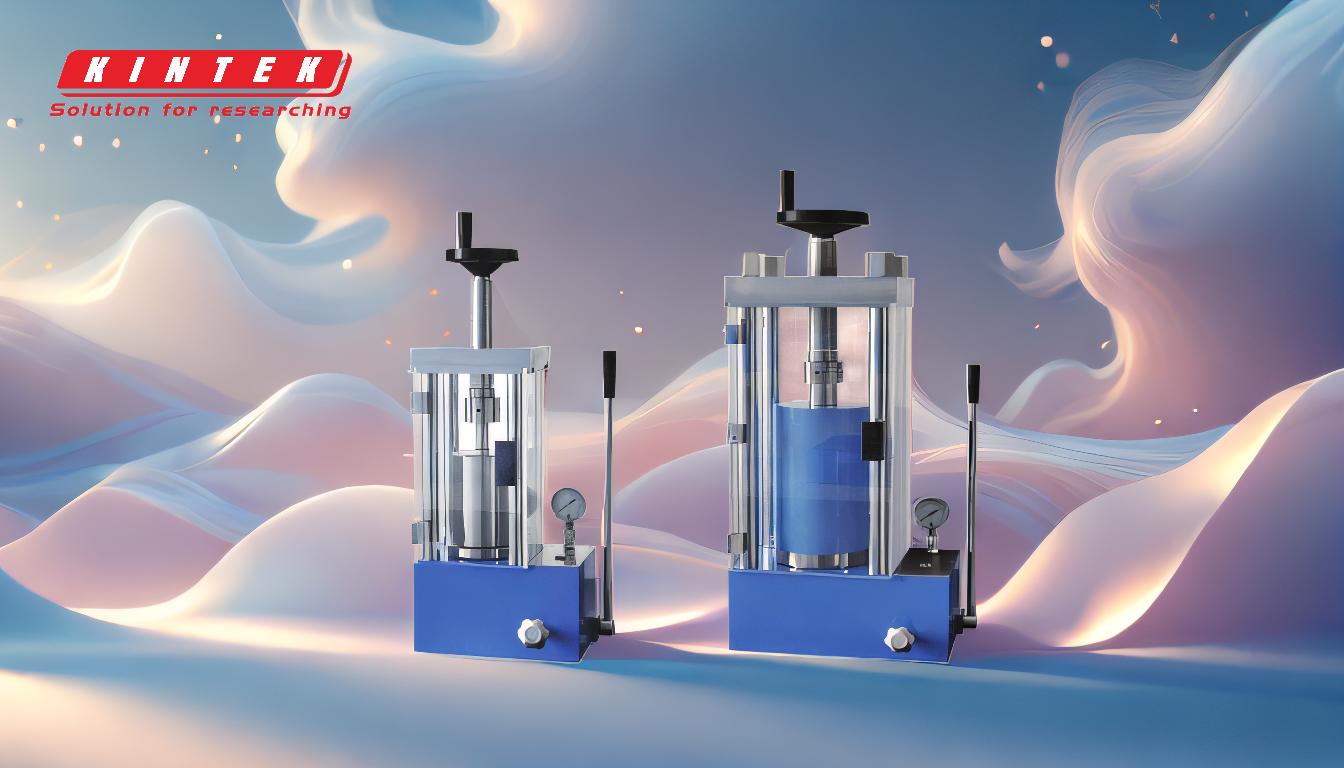
-
Definición y resumen del proceso:
- El prensado isostático en caliente (HIP) es una técnica que aplica alta temperatura y presión uniforme en tres dimensiones para densificar materiales o unir componentes.
- El proceso consiste en colocar el material en un recipiente sellado o molde flexible, que se somete a alta presión (normalmente con un gas inerte como el argón) y temperaturas elevadas.
- Esta combinación de calor y presión elimina los huecos, la microcontracción y la porosidad, dando como resultado materiales densos y de alto rendimiento.
-
Componentes clave del HIP:
- Recipiente de alta presión:El núcleo del sistema HIP, capaz de soportar presiones y temperaturas extremas.
- Gas inerte (Argón):Se utiliza como medio de transferencia de presión para garantizar una distribución uniforme de la presión y evitar la oxidación o la contaminación.
- Sistema de calefacción:Proporciona la energía térmica necesaria para facilitar la sinterización, la unión por difusión o la densificación.
-
Aplicaciones principales:
- Eliminación de defectos en piezas moldeadas:El HIP se utiliza ampliamente para eliminar la microcontracción y la porosidad en las piezas fundidas de metal, mejorando sus propiedades mecánicas.
- Consolidación del polvo:El proceso es eficaz para compactar materiales en polvo en componentes densos y uniformes con geometrías complejas.
- Adhesión por difusión (revestimiento):El HIP permite unir materiales distintos, creando uniones resistentes y duraderas sin necesidad de adhesivos o fijaciones adicionales.
- Mejora de las piezas de fabricación aditiva:En el caso de los componentes impresos en 3D, el HIP resuelve problemas como la porosidad y la mala adherencia de las capas, lo que se traduce en una microestructura uniforme y un mejor rendimiento.
-
Ventajas del HIP:
- Propiedades superiores del material:El HIP mejora la densidad, la ductilidad, la resistencia a la fatiga y la estabilidad térmica, por lo que es ideal para aplicaciones de alto esfuerzo.
- Formas complejas:El proceso puede producir formas intrincadas y complejas difíciles de conseguir con los métodos de fabricación tradicionales.
- Reducción del tiempo de producción:El HIP consolida múltiples etapas de fabricación, como el tratamiento térmico y el envejecimiento, en un único proceso, lo que agiliza la producción.
-
Aplicaciones industriales:
- Aeroespacial:El HIP se utiliza para fabricar álabes de turbinas, componentes de motores y otras piezas críticas que requieren gran resistencia y fiabilidad.
- Dispositivos médicos:El proceso se emplea para fabricar implantes biocompatibles e instrumentos quirúrgicos con excelentes propiedades mecánicas.
- Automoción:El HIP mejora el rendimiento y la durabilidad de los componentes del motor, las piezas de la transmisión y otras piezas de automoción sometidas a grandes esfuerzos.
- Energía:El HIP se utiliza en la producción de componentes para reactores nucleares, equipos de petróleo y gas y sistemas de energías renovables.
-
Comparación con los procesos convencionales:
- A diferencia de los métodos de prensado tradicionales, que aplican presión en una sola dirección, el HIP garantiza una distribución uniforme de la presión, lo que da lugar a propiedades isotrópicas.
- El HIP consigue mayores densidades y mejores propiedades del material a temperaturas de sinterización más bajas que el sinterizado convencional.
-
Futuras tendencias e innovaciones:
- Integración con la fabricación aditiva:El HIP se utiliza cada vez más para mejorar las propiedades de las piezas impresas en 3D, abordando retos como la porosidad y la anisotropía.
- Materiales avanzados:El proceso se está adaptando a nuevos materiales, como la cerámica y los compuestos, para ampliar sus aplicaciones.
- Automatización y optimización de procesos:Los avances en los sistemas de automatización y control están mejorando la eficacia y repetibilidad de los procesos de HIP.
En resumen, el prensado isostático en caliente es una técnica de fabricación versátil y potente que mejora las propiedades de los materiales, elimina defectos y permite la producción de componentes complejos de alto rendimiento.Sus aplicaciones abarcan una amplia gama de industrias, y las innovaciones en curso siguen ampliando sus capacidades y eficiencia.
Cuadro sinóptico:
Aspecto | Detalles |
---|---|
Resumen del proceso | Combina alta temperatura y presión uniforme para densificar materiales. |
Componentes clave | Recipiente de alta presión, gas inerte (argón) y sistema de calentamiento. |
Aplicaciones principales | Eliminación de defectos en piezas fundidas, consolidación de polvos, unión por difusión. |
Ventajas | Propiedades superiores del material, formas complejas, tiempo de producción reducido. |
Usos industriales | Aeroespacial, dispositivos médicos, automoción, energía. |
Tendencias futuras | Integración con fabricación aditiva, materiales avanzados y automatización. |
Descubra cómo el prensado isostático en caliente puede transformar su proceso de fabricación. póngase en contacto con nosotros ¡!