CVD (deposición química de vapor) y PVD (deposición física de vapor) son dos técnicas de recubrimiento ampliamente utilizadas para insertos, cada una con distintos procesos, propiedades y aplicaciones. La CVD implica reacciones químicas a altas temperaturas (800–1000 °C) para depositar recubrimientos más gruesos (10–20 μm), mientras que la PVD utiliza la vaporización física a temperaturas más bajas (250–500 °C) para crear películas más delgadas y ultraduras (3 –5 µm). Los recubrimientos CVD son más densos y uniformes, pero pueden introducir tensiones de tracción y grietas finas debido a las altas temperaturas de procesamiento. Los recubrimientos PVD, por otro lado, generan tensiones de compresión y son ideales para aplicaciones de precisión que requieren superficies lisas y duraderas. La elección entre CVD y PVD depende de factores como el espesor del recubrimiento, la temperatura de funcionamiento y los requisitos específicos de la aplicación.
Puntos clave explicados:
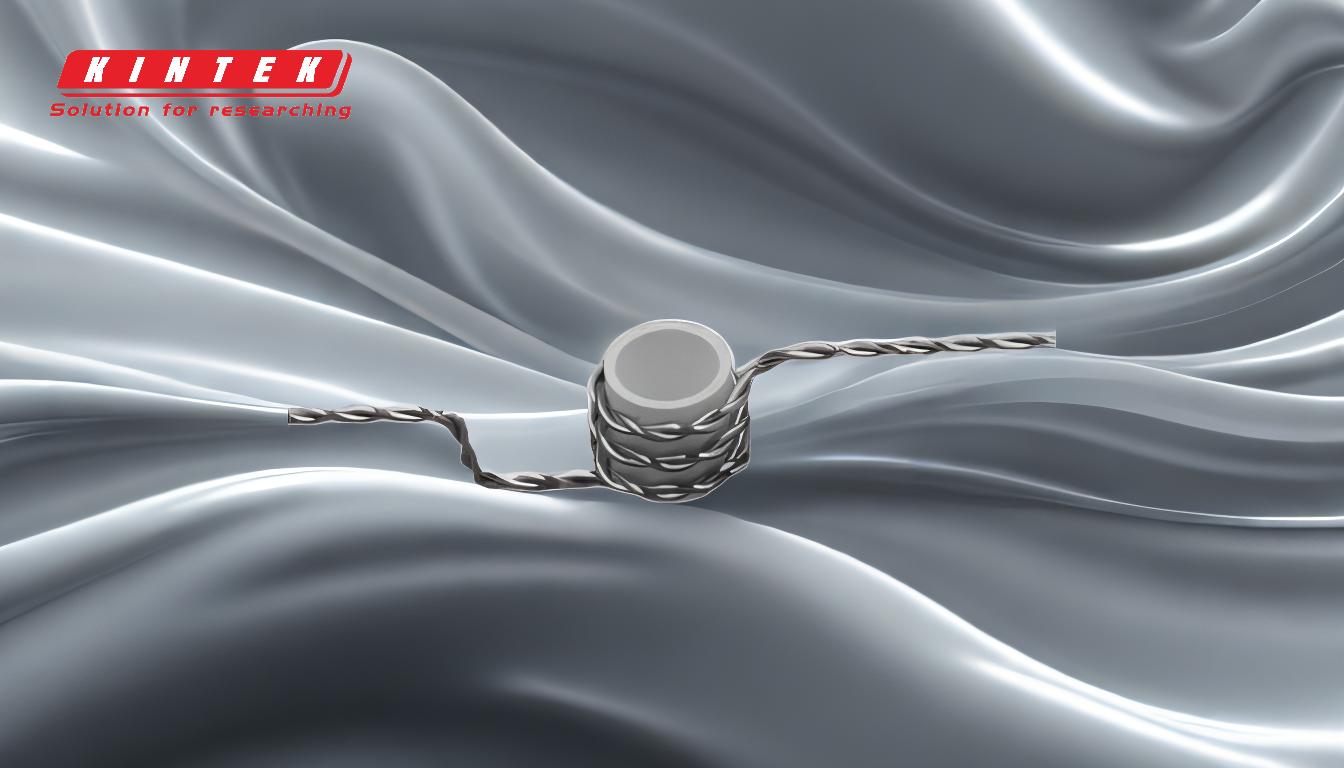
-
Mecanismo de deposición:
- ECV: Implica reacciones químicas entre precursores gaseosos y el sustrato a altas temperaturas (800–1000 °C). Esto da como resultado una deposición multidireccional, donde el recubrimiento se forma uniformemente en todas las superficies, incluidas las geometrías complejas.
- PVD: Utiliza un proceso físico, como pulverización catódica o evaporación, para depositar material directamente sobre el sustrato en una línea de visión. Esto limita la cobertura a las superficies expuestas pero permite un control preciso sobre las propiedades de la película.
-
Temperatura de funcionamiento:
- ECV: Requiere altas temperaturas (800–1000 °C), que pueden afectar las propiedades mecánicas del sustrato y provocar tensiones de tracción o grietas finas en el revestimiento.
- PVD: Funciona a temperaturas más bajas (250–500 °C), lo que lo hace adecuado para materiales sensibles al calor y reduce el riesgo de deformación del sustrato.
-
Espesor y uniformidad del recubrimiento:
- ECV: Produce recubrimientos más gruesos (10–20 μm) con excelente uniformidad, lo que lo hace ideal para aplicaciones que requieren alta resistencia al desgaste y durabilidad.
- PVD: Forma recubrimientos más delgados (3–5 μm) con suavidad y precisión superiores, adecuados para aplicaciones que exigen acabados superficiales finos y cambios dimensionales mínimos.
-
Estrés y adherencia:
- ECV: Las altas temperaturas de procesamiento pueden provocar tensiones de tracción en el revestimiento, lo que puede provocar microfisuras y una reducción de la adherencia en algunos casos.
- PVD: Genera tensión de compresión durante el enfriamiento, mejorando la adhesión y durabilidad del recubrimiento, especialmente en aplicaciones de alta precisión.
-
Compatibilidad de materiales:
- ECV: Se utiliza principalmente para cerámicas y polímeros y ofrece excelente resistencia química y estabilidad térmica.
- PVD: Puede depositar una gama más amplia de materiales, incluidos metales, aleaciones y cerámicas, lo que proporciona una mayor versatilidad para diversas aplicaciones.
-
Aplicaciones:
- ECV: Se utiliza comúnmente en industrias que requieren recubrimientos gruesos y resistentes al desgaste, como herramientas de corte, componentes aeroespaciales y fabricación de semiconductores.
- PVD: Preferido para aplicaciones que necesitan recubrimientos finos, suaves y precisos, como dispositivos médicos, componentes ópticos y acabados decorativos.
-
Costo y tiempo de procesamiento:
- ECV: Generalmente es más caro y requiere más tiempo debido a las altas temperaturas y a los complejos procesos químicos implicados.
- PVD: Ofrece tiempos de procesamiento más rápidos y costos más bajos, lo que lo hace más económico para producción de gran volumen.
En resumen, la elección entre insertos de recubrimiento CVD y PVD depende de los requisitos específicos de la aplicación, incluido el espesor del recubrimiento, la temperatura de funcionamiento, la compatibilidad del material y las propiedades superficiales deseadas. CVD es ideal para recubrimientos gruesos y uniformes en ambientes de alta temperatura, mientras que PVD sobresale en aplicaciones de precisión que requieren superficies lisas y duraderas a temperaturas más bajas.
Tabla resumen:
Aspecto | ECV | PVD |
---|---|---|
Mecanismo de deposición | Reacciones químicas a altas temperaturas (800–1000 °C), multidireccionales | Vaporización física a temperaturas más bajas (250–500 °C), línea de visión |
Espesor del recubrimiento | Más grueso (10–20 μm), uniforme | Más delgado (3–5 μm), ultraduro y liso |
Temperatura de funcionamiento | Alto (800–1000 °C), puede causar tensión de tracción | Bajo (250–500 °C), reduce la deformación del sustrato |
Estrés y adherencia | Esfuerzos de tracción, posibles microfisuras | Tensión de compresión, mayor adherencia. |
Compatibilidad de materiales | Cerámicas, polímeros, alta resistencia química. | Metales, aleaciones, cerámicas, versátiles. |
Aplicaciones | Herramientas de corte, aeroespacial, semiconductores. | Dispositivos médicos, óptica, acabados decorativos. |
Costo y procesamiento | Caro, requiere mucho tiempo | Procesamiento más rápido y rentable |
¿Necesita ayuda para elegir entre CVD y PVD para su aplicación? Póngase en contacto con nuestros expertos hoy ¡Para asesoramiento personalizado!