El objetivo de los procesos de fabricación a base de polvos
Tabla de contenido
- El objetivo de los procesos de fabricación a base de polvos
- El proceso de prensado isostático en frío (CIP)
- El proceso de prensado isostático en caliente (HIP)
- La oportunidad de preprocesamiento de construcciones en un solo paso mediante fabricación aditiva de múltiples materiales
- El uso de la tecnología de deposición selectiva de Kintek en el prensado isostático
- El potencial de un enfoque similar para piezas procesadas mediante HIP
- Conclusión: El puente de la deposición selectiva de polvo entre la nueva fabricación aditiva y la fabricación tradicional
El objetivo de la mayoría de los procesos de fabricación basados en polvo.
El objetivo de la mayoría de los procesos de fabricación a base de polvos , como la pulvimetalurgia (PM), es producir piezas densas con menos del 1% de porosidad sin fundir el material de partida. El polvo suelto utilizado en estos procesos suele tener una densidad de apilamiento baja, con una densidad máxima teórica de sólo el 64 % para partículas perfectamente esféricas apiladas aleatoriamente. Sin embargo, utilizando distribuciones adecuadas del tamaño de las partículas de polvo o polvos deformables, se pueden lograr densidades de empaquetamiento superiores al 90%.
Las limitaciones del prensado uniaxial.
Para obtener resultados satisfactorios en los procesos de fabricación a base de polvo, aplicar presión es fundamental. Comúnmente se usa el prensado uniaxial, donde se aplica presión en una dirección. Sin embargo, este método tiene limitaciones, particularmente para piezas gruesas. Tiende a producir diferencias de densidad a lo largo de la dirección de prensado, lo que puede afectar la calidad de la pieza final.
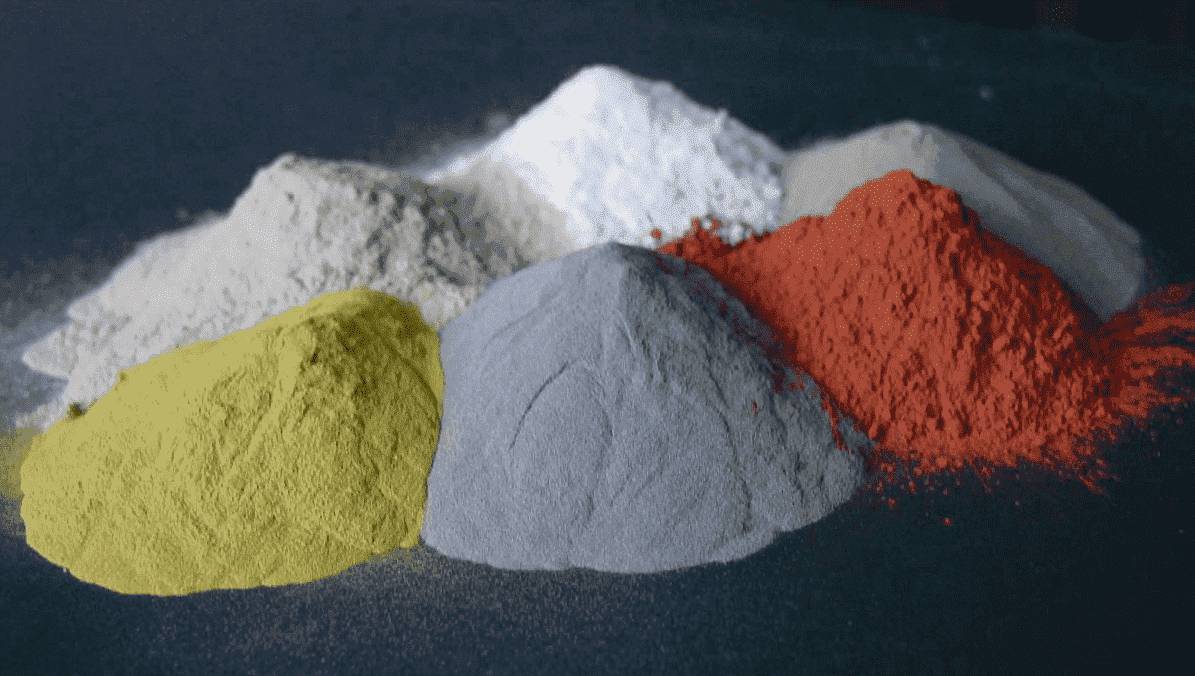
La solución: prensado isostático
Para superar las limitaciones del prensado uniaxial, el prensado isostático se utiliza a menudo para piezas a granel. El prensado isostático es una técnica de procesamiento de polvo que utiliza la presión del fluido para compactar la pieza. Los polvos metálicos se colocan en un recipiente flexible, que sirve como molde para la pieza. La presión del fluido se ejerce sobre toda la superficie exterior del recipiente, lo que hace que presione y forme el polvo con la geometría deseada. A diferencia del prensado uniaxial, el prensado isostático aplica presión desde todas las direcciones, lo que da como resultado una distribución de densidad más uniforme.
Procesos alternativos
Prensado isostático
El prensado isostático es un proceso de fabricación a base de polvo ampliamente utilizado que aplica una presión uniforme para consolidar polvos o reparar defectos en piezas fundidas. Se puede utilizar para una variedad de materiales, incluidos cerámica, metales, compuestos, plásticos y carbono. El proceso consiste en colocar el polvo en un molde flexible, sellarlo y someterlo a presión desde todas las direcciones. El prensado isostático ofrece beneficios únicos para aplicaciones cerámicas y refractarias, ya que permite la formación de formas de productos con tolerancias precisas, lo que reduce la necesidad de un costoso mecanizado.
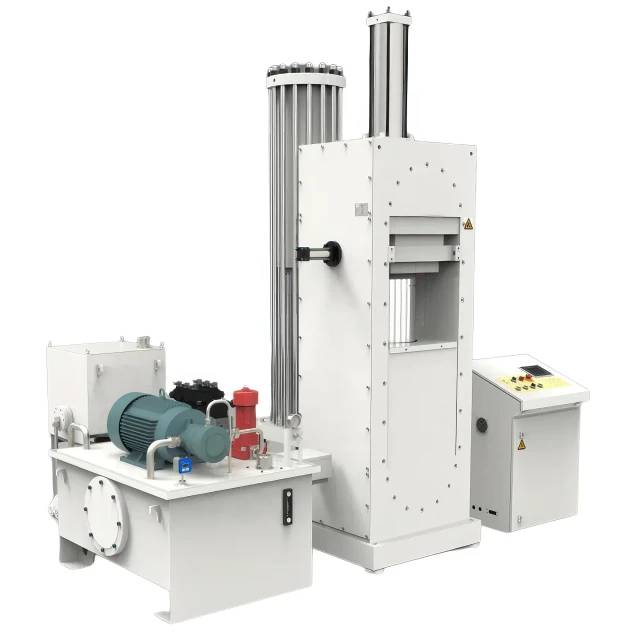
Procesamiento de metales en polvo
El procesamiento de metales en polvo es otra técnica de fabricación a base de polvo que permite la producción de productos con propiedades que pueden superar a los materiales aleados. En este proceso, se mezclan polvos metálicos o cerámicos, junto con un aglutinante, para formar una mezcla que se puede prensar en las formas deseadas. Para piezas más grandes, la mezcla se vierte en moldes. Este proceso se usa comúnmente en la producción de productos como brocas de compuesto de diamante policristalino (PDC) para perforación de pozos profundos, donde la mezcla se presiona y se cuece para producir productos con una forma casi neta.
Avances en pulvimetalurgia
Los procesos a base de polvo, como la compactación de polvo, el prensado isostático en caliente de polvo (P-HIP), el moldeo por inyección de metal (MIM) y la sinterización por plasma por chispa, se utilizan cada vez más para fabricar formas netas (NS) y casi netas. Componentes de forma (NNS) de aleaciones de alto rendimiento. Estos procesos tienen como objetivo fabricar piezas que se ajusten estrechamente a la geometría final requerida, reduciendo costos, plazos de entrega y desperdicio de materiales al minimizar pasos del proceso como el mecanizado y el acabado. Las tecnologías basadas en polvo tienen la capacidad de producir piezas con propiedades de rendimiento que pueden igualar o incluso mejorar las de los procesos de fabricación tradicionales como la fundición. Esto se debe a factores como la microestructura uniforme asociada con los materiales particulados y los avances en la pulvimetalurgia que permiten producir una amplia gama de aleaciones de alto rendimiento en formato de polvo.
En conclusión, el objetivo de los procesos de fabricación basados en polvo es producir piezas densas con altas densidades de empaquetamiento y mínima porosidad. El prensado isostático es una técnica valiosa que se utiliza para superar las limitaciones del prensado uniaxial, proporcionando una distribución de densidad más uniforme en piezas gruesas. Además, procesos alternativos como el procesamiento de metal en polvo y los avances en la pulvimetalurgia han ampliado las capacidades de la fabricación a base de polvo, permitiendo la producción de formas complejas y aleaciones de alto rendimiento.
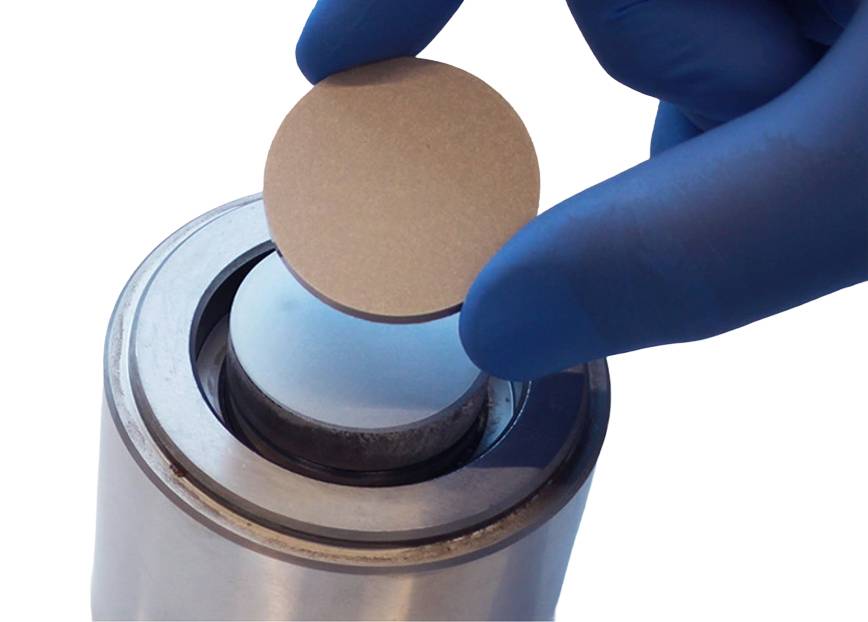
El proceso de prensado isostático en frío (CIP)
El proceso del PIC
El prensado isostático en frío (CIP) es un método de procesamiento de materiales que se utiliza para dar forma y compactar polvos en componentes de diferentes tamaños y formas. Consiste en colocar el polvo o una parte verde de baja densidad en un recipiente flexible sellado y sumergirlo en líquido dentro de un recipiente a presión. Se aplica una presión de varios miles de bares, comprimiendo el compacto verde lo más cerca posible de su densidad máxima de empaquetamiento. Esta mayor densidad inicial acelera la consolidación hasta la densidad final en el ciclo térmico.
El CIP utiliza el principio propuesto por el científico francés Blaise Pascal, que establece que un cambio de presión en un fluido encerrado e incompresible se transmite sin disminución a todas las partes del fluido y a la superficie de su recipiente. Los materiales en polvo se sellan en un molde de formación con baja resistencia a la deformación, como una bolsa de goma, y se aplica presión líquida para comprimir el cuerpo moldeado uniformemente sobre toda su superficie.
El prensado de moldes metálicos es un método de prensado similar al CIP. En este método, los materiales en polvo se introducen en un espacio cerrado por un molde de metal y un punzón inferior. Luego se comprimen reduciendo la distancia entre los punzones superior e inferior.
Los beneficios de una alta densidad inicial para acelerar la consolidación hasta la densidad final en el ciclo térmico
La alta densidad inicial lograda mediante el proceso CIP ofrece varios beneficios en la consolidación de polvos. Estos beneficios incluyen:
Compresión predecible durante el proceso de sinterización posterior: la alta compactación y la densidad uniforme proporcionan una compresión predecible durante el proceso de sinterización, lo que da como resultado una densidad final consistente y confiable.
Capacidad para procesar formas grandes, complicadas y perfectas: CIP permite el procesamiento de formas grandes y complejas con alta precisión. Esto ahorra tiempo y costes durante los procesos de postratamiento.
Generación de piezas con relaciones de aspecto grandes y densidades uniformes: CIP puede producir piezas con relaciones de aspecto superiores a 2:1, manteniendo densidades uniformes en todo el componente.
Resistencia en verde para manipulación y tratamiento durante el proceso: El compacto verde formado mediante CIP tiene suficiente resistencia para someterse a manipulación y tratamiento en proceso, lo que reduce los costos de producción.
En general, el proceso CIP ofrece una conformación y compactación de polvos eficiente y eficaz, lo que da como resultado componentes de alta calidad con las densidades deseadas. Su versatilidad y capacidad para procesar diversos materiales lo convierten en un método valioso en industrias como la fabricación de precisión, la aeroespacial, la defensa y la automoción.
Según un informe de DataIntelo, se prevé que el mercado mundial de equipos de prensado isostático en frío (CIP) crezca a una tasa compuesta anual sustancial durante el período previsto, 2020-2026. La creciente demanda de productos procesados CIP en industrias como la de fabricación de precisión, la aeroespacial, la defensa y la automoción está impulsando este crecimiento.
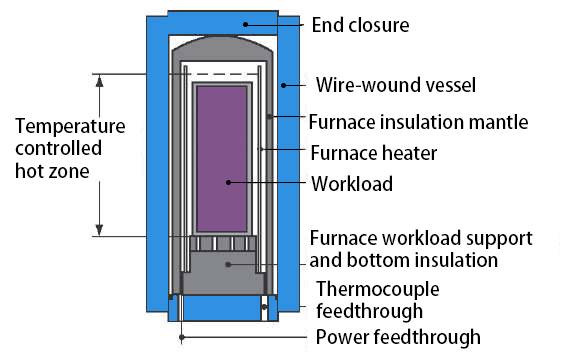
El proceso de prensado isostático en caliente (HIP)
El apalancamiento de la sinterización asistida por presión uniaxial en HIP
También se puede aplicar presión durante el ciclo térmico. En la sinterización uniaxial asistida por presión, normalmente sólo se pueden producir productos en forma de placas. Para piezas más complejas, se utiliza el prensado isostático en caliente (HIP). HIP se lleva a cabo en una atmósfera gaseosa, por lo que el principal requisito es que, para empezar, la superficie exterior de las piezas tratadas sea hermética al gas. Como tal, este proceso se puede utilizar para producir componentes sellando al vacío el polvo de la pieza en una carcasa de acero dulce. La aplicación uniforme de presión garantiza que se conserve la forma a medida que la pieza y la carcasa se contraen. Los polvos procesados mediante una estrategia HIP normalmente no son compatibles con los procesos de fusión, ya sea que requieren temperaturas excesivas o producen microestructuras desfavorables. No obstante, el esfuerzo adicional que se hace para procesar estos materiales indica su uso en aplicaciones exigentes donde incluso un nivel bajo de porosidad no es aceptable.
Los requisitos y resultados del proceso HIP.
El prensado isostático en caliente (HIP) es la aplicación simultánea de alta temperatura y presión a metales y otros materiales durante un período de tiempo específico para mejorar sus propiedades mecánicas. En la unidad HIP, un horno de alta temperatura está encerrado en un recipiente a presión. La temperatura, la presión y el tiempo del proceso se controlan con precisión para lograr las propiedades óptimas del material. Las piezas se calientan en un gas inerte, generalmente argón, que aplica una presión "isostática" uniformemente en todas las direcciones. Esto hace que el material se vuelva "plástico", permitiendo que los huecos colapsen bajo la presión diferencial. Las superficies de los huecos se unen por difusión para eliminar eficazmente los defectos, logrando una densidad cercana a la teórica y al mismo tiempo mejorando las propiedades mecánicas de las piezas, como las piezas de fundición a la cera perdida.
La incompatibilidad de los polvos procesados mediante una estrategia HIP con los procesos de fusión.
El prensado isostático en caliente (HIP) es un proceso de tratamiento de materiales que implica el uso de calor y presión para mejorar las propiedades físicas de un material. Normalmente se realiza sobre metales y cerámicas. Cuando cualquiera de estos tipos de materiales se expone al calor y la presión, sus propiedades físicas cambian. HIP es un proceso eficaz para eliminar defectos en piezas fabricadas aditivamente a base de polvo, generando material 100% denso con propiedades de fatiga y ductilidad mejoradas.
Sectores HIP se ha destacado desde que alcanzó una escala comparable a la de las piezas fundidas y forjadas y ha sido reconocido como un competidor económico de la forja y la fundición en aplicaciones con mayores costos de materia prima. Actualmente existen tres sectores principales HIP: petróleo y gas, generación de energía y aeroespacial. La producción de un componente PM HIP es más sencilla y más corta que los procesos metalúrgicos convencionales habituales. El costo de HIP en relación con los costos de energía y materiales ha disminuido en un 65% en las últimas dos décadas.
Introducción El prensado isostático en caliente (HIP) es un proceso para densificar polvos o piezas fundidas y sinterizadas en un horno a alta presión (100-200 MPa) y a temperaturas de 900 a 1250 °C, por ejemplo, para aceros y superaleaciones. La presión del gas actúa uniformemente en todas las direcciones para proporcionar propiedades isotrópicas y una densificación del 100%. Proporciona muchos beneficios y se ha convertido en una alternativa viable y de alto rendimiento a los procesos convencionales como la forja, la fundición y el mecanizado en muchas aplicaciones.
Sinterización/metalurgia de polvos: tecnología de prensado isostático en caliente (HIP)
El prensado isostático en caliente ha pasado del laboratorio de investigación a la producción regular a gran escala en el transcurso de los últimos 50 años. El futuro de esta tecnología parece brillante a medida que se acelera la demanda de propiedades mejoradas de los materiales, el uso de materiales en polvo y el deseo de producir piezas con forma neta o casi neta.
Fuente de temperatura del horno calentada por resistencia dentro del recipiente.
El proceso HIP, originalmente conocido como unión por presión de gas, se desarrolló en el laboratorio del Battelle Memorial Institute en Columbus, Ohio, en 1955. La aplicación original fue el revestimiento por enlace de difusión de circonio a aleaciones de circonio-uranio para elementos combustibles nucleares. Casi al mismo tiempo, ASEA-Suecia utilizaba la aplicación de presión isostática para compactar los primeros diamantes sintéticos. El prensado isostático en caliente (HIP) es un proceso de fabricación que se utiliza para reducir la porosidad de los metales y aumentar la densidad de muchos materiales cerámicos. Esto mejora las propiedades mecánicas y la trabajabilidad del material.
¿Qué es el prensado isostático en caliente (HIP)?
El prensado isostático en caliente (HIP), o 'Hipp'ing', es la aplicación simultánea de calor y alta presión a los materiales. Este proceso es ideal para mejorar las características de su producto fabricado aditivo eliminando la porosidad hasta en un 100%.
Hoy en día, este proceso ya se utiliza en la mejora de productos fabricados aditivos. Según Hipp'ing, el resultado es la eliminación de los huecos internos (es decir, la porosidad) y una microestructura mejorada, lo que lleva a propiedades mecánicas enormemente mejoradas. HIP se puede aplicar a una amplia gama de aleaciones, incluidos titanio, aceros, aluminio, cobre y magnesio.
La oportunidad de preprocesamiento de construcciones en un solo paso mediante fabricación aditiva de múltiples materiales
Los beneficios potenciales de la fabricación aditiva de múltiples materiales en procesos CIP y HIP
La fabricación aditiva de múltiples materiales ofrece una variedad de beneficios potenciales tanto en los procesos de consolidación por prensado isostático (CIP) como en los de prensado isostático en caliente (HIP). Mediante el uso de deposición selectiva de polvo, este enfoque puede cerrar la brecha entre la nueva tecnología de fabricación aditiva y los métodos de fabricación tradicionales para componentes de alta gama. Al consolidar piezas utilizando tecnología establecida, puede ayudar a aliviar las preocupaciones sobre la calidad y confiabilidad de los artículos producidos por AM.
Una de las ventajas clave de la fabricación aditiva multimaterial es la reducción de los costes de fabricación. Con una mayor complejidad de las piezas, menos pasos de procesamiento y menos tiempo, los fabricantes pueden lograr ahorros de costos. Esto resulta especialmente beneficioso para la producción de series pequeñas o prototipos, donde la eficiencia y la rentabilidad son cruciales.
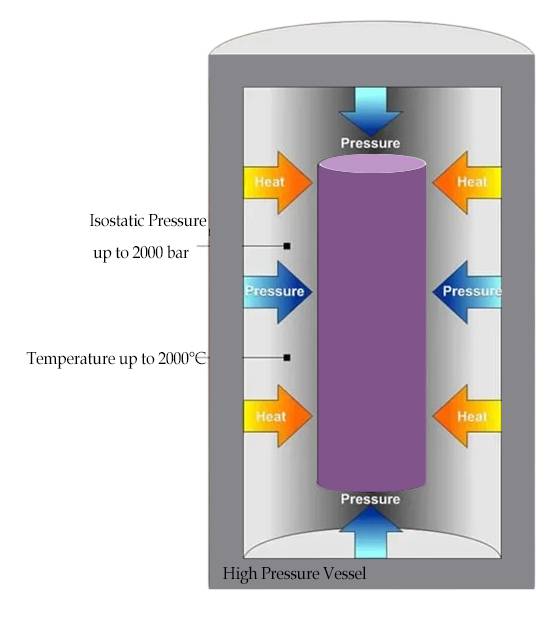
La posible disminución de los costos de fabricación con una mayor complejidad de las piezas, menos pasos de procesamiento y tiempo.
El uso de fabricación aditiva multimaterial puede conducir a una disminución de los costes de fabricación. Los métodos tradicionales de fabricación sustractiva tienen límites geométricos que ya no se aplican a la fabricación aditiva. Esto significa que se pueden crear formas y diseños complejos sin aumentar significativamente los costes de producción. Además, la capacidad de crear múltiples versiones del mismo producto sin variar el costo de producción puede reducir aún más los costos.
Otra ventaja importante de la fabricación de aditivos multimaterial
turar es la reducción drástica de los residuos de procesamiento. Al ir añadiendo material paso a paso hasta obtener el objeto deseado, se produce un desperdicio mínimo en comparación con los métodos tradicionales de fabricación sustractiva. Esto no sólo reduce los costes sino que también contribuye a un proceso de fabricación más sostenible.
El mundo de la fabricación aditiva de metales está experimentando un aumento notable en el uso de métodos como el moldeo por inyección de metales (MIM), el Binder Jetting (BJ) y el modelado por deposición fundida (FDM). Estos métodos ofrecen ventajas únicas en términos de costo, flexibilidad de diseño y propiedades del material.

En la fabricación aditiva de metales, la desaglomeración térmica es un proceso crucial después de la impresión. Implica eliminar aglutinantes y otros aditivos para obtener una pieza metálica totalmente densa. Desligar adecuadamente las piezas producidas mediante la fabricación aditiva de metales es esencial para lograr las propiedades mecánicas y la precisión dimensional deseadas.
Tanto el proceso CIP como el HIP utilizan construcciones de múltiples materiales. CIP implica el uso de carcasas de polímero con polvos cerámicos, mientras que HIP utiliza una carcasa de material de lámina de acero dulce soldada con aleaciones de pulvimetalurgia de alta gama. Estos métodos presentan una oportunidad para el preprocesamiento de construcciones en un solo paso mediante la fabricación aditiva de múltiples materiales.
Este enfoque es particularmente beneficioso para producir series pequeñas o prototipos, ya que permite una mayor complejidad de las piezas con menos pasos de procesamiento y menos tiempo. Al aprovechar las ventajas de la fabricación aditiva de múltiples materiales, los fabricantes pueden lograr una mayor eficiencia y rentabilidad en sus procesos de producción.
La base industrial para el proceso HIP se está expandiendo rápidamente debido a la creciente demanda de propiedades mejoradas de los materiales y el uso de materiales en polvo. Además, los avances en los equipos HIP, los tiempos de procesamiento más cortos y la mejora de la economía hacen que el proceso HIP sea una opción viable para una amplia gama de materiales. Esto refuerza aún más el potencial para el preprocesamiento de construcciones en un solo paso mediante la fabricación aditiva de múltiples materiales.
En conclusión, la fabricación aditiva de múltiples materiales ofrece importantes oportunidades para mejorar la eficiencia, reducir costos y lograr diseños complejos tanto en los procesos CIP como HIP. Al aprovechar las ventajas de esta tecnología, los fabricantes pueden mantenerse a la vanguardia de la innovación y satisfacer las demandas del competitivo mercado actual.
El uso de la tecnología de deposición selectiva de Kintek en el prensado isostático
La deposición simultánea de diferentes materiales.
El prensado isostático es un método de compactación de polvo en un recipiente elastomérico sumergido en un fluido a alta presión. Tradicionalmente, este proceso se ha utilizado principalmente para cerámica y metales. Sin embargo, los avances recientes en la tecnología de deposición selectiva, como el enfoque innovador de Kintek, han abierto nuevas posibilidades para el prensado isostático.
La tecnología de deposición selectiva de KinTek permite la deposición simultánea de diferentes materiales. Esto significa que en lugar de utilizar un único material en polvo, se pueden depositar múltiples materiales capa por capa. Esto abre una gama de posibilidades para crear piezas complejas de múltiples materiales con propiedades únicas.
Creación de una cubierta de polímero moldeada y hermética que rodea el polvo cerámico sin compactar
Una de las ventajas clave de la tecnología de deposición selectiva de KinTek en el prensado isostático es la capacidad de crear una cubierta de polímero hermética y con forma que rodea el polvo cerámico sin compactar. Esta cáscara actúa como una barrera, evitando que el polvo cerámico se disperse durante el proceso de prensado isostático.
Al utilizar la deposición selectiva para crear esta capa, es posible lograr una densidad verde uniforme incluso para piezas con una relación altura/diámetro grande. Esto es particularmente importante para aplicaciones donde el control dimensional es crucial, como en las industrias aeroespacial o automotriz.
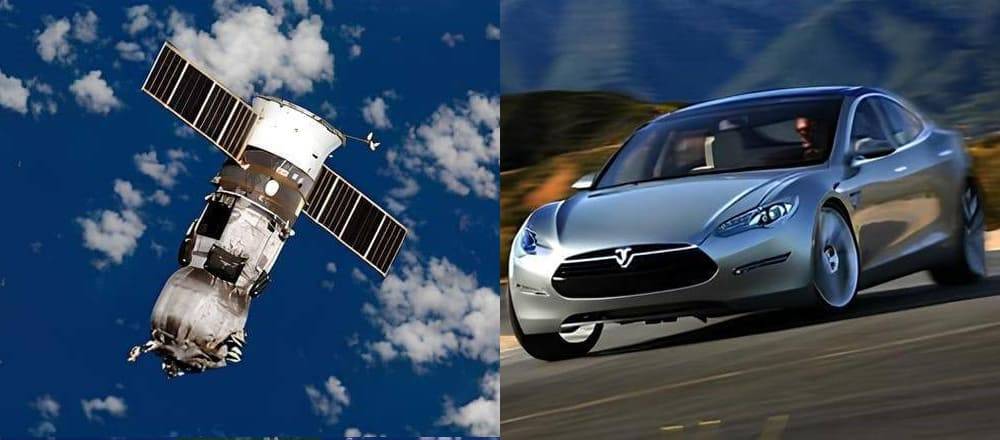
El fácil transporte y colocación de la construcción dentro de una máquina CIP
Otro beneficio de la tecnología de deposición selectiva de es la facilidad de transporte y colocación de la construcción dentro de una máquina de prensado isostático en frío (CIP). La construcción, que consiste en una carcasa de polímero moldeada rellena con polvo cerámico sin compactar, se puede manipular y colocar fácilmente dentro de la máquina CIP.
Esta facilidad de transporte y colocación no sólo aumenta la eficiencia sino que también reduce el riesgo de daños a la construcción durante el proceso de carga. Permite un proceso de prensado isostático más ágil y confiable, lo que garantiza resultados consistentes y piezas de alta calidad.
En conclusión, la tecnología de deposición selectiva de ofrece interesantes posibilidades para el prensado isostático. La deposición simultánea de diferentes materiales, la creación de una carcasa de polímero con forma y hermética a los líquidos y el fácil transporte y colocación de la construcción dentro de una máquina CIP contribuyen al avance de este proceso de fabricación. Con un mayor desarrollo y refinamiento, la tecnología de tiene el potencial de revolucionar la forma en que producimos piezas complejas de múltiples materiales con un mejor control dimensional y rendimiento.
El potencial de un enfoque similar para piezas procesadas mediante HIP
Co-deposición de un acero suave para herramientas y una aleación específica de PM utilizando un sistema de deposición selectiva de polvo
Para las piezas que deben procesarse utilizando HIP, se podría utilizar un enfoque similar. Se podría depositar conjuntamente un acero suave para herramientas y una aleación específica de PM utilizando un sistema de deposición selectiva de polvo, y solo sería necesario consolidar el exterior del acero para herramientas. Como no es necesario fundir la aleación de PM, es fácil imaginar la producción de una carcasa precargada con tuberías que permitirían sellar esta carcasa mediante soldadura al vacío, al igual que en las piezas producidas por HIP a partir de chapa soldada. El resto del procesamiento HIP puede seguir la ruta tradicional.
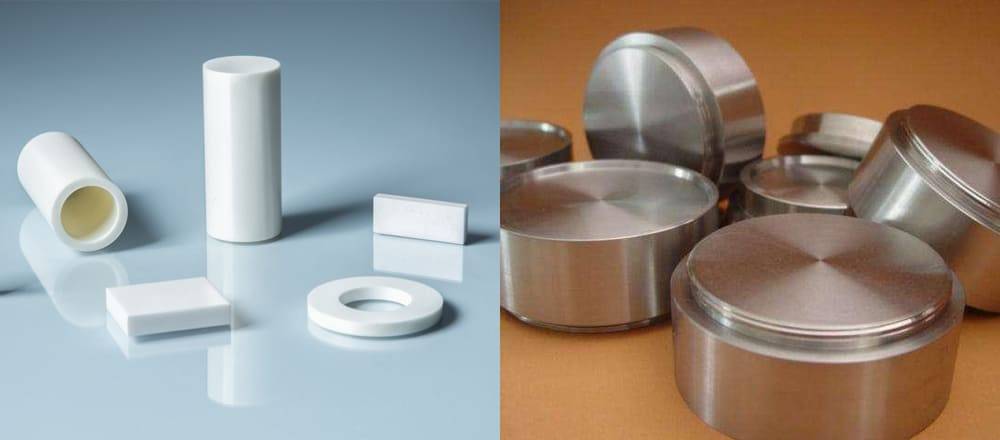
Producción de una carcasa precargada con tuberías para sellado de soldadura al vacío
Se puede utilizar un enfoque similar al procesamiento HIP para piezas que requieren tratamiento HIP. Al depositar conjuntamente un acero suave para herramientas y una aleación específica de PM utilizando un sistema de deposición selectiva de polvo, es posible producir una carcasa precargada con tuberías para sellar soldadura al vacío. Esto permite la consolidación del exterior del acero para herramientas preservando al mismo tiempo la integridad de la aleación de PM. El resto del procesamiento HIP puede continuar como de costumbre.
La ruta tradicional del resto del procesamiento HIP
Después de la codeposición de un acero suave para herramientas y una aleación específica de PM utilizando un sistema de deposición selectiva de polvo y la consolidación del exterior del acero para herramientas, el resto del procesamiento HIP puede seguir la ruta tradicional. Esto incluye el uso de tecnología de enfriamiento avanzada para mejorar la economía del procesamiento y mejorar las propiedades finales del material. Con la capacidad de enfriar más rápido utilizando gas argón y sistemas de enfriamiento internos, los ciclos HIP se pueden reducir significativamente, lo que genera ahorros de costos y una mejor calidad de las piezas.
El uso de HIP en diversas industrias ha demostrado ser muy beneficioso. HIP se puede utilizar para fabricar una amplia gama de componentes, incluidos componentes metálicos grandes y masivos con forma casi neta, como piezas de petróleo y gas e impulsores de forma neta. También es adecuado para producir pequeñas herramientas de corte PM HSS y piezas pequeñas como brackets dentales. El proceso ha evolucionado a lo largo de los años hasta convertirse en un método rentable, de alto rendimiento y de alta calidad para producir componentes metálicos y cerámicos.
HIPing ofrece numerosos beneficios, que incluyen propiedades mecánicas mejoradas, reducción de desechos, mecanizado minimizado y la capacidad de rejuvenecer piezas viejas. Se puede aplicar a una variedad de materiales, incluidos aluminio, acero, acero inoxidable, superaleaciones, titanio y cerámica. Con los avances en los equipos HIP y los tiempos de procesamiento, el proceso HIP se está volviendo cada vez más popular para una amplia gama de materiales y aplicaciones.
En conclusión, se puede aplicar un enfoque similar al procesamiento HIP a piezas que requieren tratamiento HIP. Al depositar conjuntamente un acero suave para herramientas y una aleación específica de PM utilizando un sistema de deposición selectiva de polvo, es posible producir carcasas precargadas con tuberías para sellado de soldadura al vacío. Este enfoque ofrece numerosos beneficios, incluida una mejor calidad de las piezas, un menor tiempo de procesamiento y ahorro de costos. Con los continuos avances en la tecnología HIP, el potencial para utilizar este enfoque en diversas industrias continúa expandiéndose.
Conclusión: El puente de la deposición selectiva de polvo entre la nueva fabricación aditiva y la fabricación tradicional
El potencial de la deposición selectiva de polvo para crear un puente entre la nueva tecnología de fabricación aditiva y la fabricación tradicional de componentes de alta gama.
La deposición selectiva de polvo tiene el potencial de cerrar la brecha entre la nueva tecnología de fabricación aditiva (AM) y la fabricación tradicional de componentes de alta gama. Este enfoque aprovecha los bien conocidos procesos de tratamiento a presión y ciclos térmicos que ya están disponibles en la industria. El uso de estos métodos establecidos para consolidar piezas creadas mediante FA puede ayudar a aliviar la ansiedad de la industria sobre los artículos producidos mediante esta nueva tecnología.
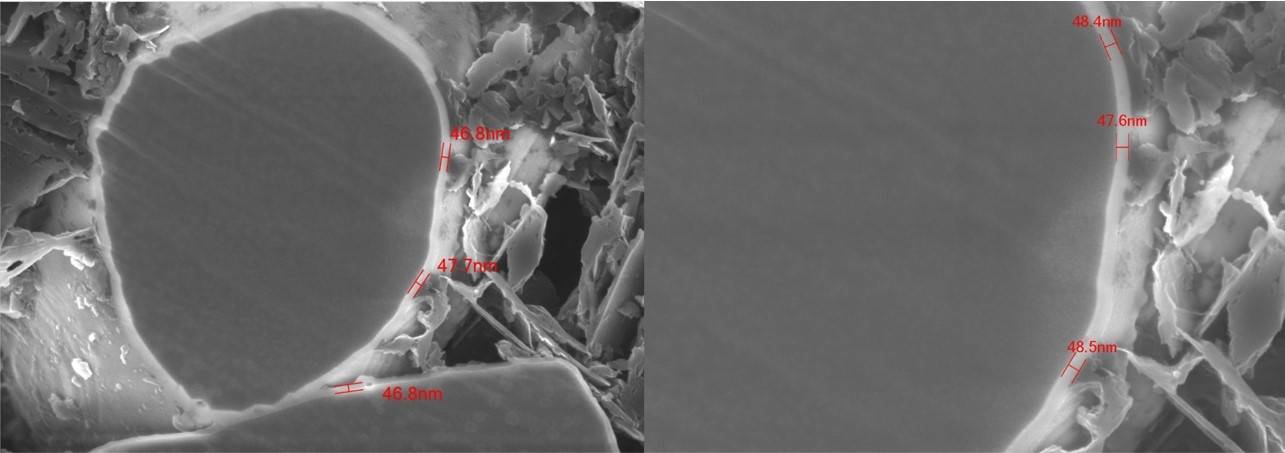
La posibilidad de aliviar la ansiedad de la industria sobre los artículos producidos mediante FA a través de este enfoque.
Una de las principales preocupaciones de la industria cuando se trata de fabricación aditiva es la calidad y fiabilidad de los productos finales. Los métodos de fabricación tradicionales se han perfeccionado durante décadas y existe un nivel de confianza en los componentes producidos a través de estos procesos.
Mediante el uso de la deposición selectiva de polvo, las piezas creadas mediante AM pueden moldearse utilizando la nueva tecnología pero consolidarse utilizando los métodos establecidos desde hace mucho tiempo. Esto puede ayudar a aliviar parte de la ansiedad que rodea al uso de AM para componentes de alta gama.
En conclusión, la deposición selectiva de polvo ofrece una solución prometedora para cerrar la brecha entre la nueva tecnología de fabricación aditiva y la fabricación tradicional. Aprovechar los procesos y técnicas establecidos en la fabricación tradicional puede ayudar a generar confianza en los componentes producidos mediante FA.
CONTÁCTANOS PARA UNA CONSULTA GRATUITA
Los productos y servicios de KINTEK LAB SOLUTION han sido reconocidos por clientes de todo el mundo. Nuestro personal estará encantado de ayudarle con cualquier consulta que pueda tener. ¡Contáctenos para una consulta gratuita y hable con un especialista del producto para encontrar la solución más adecuada para sus necesidades de aplicación!