Los revestimientos PVD (deposición física de vapor) son muy eficaces para evitar la oxidación gracias a sus excelentes propiedades de resistencia a la corrosión.Estos revestimientos se utilizan ampliamente en industrias como la aeroespacial, la de automoción y la de dispositivos médicos, ya que proporcionan una capa fina y duradera que protege el material subyacente de factores ambientales como la humedad y la oxidación.Los revestimientos PVD, como el nitruro de circonio (ZrN), han demostrado una resistencia excepcional a la corrosión, superando las 1.200 horas en pruebas de niebla salina neutra (ASTM B117) y más de 150 horas en pruebas CASS.La delgadez de los revestimientos PVD, que oscila entre 0,5 y 5 micras, no compromete su eficacia, ya que son muy adherentes y difíciles de eliminar.Además, los revestimientos de PVD pueden reproducir el acabado original de los materiales, lo que los hace funcionales y estéticamente agradables.En general, los revestimientos de PVD son una solución fiable para prevenir la oxidación y prolongar considerablemente la vida útil de los productos.
Explicación de los puntos clave:
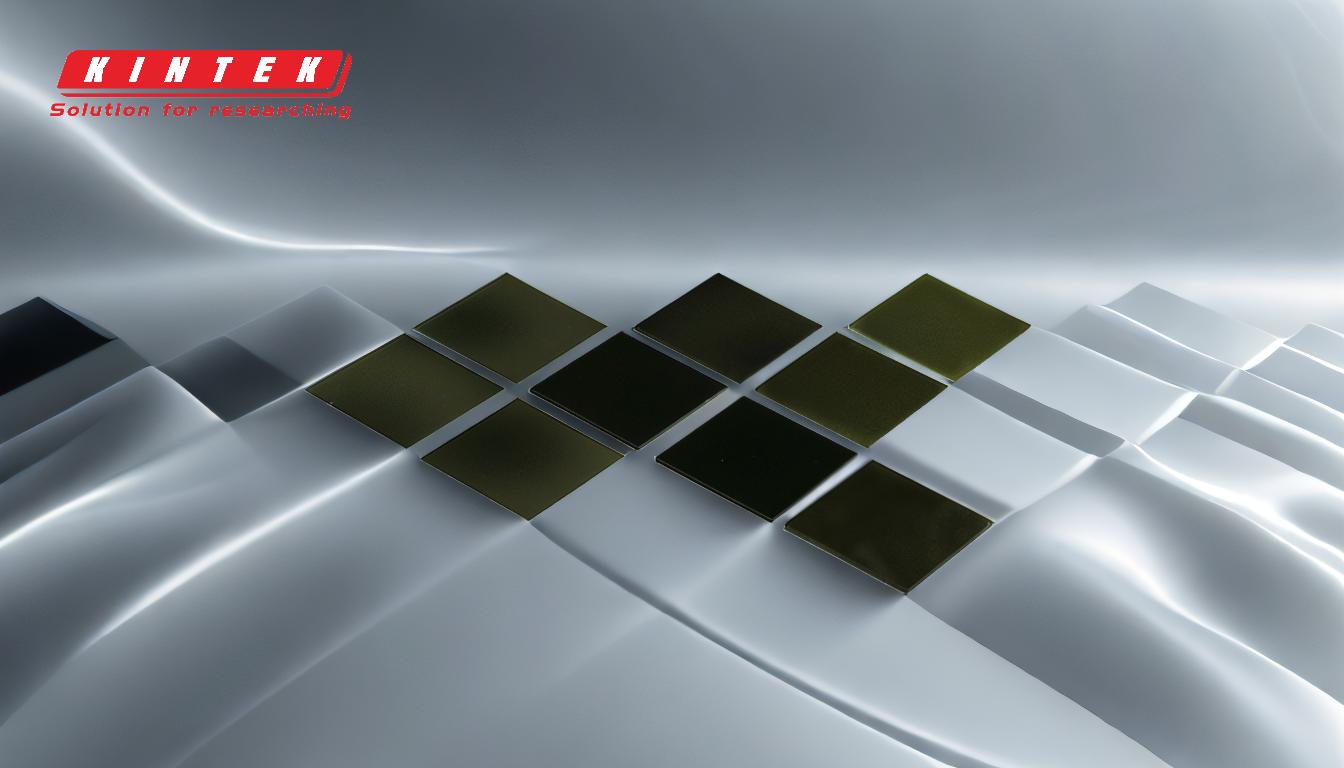
-
Resistencia a la corrosión de los revestimientos PVD
- Los revestimientos de PVD están diseñados específicamente para resistir la corrosión y la oxidación, por lo que son muy eficaces para evitar la oxidación.
- Forman una barrera protectora que protege el material subyacente de factores ambientales como la humedad, la sal y los productos químicos.
- Por ejemplo, se ha comprobado que los revestimientos de nitruro de circonio (ZrN) resisten más de 1.200 horas en pruebas de niebla salina neutra (ASTM B117), que es una medida estándar de resistencia a la corrosión.
-
Capa fina pero duradera
- Los revestimientos PVD son extremadamente finos, de 0,5 a 5 micras, pero su delgadez no compromete su capacidad protectora.
- Los revestimientos son muy adherentes, lo que significa que se adhieren fuertemente al sustrato, lo que dificulta su eliminación y garantiza una protección duradera.
- A pesar de su delgadez, los revestimientos PVD pueden reproducir el acabado original de los materiales, manteniendo tanto la funcionalidad como la estética.
-
Aplicaciones en entornos propensos a la oxidación
- Los revestimientos de PVD se utilizan en sectores en los que la prevención de la oxidación es fundamental, como la automoción (p. ej., ruedas, pistones), la industria aeroespacial y los dispositivos médicos.
- También se aplican a herramientas y equipos expuestos a condiciones duras, como herramientas de corte, matrices y moldes, donde la resistencia a la corrosión es esencial para la longevidad.
- La capacidad de los revestimientos PVD para soportar condiciones extremas, como la niebla salina y los ambientes ácidos, los hace ideales para su uso en aplicaciones marinas, industriales y al aire libre.
-
Rendimiento superior en comparación con los métodos tradicionales
- Los revestimientos PVD son una alternativa más ecológica a los métodos tradicionales como el cromado, ya que no producen sustancias tóxicas durante su aplicación.
- Ofrecen una mayor resistencia a la corrosión y durabilidad en comparación con la galvanoplastia, como demuestra su rendimiento en pruebas normalizadas como CASS (pulverización de sal y ácido acético acelerada con cobre).
- La mayor vida útil de los productos revestidos con PVD (hasta 25 años en algunos casos) pone de manifiesto su eficacia para evitar la oxidación y otras formas de degradación.
-
Versatilidad en la compatibilidad de materiales
- Los revestimientos PVD pueden aplicarse a una amplia gama de sustratos, incluidos metales, polímeros y cerámicas, lo que los hace versátiles para diversas aplicaciones.
- Las propiedades del revestimiento pueden adaptarse a las necesidades específicas del sustrato, garantizando una protección óptima contra el óxido y otras formas de corrosión.
- Por ejemplo, revestimientos como el nitruro de titanio (TiN) no sólo proporcionan resistencia a la corrosión, sino que también mejoran la dureza y la resistencia al desgaste del material.
-
Rentabilidad a largo plazo
- Al evitar la oxidación y prolongar la vida útil de los productos, los revestimientos PVD reducen la necesidad de sustituciones y mantenimiento frecuentes, lo que supone un ahorro de costes a largo plazo.
- Su durabilidad y resistencia al desgaste los convierten en una solución rentable para las industrias que requieren materiales de alto rendimiento.
- La capacidad de reproducir el acabado original de los materiales también reduce la necesidad de procesos de acabado adicionales, lo que disminuye aún más los costes.
En conclusión, los revestimientos PVD son una excelente opción para prevenir la oxidación debido a su superior resistencia a la corrosión, durabilidad y versatilidad.Su naturaleza delgada pero altamente adherente garantiza una protección duradera, mientras que su compatibilidad con diversos sustratos y aplicaciones los convierte en una solución práctica para las industrias que requieren la prevención de la oxidación.
Tabla resumen:
Característica | Detalles |
---|---|
Resistencia a la corrosión | Soporta más de 1200 horas en pruebas de niebla salina neutra (ASTM B117). |
Espesor | De 0,5 a 5 micras, muy adherente y duradero. |
Aplicaciones | Automoción, aeroespacial, dispositivos médicos, equipos marinos e industriales. |
Compatibilidad de materiales | Metales, polímeros, cerámicas: adaptados para una protección óptima. |
Rentabilidad | Reduce los costes de mantenimiento y sustitución, prolonga la vida útil del producto. |
Proteja sus productos de la oxidación con revestimientos PVD-. contacte con nosotros para obtener más información.