Los trenes de laminación son equipos esenciales en la metalurgia, diseñados para moldear y procesar metales en diversas formas, como barras, varillas, chapas y más. Se clasifican en función de su diseño, funcionalidad y aplicación. Los principales tipos de laminadores son los de dos alturas, tres alturas, cuatro alturas, en racimo, continuos y planetarios. Cada tipo sirve para fines específicos, que van desde el trabajo de laboratorio a pequeña escala hasta la producción industrial a gran escala. Además, los laminadores pueden clasificarse en calientes o fríos, según la temperatura a la que se procese el metal. Comprender estas variaciones ayuda a seleccionar el laminador adecuado para las necesidades específicas del trabajo del metal.
Explicación de los puntos clave:
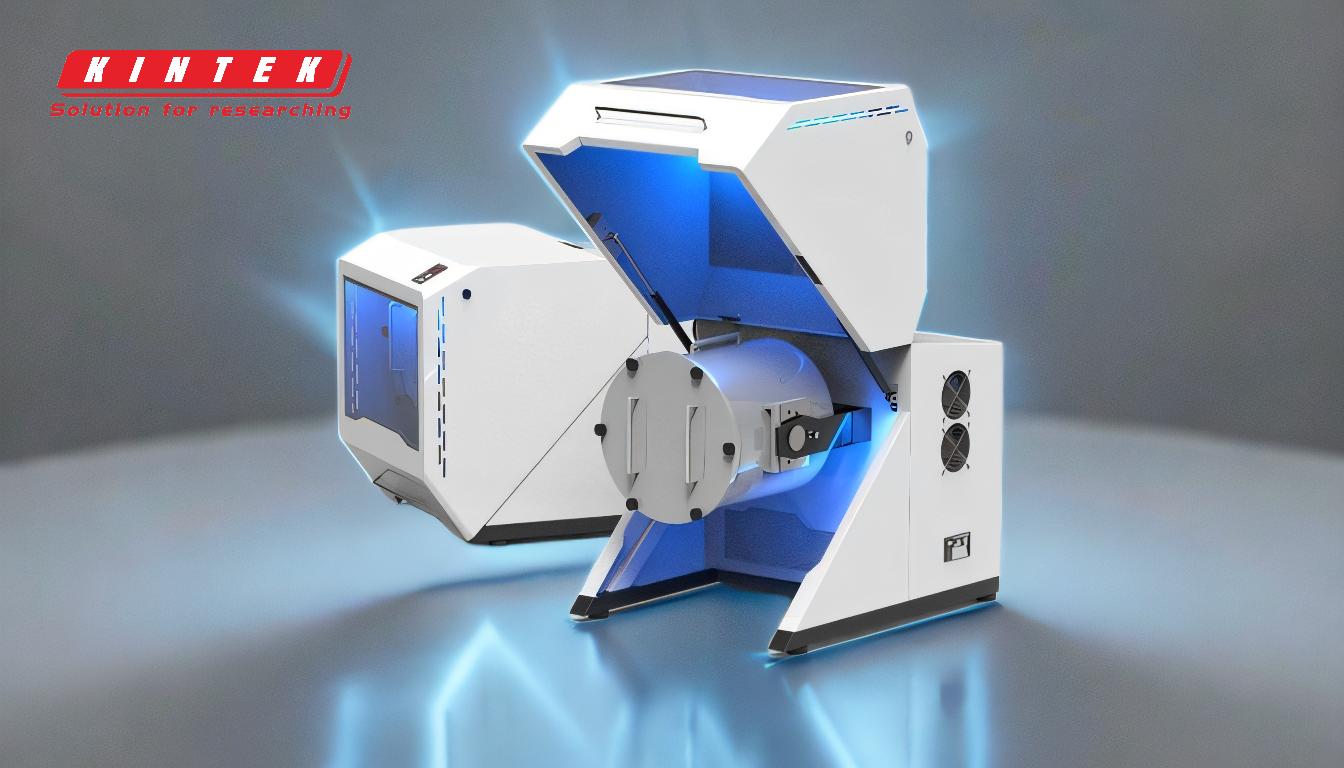
-
Trenes de laminación de dos alturas:
- Descripción: Se trata del tipo de laminador más sencillo y común, formado por dos rodillos que giran en sentidos opuestos.
- Aplicaciones: Se utilizan tanto para laminar en caliente como en frío, y son adecuados para producir barras, alambrones y chapas.
- Variantes: Pueden ser reversibles (los rodillos pueden cambiar de dirección) o no reversibles (los rodillos se mueven en una sola dirección).
-
Laminadores de tres alturas:
- Descripción: Equipados con tres rodillos, en los que el metal pasa por los rodillos superior e intermedio en una dirección y, a continuación, por los rodillos intermedio e inferior en la dirección opuesta.
- Aplicaciones: Ideal para procesos de laminación en continuo, a menudo utilizada en producciones de gran volumen.
- Variantes: Incluye calentamiento eléctrico, calentamiento por vapor, rodillos de granito, rodillos cerámicos y rodillos inoxidables.
-
Laminadores de cuatro alturas:
- Descripción: Dispone de cuatro rodillos, con dos rodillos de trabajo más pequeños soportados por dos rodillos de apoyo más grandes. Este diseño reduce la desviación de los rodillos y permite una mayor precisión.
- Aplicaciones: Comúnmente utilizado para laminar chapas finas y tiras, especialmente en procesos de laminación en frío.
- Ventajas: Proporciona un mejor control del espesor y del acabado superficial.
-
Laminadores en racimo:
- Descripción: Consiste en múltiples rodillos dispuestos en un grupo, normalmente con uno o dos rodillos de trabajo soportados por varios rodillos de apoyo.
- Aplicaciones: Se utiliza para laminar materiales muy finos, como láminas, donde se requiere una alta precisión y una desviación mínima.
- Ventajas: Ofrece un soporte de rodillo superior, lo que permite la producción de materiales ultrafinos.
-
Laminadores continuos:
- Descripción: Consta de varios soportes de rodillos dispuestos en secuencia, lo que permite que el metal pase por varias etapas de laminación en un proceso continuo.
- Aplicaciones: Adecuado para la producción de grandes volúmenes de productos largos como barras, varillas y alambrón.
- Ventajas: Aumenta la eficacia y la uniformidad de la producción al reducir la necesidad de intervención manual.
-
Laminadores planetarios:
- Descripción: Se caracteriza por un rodillo central rodeado de múltiples rodillos más pequeños, que giran alrededor del rodillo central. Este diseño permite obtener altos ratios de reducción en una sola pasada.
- Aplicaciones: Se utiliza para laminar desbastes gruesos y convertirlos en chapas o placas más finas.
- Ventajas: Capaz de lograr una reducción significativa del espesor en una sola pasada, lo que lo hace eficiente para la producción a gran escala.
-
Laminado en caliente frente a laminado en frío:
- Laminadores en caliente: Funcionan a altas temperaturas, normalmente por encima de la temperatura de recristalización del metal. Este proceso se utiliza para dar forma a grandes piezas de metal y mejorar las propiedades del material.
- Laminadores en frío: Funcionan a temperatura ambiente o próxima a ella y se utilizan en procesos de acabado para conseguir dimensiones precisas, superficies lisas y mejores propiedades mecánicas.
-
Laminadores especializados:
- Modelos pequeños de banco: Diseñados para producción de bajo volumen, trabajo de laboratorio y desarrollo en banco. Se accionan manualmente y son ideales para aplicaciones a pequeña escala.
- Modelos industriales grandes: Máquinas motorizadas diseñadas para la fabricación de grandes volúmenes, capaces de satisfacer necesidades de producción a gran escala.
Al conocer estos tipos de laminadores, los compradores pueden tomar decisiones informadas basadas en los requisitos específicos de sus procesos metalúrgicos, ya necesiten precisión, producción de gran volumen o aplicaciones especializadas.
Tabla resumen:
Tipo de laminador | Descripción | Aplicaciones | Ventajas |
---|---|---|---|
Dos altos | Dos rodillos que giran en sentidos opuestos | Barras, varillas, placas | Sencillo, versátil |
Tres-altas | Tres rodillos para laminado continuo | Producción de gran volumen | Eficaz, reversible |
Cuatro-altas | Cuatro rodillos con soporte de apoyo | Chapas finas, tiras | Preciso, mejor acabado superficial |
Agrupación | Varios rodillos en un grupo | Materiales ultrafinos (por ejemplo, láminas) | Alta precisión, desviación mínima |
Continuo | Múltiples soportes en secuencia | Barras, varillas, alambrón | Alta eficiencia, producción constante |
Planetario | Rodillo central con rodillos circundantes | De desbastes gruesos a chapas finas | Alta reducción en una sola pasada |
Laminación en caliente | Procesado a alta temperatura | Conformación de grandes piezas metálicas | Mejora de las propiedades del material |
Laminación en frío | Procesado a temperatura ambiente | Dimensiones precisas, superficies lisas | Propiedades mecánicas mejoradas |
¿Necesita ayuda para elegir el laminador adecuado para sus necesidades metalúrgicas? Póngase en contacto hoy mismo con nuestros expertos para un asesoramiento personalizado.