Los revestimientos PVD (deposición física de vapor) son realmente resistentes al calor, lo que los hace adecuados para aplicaciones en las que las altas temperaturas son un problema.Estos revestimientos son conocidos por su gran dureza, resistencia al desgaste y resistencia a la corrosión, que contribuyen a su capacidad para soportar temperaturas elevadas.Los revestimientos PVD se aplican en un entorno de vacío, lo que da como resultado una capa fina y duradera que se adhiere bien al sustrato.Su estabilidad térmica, combinada con propiedades como la baja fricción y la estabilidad química, los hace ideales para industrias como la automovilística, la aeroespacial y la médica, donde la resistencia al calor es crítica.Aunque los revestimientos PVD no son inmunes a todas las condiciones de altas temperaturas, su rendimiento es generalmente superior al de muchos otros métodos de revestimiento.
Explicación de los puntos clave:
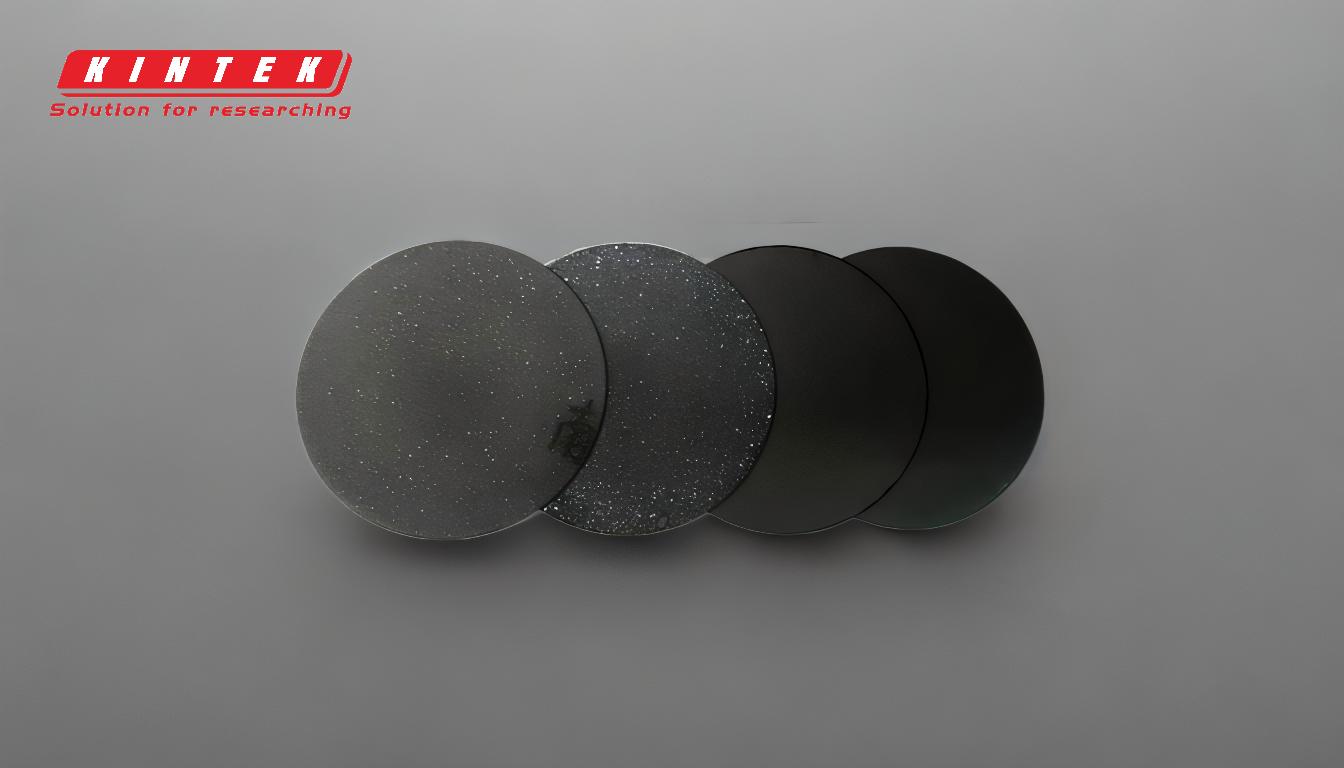
-
Resistencia al calor de los recubrimientos PVD:
- Los revestimientos de PVD presentan una excelente resistencia al calor gracias a su elevada dureza y estabilidad química.Estas propiedades les permiten mantener la integridad estructural y el rendimiento incluso a temperaturas elevadas.
- Los revestimientos se utilizan a menudo en entornos de altas temperaturas, como en motores de automoción o componentes aeroespaciales, donde deben soportar tensiones térmicas sin degradarse.
-
Naturaleza fina y duradera:
- Los revestimientos PVD son extremadamente finos, de 0,5 a 5 micras, pero su durabilidad es excepcional.Esta delgadez no compromete su capacidad para resistir el calor, ya que los materiales utilizados en PVD (por ejemplo, TiN, CrN) son intrínsecamente resistentes al calor.
- La adherencia de los revestimientos al sustrato es fuerte, lo que garantiza que permanezcan intactos incluso bajo ciclos térmicos o tensiones mecánicas.
-
Aplicaciones en entornos de alta temperatura:
-
Los revestimientos PVD se utilizan ampliamente en industrias en las que la resistencia al calor es crítica.Por ejemplo:
- Automoción:En componentes de motores como pistones y válvulas, donde las altas temperaturas y la fricción son habituales.
- Aeroespacial:En álabes de turbinas y otras piezas expuestas a calor extremo durante el funcionamiento.
- Médico:En instrumentos quirúrgicos sometidos a esterilización repetida a altas temperaturas.
-
Los revestimientos PVD se utilizan ampliamente en industrias en las que la resistencia al calor es crítica.Por ejemplo:
-
Comparación con otros métodos de recubrimiento:
- Los revestimientos PVD superan a muchos métodos de revestimiento tradicionales, como la galvanoplastia, en términos de resistencia al calor.Son más duros, más resistentes a la corrosión y más adecuados para aplicaciones a altas temperaturas.
- A diferencia de algunos revestimientos que pueden degradarse u oxidarse a altas temperaturas, los revestimientos PVD mantienen sus propiedades, lo que los convierte en una opción fiable para entornos exigentes.
-
Limitaciones de los revestimientos PVD en la resistencia al calor:
- Aunque los revestimientos PVD son resistentes al calor, su rendimiento puede verse influido por el material del sustrato y el proceso PVD específico utilizado.Por ejemplo, los revestimientos de determinadas aleaciones pueden funcionar mejor bajo tensión térmica que otros.
- La delgadez del revestimiento, aunque beneficiosa para muchas propiedades, también puede limitar su capacidad para proporcionar protección a largo plazo en entornos de temperaturas extremadamente altas sin un soporte de sustrato adecuado.
-
Rendimiento específico del material:
-
La resistencia al calor de los revestimientos PVD puede variar en función de los materiales utilizados.Por ejemplo:
- TiN (nitruro de titanio):Conocido por su gran dureza y estabilidad térmica, lo que lo hace ideal para aplicaciones de alta temperatura.
- CrN (Nitruro de cromo):Ofrece una excelente resistencia a la oxidación y suele utilizarse en entornos con temperaturas elevadas.
- La elección del material de revestimiento puede adaptarse a los requisitos específicos de resistencia al calor.
-
La resistencia al calor de los revestimientos PVD puede variar en función de los materiales utilizados.Por ejemplo:
-
Ventajas adicionales que contribuyen a la resistencia al calor:
-
Los revestimientos de PVD proporcionan otras propiedades que mejoran indirectamente su resistencia al calor:
- Resistencia al desgaste:Reduce la pérdida de material por fricción, lo que es crucial en aplicaciones de alta temperatura.
- Resistencia a la corrosión:Protege el sustrato de la oxidación y la degradación química, que puede agravarse con el calor.
- Baja fricción:Minimiza la generación de calor debido a la fricción, mejorando aún más el rendimiento del revestimiento en entornos de alta temperatura.
-
Los revestimientos de PVD proporcionan otras propiedades que mejoran indirectamente su resistencia al calor:
En resumen, los revestimientos PVD son resistentes al calor y muy adecuados para aplicaciones que requieren durabilidad a altas temperaturas.Su delgadez, dureza y estabilidad química los convierten en la opción preferida en industrias en las que el estrés térmico es un problema.Sin embargo, su rendimiento puede variar en función del sustrato y del material de revestimiento específico, por lo que una selección cuidadosa es esencial para obtener resultados óptimos.
Tabla resumen:
Propiedad | Descripción |
---|---|
Resistencia al calor | Su elevada dureza y estabilidad química garantizan el rendimiento a temperaturas elevadas. |
Espesor | De 0,5 a 5 micras, ofrece durabilidad sin comprometer la resistencia al calor. |
Aplicaciones | Automoción (piezas de motor), aeroespacial (álabes de turbina), medicina (herramientas quirúrgicas). |
Ejemplos de materiales | TiN (nitruro de titanio), CrN (nitruro de cromo). |
Ventajas adicionales | La resistencia al desgaste, la resistencia a la corrosión y la baja fricción mejoran la resistencia al calor. |
Descubra cómo los revestimientos PVD pueden mejorar sus aplicaciones de alta temperatura. póngase en contacto con nosotros ¡!