Los revestimientos PVD (deposición física de vapor) son famosos por su dureza, resistencia al desgaste y durabilidad, lo que los hace muy resistentes a los arañazos en muchas condiciones.Sin embargo, no son totalmente a prueba de arañazos.La resistencia al rayado de los revestimientos PVD depende de factores como el tipo de material de revestimiento, el sustrato sobre el que se aplica y las condiciones ambientales.Aunque los revestimientos PVD mejoran significativamente la dureza de la superficie y la resistencia al desgaste de los materiales, aún pueden ser rayados por sustancias más duras o bajo tensiones mecánicas extremas.Su delgadez (0,5-5 micras) y alta adherencia al sustrato contribuyen a su durabilidad, pero no son impermeables a todas las formas de abrasión o daño.
Explicación de los puntos clave:
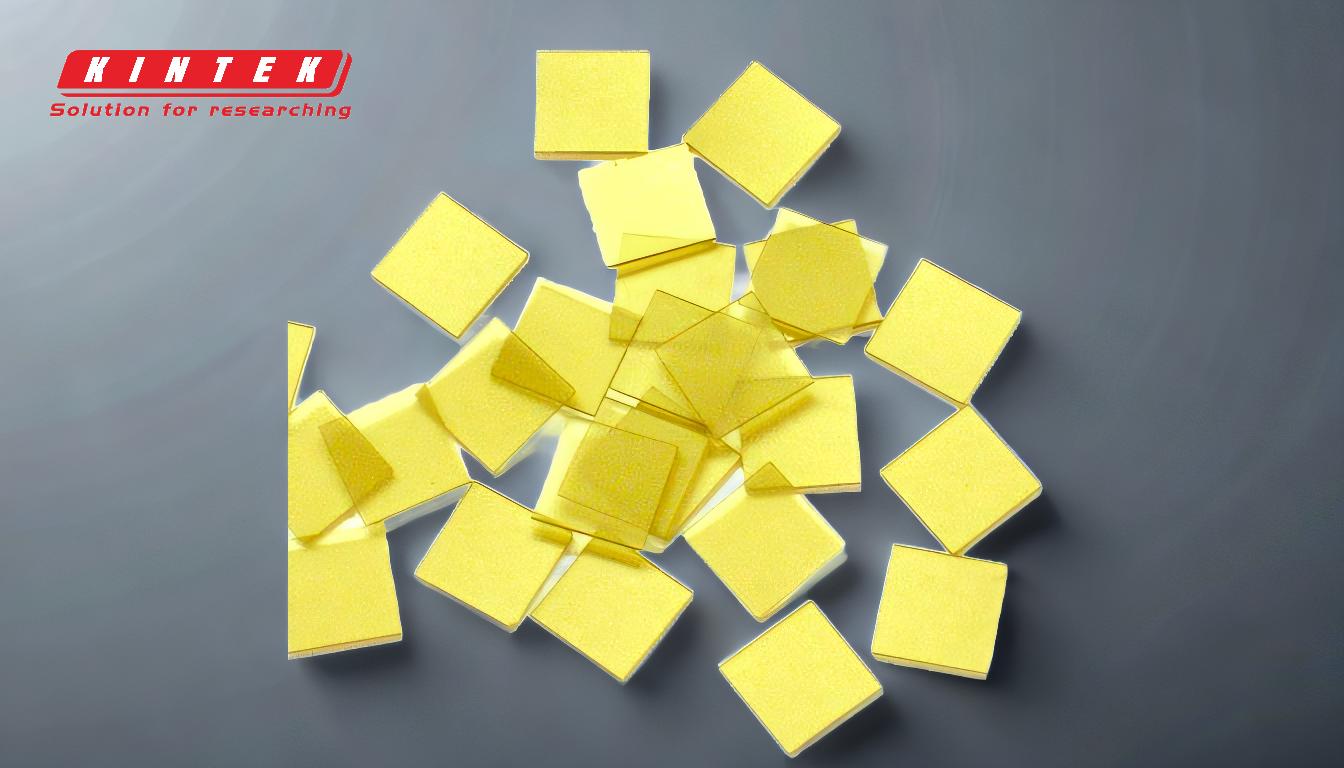
-
Los revestimientos PVD son muy resistentes a los arañazos, pero no son a prueba de arañazos
- Los revestimientos de PVD son conocidos por su gran dureza, que los hace resistentes a los arañazos y al desgaste.Sin embargo, "a prueba de arañazos" implica inmunidad total a los arañazos, lo que no es el caso.
- La dureza de los revestimientos de PVD, a menudo medida en la escala de Vickers, los hace más resistentes a los arañazos que muchos materiales sin tratar.Por ejemplo, revestimientos como el TiN (nitruro de titanio) y el CrN (nitruro de cromo) son excepcionalmente duros y duraderos.
- A pesar de su dureza, los revestimientos PVD pueden ser rayados por materiales u objetos más duros que el propio revestimiento, como diamantes o determinadas cerámicas.
-
El grosor y la adherencia contribuyen a la durabilidad
- Los revestimientos PVD son extremadamente finos, entre 0,5 y 5 micras.Esta delgadez les permite reproducir el acabado original del sustrato al tiempo que proporcionan una capa protectora.
- La excelente adherencia de los revestimientos PVD al sustrato garantiza que el revestimiento permanezca intacto ante el desgaste normal, reduciendo la probabilidad de arañazos.
- Sin embargo, la delgadez también significa que el revestimiento tiene una profundidad limitada, por lo que la abrasión repetida o las fuerzas de alto impacto pueden acabar desgastando el revestimiento.
-
El material y el sustrato influyen en la resistencia al rayado
- La resistencia al rayado de un revestimiento PVD depende del material utilizado para el revestimiento y del sustrato sobre el que se aplica.Por ejemplo, los revestimientos de TiN son más duros y resistentes a los arañazos que otros revestimientos.
- El material del sustrato también influye.Un sustrato más duro proporcionará un mejor soporte para el revestimiento PVD, mejorando su resistencia general a los arañazos.
- En algunos casos, la combinación de un revestimiento PVD con un sustrato específico puede mejorar significativamente el límite de fatiga y la resistencia del material, como ocurre con los revestimientos TiN sobre aleación Ti-6Al-4V.
-
Factores ambientales y de aplicación
- El entorno en el que se utiliza el material recubierto afecta a su resistencia al rayado.Por ejemplo, la exposición a partículas abrasivas o productos químicos agresivos puede reducir la eficacia del revestimiento con el paso del tiempo.
- Los revestimientos de PVD son ideales para aplicaciones en sectores como la automoción, el aeroespacial y el médico, donde la resistencia al desgaste y la durabilidad son fundamentales.Sin embargo, en condiciones extremas, incluso los revestimientos de PVD pueden verse comprometidos.
- El rendimiento del revestimiento en geometrías complejas, como el dorso y los laterales de las herramientas, puede ser menos eficaz debido a las limitaciones del proceso de deposición, que pueden afectar a la resistencia al rayado en esas zonas.
-
Ventajas y limitaciones
-
Ventajas:
- Elevada dureza y resistencia al desgaste.
- Excelente adherencia al sustrato.
- Resistencia a la corrosión y a la oxidación.
- Aspecto estético mejorado sin necesidad de pulido adicional.
-
Limitaciones:
- No es totalmente resistente a los arañazos, especialmente contra materiales más duros.
- Los revestimientos finos pueden desgastarse en condiciones extremas.
- El rendimiento puede variar en geometrías complejas o superficies irregulares.
-
Ventajas:
-
Aplicaciones en las que la resistencia al rayado es importante
-
Los revestimientos PVD se utilizan ampliamente en sectores en los que la resistencia a los arañazos es fundamental, como:
- Automoción:Para componentes como segmentos de pistón y piezas de motor.
- Aeroespacial:Para álabes de turbinas y otros componentes sometidos a grandes esfuerzos.
- Médico:Para instrumentos quirúrgicos e implantes.
- Bienes de consumo:Para carcasas de relojes, marcos de smartphones y artículos decorativos.
- En estas aplicaciones, los revestimientos de PVD ofrecen un equilibrio entre durabilidad, estética y funcionalidad, aunque no son inmunes a todo tipo de daños.
-
Los revestimientos PVD se utilizan ampliamente en sectores en los que la resistencia a los arañazos es fundamental, como:
En conclusión, aunque los revestimientos de PVD son muy resistentes a los arañazos gracias a su dureza, resistencia al desgaste y excelente adherencia, no son totalmente a prueba de arañazos.Su rendimiento depende del material de revestimiento, el sustrato y las condiciones ambientales.En la mayoría de las aplicaciones prácticas, los revestimientos de PVD ofrecen una protección significativa contra los arañazos y el desgaste, lo que los convierte en una opción valiosa para mejorar la durabilidad y longevidad de diversos materiales y componentes.
Tabla resumen:
Aspecto clave | Detalles |
---|---|
Resistencia al rayado | Altamente resistente pero no a prueba de arañazos; depende del material y del sustrato. |
Espesor del revestimiento | 0,5-5 micras, proporcionando durabilidad a la vez que mantiene el acabado del sustrato. |
Adherencia | La excelente adherencia garantiza una protección duradera en condiciones normales. |
Influencia del material | Los revestimientos de TiN y CrN ofrecen una dureza y una resistencia al rayado superiores. |
Factores ambientales | Las condiciones duras o las partículas abrasivas pueden reducir la eficacia. |
Aplicaciones | Industria automovilística, aeroespacial, médica y de bienes de consumo. |
Ventajas | Gran dureza, resistencia al desgaste, resistencia a la corrosión y atractivo estético. |
Limitaciones | No es totalmente a prueba de arañazos; los revestimientos finos pueden desgastarse bajo tensiones extremas. |
Descubra cómo los revestimientos PVD pueden mejorar la durabilidad de sus productos. contacte con nuestros expertos hoy mismo ¡!