El proceso de fluidización, especialmente en los reactores de lecho fluidizado (FBR), ofrece importantes ventajas en diversas aplicaciones industriales, como el procesamiento de productos químicos, petróleo y biomasa.Las principales ventajas son la mezcla uniforme de partículas, los gradientes de temperatura constantes y la capacidad de funcionar de forma continua.Estas características mejoran la eficacia de la reacción, evitan los puntos calientes o fríos y eliminan la necesidad de procesar por lotes, lo que hace que los FBR sean muy eficaces para reacciones exotérmicas y sustratos particulados como la biomasa leñosa.Además, los FBR mejoran el rendimiento de subproductos como los bioaceites y los gases, lo que los convierte en una opción versátil y eficiente para los procesos industriales.
Explicación de los puntos clave:
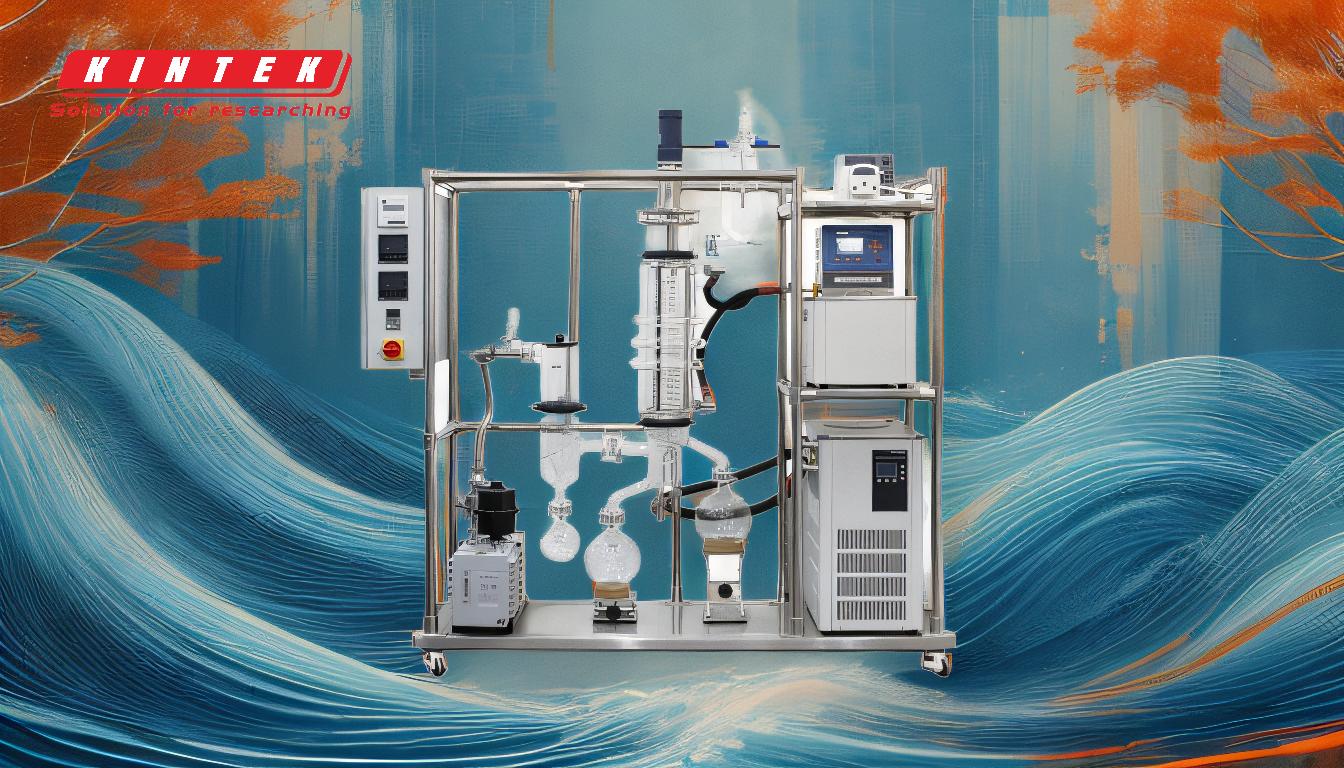
-
Mezcla uniforme de partículas
- Los reactores de lecho fluidizado garantizan una mezcla completa de las partículas sólidas gracias a su comportamiento similar al de los fluidos.
- Esto elimina los gradientes de concentración radiales y axiales, lo que mejora la eficacia de la reacción.
- La mezcla uniforme es especialmente beneficiosa para sustratos particulados como la biomasa leñosa, ya que garantiza un contacto constante entre los reactivos y los catalizadores.
-
Gradientes de temperatura uniformes
- Los FBR mantienen gradientes de temperatura uniformes en todo el reactor, evitando la formación de puntos calientes o fríos.
- Esta uniformidad es fundamental para las reacciones exotérmicas, en las que los picos de temperatura localizados pueden provocar ineficiencias o riesgos para la seguridad.
- El entorno de temperatura controlada mejora la estabilidad y previsibilidad del proceso.
-
Funcionamiento continuo
- A diferencia de los procesos por lotes, los FBR pueden funcionar de forma continua, eliminando la necesidad de frecuentes arranques y paradas.
- El funcionamiento continuo mejora la eficiencia de la producción y reduce el tiempo de inactividad, por lo que los FBR son ideales para aplicaciones industriales a gran escala.
- Esta característica es especialmente ventajosa en industrias como el refino de petróleo y la fabricación de productos químicos, donde es esencial un alto rendimiento.
-
Mayor producción de subproductos
- Los FBR son muy eficaces para maximizar el rendimiento de subproductos valiosos como bioaceites y gases.
- El proceso de fluidización garantiza un contacto óptimo entre los reactivos y los catalizadores, lo que da lugar a reacciones más completas y eficaces.
- Esto convierte a los FBR en la opción preferida para el procesamiento de biomasa y otras aplicaciones en las que la recuperación de subproductos es económicamente importante.
-
Versatilidad en todos los sectores
- Los FBR se utilizan ampliamente en diversas industrias, como la petrolera, la química y la de procesamiento de biomasa.
- Su capacidad para tratar sustratos particulados y reacciones exotérmicas los hace adaptables a una amplia gama de procesos.
- Esta versatilidad, combinada con su eficiencia y funcionamiento continuo, sitúa a los FBR como una tecnología fundamental en las operaciones industriales modernas.
-
Eficacia de reacción mejorada
- El comportamiento fluido de los materiales sólidos en los FBR garantiza una mezcla completa y unas condiciones de reacción óptimas.
- Esto conduce a velocidades de reacción más rápidas y mayores eficiencias de conversión en comparación con los reactores tradicionales.
- La eliminación de los gradientes de concentración mejora aún más el rendimiento global del reactor.
-
Escalabilidad y rentabilidad
- Los FBR son escalables, lo que los hace adecuados para aplicaciones industriales tanto a pequeña como a gran escala.
- Su funcionamiento continuo reduce los costes operativos al minimizar el consumo de energía y el tiempo de inactividad.
- Su capacidad para manipular una amplia gama de materiales y reacciones contribuye aún más a su rentabilidad.
-
Beneficios medioambientales
- El uso eficiente de reactivos y catalizadores en los FBR reduce la generación de residuos y mejora la utilización de los recursos.
- El entorno de temperatura controlada minimiza el riesgo de emisiones nocivas o subproductos.
- Estas ventajas medioambientales están en consonancia con los objetivos de sostenibilidad y los requisitos normativos de diversos sectores.
Al aprovechar estas ventajas, los reactores de lecho fluidizado proporcionan una solución robusta y eficiente para una amplia gama de procesos industriales, lo que los convierte en la opción preferida para aplicaciones que requieren alta eficiencia, escalabilidad y funcionamiento continuo.
Tabla resumen:
Ventaja | Ventaja clave |
---|---|
Mezcla uniforme de partículas | Garantiza una mezcla completa, eliminando los gradientes de concentración para una mayor eficacia. |
Gradientes de temperatura uniformes | Evita puntos calientes o fríos, ideal para reacciones exotérmicas. |
Funcionamiento continuo | Elimina el procesamiento por lotes, reduciendo el tiempo de inactividad y mejorando el rendimiento. |
Mayor rendimiento de los subproductos | Maximiza los bioaceites y gases, optimizando la utilización de los recursos. |
Versatilidad en todas las industrias | Adaptable al procesamiento de petróleo, productos químicos y biomasa. |
Eficiencia de reacción mejorada | Velocidades de reacción más rápidas y mayores eficiencias de conversión. |
Escalabilidad y rentabilidad | Adecuada para aplicaciones a pequeña y gran escala, reduce los costes operativos. |
Beneficios medioambientales | Reduce los residuos y las emisiones nocivas, alineándose con los objetivos de sostenibilidad. |
¿Está listo para mejorar sus procesos industriales con reactores de lecho fluidizado? Póngase en contacto con nuestros expertos para obtener más información.