El sinterizado selectivo por láser (SLS) es un complejo proceso de fabricación aditiva en el que influyen múltiples factores que determinan la calidad, la eficacia y las propiedades del producto final.Los factores clave son la temperatura, la velocidad de calentamiento, la presión, el tamaño de las partículas y la composición del material.La temperatura rige la cinética de sinterización y las propiedades del material, mientras que la velocidad de calentamiento afecta a la densificación y la microestructura.La presión contribuye a la reorganización de las partículas y a la reducción de la porosidad.El tamaño y la composición de las partículas desempeñan un papel fundamental en el comportamiento de la sinterización, ya que las partículas más pequeñas y las composiciones homogéneas mejoran la densificación y las propiedades mecánicas.Comprender estos factores es esencial para optimizar el proceso de SLS y conseguir piezas de alta calidad.
Explicación de los puntos clave:
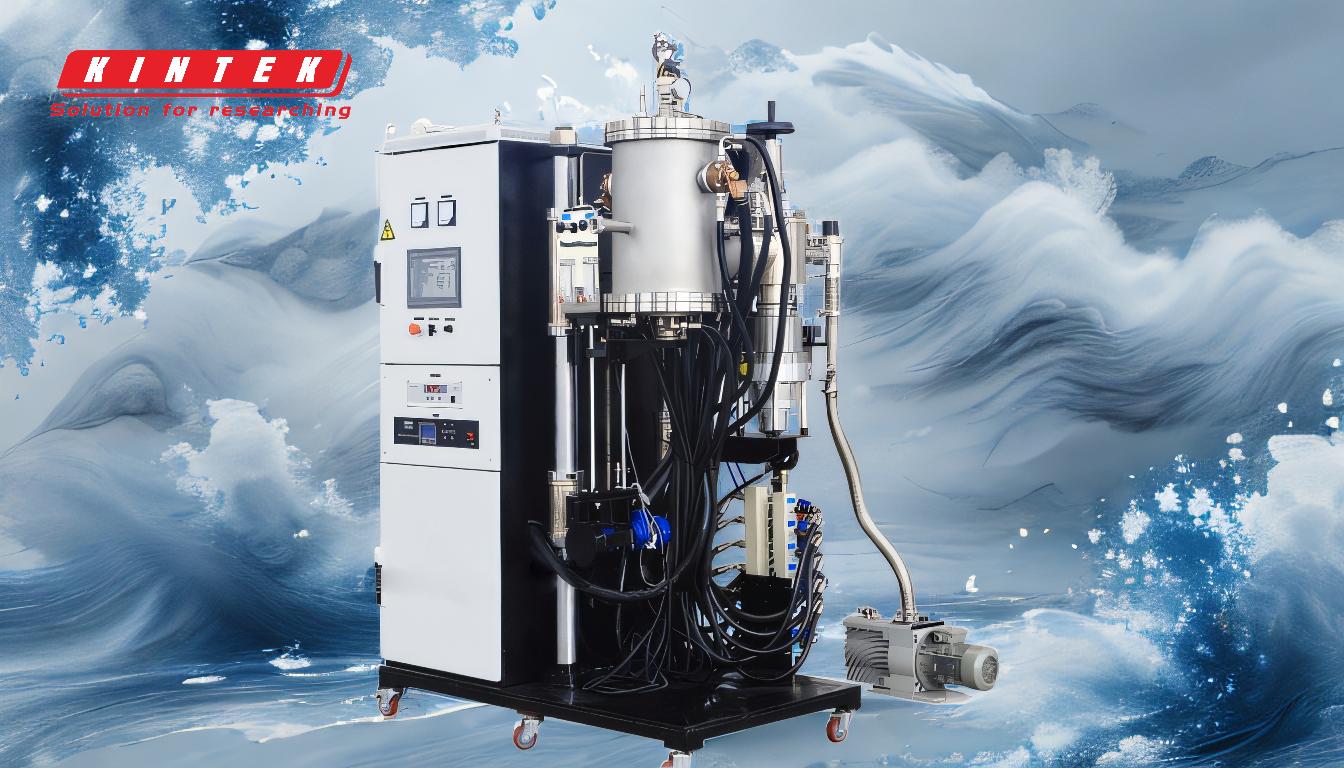
-
Temperatura:
- Papel:La temperatura es un factor crítico en el SLS, ya que influye directamente en la cinética de sinterización y en las propiedades finales del material.Determina la velocidad a la que se adhieren las partículas y el grado de densificación.
- Impacto:En general, las temperaturas más altas aceleran la sinterización, pero deben controlarse cuidadosamente para evitar defectos como el alabeo o un crecimiento excesivo del grano.Una temperatura óptima garantiza una unión adecuada sin comprometer la integridad de la pieza.
-
Velocidad de calentamiento:
- Papel:La velocidad de calentamiento afecta a la rapidez con la que el material alcanza la temperatura de sinterización e influye en el proceso de densificación.
- Impacto:Una velocidad de calentamiento controlada garantiza una densificación uniforme y minimiza los gradientes térmicos, que pueden provocar tensiones internas y distorsión de la pieza.Un calentamiento rápido puede provocar una sinterización incompleta, mientras que un calentamiento lento puede dar lugar a un consumo excesivo de energía.
-
Presión:
- Papel:La presión, aunque no siempre se aplica en el SLS, puede favorecer la reorganización de las partículas y reducir la porosidad.
- Impacto:La presión aplicada ayuda a conseguir un mejor contacto y densificación de las partículas, lo que mejora las propiedades mecánicas.Sin embargo, una presión excesiva puede provocar deformaciones o daños en la pieza.
-
Tamaño de las partículas:
- Papel:El tamaño de las partículas influye significativamente en el comportamiento de sinterización, ya que las partículas más pequeñas tienen mayor energía superficial y mayor fuerza motriz para la sinterización.
- Impacto:Las partículas más pequeñas favorecen una densificación más rápida y uniforme, dando lugar a piezas de mayor densidad y mejores propiedades mecánicas.Las partículas más grandes pueden provocar una sinterización incompleta y un aumento de la porosidad.
-
Composición del material:
- Papel:La composición del material determina su comportamiento de sinterización, incluido el punto de fusión, la conductividad térmica y las características de adherencia.
- Impacto:Las composiciones homogéneas con una distribución uniforme de las partículas garantizan una sinterización uniforme y una mejor calidad de las piezas.Las composiciones no homogéneas pueden provocar una densificación desigual y defectos.
-
Potencia láser y velocidad de exploración:
- Papel:La potencia del láser y la velocidad de barrido son parámetros críticos en SLS que controlan la entrada de energía y el tiempo de interacción con el material.
- Impacto:Una mayor potencia del láser y velocidades de exploración más lentas aumentan el aporte de energía, lo que favorece una mejor sinterización pero entraña el riesgo de sobrecalentamiento.Una potencia más baja y velocidades más rápidas pueden dar lugar a una sinterización insuficiente.Equilibrar estos parámetros es crucial para una calidad óptima de la pieza.
-
Espesor de capa:
- Papel:El grosor de la capa afecta a la resolución y al acabado superficial de la pieza final.
- Impacto:Las capas más finas ofrecen mayor resolución y superficies más lisas, pero aumentan el tiempo de fabricación.Las capas más gruesas reducen el tiempo de fabricación pero pueden comprometer la precisión de la pieza y la calidad de la superficie.
-
Atmósfera:
- Papel:El entorno de sinterización, normalmente una atmósfera inerte, evita la oxidación y la contaminación.
- Impacto:Una atmósfera controlada garantiza la constancia de las propiedades del material y evita los defectos causados por la oxidación o la contaminación.Un control inadecuado de la atmósfera puede provocar la degradación de las piezas.
-
Tratamiento posterior:
- Papel:Las fases de postprocesado, como el tratamiento térmico o el acabado superficial, pueden mejorar las propiedades de las piezas.
- Impacto:Un postprocesado adecuado mejora las propiedades mecánicas, la precisión dimensional y el acabado superficial.Descuidar el postprocesado puede dar lugar a un rendimiento subóptimo de la pieza.
Controlando y optimizando cuidadosamente estos factores, los fabricantes pueden conseguir piezas SLS de alta calidad con las propiedades deseadas, garantizando la eficacia y rentabilidad del proceso.
Tabla resumen:
Factor | Papel | Impacto |
---|---|---|
Temperatura | Regula la cinética de sinterización y las propiedades del material. | Las temperaturas más altas aceleran la sinterización pero pueden provocar defectos; las temperaturas óptimas garantizan la adhesión. |
Velocidad de calentamiento | Afecta a la densificación y a la microestructura. | El calentamiento controlado garantiza una densificación uniforme; el calentamiento rápido puede causar problemas. |
Presión | Favorece la reorganización de las partículas y reduce la porosidad. | Mejora la densificación, pero una presión excesiva puede deformar las piezas. |
Tamaño de las partículas | Las partículas más pequeñas tienen mayor energía superficial para la sinterización. | Las partículas más pequeñas conducen a una mejor densificación y propiedades mecánicas. |
Composición del material | Determina el comportamiento de sinterización y las características de adhesión. | Las composiciones homogéneas garantizan una sinterización y una calidad de las piezas uniformes. |
Potencia láser y velocidad de exploración | Controla la entrada de energía y el tiempo de interacción. | Equilibrar estos parámetros es crucial para una sinterización óptima. |
Espesor de capa | Afecta a la resolución y al acabado superficial. | Las capas más finas mejoran la resolución pero aumentan el tiempo de construcción. |
Atmósfera | Evita la oxidación y la contaminación. | La atmósfera controlada garantiza la uniformidad de las propiedades del material. |
Postprocesado | Mejora las propiedades mecánicas, la precisión y el acabado superficial. | Un postprocesado adecuado mejora el rendimiento de la pieza. |
¿Está listo para optimizar su proceso SLS? Póngase en contacto con nuestros expertos para obtener soluciones a medida.