El espesor del revestimiento PVD (deposición física de vapor) suele oscilar entre 0,25 micras (μm) y 5 micras (μm), en función de la aplicación y las propiedades deseadas.Este revestimiento de película fina está diseñado para mejorar propiedades superficiales como la dureza, la suavidad, la resistencia a la corrosión y la resistencia al desgaste sin alterar significativamente las dimensiones o el aspecto del sustrato.El grosor se controla cuidadosamente para garantizar un rendimiento óptimo, ya que las aplicaciones decorativas suelen requerir revestimientos más finos (por ejemplo, de 0,30 micras) y las aplicaciones funcionales (por ejemplo, herramientas o piezas industriales), revestimientos más gruesos (por ejemplo, de 2 a 5 micras).Los revestimientos PVD son muy duraderos, resistentes al desgaste y la corrosión, y pueden reproducir el acabado original de los materiales con un esfuerzo mínimo.
Explicación de los puntos clave:
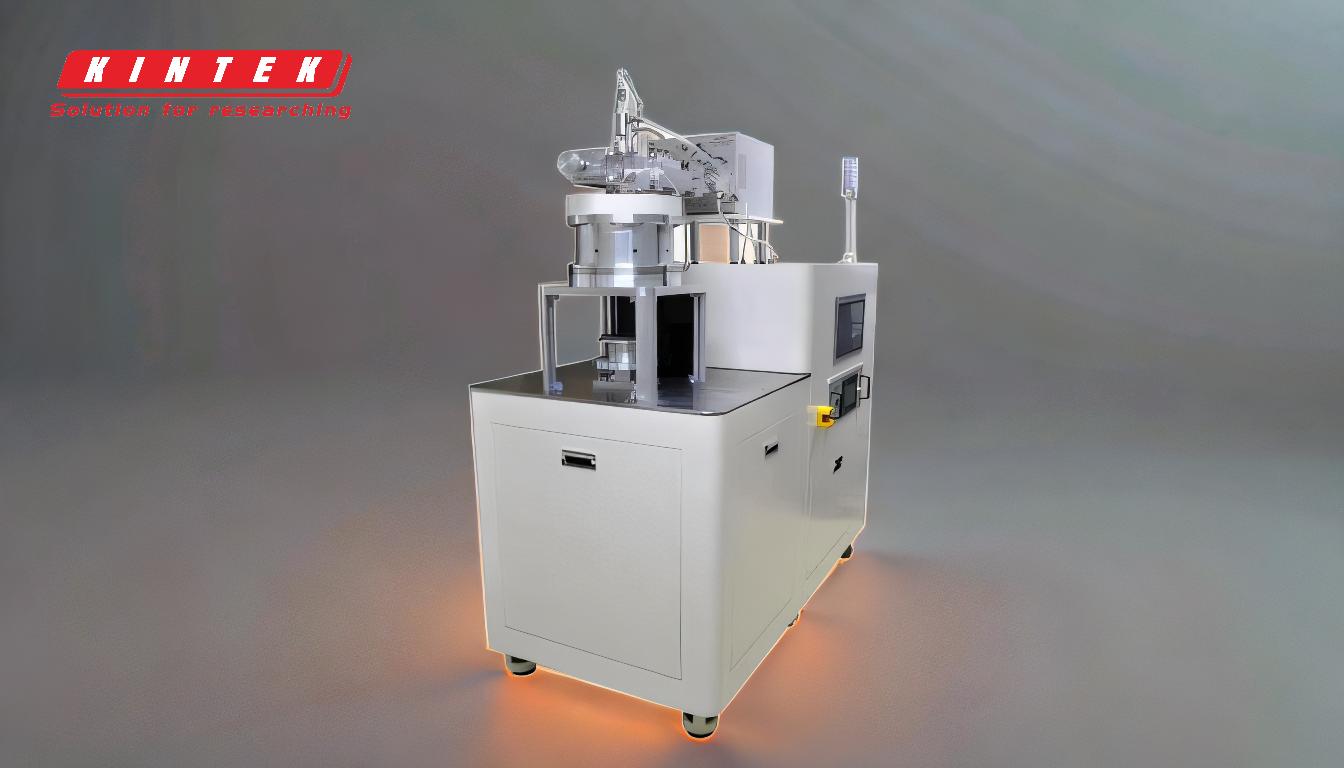
-
Gama de espesores típicos de los recubrimientos PVD:
- Los revestimientos de PVD oscilan generalmente entre 0,25 micras a 5 micras de espesor.
- Esta gama se elige para equilibrar las mejoras de rendimiento (por ejemplo, dureza, resistencia a la corrosión) con un impacto mínimo en las dimensiones y el aspecto del sustrato.
- Con fines decorativos, los revestimientos pueden ser tan finos como 0,30 micras mientras que las aplicaciones funcionales suelen requerir revestimientos más gruesos de 2 a 5 micras .
-
Por qué el espesor del revestimiento PVD es fino:
- Los revestimientos de PVD están diseñados para ser finos y no alterar las especificaciones de las piezas de ingeniería.
- La delgadez garantiza que el revestimiento se adhiera bien al sustrato y mantenga las dimensiones y tolerancias originales de la pieza.
- A pesar de su delgadez, los revestimientos PVD proporcionan mejoras significativas en las propiedades superficiales, como la dureza, la resistencia al desgaste y la resistencia a la corrosión.
-
Aplicaciones y variaciones de espesor:
- Aplicaciones decorativas:Para productos como las chapas de acero inoxidable, el espesor del revestimiento suele ser de unas 0,30 micras para conseguir un acabado pulido y metálico sin añadir volumen.
- Aplicaciones funcionales:En aplicaciones industriales o de utillaje, los revestimientos más gruesos (p. ej, 2 a 5 micras ) se utilizan para aumentar la durabilidad, la dureza y la resistencia al desgaste y la corrosión.
- La elección del espesor depende de factores como el tipo de movimiento, la lubricación y el acabado superficial requerido para la aplicación.
-
Ventajas de los revestimientos PVD finos:
- Alta pureza y uniformidad:Los revestimientos de PVD son altamente uniformes y puros, lo que garantiza un rendimiento constante en toda la superficie revestida.
- Excelente adherencia:Las películas finas se adhieren fuertemente al sustrato, reduciendo el riesgo de pelado o descascarillado.
- Propiedades superficiales mejoradas:A pesar de su delgadez, los revestimientos PVD mejoran significativamente la dureza, la resistencia a la abrasión y la resistencia a la corrosión.
- Replicación estética:Los revestimientos de PVD pueden reproducir el acabado original de los materiales, manteniendo su aspecto al tiempo que añaden ventajas funcionales.
-
Comparación con otros métodos de revestimiento:
- Los revestimientos PVD suelen ser más duros y resistentes a la corrosión que los aplicados mediante galvanoplastia.
- La delgadez de los revestimientos PVD permite aplicarlos sin necesidad de capas protectoras adicionales, lo que simplifica el proceso de revestimiento y reduce los costes.
- Los revestimientos PVD también son más duraderos y resistentes a las altas temperaturas y los impactos que los métodos de revestimiento tradicionales.
-
Desafíos del grosor del revestimiento PVD:
- Uniformidad en formas complejas:Los revestimientos PVD pueden tener dificultades para conseguir un espesor uniforme en la parte posterior y los laterales de las herramientas o en geometrías complejas debido a la baja presión del aire durante el proceso de deposición.
- Control del espesor:El control preciso del espesor del revestimiento es necesario para garantizar un rendimiento óptimo, especialmente en aplicaciones funcionales en las que un revestimiento demasiado fino o demasiado grueso podría comprometer el rendimiento.
-
Ejemplos reales de grosor:
- Como referencia, 25 micras equivalen a 0,001 pulgadas un glóbulo rojo mide aproximadamente 8 micras de diámetro, y un cabello humano mide aproximadamente 80 micras de diámetro.
- Esto pone de manifiesto lo finos que son los revestimientos de PVD, incluso con su espesor máximo de 5 micras .
En resumen, el grosor del revestimiento PVD es un factor crítico a la hora de determinar el rendimiento y la idoneidad del revestimiento para aplicaciones específicas.La delgadez de los revestimientos PVD garantiza que mejoren las propiedades de la superficie sin comprometer las dimensiones o el aspecto del sustrato, lo que los hace ideales para usos tanto decorativos como funcionales.
Cuadro sinóptico:
Aspecto | Detalles |
---|---|
Grosor típico | 0,25 a 5 micras |
Aplicaciones decorativas | ~0,30 micras para acabados pulidos |
Aplicaciones funcionales | De 2 a 5 micras para mayor durabilidad y resistencia al desgaste |
Beneficios clave | Dureza, resistencia a la corrosión, resistencia al desgaste y reproducción estética |
Desafíos | Uniformidad en formas complejas y control preciso del espesor |
Descubra cómo los revestimientos PVD pueden mejorar el rendimiento de sus productos. contacte hoy con nuestros expertos ¡!