La pirólisis de neumáticos es un proceso termoquímico que convierte los neumáticos usados en productos valiosos como aceite de pirólisis, negro de humo, alambre de acero y gas de síntesis.El proceso consiste en calentar los neumáticos en ausencia de oxígeno para descomponer sus polímeros de cadena larga en moléculas más pequeñas.Este método es beneficioso para el medio ambiente, ya que reduce los residuos de neumáticos y genera materiales reutilizables.El proceso suele consistir en introducir neumáticos enteros o triturados en un reactor, calentarlos a altas temperaturas (300-900°C) y condensar los vapores resultantes en aceite líquido.Los gases no condensables se limpian y almacenan, mientras que los residuos sólidos, como el negro de humo y el alambre de acero, se recogen para su uso posterior.Todo el proceso consume mucha energía y requiere un control preciso de la temperatura y los niveles de oxígeno para garantizar la eficacia y la seguridad.
Explicación de los puntos clave:
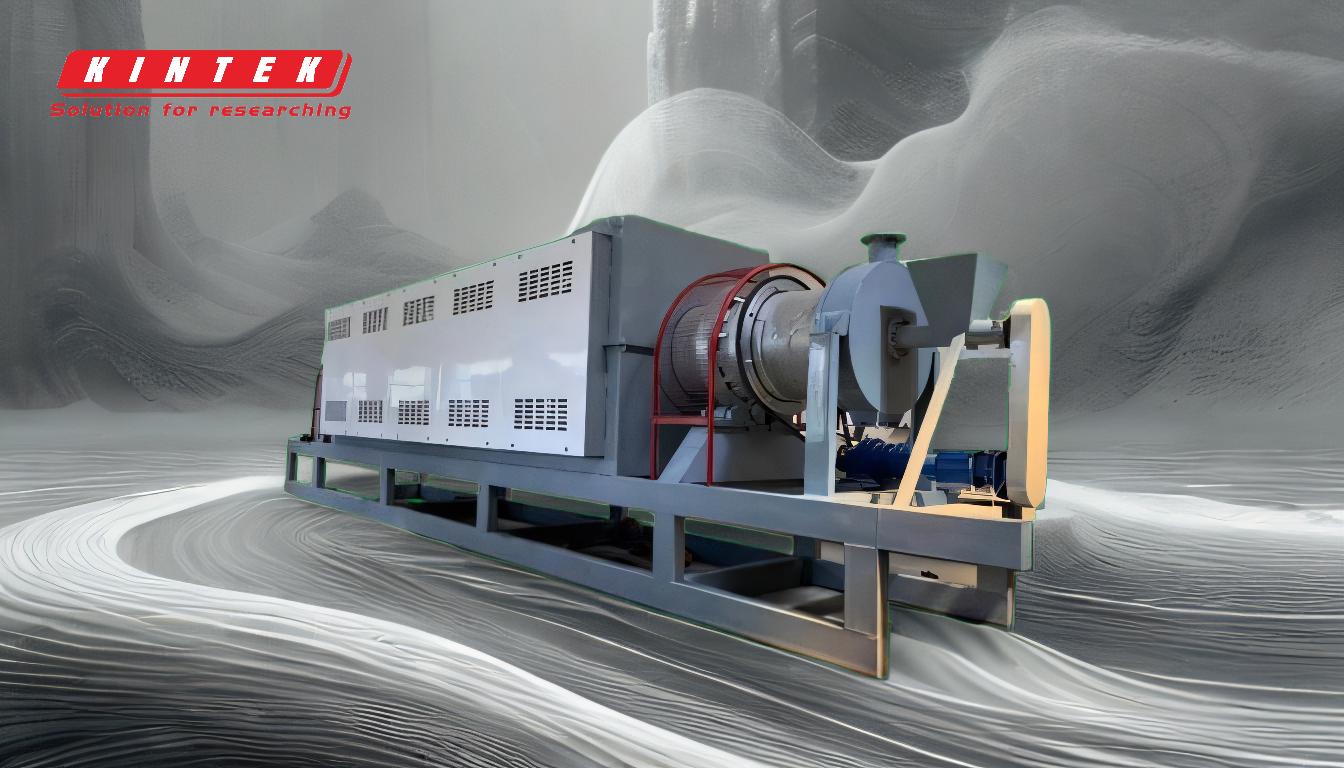
-
Definición y finalidad de la pirólisis:
- La pirólisis es un proceso de descomposición térmica que se produce en ausencia de oxígeno, descomponiendo los materiales en moléculas más pequeñas.
- En el caso de los neumáticos, la pirólisis convierte los residuos en productos útiles como aceite, negro de humo, alambre de acero y gas de síntesis, reduciendo los residuos medioambientales y generando valiosos recursos.
-
Pretratamiento de neumáticos:
- Los neumáticos se introducen enteros o triturados en el reactor.
- El pretratamiento puede incluir la eliminación de impurezas, la separación magnética para extraer los alambres de acero y la trituración de los neumáticos al tamaño necesario para un procesamiento eficaz.
-
Calentamiento y despolimerización:
- El reactor se calienta a temperaturas de entre 300 y 900°C en un entorno sin oxígeno.
- La alta temperatura hace que los neumáticos se fundan y vaporicen, descomponiendo los polímeros de cadena larga en moléculas de hidrocarburo más pequeñas.
-
Condensación y separación de productos:
- Los gases vaporizados fluyen a través de un intercambiador de calor, donde se condensan en aceite de pirólisis líquido.
- Los gases no condensables (syngas) se desulfuran, se limpian y se almacenan para su uso como combustible o para su posterior procesamiento.
-
Recogida de productos finales:
- Aceite de pirólisis:Recogido en forma líquida, puede utilizarse para calefacción, generación de energía o como materia prima para la producción de hidrógeno.
- Negro de humo:Residuo sólido, se utiliza en la fabricación de neumáticos, tintas y otras aplicaciones industriales.
- Alambre de acero:Extraído mediante separación magnética, se recicla para su uso en la construcción o la fabricación.
- Syngas:Los gases no condensables se almacenan y pueden utilizarse para alimentar el proceso de pirólisis o para otras necesidades energéticas.
-
Consideraciones energéticas y medioambientales:
- El proceso es intensivo en energía, ya que requiere un importante aporte de calor para mantener altas temperaturas.
- El control adecuado de los niveles de oxígeno es crucial para evitar la combustión y garantizar que el proceso siga siendo puramente de descomposición térmica.
- La pirólisis reduce los residuos de neumáticos en los vertederos y genera materiales reutilizables, contribuyendo a una economía circular.
-
Eficiencia del proceso y retos:
- La eficacia del proceso depende de factores como el control de la temperatura, el diseño del reactor y la calidad de la materia prima.
- Los retos incluyen la gestión de los requisitos energéticos, la garantía de una calidad constante del producto y la gestión de las emisiones o subproductos que pueden requerir un tratamiento posterior.
-
Aplicaciones de los productos de pirólisis:
- Aceite de pirólisis:Utilizado como sustituto del combustible o refinado para la producción química.
- Negro de humo:Reciclado en neumáticos nuevos o productos industriales.
- Alambre de acero:Reciclado para su uso en la construcción o la fabricación.
- Syngas:Se utiliza como fuente de combustible o para generar electricidad.
Siguiendo estos pasos, la pirólisis de neumáticos no sólo aborda el problema de los residuos de neumáticos, sino que también crea una vía sostenible para la recuperación de recursos y la generación de energía.
Tabla resumen:
Productos clave | Aplicaciones |
---|---|
Aceite de pirólisis | Calefacción, generación de energía, materia prima para la producción de hidrógeno |
Negro de humo | Fabricación de neumáticos, tintas y productos industriales |
Alambre de acero | Reciclado para la construcción o la fabricación |
Syngas | Utilizado como combustible o para generar electricidad |
Descubra cómo la pirólisis puede transformar los residuos de neumáticos en valiosos recursos-. póngase en contacto con nosotros para más detalles