El PVD, o depósito físico en fase vapor, es una técnica de deposición de materiales utilizada para crear películas finas y revestimientos sobre diversas superficies.Implica el uso de metales y otros materiales para formar revestimientos muy duraderos, resistentes al desgaste y a la corrosión.Los revestimientos PVD son conocidos por su capacidad para mejorar las propiedades de los sustratos, como la mejora de la dureza, la reducción de la fricción y el aumento de la resistencia a la oxidación y a las altas temperaturas.El proceso se lleva a cabo a temperaturas más bajas en comparación con otros métodos como el CVD (deposición química de vapor), lo que lo hace adecuado para una amplia gama de aplicaciones, como la aeroespacial, los revestimientos decorativos y los tratamientos del vidrio.
Explicación de los puntos clave:
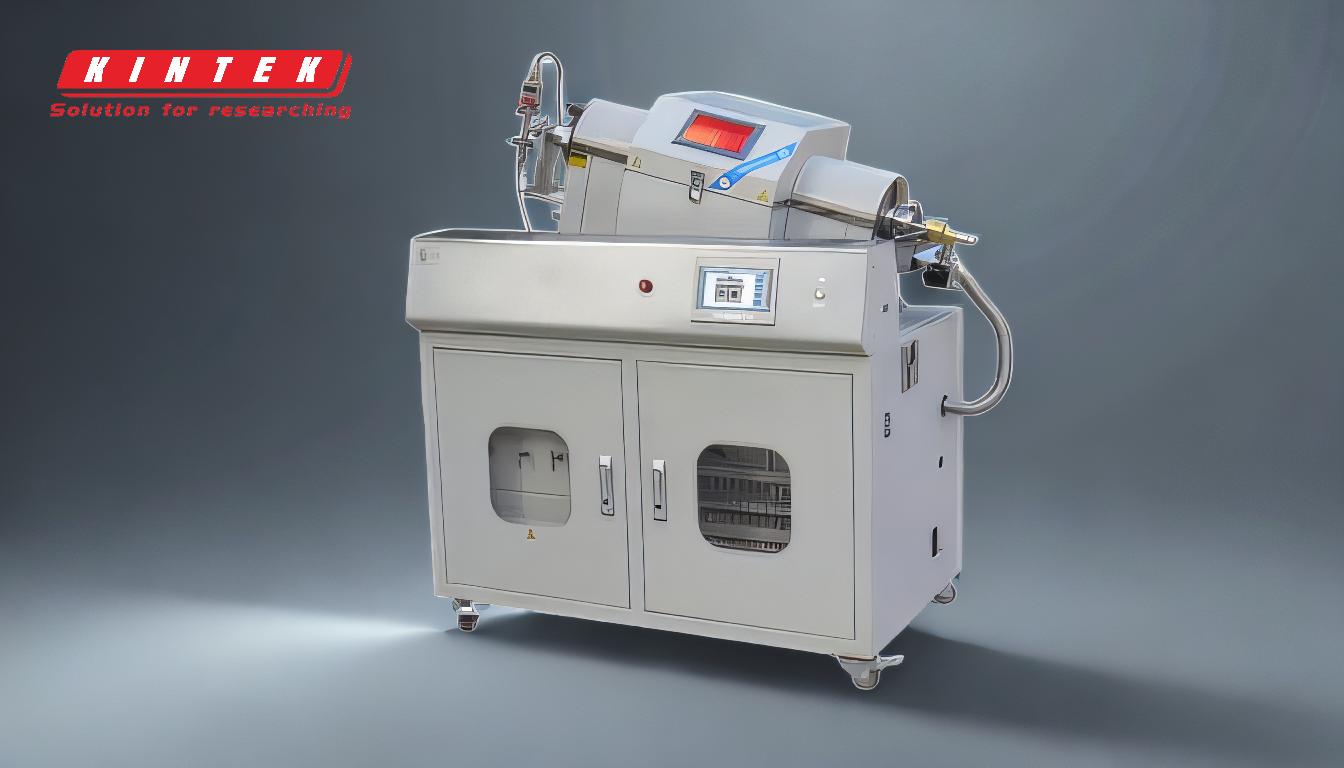
-
Definición de PVD:
- PVD son las siglas de Physical Vapor Deposition, una técnica utilizada para depositar películas finas y revestimientos sobre superficies.
- Consiste en la transferencia física de material de una fuente a un sustrato, normalmente en un entorno de vacío.
-
Materiales utilizados en PVD:
- Los materiales de PVD incluyen principalmente metales como el titanio, el cromo, el aluminio y sus compuestos [por ejemplo, nitruro de titanio (TiN), nitruro de cromo (CrN)].
- Estos materiales se eligen por su capacidad para formar revestimientos duros, duraderos y resistentes a la corrosión.
-
Propiedades de los revestimientos PVD:
- Resistencia al desgaste:Los revestimientos de PVD son muy resistentes al desgaste, por lo que son ideales para aplicaciones en las que la durabilidad es fundamental.
- Esfuerzo de compresión:Las películas PVD suelen tener una mayor tensión de compresión en comparación con las películas CVD, lo que contribuye a su durabilidad.
- Espesor:Los revestimientos de PVD son muy finos, normalmente de 0,5 a 5 micras, pero proporcionan una protección y una mejora significativas del sustrato.
- Dureza:La dureza de los revestimientos PVD es un factor clave en su capacidad para mejorar el límite de fatiga y la resistencia de los sustratos.Por ejemplo, los revestimientos de TiN pueden aumentar el límite de fatiga de la aleación Ti-6Al-4V en un 22%.
-
Ventajas del PVD:
- Deposición a baja temperatura:El PVD puede realizarse a temperaturas más bajas que el CVD, por lo que es adecuado para materiales sensibles a la temperatura.
- Mayor resistencia a la oxidación:Los revestimientos de PVD mejoran la resistencia a la oxidación de los sustratos, lo que los hace adecuados para aplicaciones de alta temperatura.
- Reducción de la fricción:Los revestimientos de PVD reducen la fricción, lo que resulta beneficioso en aplicaciones mecánicas e industriales.
- Resistencia a la corrosión:Los revestimientos de PVD son muy resistentes a la corrosión, por lo que son ideales para su uso en entornos difíciles.
-
Aplicaciones del PVD:
- Aeroespacial:El PVD se utiliza en la tecnología aeroespacial para mejorar la resistencia de los componentes a las altas temperaturas y a la ablación.
- Recubrimientos decorativos:El PVD es muy adecuado para aplicaciones decorativas, como revestimientos de relojes, joyas y elementos arquitectónicos.
- Recubrimientos de vidrio:El PVD se utiliza para aplicar al vidrio capas finas y duraderas que mejoran sus propiedades y su aspecto.
- Capas de barrera de difusión:Los revestimientos PVD se utilizan como barreras de difusión en componentes electrónicos para evitar la migración de materiales.
-
Comparación con CVD:
- Los revestimientos PVD suelen ser más resistentes al desgaste y presentan una mayor tensión de compresión en comparación con los revestimientos CVD.
- El PVD puede depositarse a temperaturas más bajas, lo que resulta ventajoso para sustratos que no pueden soportar altas temperaturas.
-
Replicación del acabado original:
- Los revestimientos PVD pueden reproducir el acabado original de los materiales con un esfuerzo mínimo, lo que los hace ideales para aplicaciones en las que la estética es importante.
En resumen, el PVD es una técnica versátil y eficaz para depositar revestimientos finos, duraderos y de alto rendimiento sobre diversos sustratos.Su capacidad para mejorar propiedades como la dureza, la resistencia al desgaste y la resistencia a la corrosión lo convierten en un proceso valioso en sectores que van desde el aeroespacial hasta las aplicaciones decorativas.
Tabla resumen:
Aspecto | Detalles |
---|---|
Definición | El depósito físico en fase vapor (PVD) deposita películas finas en un entorno de vacío. |
Materiales | Titanio, cromo, aluminio y sus compuestos (por ejemplo, TiN, CrN). |
Propiedades | Resistencia al desgaste, tensión de compresión, revestimientos finos (0,5-5 µm), alta dureza. |
Ventajas | Deposición a baja temperatura, resistencia a la oxidación, reducción de la fricción. |
Aplicaciones | Aeroespacial, revestimientos decorativos, tratamientos del vidrio, barreras de difusión. |
Comparación con CVD | Mayor resistencia al desgaste, mayor tensión de compresión, menor temperatura de deposición. |
¿Está listo para explorar cómo el PVD puede mejorar sus materiales? Póngase en contacto con nosotros para recibir asesoramiento experto.