La rotura del crisol es un problema común que puede perturbar considerablemente las operaciones y aumentar los costes. Las principales razones de la rotura de crisoles están relacionadas con una gestión inadecuada de la temperatura durante los procesos de calentamiento y enfriamiento. En concreto, los principales culpables son los niveles incorrectos de rampa/remojo y las interrupciones bruscas del suministro eléctrico o los tiempos insuficientes de rampa descendente tras la deposición. Estos problemas provocan una rápida solidificación de la masa fundida, lo que provoca tensiones térmicas en el revestimiento del crisol y, en última instancia, su rotura. Además, la selección del crisol adecuado para su aplicación específica es crucial, ya que factores como el tipo de horno, la composición de la aleación, las temperaturas de fusión y los requisitos operativos desempeñan un papel importante a la hora de garantizar la longevidad del crisol.
Explicación de los puntos clave:
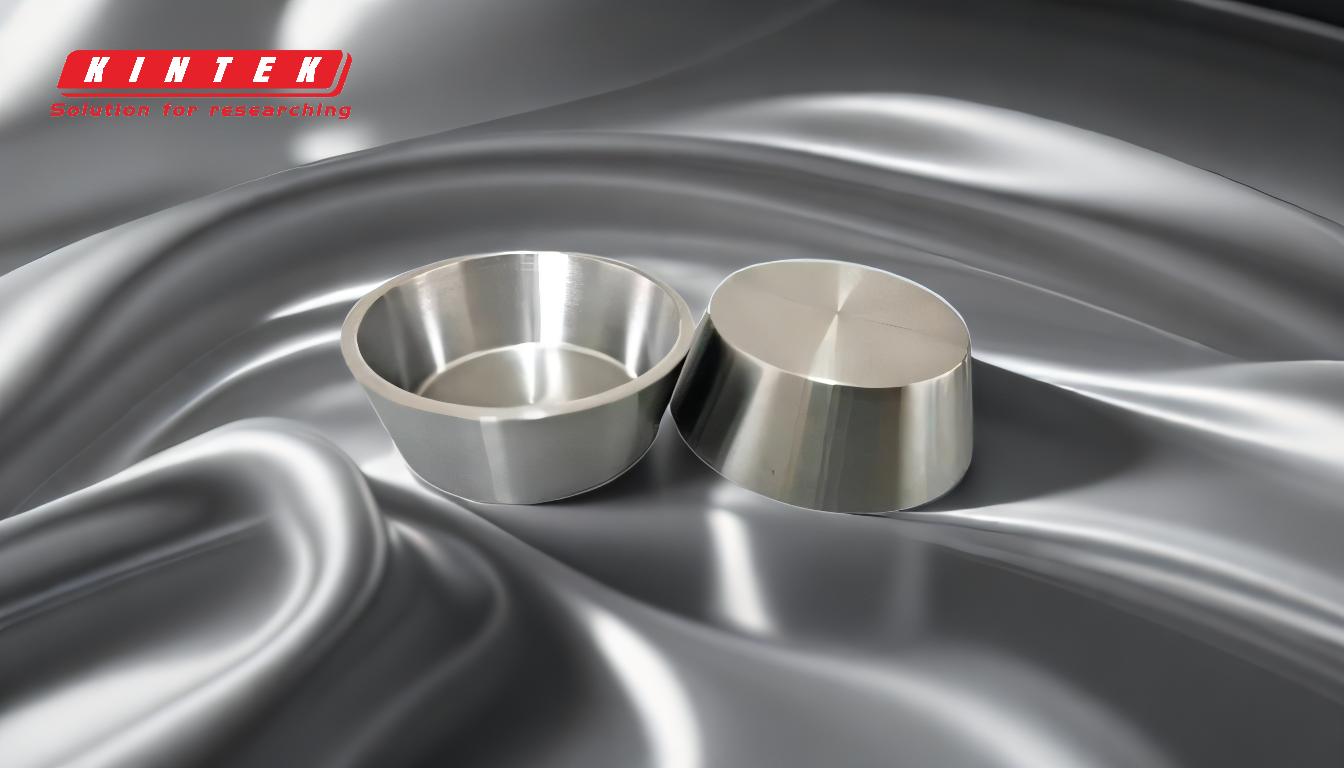
-
Niveles de rampa/remojo incorrectos:
- Explicación: Los niveles de rampa/remojo se refieren a la velocidad a la que aumenta la temperatura (rampa) y a la duración a la que se mantiene a una temperatura específica (remojo). Si estos niveles no están optimizados para el material que se está fundiendo, puede producirse un calentamiento o enfriamiento desigual, causando estrés térmico en el crisol.
- Impacto: La dilatación y contracción térmicas desiguales pueden crear microfisuras en el material del crisol, que con el tiempo pueden provocar su rotura completa. Esto es especialmente crítico en aplicaciones de alta temperatura en las que el crisol está sometido a ciclos térmicos extremos.
-
Apagado incorrecto de la fuente de alimentación o tiempo de rampa de descenso corto:
- Explicación: El corte brusco de la alimentación eléctrica o un tiempo de rampa descendente muy corto después de la deposición provocan una solidificación rápida del material fundido. Esta rápida solidificación puede crear tensiones internas en el crisol.
- Impacto: El enfriamiento rápido puede hacer que el revestimiento del crisol se contraiga de forma desigual, provocando grietas o incluso un fallo catastrófico. Esto es especialmente problemático en procesos en los que el crisol se somete repetidamente a tales choques térmicos.
-
Selección del crisol:
- Explicación: Seleccionar el crisol adecuado es fundamental para evitar roturas. Entre los factores a tener en cuenta se incluyen la capacidad y las dimensiones del horno, el tipo de aleación que se va a fundir, las temperaturas de fusión y mantenimiento, las velocidades de cambio de temperatura y los requisitos operativos específicos.
- Impacto: Un crisol que no esté adaptado a la aplicación específica puede provocar un fallo prematuro. Por ejemplo, un crisol diseñado para temperaturas más bajas puede no soportar las tensiones térmicas de un proceso a alta temperatura, lo que provocaría su rotura.
-
Prácticas operativas:
- Explicación: La forma en que se carga el crisol, el uso de fundentes o aditivos, los procesos de desgasificación o refinado, los métodos de eliminación de escorias y la forma en que se vacía el crisol influyen en su longevidad.
- Impacto: Una carga incorrecta puede provocar un calentamiento desigual, mientras que un fundente agresivo o la eliminación de escoria pueden erosionar el revestimiento del crisol. Asegurarse de que estos procesos se llevan a cabo correctamente puede prolongar considerablemente la vida útil del crisol.
-
Evitar la contaminación cruzada de las aleaciones:
- Explicación: En algunas aplicaciones, es crucial evitar la contaminación cruzada entre diferentes aleaciones. Esto puede requerir el uso de crisoles específicos para aleaciones concretas.
- Impacto: La contaminación cruzada puede provocar reacciones químicas que debiliten el material del crisol, haciéndolo más susceptible a la rotura. El uso de crisoles específicos para aleaciones concretas puede mitigar este riesgo.
-
Gestión del estrés térmico:
- Explicación: La gestión del estrés térmico es clave para evitar la rotura del crisol. Esto incluye optimizar los ciclos de calentamiento y enfriamiento para minimizar el choque térmico.
- Impacto: Una gestión adecuada del estrés térmico puede reducir significativamente la probabilidad de rotura del crisol, garantizando una vida útil más larga y un funcionamiento más fiable.
-
Compatibilidad de materiales:
- Explicación: El material del crisol debe ser compatible con la aleación que se funde. Los distintos materiales tienen propiedades térmicas y químicas diferentes, y utilizar un material incompatible puede provocar fallos prematuros.
- Impacto: Por ejemplo, un crisol de grafito puede ser adecuado para fundir determinadas aleaciones, pero podría reaccionar con otras, provocando su erosión o rotura. Garantizar la compatibilidad de los materiales es esencial para la longevidad del crisol.
-
Mantenimiento e inspección periódicos:
- Explicación: El mantenimiento y la inspección periódicos del crisol pueden ayudar a identificar posibles problemas antes de que provoquen una rotura.
- Impacto: Las grietas o la erosión pueden detectarse a tiempo, lo que permite sustituirlas o repararlas a tiempo. Este enfoque proactivo puede evitar fallos inesperados y reducir el tiempo de inactividad.
Si se tienen en cuenta estos puntos clave, se puede reducir significativamente la probabilidad de rotura del crisol, garantizando unas operaciones más fiables y rentables.
Cuadro recapitulativo:
Causa | Explicación | Impacto |
---|---|---|
Niveles de rampa/remojo incorrectos | Calentamiento o enfriamiento desigual debido a un control inadecuado de la temperatura. | Microfisuras y eventuales roturas debidas al estrés térmico. |
Apagado incorrecto de la fuente de alimentación | Solidificación rápida a partir de paradas bruscas o tiempos cortos de rampa descendente. | Contracción desigual que provoca grietas o fallos catastróficos. |
Mala selección del crisol | Utilización de un crisol inadecuado para la aplicación (por ejemplo, material o tamaño incorrectos). | Fallo prematuro bajo tensión térmica o química. |
Prácticas operativas ineficaces | Carga, fundido o eliminación de escoria inadecuados. | Erosión y calentamiento desigual, lo que reduce la vida útil del crisol. |
Contaminación cruzada de aleaciones | Reacciones químicas derivadas de la mezcla de aleaciones incompatibles. | Debilitamiento del material del crisol, aumentando el riesgo de rotura. |
Gestión inadecuada del estrés térmico | No se optimizan los ciclos de calefacción y refrigeración. | Mayor riesgo de choque térmico y rotura. |
Incompatibilidad de materiales | Utilización de materiales de crisol que reaccionan con la aleación. | Erosión o rotura debidas a reacciones químicas. |
Falta de mantenimiento | Omitir las inspecciones y el mantenimiento periódicos. | Grietas o erosión no detectadas que provocan fallos inesperados. |
Evite la rotura del crisol y optimice sus operaciones- contacte hoy mismo con nuestros expertos soluciones a medida