Conceptos básicos del prensado isostático en frío
Tabla de contenido
- Conceptos básicos del prensado isostático en frío
- Tipos de prensado isostático en frío
- CIP frente a otras técnicas
- Proceso de prensado isostático en frío
- Ventajas y desventajas del CIP para cerámicas de alúmina
- Aplicaciones del prensado isostático en frío
- Comparación con otras tecnologías de compresión
Definición y finalidad del prensado isostático en frío (CIP)
El prensado isostático en frío (CIP) es un método de procesamiento de materiales mediante la compactación de polvos mediante la aplicación de presión uniforme desde todas las direcciones. Este proceso se basa en la ley de Pascal, que establece que la presión aplicada en un fluido encerrado se transmite por igual en todas las direcciones.
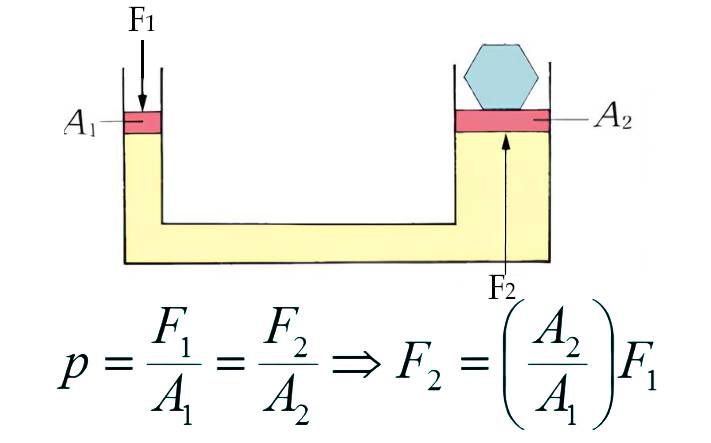
CIP implica encerrar el polvo en un molde de elastómero y aplicar presión líquida para comprimirlo. El resultado es un material sólido muy compacto. CIP se puede utilizar para una amplia gama de materiales como plásticos, grafito, cerámica, metalurgia en polvo y objetivos de pulverización catódica.
Diferenciación entre prensado isostático de bolsa húmeda y bolsa seca
Hay dos tipos de prensado isostático en frío: prensado isostático en bolsa húmeda y prensado isostático en bolsa seca.
En el prensado isostático de bolsa húmeda, el polvo se encierra en una funda de goma y se sumerge en un líquido que transmite la presión de manera uniforme al polvo. Este método se utiliza para producción de bajo volumen, creación de prototipos e investigación y desarrollo.
En el prensado isostático de bolsa seca, el molde de elastómero es una parte integral de la prensa isostática. La presión aplicada es principalmente biaxial y este método es adecuado para producción de gran volumen.
Papel de la calidad del polvo y el diseño de herramientas en CIP
La calidad del polvo y el diseño de las herramientas desempeñan papeles cruciales en el éxito del prensado isostático en frío.
La calidad del polvo utilizado afecta la densidad y resistencia del producto final. En CIP se utilizan comúnmente polvos con bajo o nulo contenido de cera. Además, las tolerancias dimensionales de las piezas producidas por CIP son relativamente grandes, por lo que el control del tamaño y la forma puede no ser tan crítico como en otros métodos de prensado.
El diseño de herramientas también es importante en CIP. Se utilizan moldes de elastómero hechos de materiales como uretano, caucho o cloruro de polivinilo. La elección del material y el diseño del molde afecta la exactitud y precisión del producto final.
Concepto y beneficios del prensado isostático
El prensado isostático, incluido el prensado isostático en frío, ofrece varias ventajas en el procesamiento de materiales.
Un beneficio importante es la capacidad de lograr una compactación uniforme y una mayor capacidad de forma en comparación con el prensado uniaxial. El prensado isostático aplica presión desde múltiples direcciones, lo que da como resultado piezas de alta calidad con mayor densidad.
El prensado isostático también es adecuado para formar formas complicadas que no se pueden comprimir con otros métodos. El uso de moldes de elastómero permite flexibilidad y versatilidad a la hora de dar forma a los materiales.
En resumen, el prensado isostático en frío es un método valioso para dar forma y compactar polvos. Ofrece ventajas únicas en términos de uniformidad, capacidad de forma y versatilidad. Al comprender los conceptos básicos de CIP y sus aplicaciones, las empresas pueden aprovechar este proceso para producir componentes de alta calidad para diversas industrias.
Tipos de prensado isostático en frío
Técnica de bolsa húmeda de CIP
El prensado isostático en frío (CIP) es un método común utilizado para compactar materiales en polvo en una masa sólida homogénea antes del mecanizado o sinterización. La técnica de bolsa húmeda es un subtipo de CIP en el que el polvo crudo se introduce en moldes flexibles que se sumergen en agua u otros líquidos. Luego se aplica presión isostática para comprimir el polvo en la forma deseada. Este proceso permite la producción de componentes complejos e incluso puede utilizarse para prensar lingotes de tungsteno que pesen hasta 1 tonelada.
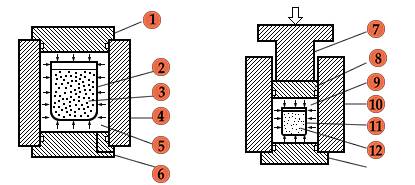
Prensado de bolsas secas y su aplicación.
Otro subtipo de CIP es el prensado en bolsa seca, que se utiliza para formas simples. En este proceso, el molde lleno de polvo se sella y se produce la compresión entre el molde y el recipiente a presión. El prensado de bolsas secas es más adecuado para la producción de grandes volúmenes de formas relativamente simples y puede automatizarse para aumentar la eficiencia.

Comparación de la producción de formas complejas entre CIP y prensado uniaxial.
Al comparar el prensado isostático en frío (CIP) con el prensado con matriz uniaxial, es evidente que el CIP permite la producción de formas más complejas. El prensado uniaxial, por otro lado, es adecuado para prensar formas simples con dimensiones fijas, como cilindros o cuadrados. CIP ofrece mayor flexibilidad en forma y tamaño, lo que permite la producción de relaciones de aspecto más largas y una mejor compactación del polvo. Además, CIP no requiere un aglutinante de cera como el prensado uniaxial, lo que elimina la necesidad de operaciones de desparafinado.
Ventajas del CIP sobre el prensado uniaxial
Existen varias ventajas del prensado isostático en frío (CIP) sobre el prensado con matriz uniaxial. En primer lugar, CIP permite la producción de formas más complejas en comparación con el prensado con matriz uniaxial, que se limita a formas simples. En segundo lugar, CIP ofrece propiedades del producto más uniformes, mayor homogeneidad y un control más preciso de las dimensiones del producto terminado. También permite relaciones de aspecto más largas, una mejor densificación del polvo y la capacidad de procesar materiales con diferentes características y formas. Además, CIP reduce los tiempos de ciclo y mejora la productividad.
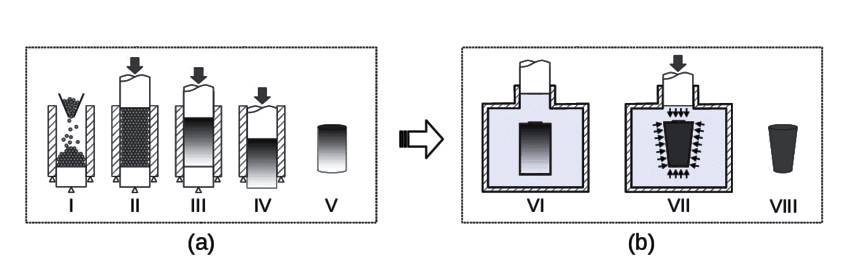
CIP frente a otras técnicas
Comparación de CIP y moldeo por inyección
Cuando se requieren componentes de formas complejas más allá de las capacidades del prensado uniaxial y se necesita un rendimiento de producción de gran volumen, se utilizan dos opciones principales: CIP (prensado isostático en frío) y moldeo por inyección. CIP fue el primer método de alta tecnología reportado en la literatura para fabricar cerámicas de alúmina. En comparación con el prensado con matriz uniaxial, CIP permite formas más complejas y gradientes de presión de prensado muy reducidos, lo que resulta en menos distorsión y agrietamiento. Sin embargo, CIP no es tan común industrialmente como el moldeo por inyección y generalmente solo se usa cuando se requieren formas muy complejas y el moldeo por inyección no es práctico.
Papel del CIP en la fabricación de cerámicas de alúmina
CIP juega un papel crucial en la fabricación de cerámicas de alúmina. Permite la producción de componentes de formas complejas que están más allá de las capacidades de otras técnicas como el prensado uniaxial. La materia prima CIP para cerámicas de alúmina puede ser alúmina Bayer molida simple, alúmina Bayer molida y secada por aspersión o nanopolvos SolGel secados por aspersión de alta tecnología. Algunas de las ventajas clave de CIP para cerámicas de alúmina incluyen la capacidad de producir formas más complejas, gradientes de presión de prensado reducidos, bajo costo de molde para piezas complejas con tiradas de producción pequeñas, sin limitación de tamaño y tiempos de ciclo de procesamiento cortos.
Uso de CIP en la producción de aisladores de bujías.
Los aisladores de bujías son uno de los componentes cerámicos con mayor volumen de producción a nivel mundial fabricados mediante CIP. Aproximadamente 3 mil millones de aisladores de bujías reciben la certificación CIP anualmente. El uso de CIP en la producción de aisladores para bujías demuestra su capacidad para manejar grandes volúmenes de producción y formas complejas. CIP es el pilar de la industria de las bujías y es un proceso de costo relativamente bajo, ideal para formas complejas y grandes tiradas de producción.
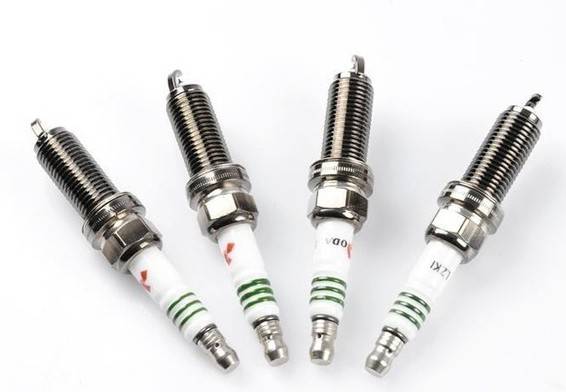
Tipos de materia prima CIP
En la producción de cerámicas de alúmina mediante CIP, se pueden utilizar varios tipos de materia prima. La materia prima comúnmente utilizada incluye alúmina Bayer molida simple, alúmina Bayer molida y secada por aspersión y, en casos raros, nanopolvos SolGel secados por aspersión de alta tecnología. La elección de la materia prima depende de los requisitos específicos del componente cerámico que se produce. La materia prima CIP requiere una excelente fluidez, que generalmente se logra mediante secado por aspersión o vibración del molde durante el llenado.
Ventajas del PIC:
- Son posibles formas más complejas en comparación con el prensado con matriz uniaxial.
- Gradientes de presión de prensado muy reducidos, lo que resulta en menos distorsión y agrietamiento.
- Bajo costo de molde, ideal para piezas complejas con tiradas de producción pequeñas.
- Sin limitación de tamaño, adecuado para componentes muy grandes
- Tiempos de ciclo de procesamiento cortos, no requiere secado ni quemado del aglutinante
Desventajas del CIP:
- Control dimensional limitado en comparación con la compactación con matrices metálicas
- La complejidad de la forma es superior al prensado con matriz uniaxial pero inferior al moldeo por inyección de polvo (PIM)
- Los polvos para CIP requieren una excelente fluidez, que a menudo se logra mediante secado por aspersión.
- Capacidad y capacidad limitadas del buque.
- Proceso comparativamente manual con tasas de producción más bajas en comparación con la compactación con troquel metálico.
CIP es un proceso de estado sólido que ofrece varias ventajas para la producción de componentes metálicos de alto rendimiento. Proporciona una microestructura uniforme, complejidad de formas, bajo costo de herramientas, escalabilidad del proceso y el potencial de producir piezas con una forma casi neta con un desperdicio mínimo de material. Sin embargo, también tiene limitaciones, como estar limitado al procesamiento de ciertos tipos de polvos, capacidad limitada del recipiente y requerir más posprocesamiento en comparación con los procesos que utilizan herramientas rígidas. A pesar de estas limitaciones, CIP sigue siendo una técnica valiosa para la producción en masa de cerámicas avanzadas y la producción de componentes de formas complejas.
Proceso de prensado isostático en frío
Proceso de prensado uniforme en CIP.
El prensado isostático en frío (CIP) es un método de procesamiento de materiales mediante la compactación de polvos encerrados en un molde de elastómero. Luego, el molde se somete uniformemente a la presión del líquido, que comprime los polvos hasta convertirlos en un sólido muy compacto. Este proceso garantiza que la presión se aplique uniformemente en todas las direcciones, lo que da como resultado un producto final homogéneo. CIP se puede utilizar para una variedad de materiales, incluidos plásticos, grafito, cerámica y metalurgia en polvo.
Uso de bolsa blanda o molde para CIP
En CIP, se utiliza un molde de elastómero o una bolsa blanda para encerrar los polvos. Este molde tiene baja resistencia a la deformación, lo que le permite comprimirse fácilmente bajo la presión aplicada. El uso de una bolsa o molde blando asegura que la presión se distribuya uniformemente entre los polvos, lo que da como resultado un producto final uniforme y compacto.
Concepto de post-CIP
Después del proceso CIP, el cuerpo moldeado se somete a un tratamiento post-CIP. Este tratamiento implica un procesamiento adicional o sinterización para lograr la resistencia y las propiedades finales deseadas. Los tratamientos post-CIP pueden variar según el material específico que se esté procesando.
Papel de la cámara de aceite en CIP
En CIP se utiliza una cámara de aceite como medio de presión. La cámara de aceite encierra el molde de elastómero y permite la aplicación de presión líquida. La cámara de aceite juega un papel crucial a la hora de transmitir uniformemente la presión aplicada al molde, asegurando que los polvos se compacten uniformemente.
Ciclos de presurización y despresurización en CIP.
El proceso CIP implica ciclos de presurización y despresurización. Durante el ciclo de presurización, la presión del líquido se aplica al molde de elastómero, comprimiendo los polvos. La presión se mantiene durante un período específico, permitiendo que los polvos se consoliden. Posteriormente comienza el ciclo de despresurización, liberando la presión y permitiendo la recuperación del cuerpo moldeado.
Automatización e implementación a gran escala de CIP.
CIP puede automatizarse e implementarse a gran escala para la producción industrial. La automatización permite un control preciso de los ciclos de presurización y despresurización, garantizando resultados consistentes y de alta calidad. La implementación a gran escala de CIP permite el procesamiento eficiente de un gran volumen de materiales, lo que lo hace adecuado para diversas industrias.
En general, el prensado isostático en frío es un método valioso para procesar materiales, ya que proporciona una compactación uniforme y productos finales de alta calidad. Su uso de un molde de elastómero, una cámara de aceite y ciclos de presurización garantiza resultados consistentes y permite la producción a gran escala. Ya sea para plásticos, cerámica o metalurgia en polvo, CIP ofrece una solución confiable y eficiente para el procesamiento de materiales.
Ventajas y desventajas del CIP para cerámicas de alúmina
Beneficios de CIP en comparación con el prensado con matriz uniaxial y otros métodos de formación de cerámica
Cuando se requieren componentes de formas complejas más allá de las capacidades del prensado uniaxial y se necesita un rendimiento de producción de gran volumen, CIP (prensado isostático en frío) y el moldeo por inyección son las dos opciones principales utilizadas. CIP fue el primer método de alta tecnología reportado en la literatura para fabricar cerámicas de alúmina. Se utiliza comúnmente para la producción en masa de cerámicas avanzadas con formas complejas o componentes cerámicos extremadamente grandes.
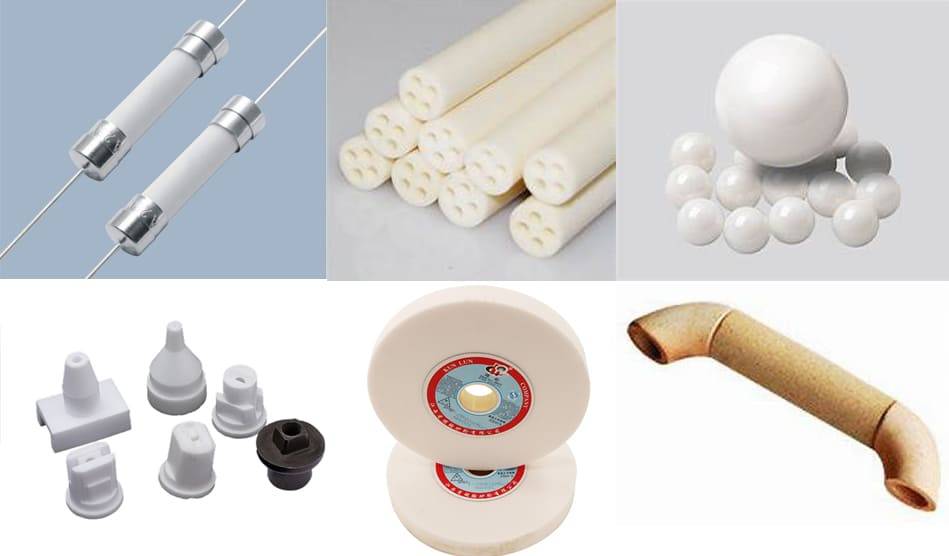
Algunas de las ventajas clave de CIP para cerámicas de alúmina son las siguientes:
Son posibles formas más complejas: CIP permite la producción de componentes con formas complejas que están más allá de las capacidades de forma del prensado con matriz uniaxial.
Gradientes de presión de prensado muy reducidos: CIP ayuda a reducir la distorsión y el agrietamiento aplicando un prensado uniforme desde todas las direcciones en tres dimensiones.
Bajo costo de molde: CIP es ideal para piezas complejas con tiradas de producción pequeñas, ya que requiere un bajo costo de molde.
Sin limitación de tamaño: el CIP no tiene limitación de tamaño, aparte de los límites de la cámara de prensa. Por lo tanto, es ideal para componentes muy grandes, especialmente los de formas complejas. Los componentes que pesan más de 1 tonelada han sido sometidos a CIP.
Tiempos de ciclo de procesamiento cortos: CIP no requiere secado ni quemado del aglutinante, lo que resulta en tiempos de ciclo de procesamiento más cortos.
Limitaciones y desafíos del CIP para cerámica
A pesar de sus ventajas, CIP también presenta algunas limitaciones y desafíos para la cerámica:
Control dimensional limitado: Lograr una alta precisión es problemático en CIP debido a la necesidad de un molde o funda de elastómero muy delgado y uniformemente grueso.
Complejidad de forma inferior a PIM: si bien CIP ofrece una complejidad de forma superior en comparación con el prensado con matriz uniaxial, sigue siendo inferior al moldeo por inyección de polvo (PIM) en términos de complejidad de forma.
Requisitos de fluidez del polvo: Los polvos utilizados en CIP requieren una excelente fluidez, lo que generalmente significa secado por aspersión o vibración del molde durante el llenado.
Comparativamente manual: CIP es un proceso comparativamente manual que requiere un manejo y control cuidadosos.
Limitado al procesamiento de ciertos tipos de polvos: CIP se limita al procesamiento de polvos con excelente fluidez, lo que puede restringir la variedad de materiales que se pueden utilizar.
Capacidad y capacidad del recipiente limitadas: CIP está limitado por la capacidad y capacidad de la cámara de prensa, lo que puede restringir el tamaño de los componentes que se pueden producir.
A pesar de estas limitaciones, CIP sigue siendo un método comúnmente utilizado para la producción en masa de cerámicas avanzadas con formas complejas o grandes tiradas de producción. Es particularmente frecuente en la industria de la alúmina, donde es el pilar de la industria de las bujías y un proceso de costo relativamente bajo, ideal para formas complejas y grandes tiradas de producción. Además de los aisladores de bujías, otros componentes comúnmente sometidos a CIP incluyen componentes de desgaste especiales (como los utilizados en bombas y la industria textil) y aisladores eléctricos.
En general, CIP ofrece ventajas únicas para la producción de cerámicas de alúmina, permitiendo la fabricación de componentes de formas complejas con gradientes de presión reducidos y tiempos de ciclo de procesamiento más cortos. Sin embargo, es importante considerar sus limitaciones y desafíos, como el control dimensional limitado y los requisitos de fluidez del polvo, al decidir el método de formación de cerámica apropiado para una aplicación específica.
Aplicaciones del prensado isostático en frío
Uso común de CIP en la producción de cerámica avanzada
El prensado isostático en frío (CIP) es una tecnología a base de polvo, de forma casi neta, que se utiliza para la producción de componentes metálicos y cerámicos. Si bien se ha utilizado comúnmente para procesar cerámica, los desarrollos recientes en la capacidad de proceso y la metalurgia de polvos han permitido que CIP se utilice cada vez más también en la fabricación de piezas metálicas de alto rendimiento.
Ventajas como el procesamiento de estado sólido, la microestructura uniforme, la complejidad de la forma, el bajo costo de herramientas y la escalabilidad del proceso han convertido al CIP en una ruta de procesamiento viable para metales. Además, el potencial para producir piezas casi en forma con un mínimo desperdicio de material ha hecho que el proceso sea más aceptable en aplicaciones específicas, como la aeroespacial y la automotriz.
Las aplicaciones comunes del prensado isostático en frío incluyen la consolidación de polvos cerámicos, grafito, materiales refractarios, aisladores eléctricos y la compresión de cerámicas avanzadas. Se utilizan habitualmente materiales como nitruro de silicio, carburo de silicio, nitruro de boro, carburo de boro, boruro de titanio y espinela. La tecnología también se está expandiendo a nuevas aplicaciones, como la compresión de objetivos de pulverización catódica, el recubrimiento de componentes de válvulas utilizados para reducir el desgaste de los cilindros en los motores y aplicaciones en las industrias de telecomunicaciones, electrónica, aeroespacial y automotriz.
Papel del CIP en la industria de las bujías y la industria de la alúmina
CIP desempeña un papel importante en la industria de las bujías y la industria de la alúmina. En la industria de las bujías, CIP se utiliza comúnmente para la producción en masa de cerámicas avanzadas con formas complejas o componentes cerámicos extremadamente grandes. No sólo se utiliza para aisladores de bujías, sino también para componentes de desgaste especiales en bombas y la industria textil, así como aisladores eléctricos.
En la industria de la alúmina, CIP se considera el pilar de la industria de las bujías. Es un proceso de costo relativamente bajo que es ideal para formas complejas y grandes tiradas de producción. Esto la convierte en una técnica imprescindible para fabricar bujías de forma eficiente.
En general, el prensado isostático en frío es un proceso probado para la producción de piezas de alto rendimiento en diversas industrias. Su capacidad para lograr altas densidades para cerámica y su versatilidad en el procesamiento tanto de cerámica como de metales la convierten en una técnica valiosa para los fabricantes.
Comparación con otras tecnologías de compresión
Prensado isostático en frío versus prensado isostático en caliente: una descripción general comparativa
En el ámbito del procesamiento de materiales destacan dos poderosas técnicas: el prensado isostático en frío (CIP) y el prensado isostático en caliente (HIP). Si bien ambos métodos comparten el objetivo de mejorar las propiedades del material, lo hacen en condiciones diferentes y cada uno ofrece ventajas únicas. A continuación se ofrece una descripción general comparativa del prensado isostático en frío frente al prensado isostático en caliente:
Prensado isostático en frío (CIP): El prensado isostático en frío, a menudo denominado compactación isostática en frío, implica someter un material a una presión uniforme desde todos los lados. Esto se logra sumergiendo el material en un medio fluido a alta presión y aplicando presión hidráulica. CIP es particularmente eficaz para dar forma y consolidar materiales en polvo, crear formas intrincadas y lograr una alta densidad verde.
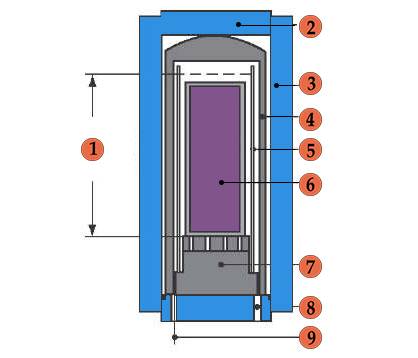
Prensado isostático en caliente (HIP): El prensado isostático en caliente (HIP) es una tecnología de proceso que utiliza alta temperatura y alta presión para someter productos metálicos o cerámicos a una presión igual en todas las direcciones para que las piezas puedan sinterizarse y densificarse. En 2021, la Asociación Norteamericana de Tratamiento Térmico, representante de la industria mundial del tratamiento térmico, clasificó el prensado isostático en caliente, la tecnología de combustión de hidrógeno y la tecnología de fabricación aditiva como las tres tecnologías y procesos más prometedores.
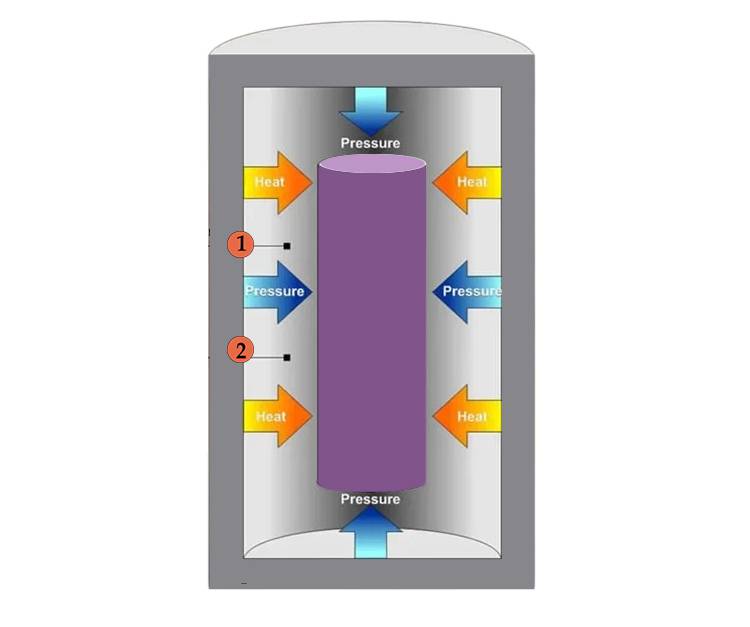
El equipo de prensado isostático en caliente consta de un recipiente de alta presión, un horno de calentamiento, un compresor, una bomba de vacío, un tanque de almacenamiento, un sistema de enfriamiento y un sistema de control por computadora, donde el recipiente de alta presión es el dispositivo clave de todo el equipo.
Desde este punto de vista, la búsqueda de métodos alternativos que se adapten a los avances tecnológicos y a los requisitos tecnológicos no sólo para los sustratos metálicos y cerámicos sino también para los basados en polímeros animó a los investigadores a trabajar en nuevas técnicas y métodos. El “método de deposición de aerosol de polvo cerámico”, como se señala, no solo requiere un tratamiento térmico adicional a alta temperatura o pasos de sinterización, sino también una aplicabilidad homogénea y continua en áreas grandes. Se ha convertido en una tendencia que atrae anualmente la atención de los investigadores sobre tecnologías de materiales semiconductores. Como resultado de todas estas ventajas, se ha considerado que el método de deposición de aerosoles merece ser examinado tanto en términos de sus detalles técnicos como de su aplicabilidad, y debido a que es una tecnología virgen que todavía está abierta al desarrollo en el campo, puede satisfacer la necesidad en tecnologías de semiconductores de nueva generación.
Existe una clara ventaja en el uso del prensado isostático, excepto en el caso del aluminio y el hierro compactados a altas densidades. A altas densidades, tanto la compactación con matriz como la isostática producen densidades verdes similares con polvos de hierro y aluminio. Sin embargo, para materiales como el aluminio que tienen un esfuerzo cortante constante, la presión radial se vuelve aproximadamente igual a la presión axial, es decir, se aproxima a una distribución de presión isostática. Sin embargo, para materiales como el cobre, donde el límite elástico es función del esfuerzo normal en el plano de corte, la presión radial sigue siendo menor que la presión axial. Aunque la distribución de presión dentro de un compacto prensado en frío puede volverse isostática, presumiblemente, la relación presión versus densidad debería ser idéntica a la de la compactación isostática sólo si la distribución de densidad es igualmente uniforme.
En resumen, el prensado isostático en frío y el prensado isostático en caliente representan enfoques distintos para el procesamiento de materiales, cada uno con sus propias ventajas. La decisión entre los dos depende de los objetivos específicos de su proyecto y de las características de los materiales involucrados.
CONTÁCTANOS PARA UNA CONSULTA GRATUITA
Los productos y servicios de KINTEK LAB SOLUTION han sido reconocidos por clientes de todo el mundo. Nuestro personal estará encantado de ayudarle con cualquier consulta que pueda tener. ¡Contáctenos para una consulta gratuita y hable con un especialista del producto para encontrar la solución más adecuada para sus necesidades de aplicación!