Los revestimientos PVD (deposición física de vapor) son famosos por su durabilidad, dureza y resistencia a la corrosión y el desgaste.Estos revestimientos se aplican en un entorno de vacío, lo que garantiza una fuerte unión con el sustrato y evita la contaminación, la oxidación y la degradación.Gracias a su gran dureza, resistencia al desgaste y propiedades de baja fricción, los revestimientos PVD se utilizan ampliamente en sectores como el de la automoción, el aeroespacial y el médico.Su resistencia al deslustre es una ventaja clave, ya que son muy resistentes a la corrosión y la oxidación, incluso en entornos difíciles.La delgadez de los revestimientos (de 0,5 a 5 micras) aumenta aún más su durabilidad y su capacidad para reproducir el acabado original de los materiales.
Explicación de los puntos clave:
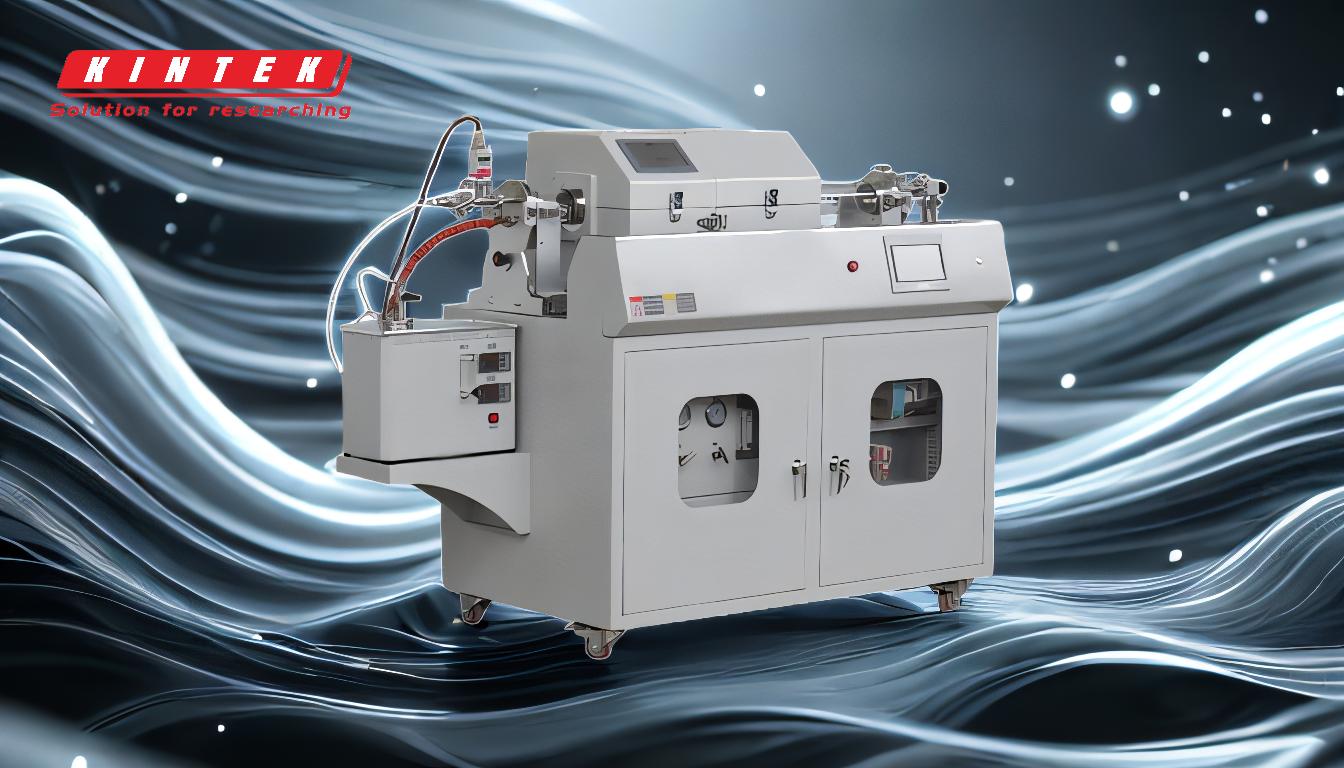
-
Durabilidad y dureza de los revestimientos PVD
- Los revestimientos PVD son conocidos por sus propiedades de superdureza, que los convierten en los revestimientos más duraderos disponibles en la actualidad.
- Su dureza contribuye a su capacidad para resistir el desgaste, los arañazos y la abrasión, que son causas comunes de deslustre en otros materiales.
- La dureza del revestimiento está directamente relacionada con su durabilidad, lo que garantiza que mantenga su aspecto y funcionalidad a lo largo del tiempo.
-
Resistencia a la corrosión y la oxidación
- Los revestimientos PVD son muy resistentes a la corrosión y la oxidación, que son las principales causas del deslustre.
- El entorno de vacío durante el proceso de revestimiento elimina la contaminación y evita la oxidación, garantizando un acabado más duradero.
- Esta resistencia hace que los revestimientos de PVD sean ideales para aplicaciones en entornos difíciles, como entornos marinos o industriales, donde la exposición a la humedad y los productos químicos es habitual.
-
Delgadez y fuerza de adherencia
- Los revestimientos PVD son extremadamente finos, entre 0,5 y 5 micras, lo que les permite reproducir el acabado original de los materiales con un esfuerzo mínimo.
- La delgadez del revestimiento, combinada con su fuerte adherencia al sustrato, dificulta su eliminación y aumenta su durabilidad.
- Esta fuerte unión garantiza que el revestimiento permanezca intacto y resistente al deslustre, incluso bajo tensión mecánica o exposición ambiental.
-
Aplicaciones en industrias exigentes
- Los revestimientos PVD se utilizan ampliamente en industrias como la automoción, la aeroespacial y la médica, donde la durabilidad y la resistencia al deslustre son fundamentales.
- Su gran tolerancia a la temperatura, resistencia al impacto y resistencia a la abrasión los hacen adecuados para aplicaciones exigentes.
- La capacidad de los revestimientos PVD para mantener su aspecto y funcionalidad en estas industrias pone de relieve su resistencia al deslustre.
-
Calidad superior en comparación con los acabados tradicionales
- Los revestimientos PVD ofrecen una calidad y longevidad superiores a las de los acabados tradicionales, que son más propensos a deslustrarse con el tiempo.
- El entorno de vacío durante la aplicación garantiza un revestimiento libre de contaminación, lo que aumenta aún más su resistencia al deslustre.
- Esta calidad superior hace que los revestimientos PVD sean la opción preferida para aplicaciones en las que es esencial mantener un aspecto impecable.
En conclusión, los revestimientos PVD son muy resistentes al deslustre debido a su dureza, resistencia a la corrosión y la oxidación, delgadez y fuerte unión con el sustrato.Estas propiedades los convierten en la opción ideal para aplicaciones en las que la durabilidad y el mantenimiento de un aspecto impecable son fundamentales.
Tabla resumen:
Propiedad | Descripción |
---|---|
Durabilidad y dureza | Los revestimientos de PVD son superduros, resistentes al desgaste, los arañazos y la abrasión. |
Resistencia a la corrosión | Altamente resistente a la oxidación y la corrosión, incluso en entornos agresivos. |
Delgadez y fuerza de adherencia | Extremadamente fino (0,5-5 micras) con una fuerte adherencia al sustrato. |
Aplicaciones | Ampliamente utilizado en las industrias automotriz, aeroespacial y médica por su durabilidad. |
Calidad superior | Supera a los acabados tradicionales con resultados más duraderos y sin contaminación. |
Descubra cómo los revestimientos PVD pueden mejorar la durabilidad de sus productos. póngase en contacto con nosotros ¡!