Los recubrimientos PVD (deposición física de vapor) son conocidos por su delgadez, que normalmente oscila entre 0,02 y 5 micras, y las aplicaciones comunes suelen estar en el rango de 3 a 5 micras. Esta delgadez es una ventaja clave, ya que preserva el filo de las herramientas de corte, reduce las fuerzas de corte y la generación de calor y minimiza el riesgo de daño térmico al sustrato. El proceso opera a temperaturas relativamente bajas (alrededor de 500 °C), lo que evita aún más la distorsión en la mayoría de los materiales. Los recubrimientos PVD se aplican en condiciones de vacío, lo que garantiza una deposición precisa y uniforme, y generan tensión de compresión durante el enfriamiento, lo que ayuda a prevenir la formación y expansión de grietas. Estas características hacen que los recubrimientos PVD sean ideales para aplicaciones de alto rendimiento, como herramientas de corte, recubrimientos ópticos y componentes de precisión.
Puntos clave explicados:
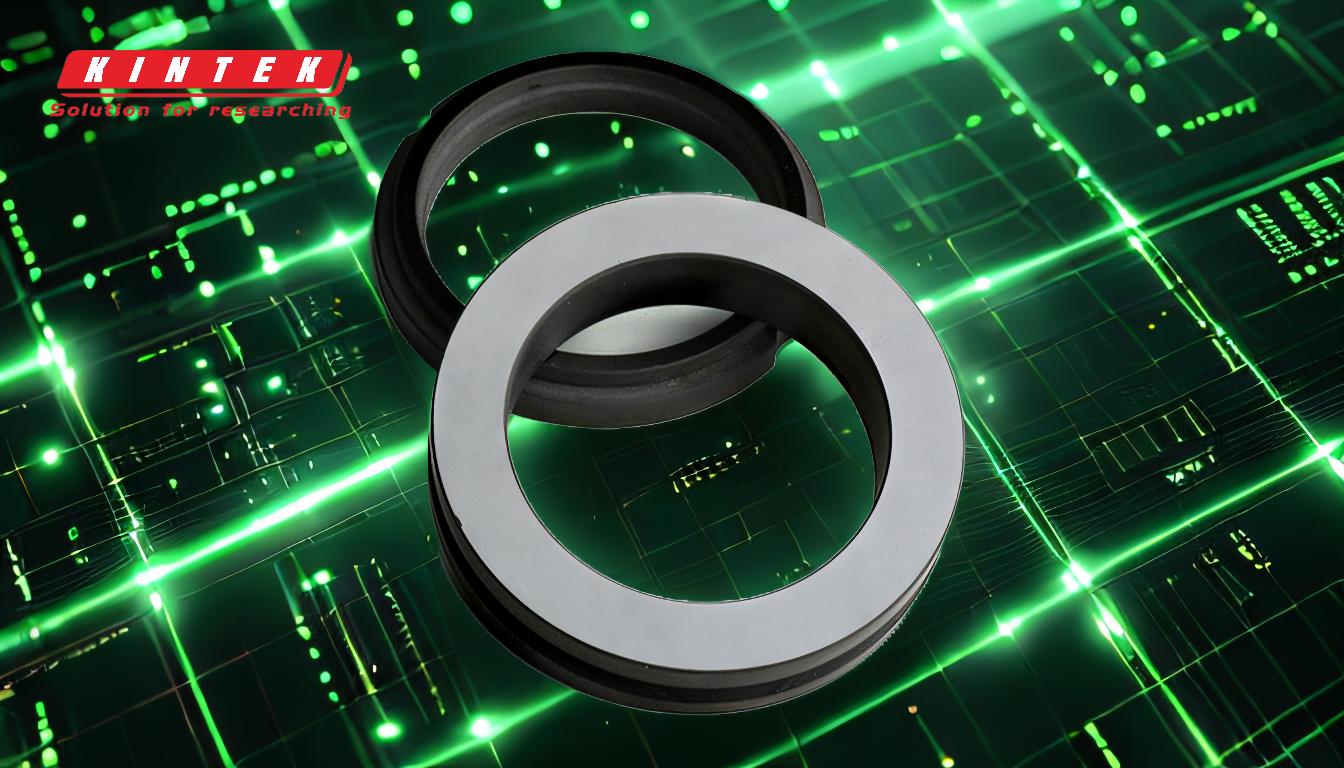
-
Rango de espesor de recubrimientos PVD:
- Los recubrimientos PVD son extremadamente finos y suelen oscilar entre 0,02 a 5 micras . Esta delgadez es una ventaja significativa en aplicaciones donde mantener el filo y la precisión de las herramientas es fundamental.
- En el caso de herramientas de corte, el espesor suele caer en el Rango de 3-5 micras , que es suficiente para mejorar la dureza y la resistencia al desgaste sin comprometer el filo del borde de la herramienta.
-
Ventajas de los recubrimientos finos de PVD:
- Preservación de la nitidez: La delgadez de los recubrimientos PVD garantiza que se mantenga el filo de las herramientas de corte, como las hojas, lo que conduce a un mejor rendimiento y una mayor vida útil de la herramienta.
- Fuerza de corte y calor reducidos: Los recubrimientos finos reducen la fuerza de corte requerida durante el mecanizado, lo que a su vez minimiza la generación de calor y el riesgo de daño térmico al sustrato.
- Formación de tensión compresiva: Durante la fase de enfriamiento, los recubrimientos PVD generan tensión de compresión, lo que ayuda a prevenir la formación de grietas y la expansión, lo que los hace adecuados para aplicaciones exigentes como procesos de corte interrumpidos (por ejemplo, fresado).
-
Deposición a baja temperatura:
- Los recubrimientos PVD se aplican a temperaturas relativamente bajas, normalmente alrededor de 500°C , que es significativamente menor que otros métodos de recubrimiento como CVD (deposición química de vapor). Este proceso a baja temperatura reduce el riesgo de distorsión térmica en el sustrato, lo que lo hace adecuado para una amplia gama de materiales, incluidos los sensibles al calor.
-
Proceso de deposición al vacío:
- El proceso PVD se lleva a cabo bajo condiciones de vacío , lo que asegura que la deposición del material de recubrimiento sea precisa y uniforme. El entorno de vacío también evita la conducción y la convección, permitiendo el transporte térmico únicamente por radiación, lo que contribuye a la alta calidad y consistencia de los recubrimientos.
-
Aplicaciones de recubrimientos finos de PVD:
- Herramientas de corte: Los recubrimientos PVD se utilizan ampliamente en herramientas de corte de carburo y acero de alta velocidad (HSS) debido a su capacidad para mejorar la dureza y la resistencia al desgaste sin comprometer la geometría de la herramienta.
- Componentes de precisión: La naturaleza delgada y uniforme de los recubrimientos PVD los hace ideales para piezas con tolerancias estrictas, como componentes de moldeo por inyección de plástico y herramientas de corte fino.
- Recubrimientos ópticos: La deposición precisa de películas delgadas en PVD lo hace adecuado para aplicaciones ópticas, donde la uniformidad y la delgadez son críticas.
-
Beneficios ambientales:
- El recubrimiento PVD es un respetuoso con el medio ambiente proceso. No produce residuos ni gases nocivos y no altera el valor reciclable de materiales como el acero inoxidable. Esto lo convierte en una opción sostenible para las industrias que buscan reducir su impacto ambiental.
-
Pasos del proceso y características:
- El proceso PVD implica tres pasos principales: (1) vaporización del material de revestimiento, (2) migración de átomos, moléculas o iones, y (3) declaración de estas partículas sobre el sustrato. Este proceso da como resultado recubrimientos puros y de alta calidad que mejoran la calidad de la superficie al reducir la rugosidad.
-
Versatilidad en la fabricación:
- Las máquinas de recubrimiento PVD son controlado por computadora , lo que permite una alta precisión y la capacidad de manejar tanto la fabricación en gran volumen y a gran escala como la producción en pequeños lotes. Esta versatilidad hace que el recubrimiento PVD sea adecuado para una amplia gama de industrias, desde la automoción hasta la aeroespacial.
En resumen, la delgadez de los recubrimientos PVD, combinada con su deposición a baja temperatura, su precisión basada en el vacío y sus beneficios medioambientales, los convierte en una solución muy eficaz para mejorar el rendimiento y la durabilidad de herramientas y componentes en diversas industrias.
Tabla resumen:
Aspecto | Detalles |
---|---|
Rango de espesor | 0,02 a 5 micrones (común: 3-5 micrones para herramientas de corte) |
Ventajas | Preserva el filo, reduce la fuerza de corte y previene el daño térmico |
Temperatura de deposición | ~500 °C (proceso a baja temperatura) |
Proceso | Basado en vacío, lo que garantiza una deposición precisa y uniforme. |
Aplicaciones | Herramientas de corte, componentes de precisión, recubrimientos ópticos. |
Impacto ambiental | Respetuoso con el medio ambiente, sin residuos ni gases nocivos. |
Mejore sus herramientas con recubrimientos PVD ultrafinos: contáctanos hoy para aprender más!