Crear una atmósfera inerte en un horno implica eliminar gases reactivos como el oxígeno y sustituirlos por gases inertes como el argón o el nitrógeno.Este proceso evita la oxidación y otras reacciones químicas indeseables durante los tratamientos a alta temperatura.Los pasos clave incluyen la creación de un vacío para eliminar el oxígeno y otros gases reactivos, seguido de la purga del horno con gas inerte para establecer un entorno estable y no reactivo.Este método es esencial para aplicaciones como el tratamiento térmico de metales, donde es fundamental mantener la integridad del material y la calidad de la superficie.
Explicación de los puntos clave:
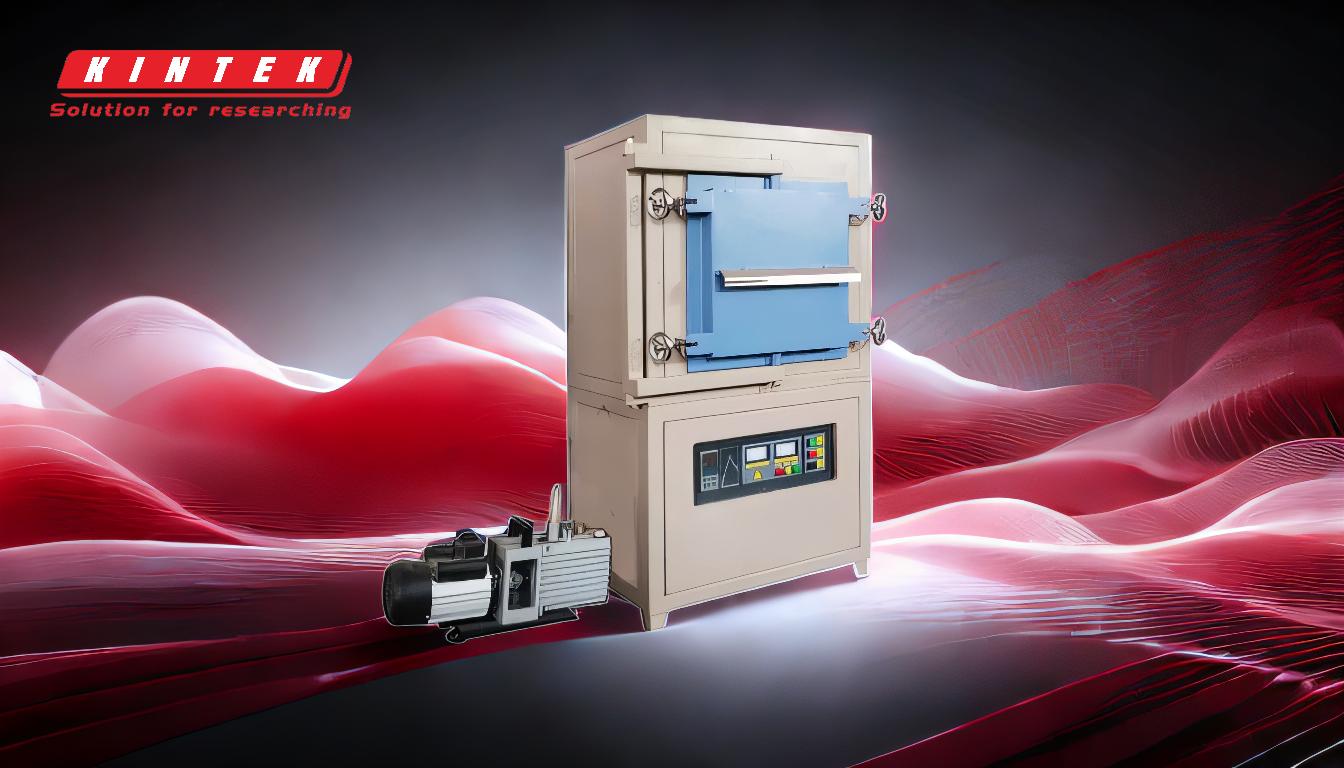
-
Finalidad de una atmósfera inerte:
- Se utiliza una atmósfera inerte para evitar reacciones superficiales como la oxidación, la descarburación o la carburación durante los procesos a alta temperatura.
- Garantiza que materiales como los metales y la cerámica conserven las propiedades y el acabado superficial deseados.
-
Pasos para crear una atmósfera inerte:
-
Crear un vacío:
- Se crea un ligero vacío (hasta 0,1 MPa) en el interior del horno mediante una bomba de vacío rotativa de paletas rellena de aceite.
- Este paso elimina el oxígeno y otros gases reactivos, minimizando el riesgo de reacciones químicas no deseadas.
-
Purga con gas inerte:
- Tras crear el vacío, se introducen en el horno gases inertes como el argón o el nitrógeno.
- Estos gases son químicamente inactivos y crean un entorno protector alrededor del material que se está tratando.
-
Crear un vacío:
-
Selección de gases inertes:
- Argón (Ar) y nitrógeno (N2) son los gases inertes más utilizados debido a su gran abundancia natural y a sus propiedades no reactivas.
- Para aplicaciones específicas gas hidrógeno también puede utilizarse, pero requiere medidas de seguridad adicionales debido a su naturaleza explosiva.
-
Consideraciones operativas:
-
Limitaciones de temperatura:
- El funcionamiento en atmósfera inerte puede requerir elementos de horno de mayor temperatura o una restricción de la temperatura máxima de funcionamiento para adaptarse a las limitaciones de los elementos calefactores.
-
Medidas de seguridad:
- Cuando se utilizan gases como el hidrógeno, deben aplicarse disposiciones de seguridad a prueba de explosiones para garantizar un funcionamiento seguro.
-
Limitaciones de temperatura:
-
Aplicaciones de las atmósferas inertes:
-
Tratamiento térmico de metales:
- Las atmósferas inertes son fundamentales para procesos como el endurecimiento de aceros con alto contenido en carbono, en los que es esencial mantener una superficie neutra para evitar la descarburación o la carburación.
-
Procesos cerámicos:
- Las atmósferas inertes evitan la oxidación y otras reacciones químicas que podrían degradar la calidad de los materiales cerámicos durante la cocción.
-
Tratamiento térmico de metales:
-
Mantenimiento de la atmósfera inerte:
- La atmósfera inerte se mantiene supervisando y controlando continuamente el flujo de gas para garantizar un entorno estable.
- Para evitar la entrada de gases reactivos, es necesario realizar comprobaciones periódicas para detectar fugas y sellar correctamente el horno.
Siguiendo estos pasos y consideraciones, se puede crear y mantener eficazmente una atmósfera inerte en un horno, garantizando resultados óptimos para procesos a alta temperatura.
Tabla resumen:
Aspecto clave | Detalles |
---|---|
Finalidad | Prevenir la oxidación, la descarburación y la carburación durante el tratamiento térmico. |
Pasos | 1.Crear un vacío para eliminar los gases reactivos.2.Purgar con gas inerte (argón/nitrógeno). |
Gases inertes comunes | Argón (Ar), Nitrógeno (N2) o Hidrógeno (H2) con medidas de seguridad. |
Aplicaciones | Tratamiento térmico de metales, procesamiento de cerámica, etc. |
Mantenimiento | Supervise el flujo de gas, compruebe si hay fugas y asegúrese de que el sellado es correcto. |
¿Necesita ayuda para crear una atmósfera inerte para su horno? Póngase en contacto con nuestros expertos para obtener soluciones a medida.