El carburo de silicio (SiC) y la cerámica son dos materiales muy utilizados, pero sirven para fines diferentes y tienen propiedades distintas.El carburo de silicio es un tipo de cerámica avanzada que ofrece un rendimiento superior en entornos de alta temperatura, alta tensión y corrosión.Destaca en aplicaciones que requieren una alta conductividad térmica, resistencia al desgaste y resistencia mecánica, lo que lo convierte en la opción preferida para sectores como el de los semiconductores, el aeroespacial y el energético.La cerámica tradicional, aunque versátil, a menudo carece de la extrema durabilidad y eficacia térmica del carburo de silicio.Sin embargo, la elección entre carburo de silicio y cerámica depende de la aplicación específica, ya que la cerámica puede resultar más rentable o adecuada para entornos menos exigentes.
Explicación de los puntos clave:
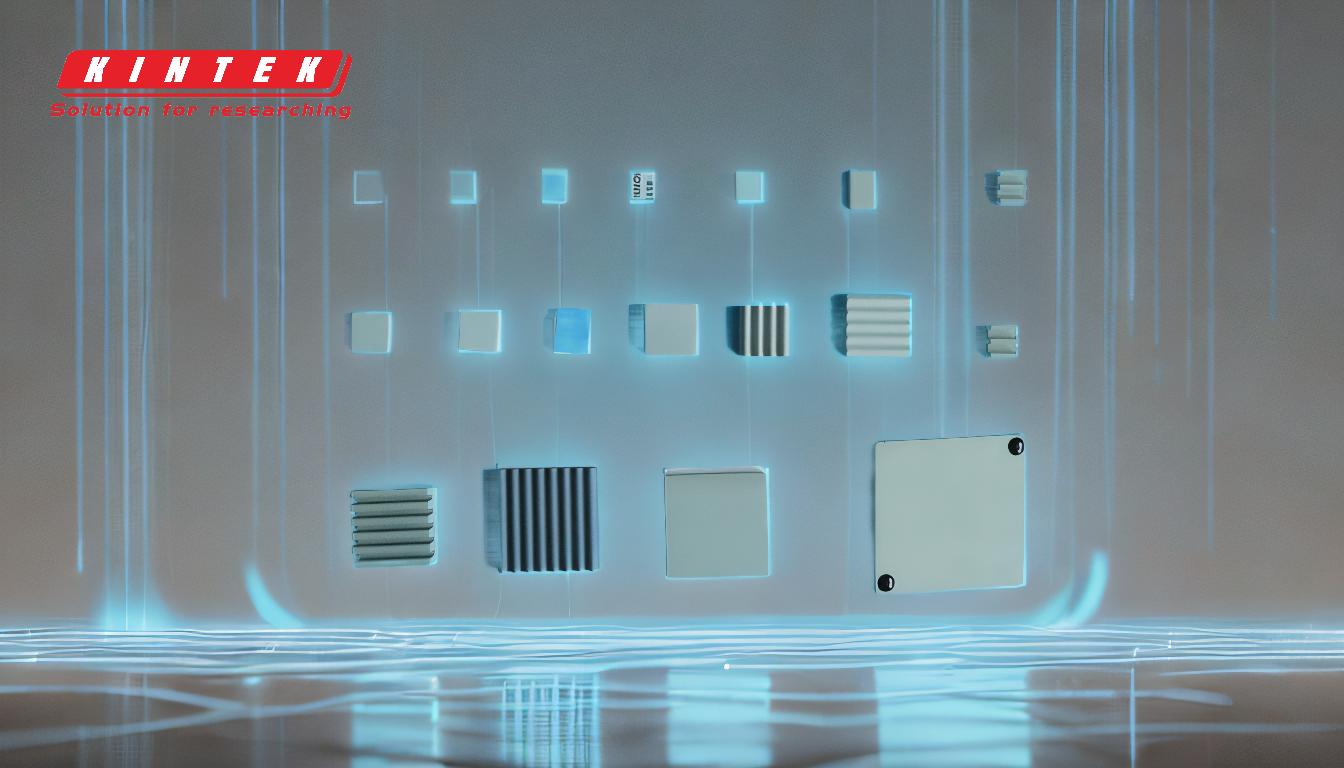
-
Propiedades térmicas y mecánicas:
- El carburo de silicio presenta una excepcional resistencia mecánica a altas temperaturas, una gran dureza y una elevada conductividad térmica.Estas propiedades lo hacen ideal para aplicaciones como muebles de horno boquillas de combustión e intercambiadores de calor.
- Las cerámicas tradicionales pueden no igualar la conductividad térmica o la resistencia al desgaste del carburo de silicio, lo que limita su uso en entornos extremos.
-
Eficacia eléctrica:
- Los elementos calefactores de carburo de silicio convierten el 100% de la electricidad en calor, ofreciendo una mayor eficiencia eléctrica.Esto es especialmente beneficioso en hornos industriales y aplicaciones de calefacción.
- Las cerámicas, aunque son térmicamente estables, pueden no alcanzar el mismo nivel de eficiencia eléctrica, por lo que el carburo de silicio es una mejor opción para los procesos que consumen mucha energía.
-
Resistencia a la corrosión y al desgaste:
- El carburo de silicio es muy resistente a la corrosión, el desgaste y la abrasión, por lo que resulta adecuado para entornos duros como el procesamiento químico, la perforación petrolífera y la fabricación de semiconductores.
- La cerámica tradicional puede degradarse más rápidamente en condiciones similares, requiriendo sustituciones más frecuentes.
-
Versatilidad en las aplicaciones:
- El carburo de silicio se utiliza en una amplia gama de industrias, como la generación de energía, la automoción, la industria aeroespacial y campos de alta tecnología como los semiconductores y la tecnología espacial.
- La cerámica se utiliza más comúnmente en aplicaciones tradicionales como la alfarería, los azulejos y usos industriales menos exigentes.
-
Aspectos económicos:
- Aunque el carburo de silicio ofrece un rendimiento superior, suele ser más caro que la cerámica tradicional.Para aplicaciones en las que no se requiere una durabilidad y eficacia extremas, la cerámica puede ser una opción más rentable.
-
Perspectivas de futuro:
- El carburo de silicio se adopta cada vez más en industrias de alta tecnología y vanguardia, lo que indica su creciente importancia en aplicaciones avanzadas.
- La cerámica tradicional sigue dominando en ámbitos en los que el coste y la facilidad de fabricación priman sobre el rendimiento.
En conclusión, el carburo de silicio suele ser mejor que la cerámica tradicional para las aplicaciones de alto rendimiento que requieren una durabilidad extrema, eficiencia térmica y resistencia a condiciones duras.Sin embargo, la elección entre ambos materiales depende en última instancia de los requisitos específicos de la aplicación, incluidos el coste, las condiciones medioambientales y las necesidades de rendimiento.
Cuadro sinóptico:
Propiedad | Carburo de silicio (SiC) | Cerámica tradicional |
---|---|---|
Conductividad térmica | Alta | Bajo |
Resistencia al desgaste | Excepcional | Moderado |
Resistencia a la corrosión | Muy resistente | Menos resistente |
Eficiencia Eléctrica | 100% de conversión de electricidad en calor | Menor eficiencia |
Coste | Mayor | Más rentable |
Aplicaciones | Semiconductores, aeroespacial, energía | Cerámica, azulejos, usos menos exigentes |
¿Aún no sabe qué material se adapta mejor a sus necesidades? Póngase en contacto con nuestros expertos para un asesoramiento personalizado.