El depósito físico en fase vapor (PVD) es un sofisticado proceso de revestimiento utilizado para depositar finas películas de material sobre un sustrato.El proceso consiste en convertir un material sólido en una fase de vapor, transportarlo a través de un vacío o un entorno de baja presión y, a continuación, condensarlo sobre el sustrato para formar un revestimiento fino, duradero y, a menudo, funcional.El PVD se utiliza ampliamente en industrias como la electrónica, la óptica y la fabricación para crear revestimientos resistentes a la corrosión, al desgaste y decorativos.El proceso se lleva a cabo en un entorno controlado, normalmente con cámaras de vacío, y emplea métodos como la pulverización catódica, la evaporación o la descarga de arco para conseguir las propiedades de revestimiento deseadas.
Explicación de los puntos clave:
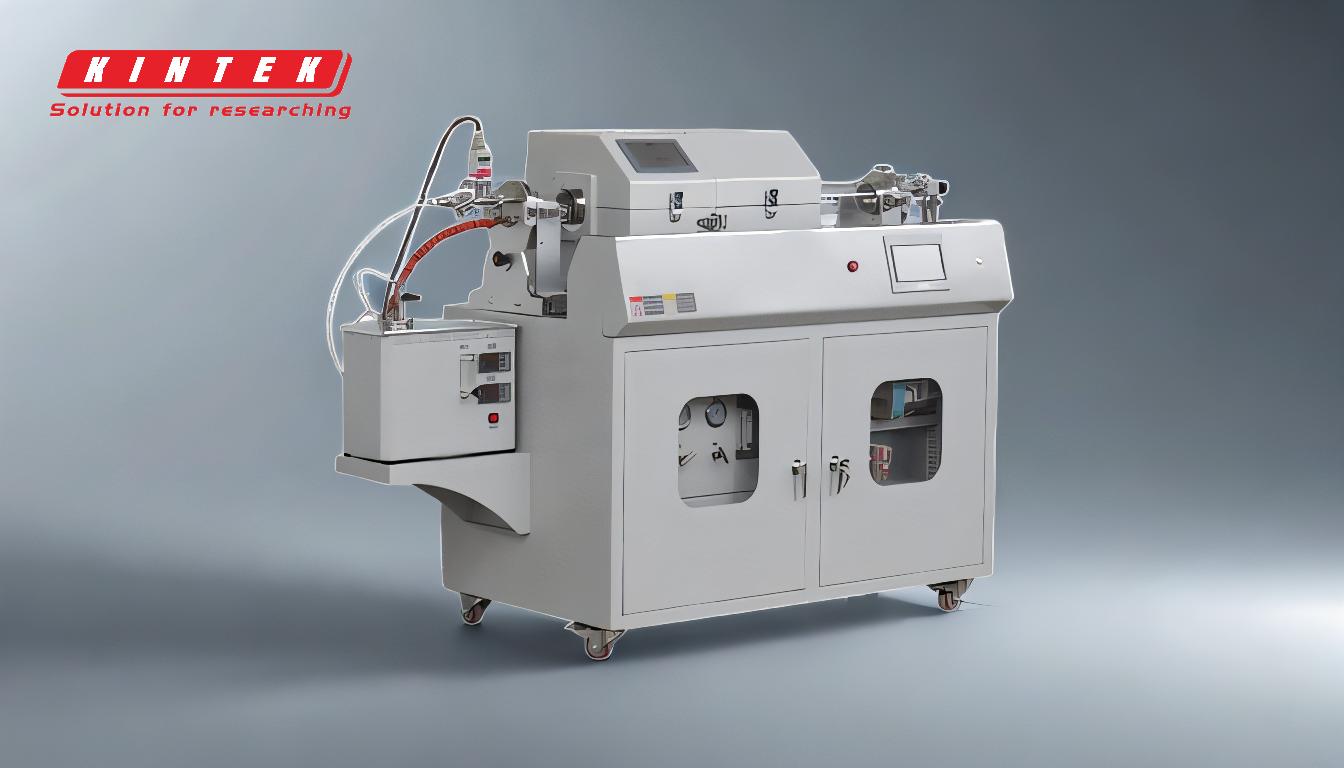
-
Gasificación del material de revestimiento:
-
El primer paso del PVD consiste en convertir el material de revestimiento sólido (blanco) en una fase de vapor.Esto se consigue mediante métodos como
- Evaporación térmica:Calentamiento del material hasta su evaporación.
- Pulverización catódica:Bombardeo del objetivo con iones de alta energía para desprender los átomos.
- Descarga de arco:Utilización de un arco eléctrico para vaporizar el material.
- Rayo láser o haz de electrones:Se utilizan haces de energía focalizados para vaporizar el material objetivo.
- La elección del método depende de las propiedades del material y de las características deseadas del revestimiento.
-
El primer paso del PVD consiste en convertir el material de revestimiento sólido (blanco) en una fase de vapor.Esto se consigue mediante métodos como
-
Migración de átomos, moléculas o iones de revestimiento:
-
Una vez gasificados, los átomos, moléculas o iones del material de revestimiento se desplazan por la cámara de reacción.Este paso implica
- Colisiones y Reacciones:Las partículas vaporizadas pueden chocar con otras partículas o gases de fondo, dando lugar a reacciones que pueden modificar sus propiedades.
- Deposición en la línea de visión:Las partículas se desplazan en línea recta y se depositan sobre el sustrato, garantizando un revestimiento preciso y controlado.
- En el proceso de migración influyen el nivel de vacío, la temperatura y la presión dentro de la cámara.
-
Una vez gasificados, los átomos, moléculas o iones del material de revestimiento se desplazan por la cámara de reacción.Este paso implica
-
Deposición sobre el sustrato:
-
El último paso consiste en la condensación del material vaporizado sobre el sustrato para formar una fina película.Los aspectos clave son:
- Adhesión:El material de revestimiento se adhiere fuertemente al sustrato, garantizando su durabilidad.
- Control del espesor:El espesor del revestimiento se controla mediante un monitor de velocidad de cristal de cuarzo, que mide la velocidad de deposición y garantiza la uniformidad.
- Propiedades del revestimiento:La película resultante puede tener propiedades como alta dureza, resistencia a la corrosión y estabilidad térmica, dependiendo del material y de los parámetros del proceso.
-
El último paso consiste en la condensación del material vaporizado sobre el sustrato para formar una fina película.Los aspectos clave son:
-
Entorno de vacío:
-
El PVD se realiza en una cámara de vacío o de baja presión para minimizar la contaminación y las reacciones químicas no deseadas.El entorno de vacío
- Reduce la presencia de gases de fondo que podrían interferir en el proceso de deposición.
- Mejora la pureza y la calidad del revestimiento.
- Permite un control preciso del proceso de deposición.
-
El PVD se realiza en una cámara de vacío o de baja presión para minimizar la contaminación y las reacciones químicas no deseadas.El entorno de vacío
-
Aplicaciones del PVD:
-
El PVD se utiliza en una amplia gama de industrias debido a su capacidad para producir revestimientos funcionales de alta calidad.Entre las aplicaciones más comunes se incluyen:
- Electrónica:Películas finas para semiconductores y microelectrónica.
- Óptica:Revestimientos antirreflejos y protectores para lentes y espejos.
- Fabricación:Recubrimientos resistentes al desgaste y a la corrosión para herramientas y componentes.
- Recubrimientos decorativos:Acabados duraderos y estéticamente agradables para productos de consumo.
-
El PVD se utiliza en una amplia gama de industrias debido a su capacidad para producir revestimientos funcionales de alta calidad.Entre las aplicaciones más comunes se incluyen:
-
Ventajas del PVD:
- Durabilidad:Los revestimientos de PVD son muy duraderos y resistentes al desgaste, la corrosión y las altas temperaturas.
- Precisión:El proceso permite un control preciso del espesor y la composición de la película.
- Versatilidad:El PVD puede utilizarse con una amplia gama de materiales y sustratos.
- Respetuoso con el medio ambiente:El PVD es un proceso limpio que produce un mínimo de residuos y en el que no intervienen productos químicos nocivos.
-
Limitaciones del PVD:
- Coste:El equipo y el proceso pueden ser caros, especialmente para aplicaciones a gran escala.
- Complejidad:El proceso requiere equipos y conocimientos especializados.
- Limitación de la línea de visión:El revestimiento sólo se aplica a las superficies directamente expuestas al material vaporizado, lo que puede limitar su uso para geometrías complejas.
En resumen, el PVD es una tecnología de revestimiento versátil y precisa que implica la vaporización de un material sólido, su transporte en un entorno de vacío y su deposición sobre un sustrato para formar una película fina y funcional.El proceso se utiliza ampliamente en diversas industrias debido a su capacidad para producir revestimientos duraderos y de alto rendimiento con una excelente adherencia y uniformidad.
Tabla resumen:
Aspecto | Detalles |
---|---|
Proceso | Convierte el material sólido en vapor, lo transporta en vacío, lo deposita sobre el sustrato. |
Métodos | Evaporación térmica, pulverización catódica, descarga de arco, láser/rayo electrónico. |
Pasos clave | Gasificación, migración, deposición. |
Aplicaciones | Electrónica, óptica, fabricación, revestimientos decorativos. |
Ventajas | Durabilidad, precisión, versatilidad, respetuoso con el medio ambiente. |
Limitaciones | Coste elevado, complejidad, limitación de la línea de visión. |
Descubra cómo el PVD puede mejorar sus productos póngase en contacto para recibir asesoramiento experto.