La sinterización del óxido de circonio es un proceso crítico en la producción de materiales cerámicos de alto rendimiento, pero plantea varios retos.Entre ellos figuran los relacionados con el choque térmico, las propiedades de los materiales y el diseño del equipo de sinterización.Comprender estos problemas es esencial para optimizar el proceso de sinterización y garantizar la calidad y durabilidad del producto final.
Explicación de los puntos clave:
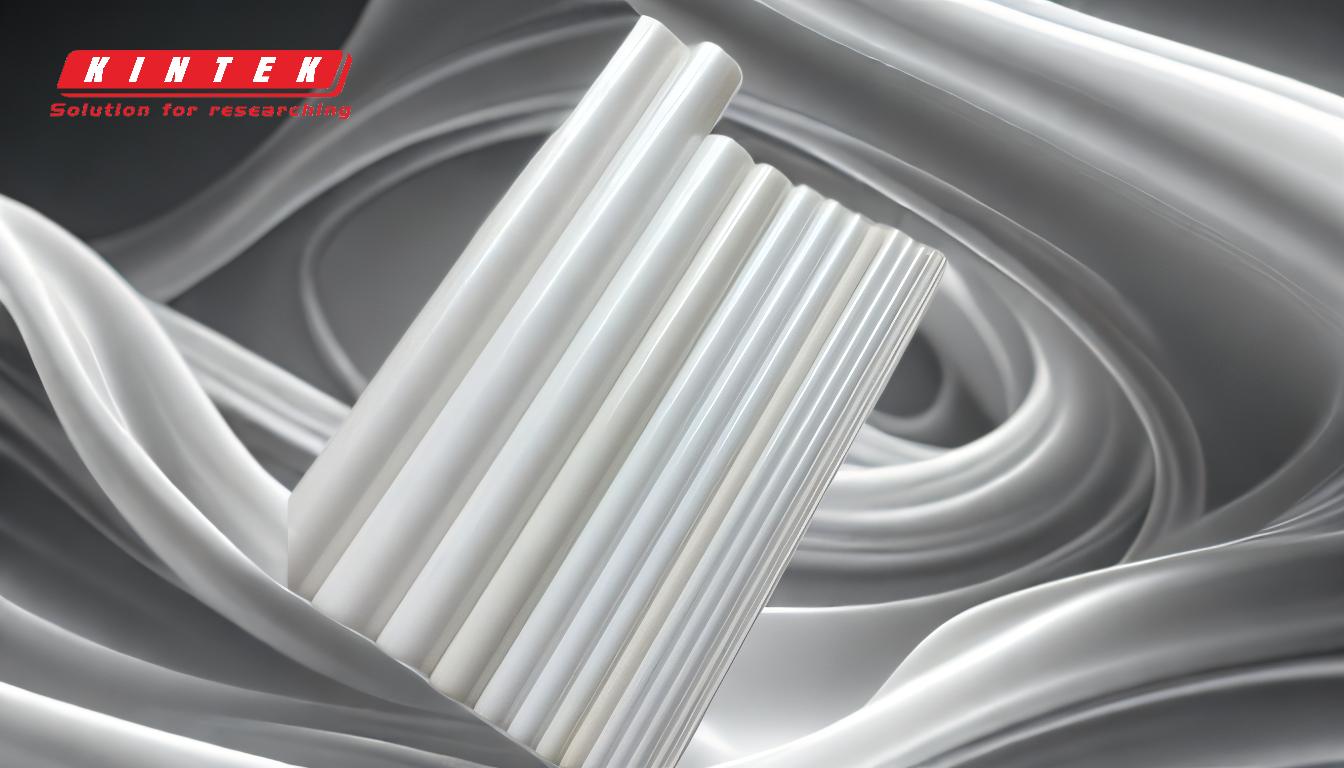
-
Resistencia al choque térmico:
- Problema:Durante el proceso de sinterización, las piezas de óxido de circonio están sometidas a rápidos cambios de temperatura, especialmente cuando se enfrían inmediatamente después de la sinterización.Esto puede provocar un choque térmico que cause grietas o fallos en el material.
- Solución:Para mitigarlo, es crucial utilizar materiales y diseños que puedan soportar fuertes cargas de choque térmico.Por ejemplo, las placas de empuje en horno de sinterización de óxido de circonio debe fabricarse con materiales que combinen de forma equilibrada las propiedades térmicas, mecánicas y químicas.A menudo se utiliza alúmina de gran pureza sin sílice, pero debe seleccionarse cuidadosamente para evitar fallos durante los ciclos térmicos.
-
Propiedades del material:
- Problema:Las propiedades del propio material de circonio, como su pureza y composición, pueden afectar significativamente al proceso de sinterización.Las impurezas o composiciones incorrectas pueden provocar defectos en el producto final.
- Solución:Garantizar el uso de polvos de circonio de gran pureza y mantener un control estricto sobre la composición del material puede ayudar a conseguir un producto sinterizado uniforme y sin defectos.Esto incluye una cuidadosa selección de las materias primas y rigurosas medidas de control de calidad.
-
Diseño del horno de sinterización:
- Problema:El diseño del horno de sinterización desempeña un papel crucial en el éxito del proceso de sinterización.Un diseño inadecuado del horno puede provocar un calentamiento desigual, un control deficiente de la temperatura y una sinterización ineficaz.
- Solución:Es esencial invertir en hornos de sinterización bien diseñados que ofrezcan un control preciso de la temperatura y un calentamiento uniforme.Los hornos modernos suelen incorporar funciones avanzadas como perfiles de temperatura programables y supervisión en tiempo real para garantizar unas condiciones de sinterización óptimas.
-
Parámetros del proceso:
- Problema:Unos parámetros de sinterización incorrectos, como la temperatura, la velocidad de calentamiento y el tiempo de mantenimiento, pueden provocar una sinterización incompleta o un exceso de sinterización, con las consiguientes propiedades deficientes del material.
- Solución:La optimización de los parámetros de sinterización en función de los requisitos específicos del material de óxido de circonio es crucial.Esto implica realizar pruebas y experimentos exhaustivos para determinar los mejores ajustes para conseguir las propiedades deseadas del material.
-
Tratamiento posterior al sinterizado:
- Problema:El tratamiento de las piezas de óxido de circonio tras la sinterización, como la velocidad de enfriamiento y el enfriamiento rápido, puede influir en las propiedades finales del material.Un enfriamiento rápido puede introducir tensiones y defectos.
- Solución:Aplicar procesos de enfriamiento controlados y evitar el enfriamiento rápido puede ayudar a reducir las tensiones térmicas y mejorar la calidad general de las piezas sinterizadas.A menudo se recomiendan procesos de enfriamiento gradual y recocido.
Si se tienen en cuenta estos puntos clave, los fabricantes pueden superar los retos asociados a la sinterización del óxido de circonio y producir materiales cerámicos duraderos y de alta calidad.Comprender los entresijos del proceso de sinterización y la función de equipos como el horno de sinterización de óxido de circonio es esencial para obtener resultados óptimos.
Cuadro sinóptico:
Desafío | Problema | Solución |
---|---|---|
Resistencia al choque térmico | Los cambios rápidos de temperatura provocan grietas o fallos. | Utilice materiales y diseños resistentes al choque térmico, como la alúmina de gran pureza. |
Propiedades de los materiales | Las impurezas o las composiciones incorrectas provocan defectos. | Utilice polvos de circonio de gran pureza y mantenga un estricto control de la composición. |
Diseño del horno de sinterización | Un mal diseño del horno provoca un calentamiento desigual y una sinterización ineficaz. | Invierta en hornos con un control preciso de la temperatura y un calentamiento uniforme. |
Parámetros del proceso | Los ajustes incorrectos provocan un sinterizado incompleto o excesivo. | Optimice la temperatura, la velocidad de calentamiento y el tiempo de mantenimiento mediante pruebas. |
Tratamiento posterior a la sinterización | El enfriamiento rápido introduce tensiones y defectos. | Aplique un enfriamiento controlado y evite el enfriamiento rápido. |
¿Problemas con el sinterizado de óxido de circonio? Póngase en contacto con nuestros expertos para optimizar su proceso y obtener resultados superiores.